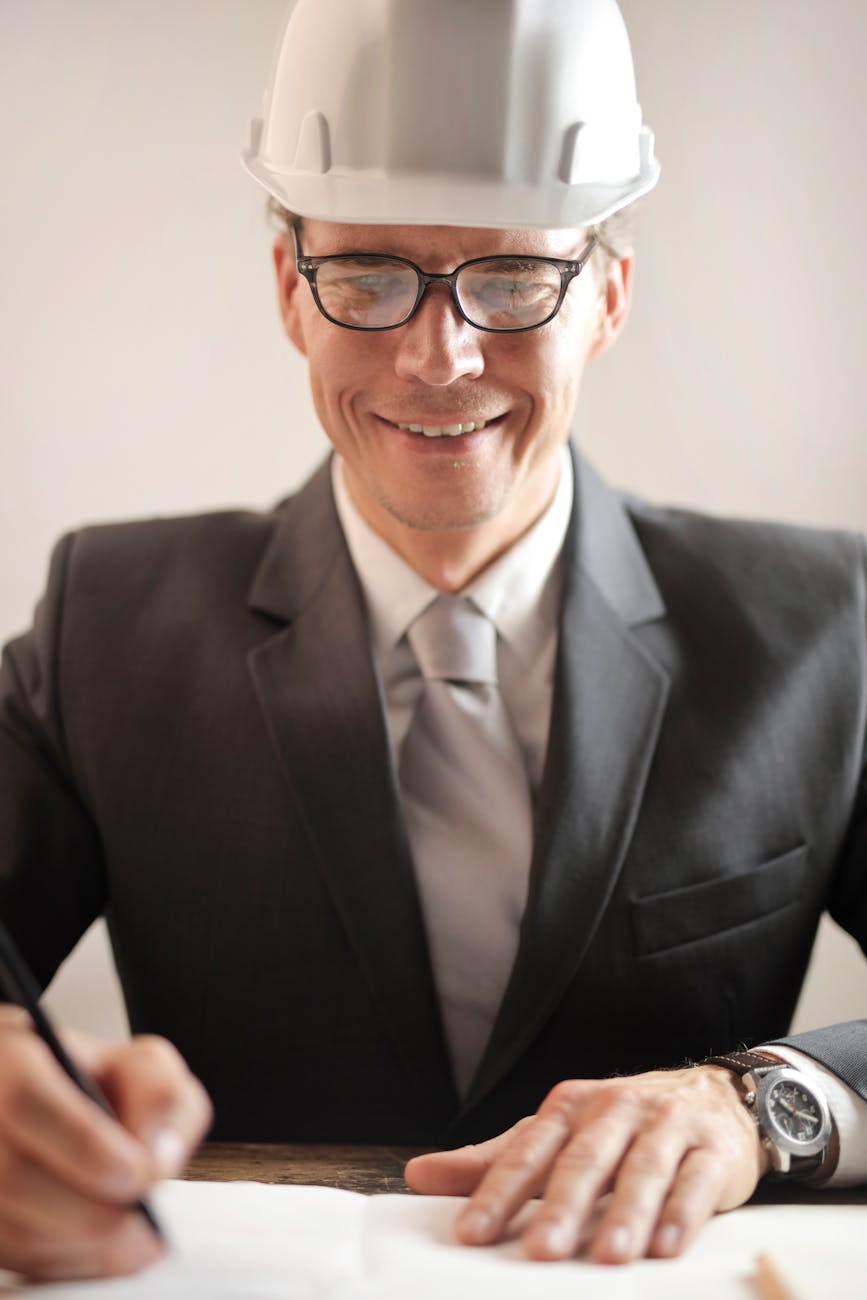
Workplace Safety Procedures
Workplace safety is a critical aspect of any organization’s operations, ensuring the well-being of employees and fostering a productive work environment. From manufacturing plants to office spaces, implementing effective safety procedures is paramount to prevent accidents, injuries, and potential hazards. In this article, we delve into the importance of workplace safety, methods to identify and mitigate risks, and strategies for fostering a culture of safety within the workplace.
Introduction to Workplace Safety Procedures
In today’s fast-paced work environment, ensuring the safety and well-being of employees is a top priority for organizations. Workplace safety procedures encompass a set of guidelines, protocols, and practices designed to protect employees from accidents, injuries, and health hazards while on the job. These procedures not only safeguard employees but also contribute to the overall success and sustainability of businesses.
Importance of Workplace Safety
Protecting Employees
The primary goal of workplace safety procedures is to protect employees from harm. By identifying potential hazards and implementing preventive measures, organizations can significantly reduce the risk of workplace accidents and injuries. This not only ensures the physical well-being of employees but also fosters a sense of security and confidence among them.
Legal Compliance
Compliance with occupational health and safety regulations is not just a legal requirement but also a moral obligation for employers. Failure to adhere to safety standards can result in legal liabilities, fines, and damage to the company’s reputation. By implementing robust safety procedures, organizations demonstrate their commitment to compliance and create a safe working environment for their employees.
Enhancing Productivity
A safe work environment is conducive to productivity and efficiency. When employees feel safe and secure in their workplace, they are more likely to focus on their tasks without distractions or concerns about potential hazards. Moreover, reducing accidents and injuries minimizes downtime and absenteeism, resulting in improved overall productivity and performance.
Identifying Workplace Hazards
Before implementing safety procedures, it is essential to identify potential hazards that may exist within the workplace. These hazards can vary depending on the nature of the work environment but commonly include:
Physical Hazards
Physical hazards include any factors within the workplace that can cause harm without necessarily coming into contact with the body. Examples include slippery floors, uneven surfaces, machinery, and electrical hazards.
Chemical Hazards
Chemical hazards arise from exposure to hazardous substances such as cleaning agents, solvents, and toxic gases. Employees working with or around these substances must be trained on proper handling, storage, and disposal procedures to minimize risks.
Biological Hazards
Biological hazards refer to exposure to bacteria, viruses, fungi, and other microorganisms that can cause illness or infection. In certain workplaces, such as healthcare facilities or laboratories, employees may be at risk of exposure to biological hazards and must follow strict protocols to prevent transmission.
Developing a Safety Plan
Once potential hazards have been identified, organizations must develop a comprehensive safety plan to mitigate risks and ensure the well-being of their employees. A safety plan typically includes the following components:
Risk Assessment
A thorough risk assessment involves identifying potential hazards, evaluating their likelihood and severity, and implementing control measures to minimize risks. This may include conducting workplace inspections, analyzing accident data, and involving employees in the process.
Training Programs
Employee training is crucial for ensuring awareness of safety procedures and protocols. Training programs should cover topics such as hazard recognition, emergency response, proper use of personal protective equipment (PPE), and first aid techniques.
Emergency Procedures
In the event of an accident, fire, or other emergencies, employees must be familiar with emergency procedures and evacuation routes. Organizations should conduct regular drills and provide clear instructions on how to respond to different types of emergencies.
Implementing Safety Measures
Once a safety plan has been developed, organizations must implement various measures to minimize risks and create a safe working environment for their employees. Key safety measures include:
Personal Protective Equipment (PPE)
PPE such as gloves, safety glasses, helmets, and respiratory masks are essential for protecting employees from workplace hazards. Employers should provide appropriate PPE based on the specific hazards present in the workplace and ensure that employees receive training on its proper use and maintenance.
Safety Signage
Clear and visible signage plays a crucial role in communicating safety information and warning employees of potential hazards. Signage should be strategically placed throughout the workplace, indicating safety protocols, emergency exits, and prohibited areas.
Regular Inspections
Regular inspections of the workplace help identify potential hazards and ensure that safety measures are being followed. Employers should establish a schedule for routine inspections and involve employees in the process to encourage accountability and participation.
Communication and Reporting
Effective communication is essential for maintaining a safe work environment and fostering a culture of safety within the organization. Key aspects of communication and reporting include:
Reporting Incidents
Employees should feel comfortable reporting any safety concerns, near misses, or accidents without fear of reprisal. Establishing a confidential reporting system encourages open communication and allows organizations to address potential hazards promptly.
Safety Meetings
Regular safety meetings provide an opportunity for employees to discuss safety issues, share best practices, and receive updates on safety protocols. These meetings promote collaboration and engagement, fostering a collective commitment to workplace safety.
Employee Feedback
Listening to employee feedback is crucial for identifying areas for improvement and addressing concerns proactively. Organizations should encourage employees to provide feedback on safety procedures, equipment, and workplace conditions, and take their input into consideration when making decisions.
Continuous Improvement
Workplace safety is an ongoing process that requires continuous evaluation and improvement. Key strategies for continuous improvement include:
Evaluating Safety Procedures
Regular evaluation of safety procedures allows organizations to identify areas for improvement and implement necessary changes. This may involve reviewing incident reports, conducting safety audits, and soliciting feedback from employees.
Updating Policies
As workplace conditions evolve and new hazards emerge, organizations must update their safety policies and procedures accordingly. Regular reviews of safety policies ensure that they remain effective and compliant with regulations.
Encouraging Participation
Creating a culture of safety requires active participation and engagement from all levels of the organization. Employers should incentivize and recognize employees for their contributions to safety initiatives, fostering a sense of ownership and accountability.
Conclusion
In conclusion, workplace safety procedures are essential for protecting employees, ensuring legal compliance, and enhancing productivity. By identifying potential hazards, developing a comprehensive safety plan, and implementing effective safety measures, organizations can create a safe and secure work environment for their employees. Continuous evaluation and improvement of safety procedures are necessary to adapt to changing workplace conditions and mitigate emerging risks.
Workplace Violence Prevention: Policies and Awareness
Hand and Finger Safety: Safeguarding Against Pinch Points and Lacerations
Workplace Hydration: Understanding Its Importance and Guidelines for Optimal Water Consumption
Workplace Hazards in Extreme Temperatures: Cold and Hot Environments
FAQs
- Why are workplace safety procedures important? Workplace safety procedures are important for protecting employees from accidents and injuries, ensuring legal compliance, and enhancing productivity.
- How can organizations identify workplace hazards? Organizations can identify workplace hazards through risk assessments, workplace inspections, and employee feedback.
- What role does training play in workplace safety? Training plays a crucial role in workplace safety by ensuring that employees are aware of safety procedures, hazard recognition, and emergency response protocols.
- How can organizations foster a culture of safety? Organizations can foster a culture of safety by promoting open communication, encouraging employee participation, and recognizing contributions to safety initiatives.
- Why is continuous improvement important in workplace safety? Continuous improvement is important in workplace safety to adapt to changing workplace conditions, identify areas for improvement, and mitigate emerging risks.