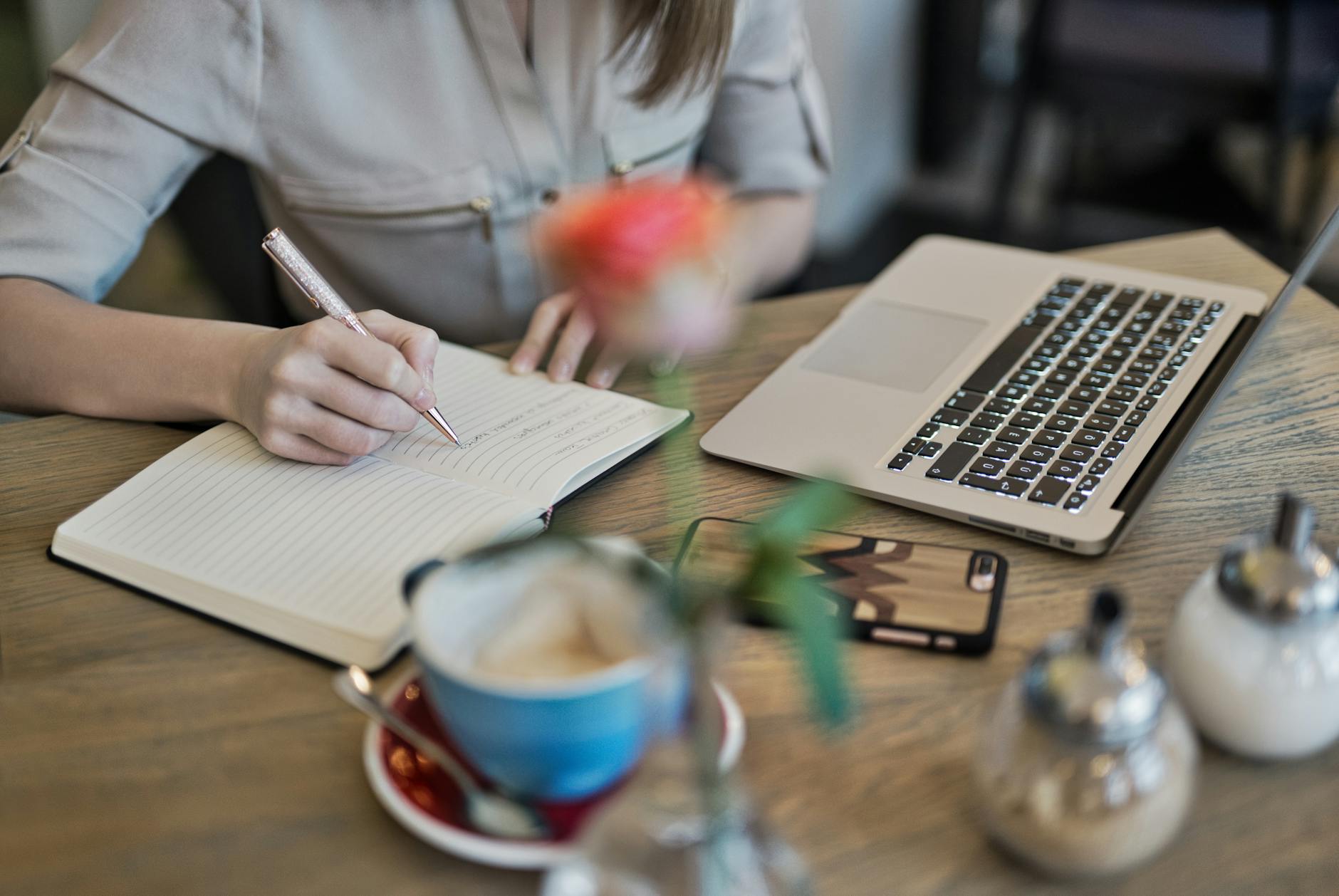
What is HIRA?: Hazard Identification and Risk Assessment?
Introduction
When it comes to workplace safety, understanding and managing risks is paramount. That’s where Hazard Identification and Risk Assessment (HIRA) steps in. But what exactly is HIRA, and why is it essential for every industry? Let’s break it down.
Understanding the Basics
Definition of Hazard Identification
Hazard Identification involves recognizing potential sources of harm in a workplace. It could be anything from slippery floors to faulty machinery or hazardous chemicals.
Definition of Risk Assessment
Risk Assessment evaluates the likelihood and impact of those identified hazards. It’s about asking: What could happen, and how bad could it be?
Difference Between Hazard and Risk
Think of a hazard as the what (e.g., a wet floor) and the risk as the so what (e.g., the likelihood of someone slipping and getting injured).
The Purpose of HIRA
Why do organizations invest time and resources in HIRA? Simple: safety, compliance, and efficiency.
- Preventing Workplace Incidents: HIRA minimizes accidents by identifying and controlling risks.
- Creating a Safer Environment: A well-executed HIRA ensures everyone goes home safe at the end of the day.
- Meeting Regulatory Requirements: HIRA helps businesses comply with legal standards like OSHA and ISO 45001.
Key Components of HIRA
Hazard Identification
- Common Workplace Hazards: Slips, trips, falls, chemical spills, and fire hazards are just the tip of the iceberg.
- How to Identify Hazards: Regular inspections, employee feedback, and reviewing past incident reports are great starting points.
Risk Assessment
- Steps in Risk Assessment:
- Identify the hazard.
- Determine who might be harmed and how.
- Evaluate risks and decide on precautions.
- Record findings and implement controls.
- Risk Matrix Explained: A simple tool to rate risks based on their likelihood and severity.
Risk Control Measures
- Hierarchy of Controls:
- Elimination – Remove the hazard.
- Substitution – Replace the hazard.
- Engineering Controls – Isolate people from the hazard.
- Administrative Controls – Change the way people work.
- Personal Protective Equipment (PPE) – Last line of defense.
The HIRA Process
HIRA isn’t a one-and-done deal—it’s a continuous loop:
- Identifying Hazards: Use tools like checklists or hazard maps.
- Assessing Risks: Analyze potential impacts using a risk matrix.
- Implementing Controls: Choose measures based on the hierarchy of controls.
- Reviewing and Monitoring: Regularly update assessments as conditions change.
Tools and Techniques in HIRA
- Checklists and Observations: Simple yet effective for spotting common hazards.
- Job Safety Analysis (JSA): Breaks down tasks to identify risks at every step.
- SWOT Analysis in Safety: Evaluates strengths, weaknesses, opportunities, and threats in your safety program.
HIRA in Different Industries
- Construction Industry: Falls from heights, equipment hazards, and site-specific risks are common.
- Manufacturing Sector: Machine-related injuries and chemical exposures require attention.
- Oil and Gas Sector: High-risk environments demand rigorous HIRA practices.
Regulatory Framework for HIRA
- OSHA Guidelines: Set the gold standard for workplace safety.
- International Standards: Frameworks like ISO 45001 emphasize the role of risk management.
Benefits of HIRA
From fewer accidents to cost savings, the benefits of HIRA are undeniable:
- Reduction in Workplace Accidents: Proactive identification and control of risks.
- Cost Efficiency: Avoid costs associated with accidents and downtime.
- Improved Employee Morale: Workers feel valued when safety is a priority.
Common Challenges in HIRA
- Resistance to Implementation: Change is never easy, but involving employees can help.
- Lack of Proper Training: Without education, even the best tools are ineffective.
- Overlooking Hidden Hazards: Attention to detail is crucial.
Best Practices for Effective HIRA
- Engage Employees: They’re on the front lines and can provide valuable insights.
- Regular Training and Updates: Keep the team informed about new risks and regulations.
- Leverage Technology: Tools like safety apps and sensors make HIRA more efficient.
What is HIRA: Hazard Identification and Risk Assessment?
Hazard Identification and Risk Assessment (HIRA) is a critical process used in various industries to identify potential hazards in the workplace and assess the risks associated with those hazards. The goal of HIRA is to ensure a safe and healthy working environment by proactively managing risks and implementing effective control measures.
Components of HIRA
- Hazard Identification
- This step involves identifying potential sources of harm or danger in the workplace.
- Hazards can be physical (machinery, slippery floors), chemical (toxic substances), biological (viruses, bacteria), ergonomic (poor posture), or psychological (stress, fatigue).
- Common methods include workplace inspections, reviewing past incident reports, and consulting employees.
- Risk Assessment
- Once hazards are identified, the next step is to evaluate the likelihood of an incident occurring and the potential severity of its consequences.
- Risks are typically categorized as high, medium, or low, helping prioritize actions to mitigate them.
- Tools like risk matrices and scoring systems are often used for this evaluation.
- Control Measures
- After assessing risks, appropriate control measures are implemented to eliminate or reduce the risks to an acceptable level.
- These measures follow a hierarchy:
- Elimination: Remove the hazard entirely.
- Substitution: Replace the hazard with a safer alternative.
- Engineering Controls: Use physical changes like guards or barriers.
- Administrative Controls: Implement policies, training, and procedures.
- Personal Protective Equipment (PPE): As a last resort, provide safety gear.
Importance of HIRA
- Prevention of Accidents and Injuries
- Identifying and addressing hazards reduces the likelihood of workplace incidents.
- Regulatory Compliance
- Many countries mandate risk assessments to comply with occupational health and safety laws.
- Improved Workplace Safety Culture
- HIRA promotes awareness among employees about potential risks and fosters a culture of safety.
- Cost Reduction
- By preventing accidents, organizations can save on medical expenses, legal fees, and compensation claims.
Steps to Conduct HIRA
- Prepare a Team
- Assemble a group with diverse expertise, including safety officers, supervisors, and employees.
- Identify Activities
- List all tasks and processes in the workplace.
- Identify Hazards
- Use tools like checklists, hazard maps, and job safety analyses to find risks.
- Evaluate Risks
- Analyze the severity and likelihood of potential incidents using a risk matrix.
- Implement Controls
- Apply the most effective control measures to mitigate risks.
- Review and Update
- Regularly revisit the HIRA process to adapt to changes in the workplace or new hazards.
Conclusion
HIRA is more than a regulatory checkbox—it’s a lifesaving strategy. By identifying hazards and assessing risks, organizations can create safer, more efficient workplaces. Whether you’re in construction, manufacturing, or oil and gas, HIRA is a must-have tool in your safety arsenal.
Difference Between HIRA and JSA | Explained with Example | Free Download PPT
Risk Assessment vs Job Safety Analysis
What are the 5 Steps of a JSA?
5 Step Process of Risk Assessment
FAQs
- What is the difference between HIRA and JSA?
HIRA covers broader risks, while JSA focuses on task-specific hazards. - How often should HIRA be conducted?
Regularly and whenever significant changes occur in the workplace. - Is HIRA applicable to small businesses?
Absolutely! Safety knows no size—small businesses benefit just as much. - What are the legal requirements for HIRA?
Requirements vary by country but generally align with OSHA or ISO standards. - How can employees contribute to HIRA?
By reporting hazards, participating in assessments, and adhering to safety protocols.