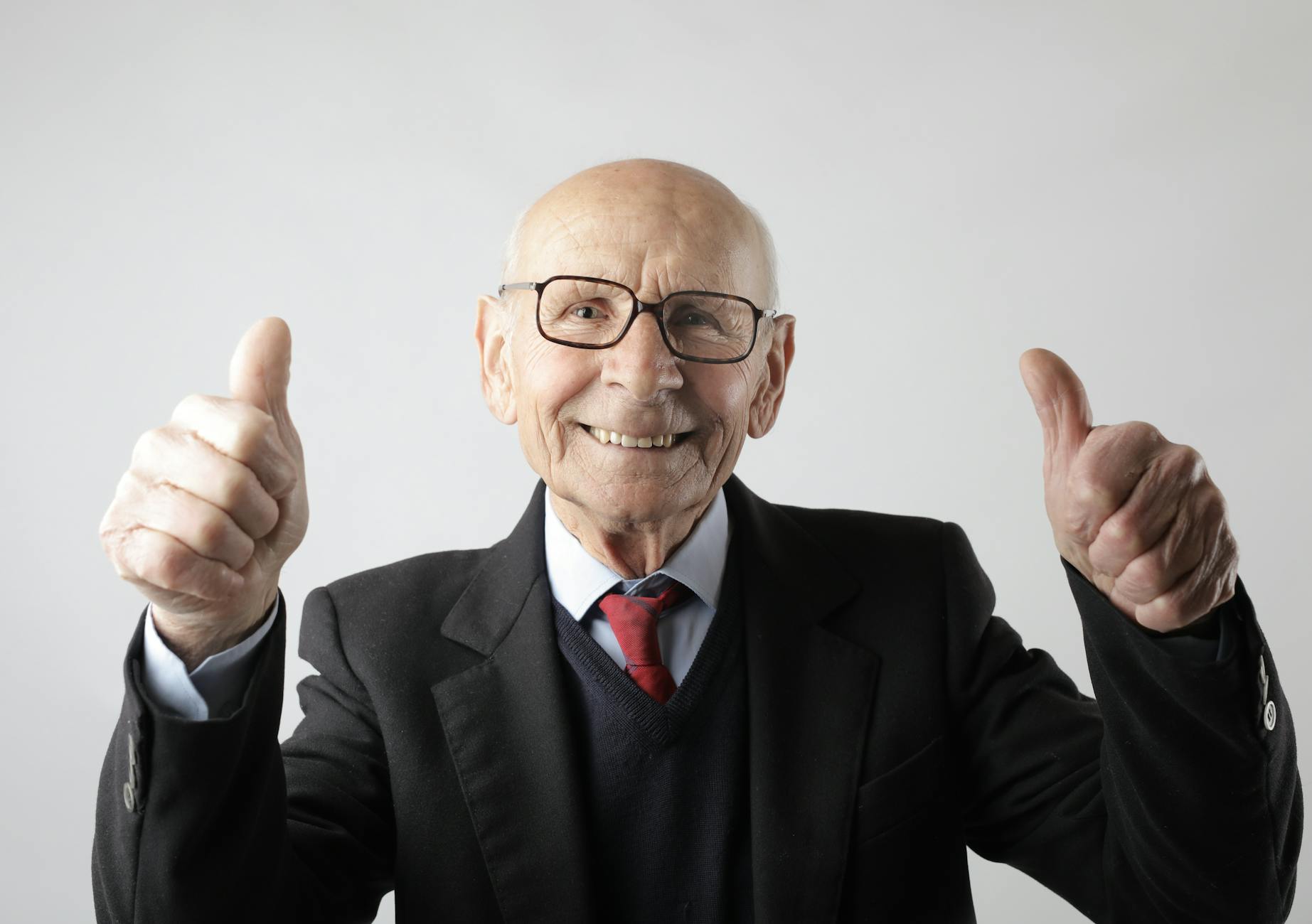
What Does a Safety Manager Do?
Introduction
Ever wondered what keeps a workplace safe and accident-free? Meet the unsung hero: the Safety Manager. These professionals play a crucial role in ensuring that your work environment is secure, compliant, and prepared for any safety-related incidents. But what exactly does a Safety Manager do? Let’s dive in and find out.
What is a Safety Manager?
A Safety Manager is a professional responsible for developing, implementing, and overseeing health and safety protocols in the workplace. Their main goal is to prevent accidents and injuries, ensuring a safe environment for everyone.
Importance of a Safety Manager in the Workplace
Safety Managers are essential because they help reduce workplace hazards, ensure compliance with laws, and promote a culture of safety. Their efforts not only protect employees but also save companies money by preventing costly accidents and legal issues.
Roles and Responsibilities of a Safety Manager
Developing Safety Policies
Safety Managers create and update safety policies tailored to their specific workplace. These policies are designed to mitigate risks and ensure a consistent approach to safety across the organization.
Conducting Risk Assessments
One of the core tasks of a Safety Manager is to identify potential hazards through regular risk assessments. They analyze work processes, machinery, and workspaces to pinpoint areas that could pose a threat.
Training Employees on Safety Protocols
Education is a significant part of a Safety Manager’s role. They conduct training sessions to educate employees about safety procedures, emergency response plans, and the correct use of safety equipment.
Investigating Accidents and Incidents
When accidents happen, Safety Managers step in to investigate. They determine the root cause of incidents and develop strategies to prevent future occurrences.
Ensuring Compliance with Regulations
Safety regulations are constantly evolving, and it’s the Safety Manager’s job to keep the company compliant. They stay up-to-date with local, state, and federal safety laws and ensure all practices meet these standards.
Key Skills Required for a Safety Manager
Attention to Detail
Safety Managers need a keen eye for detail to spot potential hazards and ensure that safety protocols are meticulously followed.
Strong Communication Skills
Clear communication is crucial. Safety Managers must convey safety procedures and policies effectively to employees at all levels of the organization.
Analytical Thinking
The ability to analyze data and incidents helps Safety Managers identify trends and develop proactive safety measures.
Leadership and Team Management
Safety Managers often lead teams and must inspire a culture of safety. Strong leadership skills are essential to guide and motivate others.
Day-to-Day Activities of a Safety Manager
Routine Safety Inspections
Daily inspections are a part of the job. Safety Managers check equipment, workspaces, and processes to ensure compliance with safety standards.
Safety Meetings and Briefings
Regular meetings with staff keep everyone informed about safety practices and any changes to protocols. These briefings are essential for maintaining a high level of safety awareness.
Reporting and Documentation
Accurate documentation is vital. Safety Managers maintain detailed records of inspections, incidents, and training sessions to track progress and identify areas for improvement.
Safety Manager’s Role in Different Industries
Construction
In construction, Safety Managers focus on preventing accidents related to heavy machinery, heights, and hazardous materials. They ensure all safety gear is used correctly and that safety protocols are strictly followed.
Manufacturing
Manufacturing environments pose unique challenges, including machinery operation and chemical handling. Safety Managers in this sector emphasize machine safety, ergonomics, and proper handling procedures.
Healthcare
Healthcare Safety Managers address risks such as exposure to infectious diseases, handling of biohazards, and ensuring a safe environment for both staff and patients.
Office Environments
Even in less hazardous office settings, Safety Managers play a role in ensuring ergonomic setups, fire safety, and emergency preparedness.
Challenges Faced by Safety Managers
Keeping Up with Changing Regulations
Safety regulations are not static. Keeping up with the latest laws and best practices is a constant challenge for Safety Managers.
Managing Employee Behavior and Attitudes
Cultivating a culture of safety can be difficult. Safety Managers must address complacency and ensure that all employees take safety seriously.
Balancing Safety with Productivity
Sometimes, safety measures can slow down work processes. Safety Managers need to find a balance that keeps everyone safe without hindering productivity.
A safety manager is responsible for ensuring the health and safety of employees in the workplace. Their primary duties include developing, implementing, and overseeing safety policies and procedures to prevent accidents, injuries, and occupational hazards. Here are the key responsibilities of a safety manager:
Policy Development: Creating comprehensive safety policies that comply with local, state, and federal regulations.
Training and Education: Conducting safety training programs and workshops to educate employees on proper safety practices and emergency procedures.
Risk Assessment: Identifying potential hazards through regular inspections and risk assessments, and implementing measures to mitigate these risks.
Incident Investigation: Investigating accidents, injuries, and near-misses to determine their causes and to develop strategies to prevent future occurrences.
Compliance Monitoring: Ensuring that the workplace adheres to all safety regulations and standards. This includes keeping up-to-date with changes in safety laws and regulations.
Safety Audits: Conducting regular safety audits and inspections to ensure compliance with safety protocols and to identify areas for improvement.
Emergency Response Planning: Developing and maintaining emergency response plans and procedures for dealing with various types of emergencies, such as fires, chemical spills, or natural disasters.
Record Keeping: Maintaining detailed records of safety inspections, training sessions, incident reports, and compliance audits.
Communication: Serving as a liaison between management and employees on safety-related issues, and promoting a culture of safety within the organization.
Continuous Improvement: Continuously reviewing and improving safety policies and procedures to enhance the overall safety of the workplace.
By fulfilling these responsibilities, safety managers play a crucial role in creating a safe work environment, reducing the likelihood of workplace accidents, and ensuring the well-being of employees.
Conclusion
Safety Managers are the backbone of a secure workplace. Their comprehensive approach to safety, from policy development to daily inspections, ensures that employees can work in a safe and productive environment. By balancing the demands of safety and efficiency, they play a vital role in the success of any organization.
How to Write Safety Observation by Safety Officer | Download PPT
Safety Officer Duties and Responsibilities
Safety Officer Job Good or Bad?
What is the Highest Salary in Safety Field?
What is a Safety Manager Salary?
FAQs
What qualifications are needed to become a Safety Manager?
Typically, a bachelor’s degree in occupational health, safety, engineering, or a related field is required. Certifications like CSP (Certified Safety Professional) can enhance career prospects.
How does a Safety Manager contribute to a company’s success?
Safety Managers help prevent accidents, reduce downtime, and ensure compliance with regulations, all of which contribute to a more efficient and profitable company.
What tools do Safety Managers use?
Safety Managers use a variety of tools, including risk assessment software, incident reporting systems, and personal protective equipment (PPE) to maintain workplace safety.
Can a Safety Manager work in multiple industries?
Yes, Safety Managers can work in various industries such as construction, manufacturing, healthcare, and more. Their skills are transferable, although industry-specific knowledge is often required.
How often should safety training be conducted?
Safety training should be conducted regularly, at least annually, and whenever new procedures or equipment are introduced. Regular refresher courses help maintain high safety standards.