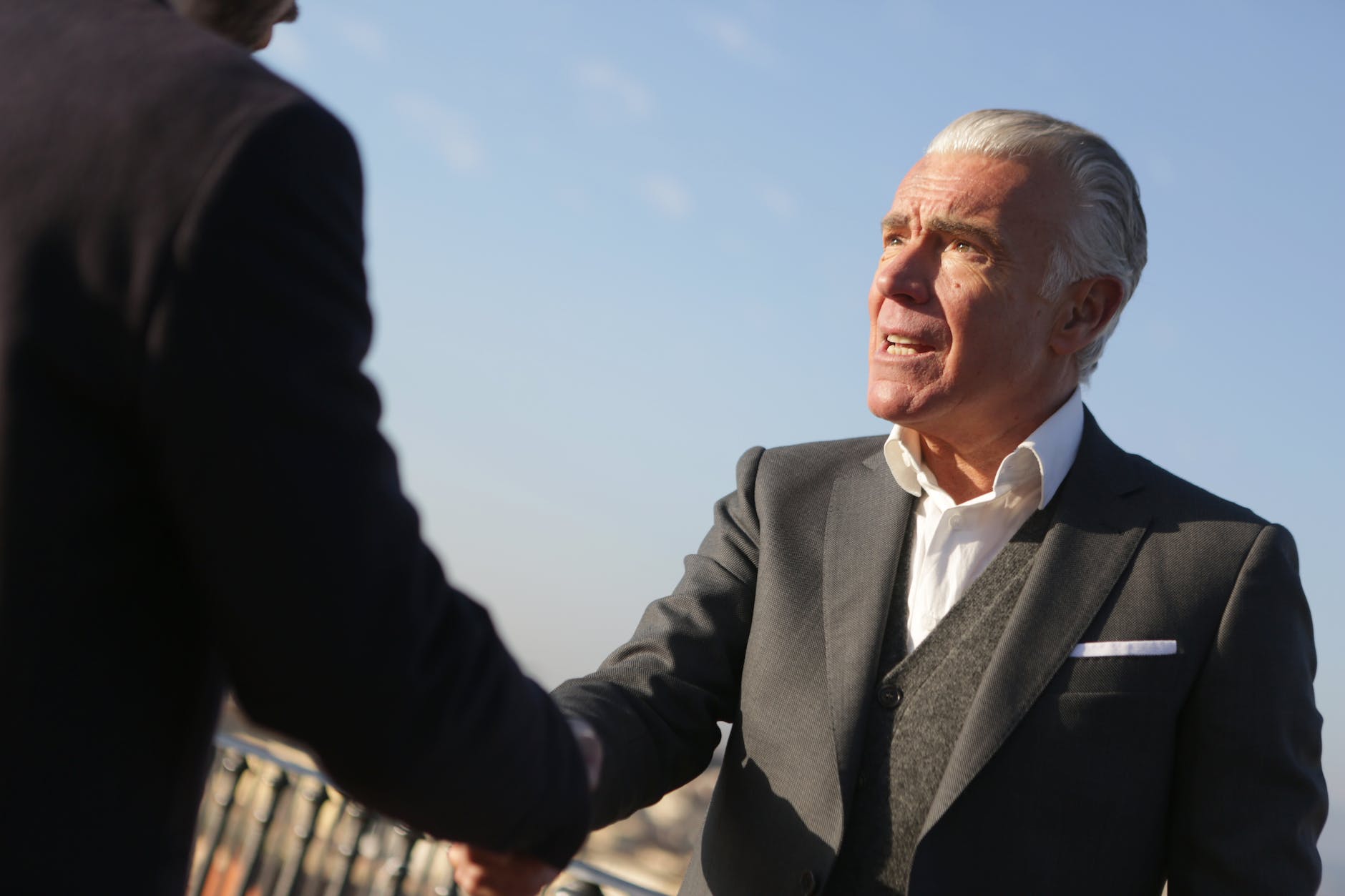
Safety Manager: What are the Duties of a Safety Manager?
In today’s fast-paced and dynamic work environments, ensuring the safety of employees is paramount. This responsibility falls on the shoulders of a dedicated professional known as the Safety Manager. In this comprehensive guide, we will delve into the intricate duties and responsibilities that define the role of a Safety Manager.
I. Introduction
A. Definition of a Safety Manager
Safety Managers play a critical role in organizations by overseeing and implementing safety protocols to protect employees, assets, and the environment.
B. Importance of Safety Management
Understanding the significance of safety management sets the foundation for effective risk mitigation and a secure work environment.
II. Qualifications and Skills
A. Educational Background
Safety Managers typically hold degrees in occupational health and safety, engineering, or related fields.
B. Certifications
Certifications such as Certified Safety Professional (CSP) enhance a Safety Manager’s credibility and expertise.
C. Communication Skills
Effective communication is key, as Safety Managers interact with employees at all levels to convey safety policies and procedures.
D. Attention to Detail
Meticulous attention to detail ensures thorough risk assessments and the identification of potential hazards.
III. Key Responsibilities
A. Risk Assessment
Safety Managers conduct comprehensive risk assessments to identify potential hazards and implement preventive measures.
B. Implementation of Safety Policies
They are responsible for the development and implementation of safety policies and procedures in alignment with industry standards.
C. Training Programs
Safety Managers organize and conduct training programs to educate employees on safety protocols and emergency procedures.
D. Incident Investigation
In the unfortunate event of an incident, Safety Managers lead investigations to determine root causes and prevent future occurrences.
E. Regulatory Compliance
Staying abreast of changing regulations and ensuring compliance is a crucial aspect of the Safety Manager’s role.
IV. Role in Emergency Preparedness
A. Creating Emergency Plans
Safety Managers develop and update emergency response plans to address various scenarios.
B. Conducting Drills
Regular drills and simulations prepare employees to respond effectively in emergency situations.
C. Collaborating with Emergency Services
Safety Managers liaise with local emergency services to enhance coordination during crises.
V. Safety Culture
A. Fostering a Culture of Safety
They actively promote a safety-first culture by encouraging employee involvement and awareness.
B. Employee Involvement
Involving employees in safety initiatives fosters a sense of ownership and accountability.
C. Continuous Improvement
Safety Managers drive continuous improvement by analyzing safety performance data and implementing enhancements.
A Safety Manager plays a crucial role in ensuring the health and well-being of employees within an organization. The primary duties of a Safety Manager include:
- Risk Assessment:
- Identify and assess potential hazards in the workplace.
- Evaluate the level of risk associated with each hazard.
- Develop strategies to mitigate or eliminate risks.
- Compliance with Regulations:
- Stay informed about safety regulations and standards relevant to the industry.
- Ensure the organization complies with local, state, and federal safety laws.
- Training and Education:
- Develop and implement safety training programs for employees.
- Conduct regular safety meetings to educate staff on best practices and procedures.
- Emergency Preparedness:
- Establish and oversee emergency response plans.
- Conduct drills to ensure employees are familiar with emergency procedures.
- Incident Investigation:
- Investigate accidents, incidents, and near misses to determine root causes.
- Develop and implement corrective actions to prevent recurrence.
- Safety Inspections:
- Conduct regular inspections of the workplace to identify safety hazards.
- Ensure that safety equipment is in good working condition.
- Safety Policies and Procedures:
- Develop and update safety policies and procedures.
- Communicate and enforce safety rules throughout the organization.
- Safety Communication:
- Foster a culture of safety through effective communication.
- Encourage employees to report safety concerns and incidents.
- Personal Protective Equipment (PPE):
- Ensure that employees have access to and use appropriate PPE.
- Monitor compliance with PPE requirements.
- Recordkeeping:
- Maintain accurate records of safety training, inspections, and incidents.
- Prepare reports for management and regulatory agencies as required.
- Continuous Improvement:
- Identify opportunities for improvement in safety processes.
- Implement measures to enhance overall safety performance.
- Collaboration:
- Collaborate with other departments to integrate safety into all aspects of operations.
- Work with management to create a safety-conscious work culture.
- Contractor Safety Management:
- Ensure that contractors and vendors comply with safety standards.
- Evaluate and approve contractors’ safety plans.
- Safety Audits:
- Conduct regular safety audits to assess the effectiveness of safety programs.
- Implement corrective actions based on audit findings.
By fulfilling these duties, a Safety Manager helps create a secure and healthy work environment, reducing the risk of accidents and promoting the overall well-being of employees.
VI. Challenges in Safety Management
A. Balancing Productivity and Safety
Safety Managers face the challenge of maintaining safety standards without compromising productivity.
B. Handling Resistance to Safety Measures
Overcoming resistance to new safety protocols requires effective communication and change management skills.
VII. Benefits of an Effective Safety Manager
A. Reduced Accidents
A competent Safety Manager contributes to a significant reduction in workplace accidents.
B. Increased Employee Morale
A focus on safety enhances employee morale and job satisfaction.
C. Cost Savings
Proactive safety measures lead to cost savings by preventing accidents and associated expenses.
VIII. Tips for Aspiring Safety Managers
A. Continuous Learning
Stay updated with industry trends and advancements through continuous learning and professional development.
B. Networking in the Industry
Building a network within the safety management community fosters knowledge exchange and career opportunities..
IX. Conclusion
A. Recap of Key Points
Safety Managers are indispensable for creating and maintaining a safe work environment.
B. Importance of Safety Managers in Every Industry
Their role extends across industries, emphasizing the universal importance of safety management.
Safety Manager: What is the qualification required to become a Safety Manager?
Safety Engineer: What is the Qualification Required to Become a Safety Engineer?
Which Course is Best for Safety Officer?
How to Become an Occupational Health and Safety Officer
X. FAQs
A. What qualifications are needed to become a Safety Manager?
To become a Safety Manager, a relevant degree in occupational health and safety, engineering, or a related field is typically required. Additionally, certifications such as the Certified Safety Professional (CSP) can enhance credibility.
B. How can a Safety Manager promote a culture of safety?
Safety Managers can promote a culture of safety by actively involving employees, conducting regular training programs, and fostering open communication about safety concerns.
C. What challenges do Safety Managers commonly face?
Safety Managers often face challenges in balancing productivity and safety, overcoming resistance to new safety measures, and staying updated with evolving regulations.
D. Are there specific industries where Safety Managers are more crucial?
Safety Managers are crucial in various industries, including manufacturing, construction, healthcare, and oil and gas, where workplace hazards are more prominent.
E. How can companies measure the success of their safety programs?
Companies can measure the success of their safety programs by tracking accident rates, conducting regular safety audits, and obtaining employee feedback. Continuous improvement and a reduction in accidents indicate a successful safety program.