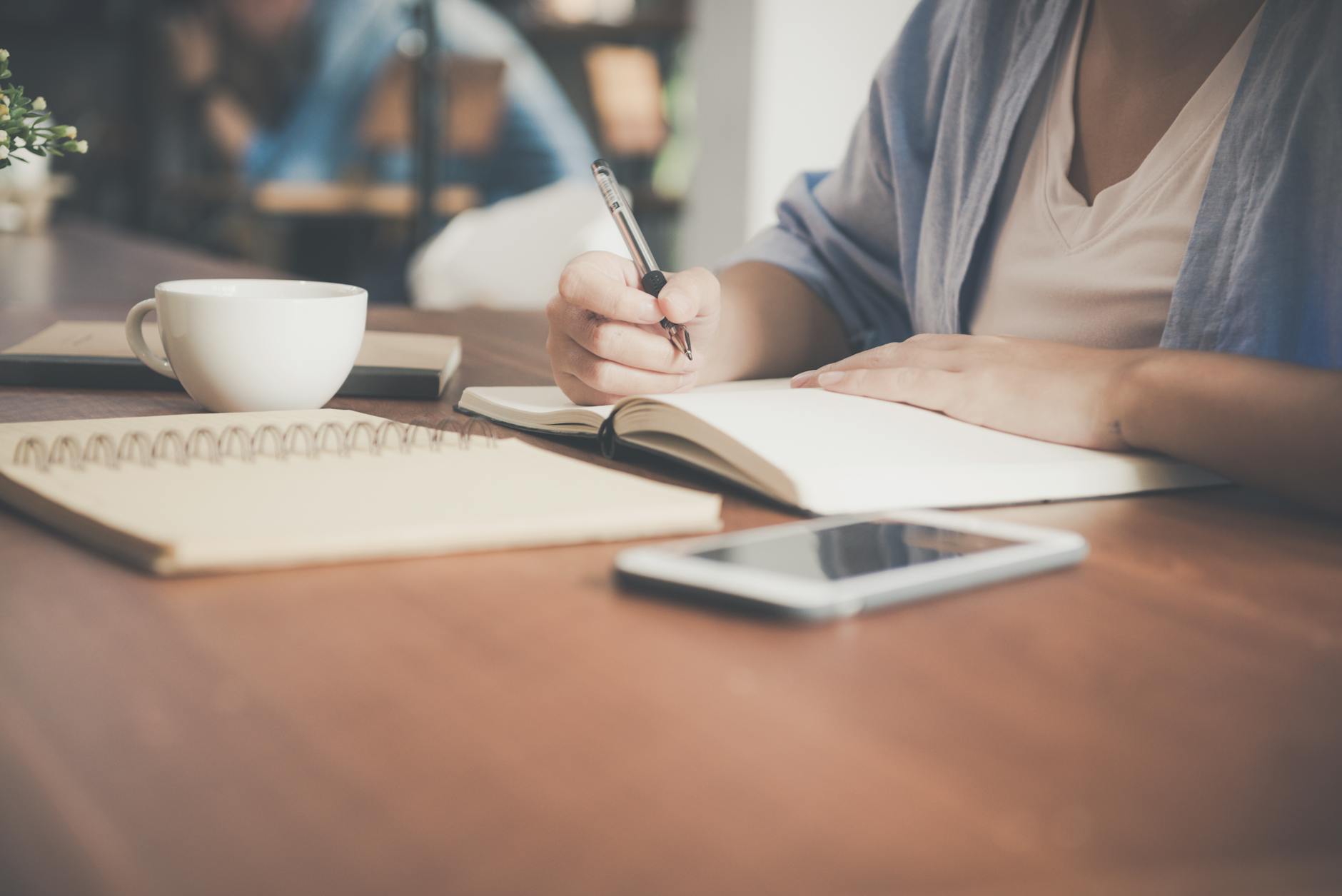
What are the 5 Steps of a JSA?
Introduction
Have you ever wondered what steps you should take to ensure a safe working environment? One of the most effective tools in workplace safety is the Job Safety Analysis (JSA). In this article, we’ll walk you through the five essential steps of a JSA, showing you how to identify potential hazards and implement preventive measures to keep everyone safe.
What is Job Safety Analysis (JSA)?
Job Safety Analysis (JSA) is a systematic process used to evaluate a job or task to identify potential hazards and determine the safest way to perform it. The primary goal of a JSA is to prevent workplace accidents and injuries by addressing risks before they result in harm.
Step 1: Select the Job to be Analyzed
The first step in a JSA is to select the job to be analyzed. This step is crucial because it sets the foundation for the entire analysis. Jobs are typically chosen based on their risk level, frequency, and severity of potential accidents. For example, tasks involving heavy machinery, hazardous chemicals, or complex procedures are prime candidates for a JSA.
Step 2: Break the Job Down into Steps
Once a job is selected, the next step is to break the job down into individual steps. This involves detailing each action required to complete the task from start to finish. Breaking the job into steps helps in identifying specific hazards associated with each part of the process. For instance, if you’re analyzing the job of operating a forklift, steps might include inspecting the forklift, starting it, driving to the load, lifting the load, and so on.
Step 3: Identify Potential Hazards
The third step is to identify potential hazards associated with each step of the job. Hazards can be physical, chemical, biological, ergonomic, or a combination of these. To effectively spot hazards, consider asking questions like: “What can go wrong?” and “What are the consequences?” Using tools like checklists, brainstorming sessions, and past incident reports can aid in thorough hazard identification.
Step 4: Determine Preventive Measures
After identifying hazards, the next step is to determine preventive measures to eliminate or control these risks. This involves developing control measures based on the hierarchy of controls:
- Elimination: Remove the hazard entirely.
- Substitution: Replace the hazard with something less dangerous.
- Engineering Controls: Isolate people from the hazard.
- Administrative Controls: Change the way people work.
- Personal Protective Equipment (PPE): Use protective gear to reduce exposure.
For example, if a task involves handling toxic chemicals, preventive measures might include substituting the chemical with a safer alternative, using enclosed systems to handle the chemical, training workers on proper handling procedures, and providing appropriate PPE.
Step 5: Review and Update the JSA
The final step is to review and update the JSA regularly. This ensures that the analysis remains relevant and effective as conditions change. Regular reviews should be scheduled, and updates should be made whenever there are changes in the job process, equipment, or after an incident. For example, if new machinery is introduced, the JSA should be updated to include any new hazards and preventive measures.
Conclusion
In summary, the five steps of a JSA—selecting the job, breaking it down into steps, identifying hazards, determining preventive measures, and reviewing and updating the JSA—are essential for maintaining a safe workplace. By systematically analyzing and addressing potential hazards, you can significantly reduce the risk of accidents and injuries.
5 Step Process of Risk Assessment
Hazard Communication: Elements and SDS Importance
FAQs
What is the difference between JSA and JHA?
JSA (Job Safety Analysis) and JHA (Job Hazard Analysis) are often used interchangeably. However, JHA typically focuses more on identifying hazards, while JSA includes identifying hazards and determining preventive measures.
How often should a JSA be reviewed?
A JSA should be reviewed regularly, at least annually, and whenever there are changes in the job process, equipment, or after an incident.
Who should be involved in a JSA?
A JSA should involve employees who perform the job, supervisors, safety professionals, and any other stakeholders who can provide valuable insights into the task and its associated risks.
Can a JSA be used for non-hazardous jobs?
Yes, a JSA can be used for any job to ensure it is performed safely. Even non-hazardous jobs can benefit from a systematic analysis to identify and mitigate risks.
What are the common mistakes in conducting a JSA?
Common mistakes include not involving employees in the process, failing to identify all hazards, not updating the JSA regularly, and not implementing the identified preventive measures.
Good job.Do most developing countries comply with safety?