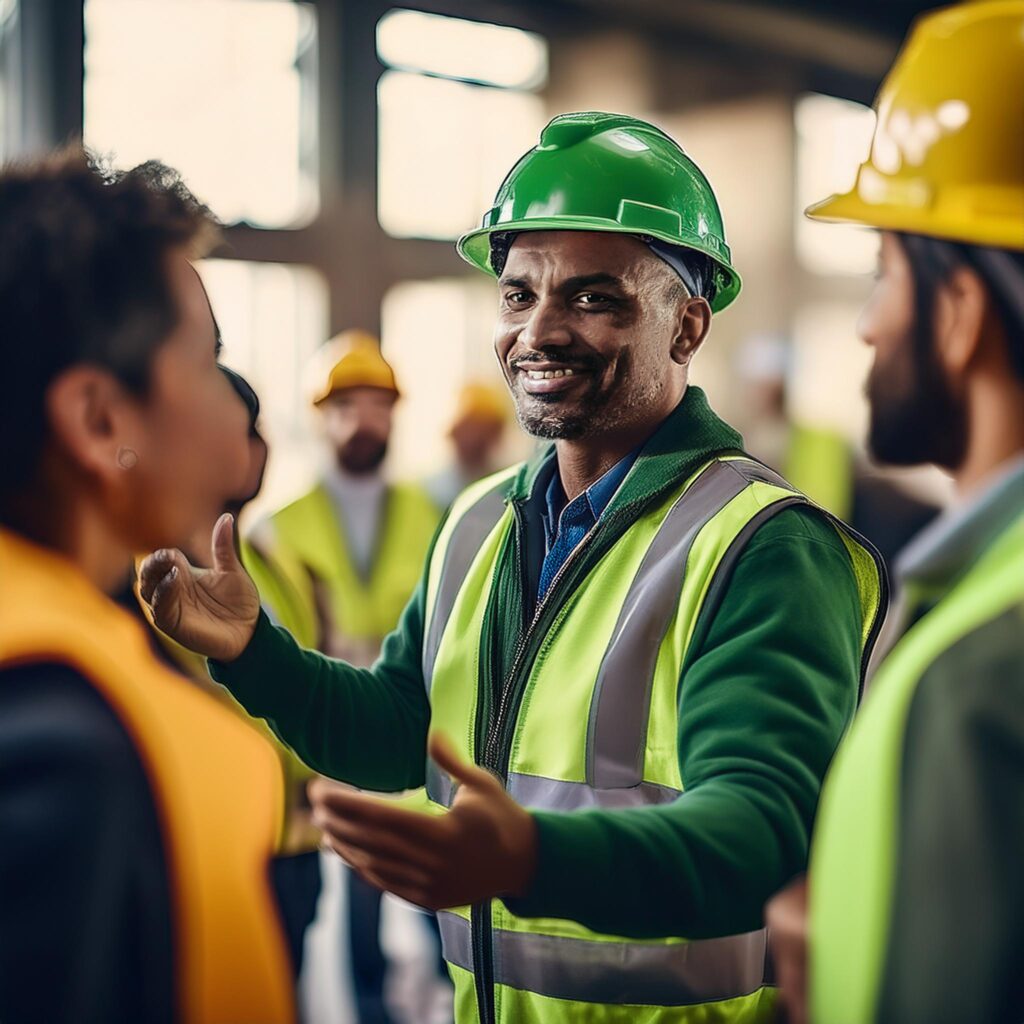
Weekly Work of Safety Officer
Introduction
Keeping a workplace safe is no small feat. Safety officers are the unsung heroes behind the scenes, ensuring everything runs smoothly and workers stay out of harm’s way. But what exactly does a safety officer do each week? Let’s dive into their responsibilities and see how they maintain safety standards.
Planning and Preparation
Safety begins with a plan, and safety officers are masters at creating them.
Reviewing Weekly Safety Reports
Every week starts with a detailed review of previous safety reports. What went right? What needs improvement? This review sets the stage for a productive week.
Setting Safety Goals for the Week
After assessing past performance, safety officers set clear, actionable goals to tackle any identified gaps or challenges.
Coordinating with Other Departments
Collaboration is key. Safety officers often meet with other departments to align on safety measures and ensure everyone is on the same page.
Inspections and Audits
Nothing beats a hands-on approach to workplace safety.
Conducting Workplace Safety Inspections
Armed with checklists and sharp eyes, safety officers inspect work areas for hazards. They look for issues like obstructed pathways, faulty equipment, or improper PPE use.
Auditing Compliance with Safety Standards
Inspections aren’t just about spotting hazards—they’re about ensuring compliance with regulatory standards and internal policies.
Training and Awareness
A safe workplace is an informed workplace.
Organizing Safety Training Sessions
Regular training keeps employees updated on the latest safety practices. Whether it’s fire drills or equipment handling, safety officers ensure everyone knows what to do.
Running Toolbox Talks
Quick, daily or weekly discussions about specific safety topics help keep safety top of mind.
Promoting Safety Campaigns
From posters to incentives, safety officers use creative campaigns to engage workers and reinforce the importance of safety.
Incident Management
Accidents happen, but a safety officer ensures they’re handled properly.
Investigating Recent Incidents
When something goes wrong, a deep dive into what happened and why is crucial.
Root Cause Analysis
This involves digging beyond the surface to find the real reasons behind an incident and ensuring it doesn’t happen again.
Implementing Corrective Actions
Once the cause is clear, solutions are put into place—whether it’s additional training, equipment upgrades, or procedural changes.
Documentation and Reporting
Paperwork might not be glamorous, but it’s vital.
Preparing Weekly Safety Reports
These reports highlight everything from inspection findings to incident investigations, ensuring transparency and accountability.
Updating Policies and Procedures
Safety standards evolve, and so should company policies. Safety officers ensure documentation reflects the latest best practices.
Submitting Reports to Management
Sharing insights with upper management helps drive informed decisions and gain support for safety initiatives.
Engagement with Workers
Building trust with workers is just as important as enforcing rules.
Conducting Worker Consultations
One-on-one or group discussions help safety officers understand worker concerns and gather feedback.
Addressing Safety Concerns
Quick responses to issues raised by workers foster a culture of safety and trust.
Weekly Safety Meetings
Safety officers bring everyone together to review and plan.
Reviewing Progress and Challenges
These meetings recap achievements and discuss obstacles, ensuring everyone is informed and aligned.
Planning for Upcoming Activities
Looking ahead, safety officers outline the next steps to maintain or improve workplace safety.
Evaluating and Improving Practices
Safety is an ongoing journey, not a destination.
Monitoring Effectiveness of Safety Measures
Are the implemented solutions working? Safety officers constantly evaluate their impact.
Introducing New Safety Initiatives
Innovative ideas keep safety programs fresh and effective.
The weekly work of a Safety Officer involves a combination of routine inspections, meetings, training, and long-term planning to ensure a safe and compliant workplace. Here is a breakdown of the tasks a Safety Officer typically performs over a week:
Monday: Kickstart the Week
- Review Weekly Goals:
- Analyze the safety performance from the previous week.
- Set safety objectives and priorities for the current week.
- Site Walkthrough:
- Conduct a comprehensive site inspection to identify hazards or unsafe practices.
- Take note of issues that require immediate and long-term actions.
- Team Briefing:
- Hold a meeting with supervisors and department heads to discuss safety concerns and updates.
- Share weekly safety goals and focus areas.
Tuesday: Training and Development
- Safety Training:
- Organize training sessions on topics like emergency response, proper PPE use, or handling hazardous materials.
- Update workers on new regulations or procedures.
- Incident Review:
- Investigate and analyze any incidents or near-misses from the past week.
- Document findings and share lessons learned with the team.
- Update Safety Records:
- Ensure training logs, certifications, and safety records are up to date.
Wednesday: Midweek Monitoring
- Focused Inspections:
- Perform targeted inspections in high-risk areas or departments.
- Check the functionality of safety equipment such as fire extinguishers, alarms, and first aid kits.
- Policy Review:
- Evaluate the effectiveness of current safety policies.
- Suggest updates or modifications to align with industry standards.
- Worker Feedback:
- Interact with employees to gather feedback on safety measures.
- Address their concerns and implement solutions where feasible.
Thursday: Risk Assessment and Planning
- Risk Assessments:
- Conduct detailed risk assessments for ongoing or upcoming projects.
- Collaborate with project managers to plan safer workflows.
- Emergency Preparedness:
- Review and update emergency response plans.
- Schedule emergency drills (e.g., fire, evacuation, or chemical spill).
- External Coordination:
- Coordinate with local authorities or external safety consultants, if required.
- Ensure compliance with regulatory requirements.
Friday: End-of-Week Review
- Weekly Safety Report:
- Prepare a detailed report summarizing the week’s safety activities, inspections, and incidents.
- Highlight trends, areas of improvement, and successes.
- Management Meeting:
- Present the weekly safety report to senior management.
- Discuss planned actions for unresolved issues or risks.
- Site Inspection:
- Conduct a final walkthrough to ensure that unresolved hazards are addressed.
- Verify that the site is safe for the weekend.
Weekend Preparations (Optional):
For operations that run during weekends:
- Assign safety responsibilities to on-call personnel.
- Prepare an action plan for weekend safety monitoring.
Key Weekly Focus Areas
- Compliance: Regularly verify adherence to local and international safety regulations.
- Training: Emphasize continuous learning and skill development for workers.
- Incident Prevention: Proactively address risks and hazards to minimize incidents.
- Documentation: Keep records organized and accessible for audits or reviews.
By maintaining a structured weekly routine, a Safety Officer ensures a safe working environment while fostering a culture of safety among employees.
Conclusion
A safety officer’s work is dynamic, challenging, and deeply rewarding. By staying proactive and engaged, they ensure workplaces are safer, healthier, and more productive.
The Role of a Safety Officer: Beyond Inspections and Audits
How to Become a Safety Manager Without a Degree in 2025
HSE Supervisor Salary in 2025
FAQs
What is the most critical part of a safety officer’s weekly work?
Conducting inspections and addressing hazards promptly is crucial.
How do safety officers handle emergencies?
They follow predefined protocols, coordinate with response teams, and ensure everyone’s safety.
How often do safety officers update their safety plans?
Plans are reviewed and updated as needed, often weekly or after significant incidents.
What tools do safety officers use for inspections?
They use checklists, inspection software, and monitoring equipment.
How can companies support their safety officers?
Providing resources, training, and a supportive culture helps safety officers excel.