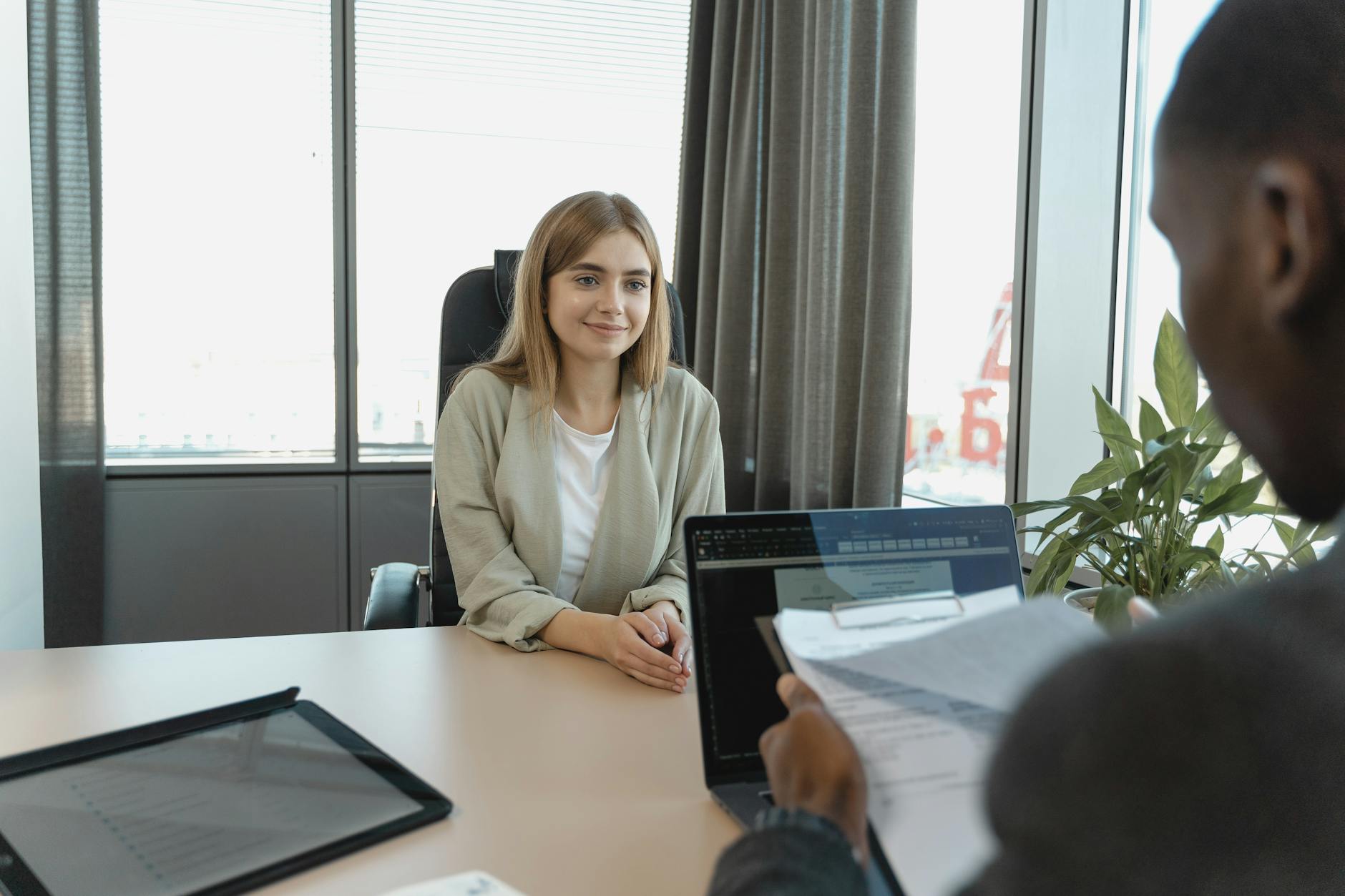
Top 100 Safety Manager Interview Questions and Answers 2024 | Free Download PDF
Introduction
Landing a job as a Safety Manager is a significant achievement in one’s career, particularly given the critical role this position plays in any organization. Whether you’re an experienced professional or just stepping into this role, preparing for the interview is key to success. This guide will cover the top 100 safety manager interview questions for 2024 and provide sample answers to help you nail the interview.
The Importance of a Safety Manager
Role of a Safety Manager in Various Industries
A Safety Manager ensures that an organization complies with safety regulations and that employees work in a safe environment. This role is vital across industries such as construction, manufacturing, oil and gas, and healthcare, where workplace hazards can lead to serious injuries or fatalities if not properly managed.
Skills and Qualities Required for a Safety Manager
To excel as a Safety Manager, you need a deep understanding of safety regulations, strong leadership skills, attention to detail, and the ability to communicate effectively with all levels of an organization. These skills help in creating and maintaining a safe work environment, which is the ultimate goal of any safety manager.
Preparing for the Safety Manager Interview
Researching the Company
Before attending any interview, it’s crucial to research the company. Understand its safety culture, the types of projects they handle, and the specific safety challenges they face. This knowledge will allow you to tailor your responses to show how your experience aligns with the company’s needs.
Understanding the Job Description
Carefully read the job description to understand the specific responsibilities and qualifications required. Highlight your relevant experience and be prepared to discuss how it matches the job requirements. This step ensures that you can confidently answer questions about your suitability for the role.
Reviewing Your Resume and Experience
Make sure you are familiar with every detail on your resume. Be ready to discuss your previous roles, responsibilities, and achievements. Focus on how your past experiences have prepared you for the Safety Manager role, particularly in terms of managing safety programs and compliance.
General Interview Questions
Tell me about yourself.
This is often the first question in an interview. Your response should be a concise summary of your professional background, focusing on your experience in safety management. Mention your key skills and how they align with the role you’re applying for.
Sample Answer:
“I have over 10 years of experience in safety management, primarily in the construction and manufacturing industries. My expertise includes conducting safety audits, implementing safety training programs, and ensuring compliance with OSHA regulations. I’m passionate about creating safe work environments and have a proven track record of reducing workplace accidents through proactive safety management.”
Why do you want to work as a Safety Manager?
Here, the interviewer wants to understand your motivation for pursuing this role. Focus on your passion for safety and your desire to make a difference in the workplace.
Sample Answer:
“I’ve always been passionate about ensuring that people work in safe environments. As a Safety Manager, I can directly influence workplace safety and help prevent accidents and injuries. I find it fulfilling to see the positive impact of effective safety programs on both employee well-being and company performance.”
What are your strengths and weaknesses?
This question assesses your self-awareness and how you handle your weaknesses. Be honest but strategic in your response.
Sample Answer:
“My greatest strength is my attention to detail, which is crucial in safety management. I’m thorough in conducting audits and identifying potential hazards. However, I’ve found that I can be overly cautious at times, which I’m working on by improving my decision-making speed without compromising safety.”
Technical Safety Manager Questions
How do you ensure compliance with OSHA regulations?
This question tests your knowledge of OSHA regulations and your ability to ensure compliance.
Sample Answer:
“I ensure compliance with OSHA regulations by staying updated on any changes and conducting regular training sessions for employees. I also perform routine inspections and audits to identify and rectify any non-compliance issues. Additionally, I maintain detailed records of all safety-related activities to ensure transparency and accountability.”
Can you explain the process of a safety audit?
Safety audits are a crucial part of a Safety Manager’s role. Be prepared to discuss the process in detail.
Sample Answer:
“The safety audit process begins with planning, where I define the scope and objectives. Next, I gather relevant documents, such as previous audit reports, safety records, and compliance manuals. During the audit, I conduct on-site inspections, interview employees, and observe work practices. After the audit, I analyze the findings and prepare a report highlighting any non-compliance issues and recommendations for improvement. Finally, I follow up to ensure that corrective actions are implemented.”
Steps involved in conducting a safety audit
- Planning the Audit: Define the scope, objectives, and methodology.
- Document Review: Gather and review relevant safety documentation.
- On-site Inspection: Observe work practices and interview employees.
- Data Analysis: Analyze findings to identify non-compliance and areas for improvement.
- Reporting: Prepare a detailed report with recommendations.
- Follow-Up: Ensure that corrective actions are implemented.
Common pitfalls to avoid during a safety audit
- Failing to engage employees during the audit.
- Overlooking minor hazards that could escalate.
- Inadequate documentation of findings and corrective actions.
Behavioral Safety Manager Questions
Describe a time when you had to handle a safety violation.
Behavioral questions are designed to assess how you handle specific situations based on past experiences.
Sample Answer:
“In one of my previous roles, I encountered a situation where an employee consistently ignored safety protocols, putting themselves and others at risk. I immediately addressed the issue by discussing it with the employee, understanding their concerns, and re-educating them on the importance of following safety procedures. I also implemented additional supervision to ensure compliance. As a result, the employee’s behavior improved, and we avoided potential accidents.”
How do you manage conflict within your team?
Conflict resolution is a key skill for any manager, including Safety Managers.
Sample Answer:
“I believe in addressing conflicts early and directly. I encourage open communication within my team and make sure everyone feels heard. When conflicts arise, I bring the involved parties together to discuss their perspectives and work towards a mutually acceptable solution. I focus on the underlying issues rather than the symptoms to prevent future conflicts.”
Give an example of a successful safety program you implemented.
This question allows you to showcase your achievements in safety management.
Sample Answer:
“At my previous company, I implemented a comprehensive safety program that included regular training, safety drills, and a reward system for reporting hazards. This program significantly reduced workplace accidents by 40% within the first year. The key to its success was engaging employees at all levels and creating a safety-first culture.”
1. General Safety Management Questions
Q1: What inspired you to pursue a career in safety management?
A1: “My passion for creating a safe work environment and protecting people from potential hazards inspired me to pursue safety management. I believe that a safe workplace not only protects employees but also boosts morale and productivity.”
Q2: How do you stay updated with the latest safety regulations and standards?
A2: “I regularly attend workshops, webinars, and conferences, and I subscribe to industry journals and newsletters. I also participate in professional networks where I can learn and share best practices.”
Q3: Can you explain the role of a safety manager in a company?
A3: “A safety manager is responsible for developing, implementing, and maintaining safety programs to ensure compliance with regulations. They also conduct risk assessments, investigate incidents, and train employees on safety protocols to prevent accidents and injuries.”
Q4: What is your experience with OSHA regulations?
A4: “I have extensive experience with OSHA regulations, including conducting compliance audits, creating safety plans that adhere to OSHA standards, and ensuring that all safety protocols are up-to-date with current regulations.”
2. Risk Assessment and Management
Q5: How do you conduct a risk assessment in the workplace?
A5: “I start by identifying potential hazards in the workplace. Then, I evaluate the risks associated with these hazards, prioritize them based on their severity, and develop a plan to mitigate or eliminate them. I also ensure that all assessments are documented and reviewed regularly.”
Q6: Can you describe a situation where you identified a potential hazard and how you addressed it?
A6: “In a previous role, I noticed that employees were frequently slipping on a particular floor. I investigated and found that the floor material became slippery when wet. I implemented a plan to improve drainage, applied anti-slip coatings, and provided additional training to employees on handling spills.”
Q7: How do you ensure that risk assessments are effectively communicated to all employees?
A7: “I ensure that risk assessments are communicated through clear, concise reports, regular safety meetings, and visual aids like posters and signs. I also make sure to involve employees in the risk assessment process so they understand the importance of each safety measure.”
Q8: What methods do you use to prioritize risks in your assessments?
A8: “I prioritize risks based on their potential impact and the likelihood of occurrence. High-impact, high-probability risks are addressed immediately, while lower-priority risks are managed over time. This approach ensures that the most serious hazards are mitigated first.”
3. Incident Investigation and Reporting
Q9: How do you approach investigating an incident or accident in the workplace?
A9: “I follow a systematic approach that includes securing the scene, gathering evidence, interviewing witnesses, and analyzing data to determine the root cause. I then develop corrective actions to prevent recurrence and document the findings in a detailed report.”
Q10: Can you give an example of a successful incident investigation you conducted?
A10: “I once investigated a machinery-related injury where an employee was hurt by a malfunctioning device. Through interviews and a review of maintenance records, I discovered a lapse in the regular maintenance schedule. We implemented a stricter maintenance protocol, and similar incidents were prevented.”
Q11: How do you ensure that incident reports are accurate and complete?
A11: “I ensure accuracy by thoroughly reviewing all aspects of the incident, including witness statements, physical evidence, and timelines. I also encourage those involved to review and verify the report before it’s finalized.”
Q12: What is the importance of root cause analysis in incident investigation?
A12: “Root cause analysis is crucial because it helps identify the underlying issues that lead to incidents. By addressing these root causes, we can implement more effective preventive measures, reducing the likelihood of future incidents.”
4. Compliance and Regulations
Q13: How do you ensure that your company complies with all safety regulations?
A13: “I ensure compliance by regularly reviewing and updating safety policies to align with current regulations, conducting internal audits, and providing continuous training for employees on regulatory requirements.”
Q14: How would you handle a situation where your company is non-compliant with safety regulations?
A14: “I would immediately address the non-compliance issue by identifying the root cause, implementing corrective actions, and ensuring that all employees are informed of the changes. I would also schedule follow-up audits to ensure continued compliance.”
Q15: What steps would you take if you discovered a violation of OSHA standards?
A15: “Upon discovering a violation, I would document it, report it to the necessary internal stakeholders, and take immediate corrective action to rectify the situation. I would also review and update our safety protocols to prevent future violations.”
Q16: Can you explain the importance of documentation in maintaining compliance?
A16: “Documentation is essential for maintaining compliance as it provides a record of all safety activities, training, audits, and incidents. It serves as evidence that the company is following regulations and helps identify areas that need improvement.”
5. Safety Training and Education
Q17: How do you develop a safety training program?
A17: “I start by assessing the specific needs of the workplace, identifying potential hazards, and determining the skills and knowledge employees need. I then create training materials that are engaging and relevant, incorporating hands-on activities and real-world examples.”
Q18: How do you ensure that safety training is effective?
A18: “I measure the effectiveness of safety training by conducting pre- and post-training assessments, gathering feedback from participants, and observing workplace practices. Continuous monitoring and follow-up training sessions are also important to reinforce learning.”
Q19: Can you provide an example of a successful safety training initiative you’ve led?
A19: “I led a safety training initiative focused on lockout/tagout procedures. After the training, we saw a significant decrease in machinery-related incidents. The success was due to hands-on practice sessions, clear instructions, and regular refresher courses.”
Q20: How do you handle employees who are resistant to safety training?
A20: “I address resistance by explaining the importance of safety training and its impact on their well-being. I also try to make the training more engaging by including interactive elements and real-life scenarios that they can relate to.”
6. Communication and Leadership
Q21: How do you communicate safety policies to employees?
A21: “I communicate safety policies through multiple channels, including email, company intranet, posters, and regular safety meetings. I also ensure that policies are explained in clear, simple language, and provide opportunities for employees to ask questions.”
Q22: How do you encourage a culture of safety in the workplace?
A22: “I encourage a culture of safety by leading by example, recognizing and rewarding safe behavior, and involving employees in safety decision-making. Regular communication and training also reinforce the importance of safety.”
Q23: Can you describe your leadership style when it comes to safety management?
A23: “My leadership style is collaborative and supportive. I believe in empowering employees to take ownership of their safety responsibilities while providing the guidance and resources they need to succeed.”
Q24: How do you handle conflicts between safety protocols and production goals?
A24: “I address conflicts by finding a balance that prioritizes safety without compromising productivity. I work closely with production teams to develop solutions that meet safety standards while allowing for efficient operations.”
7. Emergency Response and Preparedness
Q25: How do you prepare a workplace for emergency situations?
A25: “I prepare the workplace by developing comprehensive emergency response plans, conducting regular drills, and ensuring that all employees are trained on emergency procedures. I also coordinate with local emergency services to ensure a prompt response in case of an incident.”
Q26: Can you give an example of how you handled an emergency situation in the workplace?
A26: “In a previous role, we had a chemical spill that required an immediate evacuation. I coordinated the evacuation, ensured that all employees were accounted for, and worked with the emergency response team to contain the spill. The situation was handled quickly and safely.”
Q27: What is the importance of regular emergency drills?
A27: “Regular emergency drills are essential because they prepare employees for real-life emergencies, ensuring that they know what to do and where to go. Drills also help identify any weaknesses in the emergency response plan, allowing for improvements.”
Q28: How do you ensure that all employees are aware of emergency procedures?
A28: “I ensure awareness by providing regular training, distributing easy-to-understand emergency procedure guides, and conducting unannounced drills. I also make sure that emergency exits and equipment are clearly marked and accessible.”
8. Specific Industry-Related Questions
Q29: How do you manage safety in a high-risk industry, such as construction or oil and gas?
A29: “Managing safety in high-risk industries requires rigorous risk assessments, strict adherence to safety protocols, and continuous monitoring. I focus on training employees on the specific hazards they may encounter and ensuring that all equipment is properly maintained.”
Q30: Can you discuss your experience with safety management in (specific industry)?
A30: “I have extensive experience in the construction industry, where I implemented safety programs that reduced incident rates by 30%. My approach included regular site inspections, safety training tailored to construction hazards, and close collaboration with site managers.”
9. Behavioral and Situational Questions
Q31: Describe a time when you had to persuade management to implement a safety initiative.
A31: “I once had to persuade management to invest in ergonomic equipment to reduce repetitive strain injuries. I presented data showing the long-term cost savings from reduced injuries and improved employee productivity. The initiative was approved, and we saw a significant reduction in injury-related downtime.”
Q32: How do you handle a situation where an employee consistently disregards safety protocols?
A32: “I address the issue by having a private conversation with the employee to understand their reasons for disregarding protocols. I reinforce the importance of safety and provide additional training if necessary. If the behavior continues, I follow the company’s disciplinary procedures.”
Q33: How do you stay calm and focused during a safety crisis?
A33: “During a safety crisis, I stay calm by focusing on the immediate tasks at hand and following the established emergency procedures. I prioritize clear communication with the team and emergency responders to ensure a coordinated response.”
Q34: Describe a time when you had to make a quick decision in a safety-related situation.
A34: “During a fire alarm in a facility, I had to quickly decide whether to evacuate or investigate further. I opted for a cautious evacuation, which turned out to be the right choice as there was a small fire in one of the storage rooms. The quick decision helped prevent injuries.”
10. Continuous Improvement and Innovation
Q35: How do you stay innovative in your approach to safety management?
A35: “I stay innovative by continuously researching new safety technologies, attending industry conferences, and networking with other safety professionals. I’m always looking for ways to improve safety processes, whether through new tools, training methods, or data analysis techniques.”
Q36: Can you give an example of a new safety initiative you introduced that had a positive impact?
A36: “I introduced a digital incident reporting system that streamlined the reporting process and provided real-time data analysis. This initiative led to quicker response times and more accurate incident tracking, resulting in a 15% reduction in workplace accidents.”
Q37: How do you measure the success of your safety programs?
A37: “I measure success through key performance indicators such as incident rates, near-miss reports, employee feedback, and compliance audit results. Regular reviews of these metrics help me adjust safety programs as needed to achieve continuous improvement.”
Q38: What role does employee feedback play in your safety management approach?
A38: “Employee feedback is crucial because it provides insights into potential hazards and the effectiveness of safety programs. I encourage open communication and regularly solicit feedback through surveys and safety committees to ensure that all voices are heard.”
11. Industry-Specific Regulatory Knowledge
Q39: What is the importance of the (specific industry regulation) in your role?
A39: “The (specific industry regulation) is critical because it sets the standards for safety practices in our industry. Compliance ensures that we are protecting our employees, avoiding legal penalties, and maintaining our reputation as a safe and responsible company.”
Q40: Can you discuss your experience with (specific safety regulation or standard)?
A40: “I have extensive experience with the ISO 45001 standard, which focuses on occupational health and safety management systems. Implementing this standard in my previous role helped us reduce workplace injuries by 25% and improved overall safety culture.”
12. Advanced Safety Management Topics
Q41: How do you integrate safety management into the overall business strategy?
A41: “I integrate safety management into the business strategy by aligning safety goals with organizational objectives. This includes showing how safety improvements can lead to cost savings, enhance productivity, and improve employee satisfaction, thereby contributing to the company’s success.”
Q42: What is your approach to managing safety in a global organization?
A42: “Managing safety in a global organization requires understanding the different regulatory environments and cultural attitudes towards safety in each location. I develop global safety standards while allowing for local adaptations to ensure compliance and effectiveness across all regions.”
Q43: How do you handle the safety challenges of remote or isolated work environments?
A43: “In remote or isolated environments, I focus on ensuring that employees have access to the necessary safety resources, including communication tools, emergency response plans, and regular check-ins. I also implement specific training for the unique hazards they may face.”
Q44: Can you discuss your experience with managing contractor safety?
A44: “Managing contractor safety involves ensuring that all contractors are fully trained and compliant with our safety standards before they start work. I conduct regular audits and maintain open communication with contractors to ensure ongoing compliance.”
13. Technology and Safety Management
Q45: How do you incorporate technology into safety management?
A45: “I incorporate technology by using safety management software to track incidents, conduct audits, and analyze data. I also explore new technologies, such as wearable devices that monitor worker health and safety in real-time, to enhance our safety programs.”
Q46: Can you give an example of how technology improved safety in your previous role?
A46: “In my previous role, I implemented a drone-based inspection system for high-risk areas, which significantly reduced the need for employees to enter hazardous environments. This technology not only improved safety but also increased inspection efficiency.”
Q47: What is the role of data analysis in safety management?
A47: “Data analysis plays a critical role in identifying trends, predicting potential hazards, and measuring the effectiveness of safety programs. By analyzing incident reports, near-misses, and safety audit results, I can make informed decisions to improve workplace safety.”
Q48: How do you ensure the cybersecurity of safety management systems?
A48: “Ensuring cybersecurity involves working closely with the IT department to implement strong security protocols, regularly updating software, and training employees on best practices for data protection. This ensures that our safety management systems remain secure and effective.”
14. Environmental Safety
Q49: How do you manage environmental safety in the workplace?
A49: “I manage environmental safety by ensuring compliance with environmental regulations, conducting regular audits, and implementing waste reduction and pollution prevention programs. I also work to raise employee awareness about environmental impact and sustainable practices.”
Q50: Can you discuss your experience with hazardous materials management?
A50: “I have experience managing hazardous materials, including ensuring proper labeling, storage, and disposal according to regulatory requirements. I also provide training to employees on how to handle hazardous materials safely and respond to spills or exposures.”
15. Final Interview Questions
Q51: What do you consider your greatest achievement in your safety management career?
A51: “My greatest achievement was leading a safety initiative that resulted in a 50% reduction in workplace accidents over two years. This success was achieved through a combination of rigorous training, improved communication, and a strong focus on hazard identification and mitigation.”
Q52: How do you see the role of safety manager evolving in the next five years?
A52: “I see the role of safety manager evolving with advancements in technology, greater emphasis on mental health and well-being, and an increasing focus on sustainability. Safety managers will need to be adaptable and continuously update their skills to meet these emerging challenges.”
Q53: Why do you believe you are the best candidate for this safety manager position?
A53: “I believe I am the best candidate because of my extensive experience, proven track record in reducing workplace incidents, and my ability to lead and inspire teams to prioritize safety. My approach is proactive, data-driven, and centered on continuous improvement.”
Q54: What is your approach to balancing the needs of the business with safety requirements?
A54: “My approach is to integrate safety into all aspects of business operations, showing how safety initiatives can lead to long-term benefits like increased productivity, reduced costs, and improved employee morale. I work collaboratively with all departments to ensure safety is seen as a business enabler.”
16. Leadership and Team Management
Q55: How do you manage a team of safety professionals?
A55: “I manage a team by fostering a collaborative environment where everyone feels valued and heard. I set clear expectations, provide ongoing training and development opportunities, and encourage open communication. I also recognize and reward team members for their contributions.”
Q56: Can you describe a situation where you had to lead a team through a difficult safety challenge?
A56: “I led a team through a major restructuring that impacted safety procedures. I worked closely with the team to develop new protocols, provided additional support and training, and ensured that everyone was on board with the changes. The transition was smooth, and we maintained a high level of safety throughout the process.”
Q57: How do you handle performance issues within your safety team?
A57: “I handle performance issues by first understanding the root cause, whether it’s a lack of training, resources, or motivation. I then work with the individual to create a performance improvement plan, providing the necessary support and follow-up to help them succeed.”
Q58: What role does mentorship play in your approach to safety management?
A58: “Mentorship is a key component of my approach. I believe in guiding and developing the next generation of safety professionals by sharing my knowledge, providing opportunities for growth, and offering constructive feedback. This helps build a strong, capable team that can continue to advance safety initiatives.”
Q59: How do you manage stress and maintain work-life balance in a demanding safety management role?
A59: “I manage stress by staying organized, prioritizing tasks, and delegating when necessary. I also make sure to take breaks, stay active, and maintain a healthy work-life balance. This approach helps me stay focused and effective in my role.”
17. Advanced Risk Management
Q60: How do you approach risk management in a rapidly changing environment?
A60: “In a rapidly changing environment, I focus on staying agile by continuously monitoring potential risks, adapting safety protocols quickly, and ensuring that employees are informed and prepared for any changes. This proactive approach helps mitigate risks before they become major issues.”
Q61: Can you discuss your experience with implementing a risk management framework?
A61: “I have implemented risk management frameworks in several organizations, focusing on identifying, assessing, and mitigating risks across all areas of the business. My approach includes regular reviews, employee training, and integrating risk management into the overall business strategy.”
Q62: How do you assess the effectiveness of risk management strategies?
A62: “I assess effectiveness by monitoring key metrics such as incident rates, near-misses, and compliance audit results. I also gather feedback from employees and conduct regular reviews of risk management strategies to identify areas for improvement.”
Q63: How do you involve employees in the risk management process?
A63: “I involve employees by encouraging them to report potential hazards, participate in risk assessments, and provide feedback on safety measures. Their involvement ensures that risk management strategies are practical, effective, and widely supported.”
18. Continuous Improvement and Auditing
Q64: How do you approach continuous improvement in safety management?
A64: “I approach continuous improvement by regularly reviewing safety performance data, conducting audits, and staying informed about industry best practices. I also encourage a culture of learning and innovation, where employees are empowered to suggest and implement safety improvements.”
Q65: Can you describe your experience with safety audits?
A65: “I have extensive experience conducting safety audits, both internal and external. My approach involves thorough preparation, detailed inspections, and clear reporting. I also ensure that any findings are addressed promptly, with corrective actions implemented to improve safety.”
Q66: How do you ensure that safety improvements are sustained over the long term?
A66: “I ensure sustainability by embedding safety improvements into the company’s culture, policies, and procedures. Continuous training, regular reviews, and employee involvement are key factors in maintaining and building on safety improvements over time.”
19. Personal and Professional Development
Q67: How do you stay motivated and continue developing your skills as a safety manager?
A67: “I stay motivated by setting personal and professional goals, seeking out new challenges, and continuously learning. I regularly attend industry conferences, pursue certifications, and stay connected with other safety professionals to stay at the forefront of the field.”
Q68: Can you discuss a time when you had to learn a new skill or concept quickly for your role?
A68: “When I transitioned to a new industry, I had to quickly learn the specific safety regulations and practices. I immersed myself in industry literature, sought out training opportunities, and connected with experienced colleagues. This allowed me to get up to speed quickly and effectively manage safety in the new environment.”
20. Final Thoughts and Vision for Safety
Q69: What is your vision for the future of safety management?
A69: “My vision for the future of safety management includes greater integration of technology, a stronger focus on mental health and well-being, and a more proactive approach to risk management. I believe that safety will continue to evolve as a critical component of business success, and I am excited to be part of that evolution.”
Q70: How would you like to see your career develop in the next few years?
A70: “In the next few years, I hope to take on more leadership responsibilities, mentor other safety professionals, and continue driving innovation in safety management. I’m also interested in contributing to industry standards and sharing my knowledge through speaking engagements and publications.”
Q71: What legacy would you like to leave as a safety manager?
A71: “I would like to leave a legacy of creating safer workplaces, fostering a strong safety culture, and developing the next generation of safety leaders. My goal is to make a lasting impact that improves the lives of employees and sets a high standard for safety management.”
21. Additional Questions
Q72: How do you ensure that safety protocols are adapted to new or evolving threats?
A72: “I ensure adaptability by staying informed about emerging risks, conducting regular reviews of safety protocols, and involving employees in discussions about potential changes. This proactive approach allows us to respond quickly and effectively to new threats.”
Q73: What is your experience with managing safety in multi-site operations?
A73: “Managing safety in multi-site operations requires strong communication, standardized safety procedures, and regular site visits. I focus on ensuring consistency across all sites while allowing for site-specific adaptations to address unique risks.”
Q74: Can you discuss your experience with regulatory inspections?
A74: “I have extensive experience preparing for and managing regulatory inspections. My approach includes thorough preparation, clear documentation, and open communication with inspectors. I also ensure that any findings are addressed promptly to maintain compliance.”
Q75: How do you balance the need for safety with operational efficiency?
A75: “I balance safety and efficiency by integrating safety into operational planning, identifying areas where safety improvements can enhance productivity, and working closely with operations teams to develop solutions that meet both safety and business goals.”
Q76: What is your approach to managing safety during organizational changes?
A76: “During organizational changes, I focus on maintaining clear communication, involving employees in the change process, and ensuring that safety protocols are updated and reinforced. This approach helps prevent disruptions and ensures that safety remains a priority.”
Q77: How do you handle the challenge of ensuring safety compliance across different departments?
A77: “I handle this challenge by fostering strong relationships with department heads, providing regular training and updates, and ensuring that safety protocols are clearly communicated and understood by all departments. Regular audits and feedback sessions also help maintain compliance.”
Q78: What is your experience with managing safety in remote work environments?
A78: “Managing safety in remote work environments involves ensuring that employees have the necessary resources and training to work safely from home. I focus on ergonomic assessments, mental health support, and regular check-ins to ensure that remote workers are safe and supported.”
Q79: How do you ensure that safety protocols are understood and followed by all employees?
A79: “I ensure understanding and compliance by providing clear, accessible training, using multiple communication channels, and involving employees in the development of safety protocols. Regular follow-ups, reminders, and positive reinforcement also help maintain compliance.”
Q80: Can you discuss a time when you had to advocate for safety in the face of resistance?
A80: “I once had to advocate for a new safety initiative that required additional investment. Despite initial resistance, I presented data showing the long-term benefits and cost savings, and I worked to gain support from key stakeholders. The initiative was eventually approved and led to significant safety improvements.”
22. Crisis Management
Q81: How do you prepare for and manage a safety crisis?
A81: “I prepare for a crisis by developing and regularly updating a comprehensive crisis management plan, conducting drills, and ensuring that all employees are trained on their roles in an emergency. During a crisis, I focus on clear communication, rapid response, and coordinating with emergency services.”
Q82: Can you describe your experience with post-crisis recovery and review?
A82: “After a crisis, I focus on supporting affected employees, reviewing the response to identify areas for improvement, and updating safety protocols as needed. I also ensure that any lessons learned are communicated to all employees and incorporated into future crisis planning.”
23. Industry Specific
Q83: How do you manage safety in high-risk industries such as oil and gas?
A83: “In high-risk industries like oil and gas, I prioritize rigorous risk assessments, continuous monitoring, and strict adherence to safety protocols. I also focus on ensuring that all employees are well-trained and that safety equipment is properly maintained and regularly inspected.”
Q84: What is your experience with safety management in construction?
A84: “In construction, my experience includes implementing comprehensive safety programs, conducting regular site inspections, and ensuring compliance with all relevant regulations. I also work closely with contractors and subcontractors to ensure that safety standards are consistently applied across all projects.”
Q85: How do you ensure safety compliance in a manufacturing environment?
A85: “In a manufacturing environment, I focus on regular equipment inspections, thorough training for all employees, and continuous monitoring of safety practices. I also ensure that safety protocols are integrated into the manufacturing processes to prevent accidents and injuries.”
Q86: Can you discuss your experience with safety management in healthcare?
A86: “In healthcare, my experience includes managing safety protocols related to infection control, hazardous materials, and patient safety. I focus on ensuring compliance with all relevant regulations and providing ongoing training to healthcare staff on best practices.”
24. Technical and Process-Oriented
Q87: How do you approach the management of safety data and metrics?
A87: “I manage safety data by using software tools to track and analyze key metrics such as incident rates, near-misses, and compliance audit results. This data-driven approach allows me to identify trends, measure the effectiveness of safety programs, and make informed decisions.”
Q88: What is your experience with root cause analysis in safety management?
A88: “I have extensive experience with root cause analysis, which involves identifying the underlying causes of safety incidents and developing corrective actions to prevent recurrence. I use a systematic approach that includes gathering data, conducting interviews, and analyzing all contributing factors.”
Q89: How do you ensure that safety improvements are effectively implemented?
A89: “I ensure effective implementation by developing clear action plans, assigning responsibilities, and setting timelines for completion. I also monitor progress and provide support as needed to ensure that safety improvements are fully integrated into the organization’s operations.”
Q90: Can you discuss your experience with safety management software?
A90: “I have experience with various safety management software platforms that help streamline incident reporting, audit management, and data analysis. These tools are invaluable in maintaining a comprehensive and efficient safety management system.”
Q91: How do you manage the safety of subcontractors and temporary workers?
A91: “I manage the safety of subcontractors and temporary workers by ensuring they receive the same level of training and orientation as permanent employees. I also conduct regular audits and inspections to ensure that all safety standards are being met and that there is no disparity in safety practices.”
Q92: What is your approach to managing change in safety protocols?
A92: “My approach to managing change involves thorough planning, clear communication, and providing the necessary training and resources to support the transition. I also involve employees in the process to ensure that the changes are practical and effective.”
Q93: How do you ensure that safety audits lead to meaningful improvements?
A93: “I ensure that audits lead to improvements by developing action plans based on audit findings, assigning responsibilities, and following up on the implementation of corrective actions. I also review the effectiveness of these actions in subsequent audits.”
Q94: Can you discuss your experience with safety training programs?
A94: “I have developed and delivered numerous safety training programs tailored to specific industries and job roles. My approach includes interactive learning, practical exercises, and regular refreshers to ensure that all employees remain up-to-date on safety practices.”
Q95: How do you handle the challenge of maintaining safety standards during peak operational periods?
A95: “During peak periods, I focus on maintaining safety by increasing monitoring, providing additional resources and support, and ensuring that safety protocols are followed despite the increased workload. I also stress the importance of safety to all employees to prevent shortcuts or lapses.”
Q96: What is your experience with safety certifications and standards?
A96: “I have experience with various safety certifications and standards, including OSHA, ISO 45001, and industry-specific regulations. I ensure that my organization complies with these standards and pursue certifications that enhance our safety programs.”
25. Industry Knowledge and Expertise
Q97: How do you stay informed about changes in safety regulations?
A97: “I stay informed by subscribing to industry newsletters, attending conferences, participating in professional networks, and regularly reviewing updates from regulatory bodies. This helps me ensure that our safety programs remain compliant and up-to-date.”
Q98: What is your experience with safety management in different industries?
A98: “My experience spans multiple industries, including construction, manufacturing, oil and gas, and healthcare. I adapt my safety management approach to the specific risks and regulations of each industry, while applying core principles of hazard identification, risk mitigation, and continuous improvement.”
Q99: How do you ensure that safety standards are consistent across all levels of the organization?
A99: “I ensure consistency by developing clear safety policies and procedures, providing regular training, and conducting audits across all levels of the organization. I also encourage a strong safety culture where everyone, from top management to frontline workers, is committed to upholding safety standards.”
Q100: Can you discuss your experience with managing safety during major projects or events?
A100: “Managing safety during major projects or events requires thorough planning, clear communication, and close monitoring of safety practices. I focus on conducting risk assessments, ensuring that all safety measures are in place, and providing additional resources as needed to maintain a safe environment throughout the project or event.”
Conclusion
In conclusion, preparing for a Safety Manager interview involves not only understanding the technical aspects of the job but also demonstrating your ability to lead, manage, and motivate a team. By familiarizing yourself with these top 100 interview questions and sample answers, you can confidently showcase your skills and experience, making you a strong candidate for the role.
Safety Manager Interview: Why Should We Hire You as a Safety Manager?
Safety Supervisor Interview: Why Should We Hire You as a Safety Supervisor?
Safety Engineer Interview: Why Should We Hire You as a Safety Engineer?
Safety Officer Interview: Why Should We Hire You as a Safety Officer?
Safety Manager: 30 Safety Manager Interview Questions (With Sample Answers)
FAQs
What are the most common safety manager interview questions?
Common questions include “Tell me about yourself,” “Why do you want to work as a Safety Manager?” and “How do you ensure compliance with safety regulations?”
How can I improve my chances of getting hired as a safety manager?
You can improve your chances by thoroughly researching the company, understanding the job description, and preparing detailed answers to potential interview questions. Highlight your relevant experience and skills, and demonstrate your passion for safety.
What should I wear to a safety manager interview?
For a safety manager interview, it’s best to wear professional attire, such as a suit or business dress. Dressing professionally shows that you take the interview seriously and are ready to step into a leadership role.
How can I showcase my leadership skills in the interview?
You can showcase your leadership skills by discussing your experience in managing teams, implementing safety programs, and resolving conflicts. Provide specific examples of how you’ve motivated your team and improved safety outcomes.
What are the most important qualities of a successful safety manager?
The most important qualities of a successful safety manager include attention to detail, strong communication skills, leadership ability, and a deep understanding of safety regulations. These qualities enable a safety manager to effectively oversee safety programs and ensure a safe work environment.
I need nebosh igc gide line syllabus and pattern