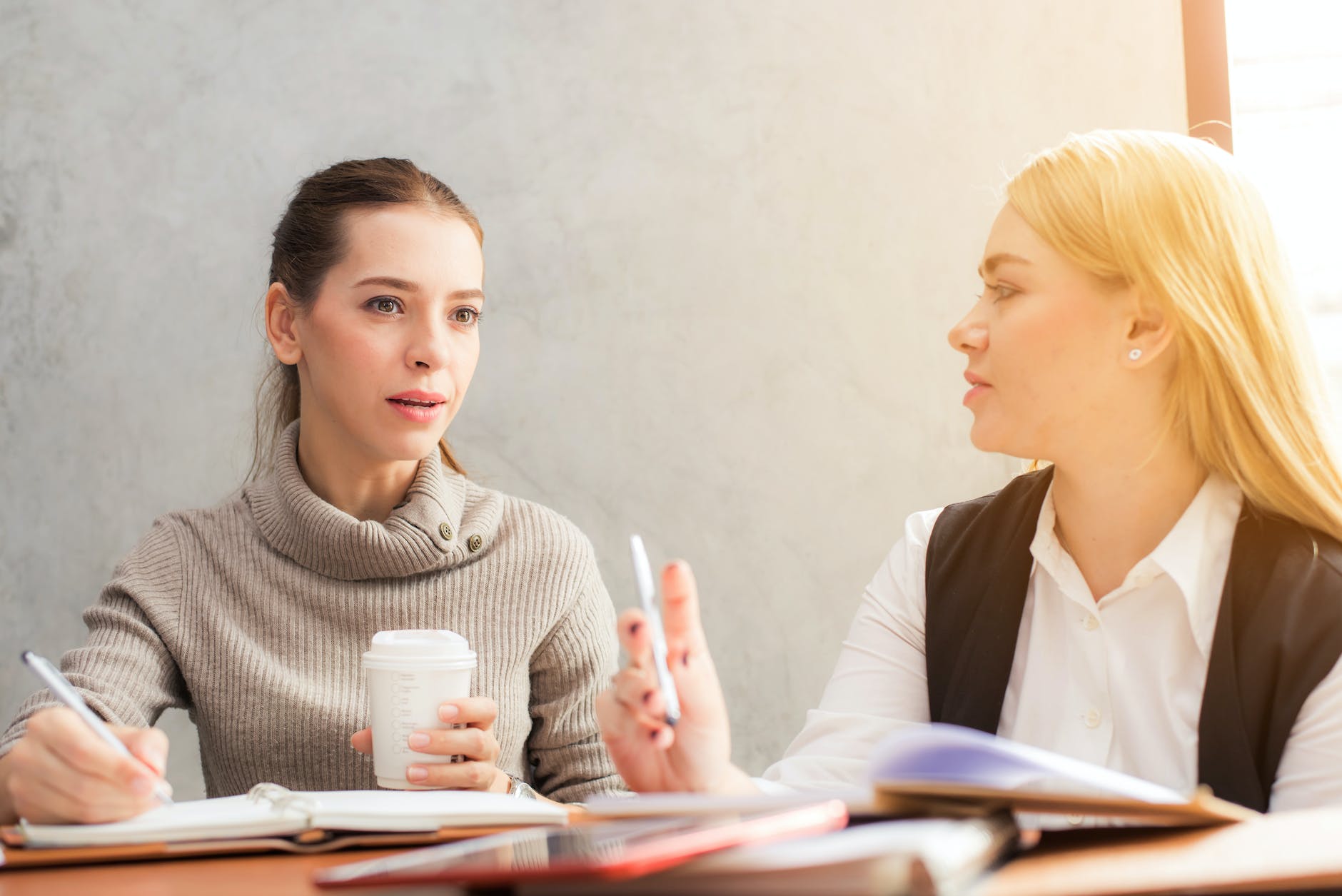
Technical Safety Interview Questions
In today’s competitive job market, technical safety has become a paramount concern across industries. This concern has led to an increase in technical safety interview questions aimed at evaluating a candidate’s understanding of safety protocols, emergency responses, and risk management.
Types of Technical Safety Interview Questions
Employers often use various types of questions to assess a candidate’s suitability for roles involving safety protocols. Behavioral-based questions delve into past experiences, situational questions assess decision-making, while technical knowledge-based questions evaluate specific safety knowledge.
Behavioral-based questions
These focus on a candidate’s previous experiences in handling safety-related situations. For instance, “Describe a time when you identified and rectified a safety hazard in your previous role.”
Situational questions
These present hypothetical scenarios to gauge how candidates would respond in safety-critical situations. An example could be, “If you witnessed a safety violation by a colleague, how would you address it?”
Technical knowledge-based questions
These assess a candidate’s grasp of safety regulations, protocols, and their ability to apply them practically. An example might be, “Explain the steps you’d take during an emergency evacuation.”
Key Areas Covered in Technical Safety Interview Questions
Technical safety interview questions often focus on essential areas crucial for maintaining a safe work environment. Candidates should be well-versed in risk assessment, understanding safety protocols, and handling emergency scenarios.
Risk assessment and management
Employers look for candidates capable of identifying potential risks and implementing strategies to mitigate them effectively.
Understanding safety protocols
Having a comprehensive understanding of safety protocols ensures adherence to industry standards, fostering a safe working environment.
Emergency response scenarios
Candidates should demonstrate their ability to handle emergency situations calmly and efficiently, ensuring the safety of themselves and others.
Top 10 Technical Safety Interview Questions and Answers
Here are some technical safety interview questions along with sample answers:
- What is a hazard analysis? Answer: Hazard analysis is a systematic process used to identify potential hazards in a workplace, assess the risks associated with those hazards, and implement controls to mitigate or eliminate them. It involves identifying, evaluating, and controlling workplace hazards to ensure the safety of employees.
- Explain the hierarchy of controls in safety management.Answer: The hierarchy of controls outlines methods for managing and controlling workplace hazards. It consists of five levels:
- Elimination: Removing the hazard entirely from the workplace.
- Substitution: Replacing the hazard with a less hazardous alternative.
- Engineering controls: Implementing physical changes to isolate people from the hazard.
- Administrative controls: Changing work practices or policies to reduce exposure to the hazard.
- Personal protective equipment (PPE): Providing equipment to protect individuals from the hazard when other controls are not feasible.
- How do you conduct a Job Safety Analysis (JSA)?Answer: A Job Safety Analysis involves breaking down a job into specific tasks, identifying potential hazards associated with each task, and determining preventive measures to control those hazards. The steps include:
- Selecting the job to be analyzed.
- Breaking the job down into steps.
- Identifying potential hazards for each step.
- Developing preventive measures to mitigate the identified hazards.
- Implementing and communicating safety measures to workers.
- What are some common safety metrics used to assess workplace safety?Answer: Common safety metrics include:
- Lost Time Injury Frequency Rate (LTIFR): Measures the number of lost time injuries per million hours worked.
- Total Recordable Incident Rate (TRIR): Calculates the number of recordable incidents per 100 full-time employees within a given period.
- Near-Miss Reporting Rate: Tracks the number of reported near-miss incidents, indicating potential hazards and risks.
- Safety Compliance Percentage: Measures the level of adherence to safety protocols and regulations.
- How do you handle a situation where an employee refuses to follow safety protocols? Answer: Addressing this situation involves understanding the employee’s concerns, reiterating the importance of safety, and explaining the consequences of not following protocols. It’s essential to listen actively, provide additional training if needed, and emphasize the collective responsibility for safety. If the refusal persists, involving higher management or HR for further guidance or disciplinary action might be necessary.
- What steps would you take to investigate a workplace accident?Answer: Conducting a thorough investigation involves several steps:
- Securing the accident scene to preserve evidence.
- Interviewing witnesses and involved parties to gather firsthand information.
- Examining records, including safety protocols and equipment maintenance logs.
- Analyzing the sequence of events leading to the accident.
- Identifying root causes and contributing factors.
- Developing corrective actions to prevent similar incidents in the future.
- Explain the concept of safety culture and how it impacts an organization. Answer: Safety culture refers to the shared values, beliefs, and attitudes regarding safety within an organization. It influences how employees perceive and prioritize safety in their daily activities. A positive safety culture fosters open communication, active participation in safety initiatives, and a proactive approach to identifying and addressing hazards. It enhances employee morale, reduces accidents, and contributes to overall organizational success.
- Describe the importance of conducting regular safety inspections.Answer: Regular safety inspections are crucial as they:
- Identify potential hazards and risks in the workplace.
- Ensure compliance with safety regulations and standards.
- Provide opportunities to assess the effectiveness of existing safety measures.
- Proactively address safety concerns before they lead to accidents or injuries.
- Demonstrate the organization’s commitment to maintaining a safe work environment.
- How would you prioritize safety when working on a tight deadline or under pressure to meet production goals?Answer: Safety should never be compromised, even when facing time constraints or production pressures. To prioritize safety:
- Communicate the importance of safety to all involved parties.
- Allocate resources for both safety measures and production needs.
- Evaluate and adjust deadlines or work processes to accommodate necessary safety measures.
- Empower employees to speak up if they perceive any safety risks.
- Reiterate that ensuring a safe workplace is essential for the long-term success and well-being of everyone involved.
- Discuss your experience with implementing safety training programs. Answer: I have experience designing and implementing safety training programs tailored to specific workplace hazards. This involves:
- Assessing the needs of the workforce and identifying key areas for training.
- Developing comprehensive training materials, including presentations, manuals, and hands-on demonstrations.
- Conducting interactive training sessions to engage employees and ensure understanding.
- Evaluating the effectiveness of training through assessments and feedback mechanisms.
- Continuously updating and improving training programs based on evolving safety requirements and feedback.
These responses aim to demonstrate a strong understanding of safety principles and practical experience in implementing safety measures within the workplace.
Tips for Excelling in Technical Safety Interviews
To excel in technical safety interviews, candidates should consider the following tips:
- Research and preparation: Familiarize yourself with industry-specific safety standards and regulations.
- Problem-solving abilities: Showcase your ability to identify and resolve safety issues proactively.
- Communication skills: Highlight your capacity to effectively communicate safety procedures and concerns.
Conclusion
Technical safety interview questions serve as a crucial tool for employers to gauge a candidate’s readiness to prioritize safety in their role. It’s imperative for candidates to not only understand safety protocols but also demonstrate practical application and problem-solving abilities.
Safety should always remain at the forefront of any work environment, and candidates who exhibit a strong understanding and commitment to safety protocols stand out in technical safety interviews.
Oil and Gas HSE Interview Questions and Answers
100 HSE Interview Questions and Answers
How do I handle a question I don’t know the answer to during an interview?
Frequently Asked Questions (FAQs)
- Q: Are technical safety interview questions only for specific industries? A: No, technical safety awareness is essential across various sectors, making these questions relevant in many industries.
- Q: How can I prepare for technical safety interview questions? A: Research industry-specific safety standards, practice situational responses, and reflect on past safety-related experiences.
- Q: What if I lack practical safety experience? A: Emphasize transferable skills like problem-solving, communication, and willingness to learn and adapt to safety protocols.
- Q: Should I only focus on technical knowledge or also on soft skills in these interviews? A: Both are important. While technical knowledge is crucial, soft skills like communication and problem-solving enhance your candidacy.
- Q: Can I ask questions about safety procedures during the interview? A: Absolutely! Demonstrating interest by asking thoughtful questions about safety shows your commitment to the role’s requirements.