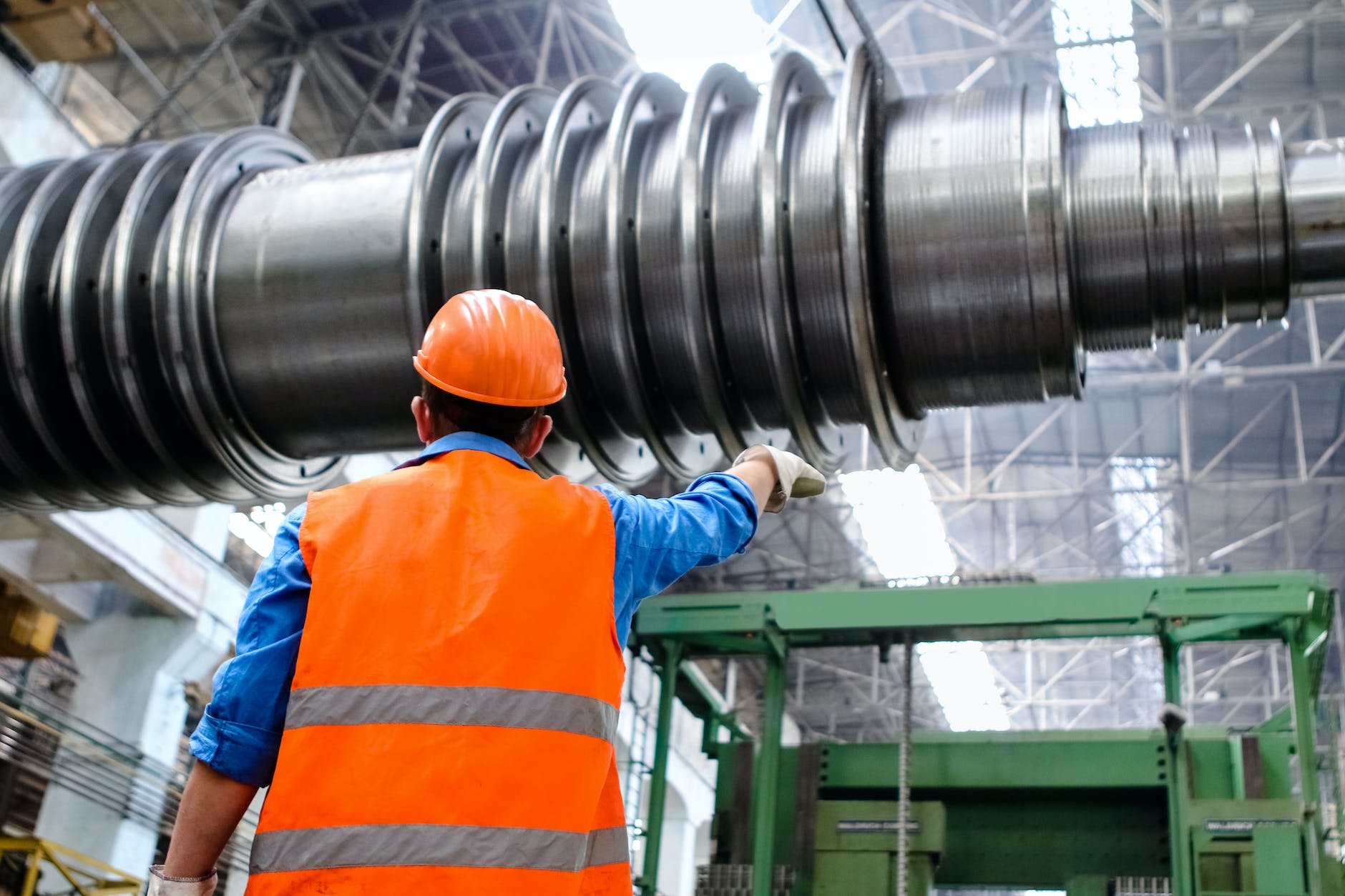
Steel Manufacturing Industry Hazards and Precautions | Download PPT
Introduction
The steel manufacturing industry plays a pivotal role in global infrastructure development, providing materials for construction, transportation, and various other sectors. However, the industry comes with its share of hazards that necessitate stringent safety measures. Understanding these hazards and implementing precautions is crucial for safeguarding the well-being of workers and maintaining a secure workplace.
Common Hazards in Steel Manufacturing
In the bustling world of steel production, workers face various hazards daily. These include physical hazards such as heavy machinery, chemical hazards from raw materials, ergonomic strains, and potential exposure to biological agents. Identifying and addressing these risks is fundamental to ensuring a safe working environment.
Machinery and Equipment Risks
The heart of steel plants lies in their machinery, presenting both opportunities and risks. Proper training for equipment operation is essential to mitigate the potential dangers associated with the heavy-duty machinery used in steel manufacturing. Regular maintenance protocols are equally crucial in preventing accidents and ensuring smooth operations.
Health Risks for Workers
Steelworkers are exposed to a myriad of health risks, including harmful substances, respiratory issues, hearing loss, and musculoskeletal disorders. Implementing comprehensive health and safety programs can significantly reduce these risks, fostering a healthier workforce.
Safety Measures in Steel Plants
Personal protective equipment (PPE) forms the first line of defense against hazards in steel plants. Additionally, the implementation of strict safety protocols, well-defined emergency response plans, and regular safety training contribute to creating a secure working environment.
Importance of Proper Ventilation
Ensuring proper ventilation is paramount in addressing air quality concerns associated with steel manufacturing. Installing effective ventilation systems and regularly monitoring and maintaining these systems can significantly reduce the health risks posed by exposure to hazardous substances.
Fire Hazards and Prevention
The high-temperature processes involved in steel manufacturing pose inherent fire risks. Understanding these risks and implementing fire prevention measures, coupled with well-practiced emergency evacuation plans, can minimize the impact of fire-related incidents.
Environmental Impact
While steel is indispensable for modern life, its production has environmental consequences. Embracing sustainable practices and adhering to regulations can mitigate the environmental impact of steel manufacturing, aligning the industry with global efforts for a greener future.
Worker Training and Awareness
Ongoing training programs and fostering safety awareness among workers are vital components of a comprehensive safety strategy. Encouraging a culture of reporting unsafe conditions ensures that potential hazards are promptly addressed, creating a safer workplace for all.
Regulatory Compliance
The steel manufacturing industry is subject to stringent safety regulations, and non-compliance can have severe consequences. Understanding and adhering to these regulations is not only a legal obligation but also crucial for maintaining a secure working environment.
The steel manufacturing industry involves various hazards that pose risks to workers' health and safety. Here are some common hazards and precautions associated with steel manufacturing:
Physical Hazards:
- Falling Objects:
- Use barriers, safety nets, and hard hats to protect against falling objects.
- Moving Machinery:
- Implement machine guarding.
- Provide training on equipment use.
- Establish clear safety zones to prevent accidents.
Chemical Hazards:
- Hazardous Substances:
- Identify and label chemicals.
- Provide MSDS and ensure proper storage and handling.
- Use appropriate PPE (gloves, goggles).
- Welding Fumes:
- Use local exhaust ventilation.
- Provide respiratory protection.
- Ensure adequate ventilation.
Heat and Noise:
- Heat Stress:
- Implement cooling measures.
- Provide adequate hydration.
- Schedule strenuous tasks during cooler periods.
- Noise Exposure:
- Use hearing protection.
- Implement engineering controls to reduce noise levels.
- Conduct regular hearing protection training.
Ergonomic Hazards:
- Repetitive Tasks:
- Rotate workers through different tasks.
- Provide ergonomic tools.
- Design workstations to minimize strain injuries.
- Heavy Lifting:
- Implement mechanical aids.
- Provide proper lifting training.
- Ensure workers use correct lifting techniques.
Electrical Hazards:
- Electrical Shocks:
- Use lockout/tagout procedures during maintenance.
- Provide electrical safety training.
- Ensure proper insulation and grounding.
Confined Spaces:
- Confined Space Entry:
- Establish proper entry procedures.
- Conduct atmospheric testing.
- Provide adequate ventilation.
Dust and Particulate Matter:
- Respiratory Hazards:
- Provide respiratory protection.
- Implement dust control measures.
- Ensure proper ventilation in work areas.
Crushing and Pinching Hazards:
- Machine Safeguards:
- Install guards on machinery to prevent crush and pinch points.
- Provide proper training on equipment operation.
Fire Hazards:
- Combustible Dust:
- Implement dust control measures.
- Use proper ventilation.
- Establish a comprehensive fire prevention program.
Personal Protective Equipment (PPE):
- Ensure that workers use appropriate PPE:
- Safety glasses, gloves, steel-toed boots, and hearing protection based on tasks and hazards.
Training and Communication:
- Regularly train workers on safety procedures:
- Emergency protocols.
- Proper use of safety equipment.
- Establish effective communication channels:
- Report hazards and incidents.
It's crucial for steel manufacturing facilities to conduct regular risk assessments, update safety protocols, and foster a culture of safety to mitigate these hazards effectively.
40 Duties of a Safety Officer PPT | Download PPT
Occupational Safety & Health Management System (OSHMS) | Download PPT
Top 10 Safety Rules of Oil and Gas Industry | Download PPT
HSE Management System PPT | Download PPT
Oil and Gas Industry Hazards and Control Measures PPT | Download PPT
Conclusion
In conclusion, navigating the hazards of the steel manufacturing industry requires a multifaceted approach that encompasses technological advancements, rigorous safety measures, and industry collaboration. Prioritizing the well-being of workers, adhering to regulations, and embracing sustainable practices are essential for the long-term success and safety of the steel industry.
FAQs
- How often should steel plant workers undergo safety training?
- Safety training should be conducted regularly, with refresher courses at least annually, to ensure that workers stay informed about the latest safety protocols.
- What personal protective equipment is mandatory for steelworkers?
- Mandatory PPE for steelworkers typically includes safety helmets, gloves, safety glasses, and steel-toed boots.
- How can steel plants minimize their environmental impact?
- Steel plants can minimize environmental impact by adopting sustainable practices, investing in cleaner technologies, and adhering to stringent environmental regulations.
- What role does automation play in reducing hazards in steel manufacturing?
- Automation in steel manufacturing reduces manual labor, minimizing the risk of accidents and improving overall workplace safety.
- Are there international standards for safety in the steel manufacturing industry?
- Yes, there are international standards, and adherence to these standards is crucial for ensuring a safe working environment in the steel industry.