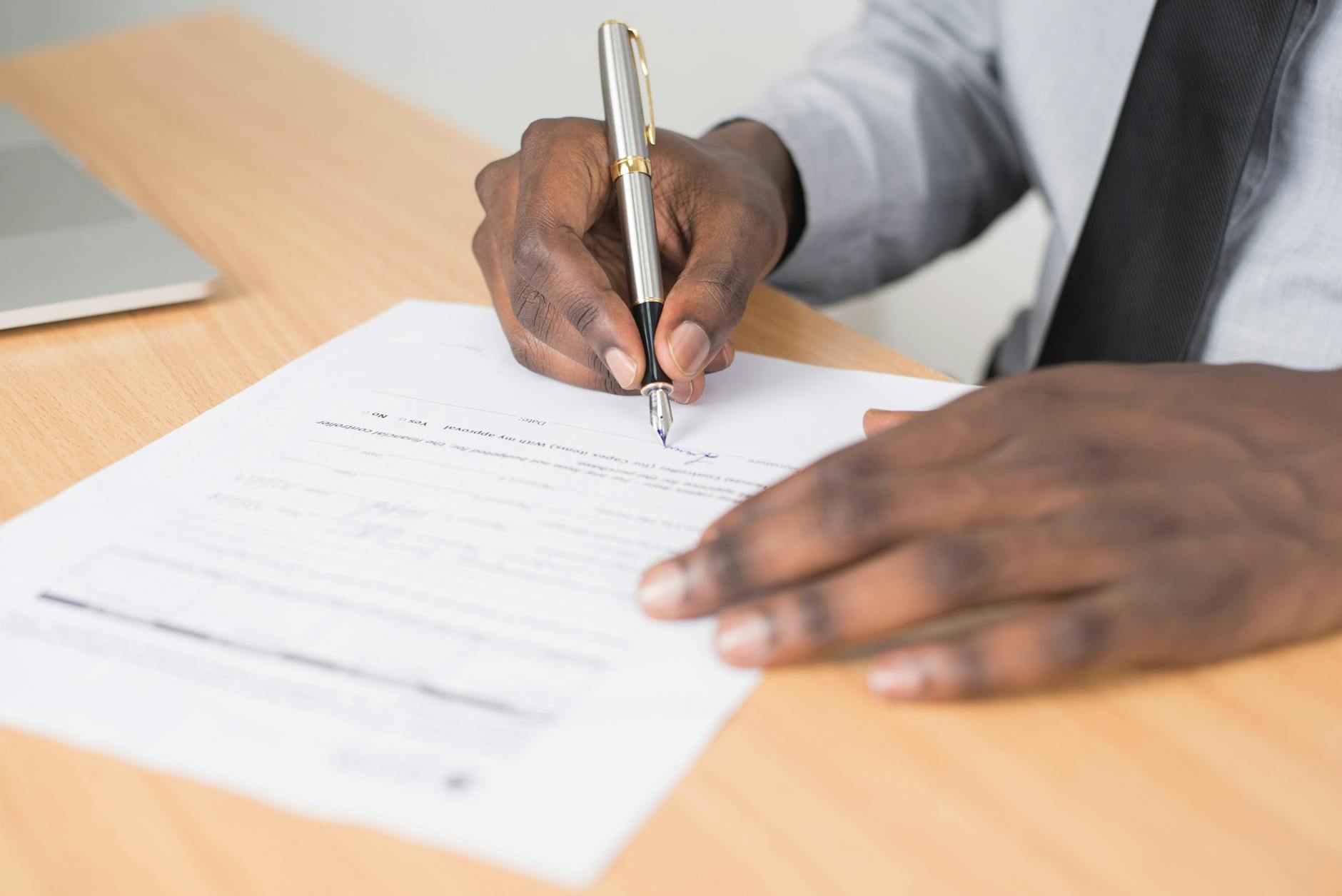
(Standard Operating Procedure) SOP Document
What is an SOP Document?
An SOP (Standard Operating Procedure) document is a formal, written guide that defines the step-by-step instructions for performing specific tasks or processes within an organization. SOPs are designed to ensure consistency, quality, and compliance in operations, regardless of who is executing the task.
Definition and Importance of SOPs
Why SOPs are Essential for Organizations
Imagine trying to bake a cake without a recipe. Even if you’re an expert, there’s a high chance you’ll miss a step or misjudge an ingredient. SOPs act as that “recipe” for organizations, ensuring everyone follows the same standards. They are crucial for:
- Reducing errors and inefficiencies.
- Ensuring compliance with regulations.
- Training new employees effectively.
How SOPs Streamline Operations
SOPs are the backbone of streamlined workflows. By providing clear instructions, they minimize downtime, reduce decision-making fatigue, and help employees focus on execution.
Key Elements of an SOP Document
For an SOP to be effective, it needs to include several critical elements:
Purpose and Scope
This section defines why the SOP exists and what processes it covers. It sets the boundaries for the document’s application.
Procedures and Guidelines
Detailed step-by-step instructions should be provided here. Use a logical order and ensure every step is explained clearly.
Roles and Responsibilities
Who does what? This section clarifies accountability, ensuring everyone knows their role in the process.
Terminology and References
Define technical terms and include references to other documents or standards to enhance clarity and usability.
Types of SOP Documents
Organizations use various types of SOPs depending on their needs:
Administrative SOPs
Focus on office tasks such as handling documents, maintaining records, or processing employee requests.
Operational SOPs
These guide on-the-ground activities, like equipment operation or inventory management.
Emergency Response SOPs
Designed for critical situations, these SOPs provide instructions for managing crises, ensuring safety, and mitigating damage.
Steps to Create an SOP Document
Crafting a solid SOP involves the following steps:
Step 1: Define the Purpose and Objectives
What do you want this SOP to achieve? Establishing clear objectives is the first step toward a meaningful document.
Step 2: Involve Stakeholders
Collaborate with those who will use or be affected by the SOP. Their insights ensure the document is practical and effective.
Step 3: Map Out the Process
Create a flowchart or diagram to visualize the steps. This helps identify any gaps or redundancies in the workflow.
Step 4: Write Clear and Concise Instructions
Use straightforward language, short sentences, and bullet points to make the SOP easy to follow.
Step 5: Review and Test the SOP
Pilot the SOP with a small team to spot errors or ambiguities. Revise it before rolling it out organization-wide.
Best Practices for Writing SOPs
Use Simple Language
Avoid jargon unless it’s industry-standard and include definitions for complex terms.
Include Visuals and Diagrams
Flowcharts, images, and tables can make instructions more accessible and engaging.
Regularly Update the SOP
Processes evolve, and so should your SOPs. Schedule regular reviews to keep them relevant.
Common Mistakes to Avoid
Overcomplicating the Content
Keep it simple. Too much detail can overwhelm users.
Skipping Stakeholder Input
An SOP crafted in isolation often fails to address practical challenges.
Ignoring Regular Reviews
Outdated SOPs can be worse than having none at all.
Benefits of Using SOPs
Improved Efficiency and Productivity
By standardizing tasks, SOPs eliminate guesswork and allow teams to work faster.
Enhanced Compliance and Safety
Adherence to industry regulations and safety standards becomes seamless.
Consistency in Operations
Every task is performed the same way, ensuring uniform quality.
How to Implement SOPs Successfully
Training Employees
Provide hands-on training sessions to familiarize teams with new SOPs.
Monitoring Compliance
Use audits or performance metrics to ensure SOPs are being followed.
Gathering Feedback for Improvement
Regular feedback loops help identify areas for enhancement.
Here’s an example of a Standard Operating Procedure (SOP) document template for a Safety Officer in an industrial setting. It outlines the procedures for maintaining safety protocols, incident management, and ensuring a safe working environment.
STANDARD OPERATING PROCEDURE (SOP)
For Safety Officer Duties
Document No: [SOP Number]
Effective Date: [Date]
Reviewed By: [Name]
Approval: [Signature & Date]
Version: 1.0
1. Purpose
This SOP defines the responsibilities, procedures, and protocols for Safety Officers to ensure workplace safety and compliance with safety regulations in the [specific industry, e.g., oil and gas, construction, manufacturing, etc.]. It aims to prevent accidents, minimize risks, and provide guidance on how to handle unsafe conditions and incidents.
2. Scope
This SOP applies to all activities performed by the Safety Officer in the [Company Name] and encompasses the identification, assessment, and management of workplace hazards. It also includes emergency response protocols, training programs, and safety audits.
3. Responsibilities
The Safety Officer is responsible for ensuring a safe working environment by performing the following duties:
- Conducting regular safety inspections and audits
- Identifying and assessing potential hazards
- Ensuring compliance with safety regulations and company policies
- Developing and implementing safety protocols and procedures
- Coordinating safety training programs for employees
- Investigating incidents, accidents, and near-misses
- Preparing safety reports and documentation
- Ensuring proper use of personal protective equipment (PPE)
- Reporting safety concerns to management and implementing corrective actions
- Conducting emergency response drills and exercises
4. Procedure
4.1 Safety Inspections
- Perform daily safety inspections of the workplace to identify hazards, unsafe conditions, and potential risks.
- Use a checklist to ensure all areas are inspected (e.g., machinery, PPE storage, fire exits, etc.).
- Record findings and take corrective actions immediately, where possible. Any non-compliance or significant hazards should be reported to management.
4.2 Hazard Identification and Risk Assessment
- Identify potential hazards by reviewing workplace operations and conditions.
- Evaluate the severity and likelihood of the risk.
- Implement control measures to minimize or eliminate identified risks, including engineering controls, administrative controls, and PPE.
- Document hazard assessments and ensure employees are aware of any changes.
4.3 Incident Reporting and Investigation
- Immediately report any workplace incident, injury, or near-miss to management.
- Investigate all incidents to determine their root cause.
- Prepare an incident report detailing the incident, findings, and corrective actions taken.
- Implement corrective and preventive actions to avoid similar incidents in the future.
4.4 Training and Safety Awareness
- Organize safety training programs for new employees and periodic refresher courses for existing employees.
- Ensure employees are trained in emergency procedures, use of PPE, and how to handle hazardous materials.
- Maintain records of all training sessions conducted.
4.5 Emergency Response Procedures
- Develop and communicate emergency response plans, including evacuation procedures, fire safety, and first aid protocols.
- Conduct regular emergency drills and provide feedback to improve response times.
- Ensure emergency equipment (e.g., fire extinguishers, first aid kits) is properly maintained and accessible.
5. Documentation and Record Keeping
- Maintain records of all safety inspections, incident reports, hazard assessments, and training sessions.
- Ensure all safety documents are up-to-date and stored in a secure, easily accessible location.
6. Compliance and Reporting
- Ensure compliance with local, state, and federal safety regulations.
- Prepare and submit safety reports to regulatory authorities as required.
- Provide regular safety performance reports to management.
7. Review and Updates
This SOP should be reviewed annually or after any major incident or change in safety regulations. Revisions or updates should be communicated to all relevant personnel.
Approval:
Signature: ___________________________
Name: [Manager/Supervisor Name]
Title: [Title]
Date: [Approval Date]
Conclusion
SOP documents are more than just guidelines; they are the foundation of any well-functioning organization. By following the steps outlined here, you can create SOPs that drive efficiency, ensure compliance, and maintain consistency across operations. Whether you’re a startup or an established enterprise, well-crafted SOPs are your secret weapon for success.
How Many Earthing Required for Tower Crane
Tower Crane Limit Switch Types
FAQs
1. What is the primary purpose of an SOP document?
The main goal is to standardize processes, ensuring consistency and quality in operations.
2. How often should SOPs be updated?
Ideally, SOPs should be reviewed annually or whenever there’s a significant change in processes.
3. Can SOPs be used for training purposes?
Absolutely! They are excellent resources for onboarding and training new employees.
4. What’s the best way to distribute SOPs within an organization?
Using digital platforms like shared drives or document management systems ensures accessibility.
5. Are SOPs legally required in some industries?
Yes, industries like healthcare, manufacturing, and aviation often require SOPs to comply with regulations.