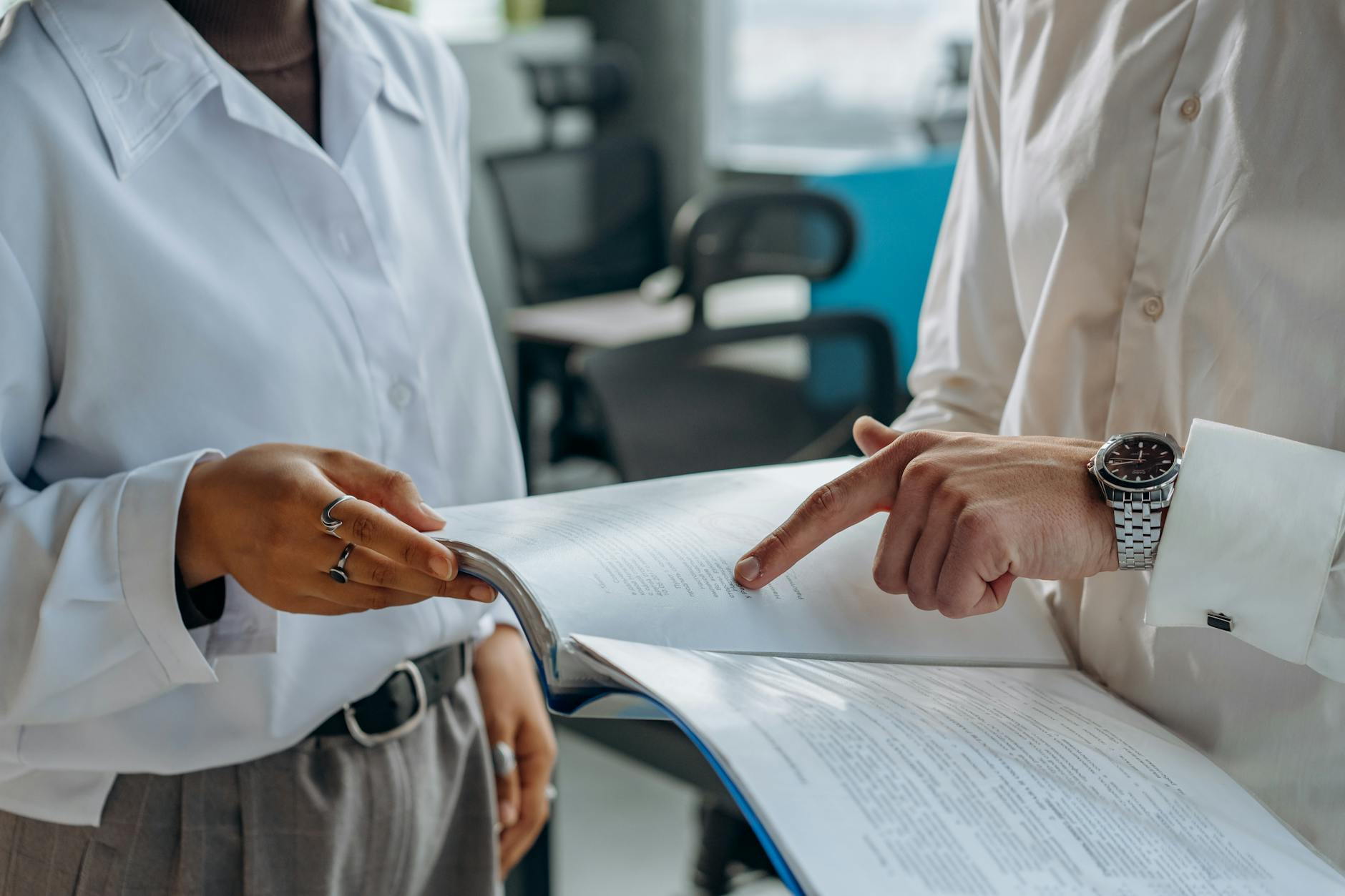
SHEMS – Safety, Health and Environment Management System
Introduction
In today’s fast-paced and often risky industrial environments, managing safety, health, and environmental concerns is crucial for any organization’s success. A robust Safety, Health, and Environment Management System (SHEMS) provides a structured approach to addressing these issues comprehensively. This system not only helps in mitigating risks but also promotes a culture of safety and sustainability.
Understanding SHEMS
Components of SHEMS
A well-rounded SHEMS integrates three core components:
- Safety Management: Focuses on preventing accidents and injuries through risk assessments, safety protocols, and regular inspections.
- Health Management: Addresses occupational health risks, ensures a healthy work environment, and promotes employee well-being.
- Environmental Management: Manages the organization’s environmental footprint by minimizing waste, reducing emissions, and ensuring compliance with environmental regulations.
Objectives of SHEMS
The primary objectives of SHEMS are:
- Preventing Workplace Accidents: By identifying and addressing potential hazards.
- Protecting Employee Health: Through proactive health management and wellness programs.
- Minimizing Environmental Impact: By implementing sustainable practices and ensuring compliance with environmental laws.
Historical Background
Evolution of SHEMS
The concept of SHEMS has evolved significantly over the years. Initially, workplace safety was the primary concern, driven by high accident rates and worker injuries during the Industrial Revolution. As awareness grew, so did the need to address health and environmental issues alongside safety.
Key Milestones in SHEMS Development
- Occupational Safety and Health Act (OSHA) of 1970: Established comprehensive safety regulations for workplaces in the United States.
- ISO 45001: An international standard for occupational health and safety management systems, introduced in 2018.
- ISO 14001: Focuses on effective environmental management and was first published in 1996.
Key Elements of SHEMS
Safety Management
Effective safety management involves:
- Risk Identification: Recognizing potential hazards before they cause harm.
- Safety Policies: Creating and enforcing safety guidelines and procedures.
- Regular Inspections: Conducting routine checks to ensure compliance with safety standards.
Health Management
Health management focuses on:
- Health Risk Assessment: Identifying and addressing potential health hazards in the workplace.
- Healthcare Services: Providing access to medical care and wellness programs.
- Promoting Healthy Lifestyles: Encouraging practices that improve overall employee health.
Environmental Management
Key aspects include:
- Waste Management: Proper disposal and recycling of waste materials.
- Emission Control: Reducing air and water pollutants to minimize environmental impact.
- Regulatory Compliance: Adhering to environmental laws and standards.
Benefits of Implementing SHEMS
Enhanced Workplace Safety
A well-implemented SHEMS reduces the likelihood of accidents and injuries, creating a safer working environment. This not only protects employees but also reduces costs related to workplace incidents.
Improved Employee Health
By focusing on health management, organizations can lower absenteeism due to health issues and increase overall productivity. Healthier employees are more engaged and motivated.
Environmental Protection
Effective environmental management reduces the company’s carbon footprint and promotes sustainability. This can also improve the company’s public image and compliance with environmental regulations.
Steps to Implement SHEMS
Planning and Commitment
Successful SHEMS implementation starts with a strong commitment from top management. This involves:
- Setting Objectives: Defining clear goals for safety, health, and environmental performance.
- Allocating Resources: Ensuring that necessary resources are available for implementation and maintenance.
Risk Assessment and Management
Conducting a thorough risk assessment involves:
- Identifying Risks: Recognizing potential hazards in the workplace.
- Developing Mitigation Strategies: Creating plans to address and manage these risks.
Training and Competence
Training ensures that employees are aware of and can effectively implement SHEMS policies. This includes:
- Regular Training Sessions: Providing up-to-date information on SHEMS procedures.
- Certification Programs: Offering formal qualifications to enhance competence.
Communication and Consultation
Effective communication involves:
- Informing Employees: Ensuring that all staff are aware of SHEMS policies and their roles.
- Consultation: Engaging employees in discussions about safety, health, and environmental concerns.
SHEMS Standards and Regulations
International Standards (ISO 45001, ISO 14001)
- ISO 45001: Provides a framework for managing occupational health and safety risks, focusing on worker safety and well-being.
- ISO 14001: Offers guidelines for environmental management, helping organizations reduce their environmental impact and comply with regulations.
National Regulations
National regulations vary by country but generally include requirements for workplace safety, health, and environmental management. Companies must stay informed about and comply with these regulations to avoid legal issues.
SHEMS in Different Industries
Construction Industry
The construction industry faces significant safety challenges due to the nature of its work. SHEMS helps manage risks such as falls, equipment accidents, and exposure to hazardous materials.
Manufacturing Industry
In manufacturing, SHEMS addresses health risks associated with exposure to chemicals, noise, and machinery. It also ensures environmental compliance by managing waste and emissions.
Oil and Gas Industry
The oil and gas industry involves high-risk operations with potential environmental impacts. SHEMS plays a crucial role in managing safety and environmental risks in this sector.
Challenges in SHEMS Implementation
Common Obstacles
Challenges in implementing SHEMS may include:
- Lack of Resources: Limited budget or personnel for SHEMS activities.
- Resistance to Change: Employees or management may resist new policies or procedures.
- Inadequate Training: Insufficient training can lead to poor implementation of SHEMS practices.
Strategies to Overcome Challenges
To address these challenges:
- Secure Management Support: Obtain commitment from top leadership to drive SHEMS implementation.
- Invest in Training: Ensure employees receive comprehensive training on SHEMS.
- Foster a Culture of Continuous Improvement: Encourage ongoing evaluation and enhancement of SHEMS practices.
Monitoring and Review of SHEMS
Key Performance Indicators (KPIs)
Monitoring KPIs helps assess the effectiveness of SHEMS. Common KPIs include:
- Incident Rates: Tracking workplace accidents and injuries.
- Health Metrics: Monitoring employee health and wellness.
- Environmental Impact: Measuring emissions, waste, and compliance with environmental regulations.
Continuous Improvement
Continuous improvement involves regularly reviewing and updating SHEMS to adapt to changing needs and regulations. This ensures the system remains effective and relevant.
Training and Awareness
Importance of Training
Training is essential for ensuring that employees understand and adhere to SHEMS policies. It helps prevent accidents, promotes health, and ensures environmental compliance.
Methods of Training
Effective training methods include:
- Workshops: Interactive sessions focusing on SHEMS principles and practices.
- E-Learning Modules: Online courses that employees can complete at their own pace.
- On-the-Job Training: Hands-on training that allows employees to apply SHEMS practices in real-world scenarios.
Understanding the Safety, Health, and Environment Management System (SHEMS)
A Safety, Health, and Environment Management System (SHEMS) is a structured framework designed to help organizations effectively manage their safety, health, and environmental responsibilities. It integrates various processes and policies to ensure that the workplace is safe for employees, compliant with health regulations, and environmentally friendly.
Key Components of SHEMS
- Safety Management
- Risk Assessment: Identifying potential hazards and evaluating the risks associated with them. This involves analyzing processes, equipment, and work environments to determine where safety measures need to be implemented.
- Safety Policies and Procedures: Developing and maintaining policies that outline safety protocols and procedures. This includes guidelines for emergency response, accident reporting, and safe work practices.
- Training and Awareness: Providing regular training to employees on safety procedures, emergency response, and safe work practices. Ensuring that all staff are aware of the safety policies and their roles in maintaining a safe workplace.
- Health Management
- Health Risk Assessments: Conducting assessments to identify potential health hazards in the workplace, such as exposure to harmful substances or ergonomic risks.
- Health Policies and Programs: Implementing programs that promote employee health and well-being. This includes initiatives like wellness programs, stress management, and health screenings.
- Medical Surveillance: Monitoring the health of employees to detect any adverse effects from workplace exposures. This includes regular health check-ups and maintaining records of employee health.
- Environmental Management
- Environmental Impact Assessment: Evaluating the potential impact of organizational activities on the environment. This involves analyzing processes and operations to minimize negative environmental effects.
- Environmental Policies and Procedures: Establishing policies to ensure compliance with environmental regulations and standards. This includes waste management, energy conservation, and pollution control.
- Sustainability Initiatives: Promoting practices that reduce the environmental footprint of the organization. This includes adopting green technologies, reducing waste, and improving resource efficiency.
Benefits of Implementing SHEMS
- Enhanced Safety and Health: By identifying and managing risks, organizations can prevent accidents and health issues, creating a safer and healthier work environment for employees.
- Regulatory Compliance: SHEMS helps organizations comply with local, national, and international regulations related to safety, health, and the environment, reducing the risk of legal issues and fines.
- Improved Environmental Performance: Through effective environmental management, organizations can reduce their environmental impact, improve sustainability, and enhance their reputation.
- Increased Employee Morale: A well-implemented SHEMS demonstrates a commitment to employee welfare and environmental responsibility, boosting morale and fostering a positive work culture.
Implementing SHEMS
- Planning: Define objectives and establish a SHEMS policy. Identify key areas for improvement and allocate resources accordingly.
- Implementation: Develop and execute plans, including safety procedures, health programs, and environmental initiatives. Ensure all employees are trained and aware of the new systems.
- Monitoring and Review: Regularly monitor the effectiveness of SHEMS. Conduct audits, review performance data, and make necessary adjustments to improve the system.
- Continuous Improvement: Use feedback and performance metrics to continually enhance the SHEMS. Implement best practices and stay updated with regulatory changes and industry standards.
By adopting a comprehensive SHEMS, organizations can not only meet regulatory requirements but also foster a culture of safety, health, and environmental stewardship, leading to long-term success and sustainability.
Conclusion
In summary, a Safety, Health, and Environment Management System (SHEMS) is vital for any organization aiming to protect its employees and the environment while achieving operational excellence. By addressing safety, health, and environmental concerns through a comprehensive system, businesses can improve performance, ensure compliance, and foster a positive workplace culture. Despite the challenges, the benefits of implementing SHEMS make it a worthwhile investment for long-term success.
10 Workplace Safety Rules That Will Keep Your Job Safe
Chandipura Virus: History | Symptoms | Who Is At Risk | How It Spreads | Treatment | Prevention
Fall Arrest System vs Fall Restraint System
Monsoon Hazards and Precautions
FAQs
What is SHEMS?
SHEMS stands for Safety, Health, and Environment Management System. It is a framework designed to manage and improve safety, health, and environmental performance within an organization.
Why is SHEMS important?
SHEMS is crucial for preventing accidents, protecting employee health, and minimizing environmental impact. It helps organizations enhance overall performance and maintain regulatory compliance.
How can a company implement SHEMS?
Implementing SHEMS involves gaining management commitment, conducting risk assessments, providing training, and ensuring effective communication and consultation with employees.
What are the benefits of SHEMS?
Benefits include enhanced workplace safety, improved employee health, and reduced environmental impact, all of which contribute to better business performance and compliance.
What challenges might a company face when implementing SHEMS?
Challenges include resource constraints, resistance to change, and inadequate training. Overcoming these challenges requires management support, investment in training, and a focus on continuous improvement.