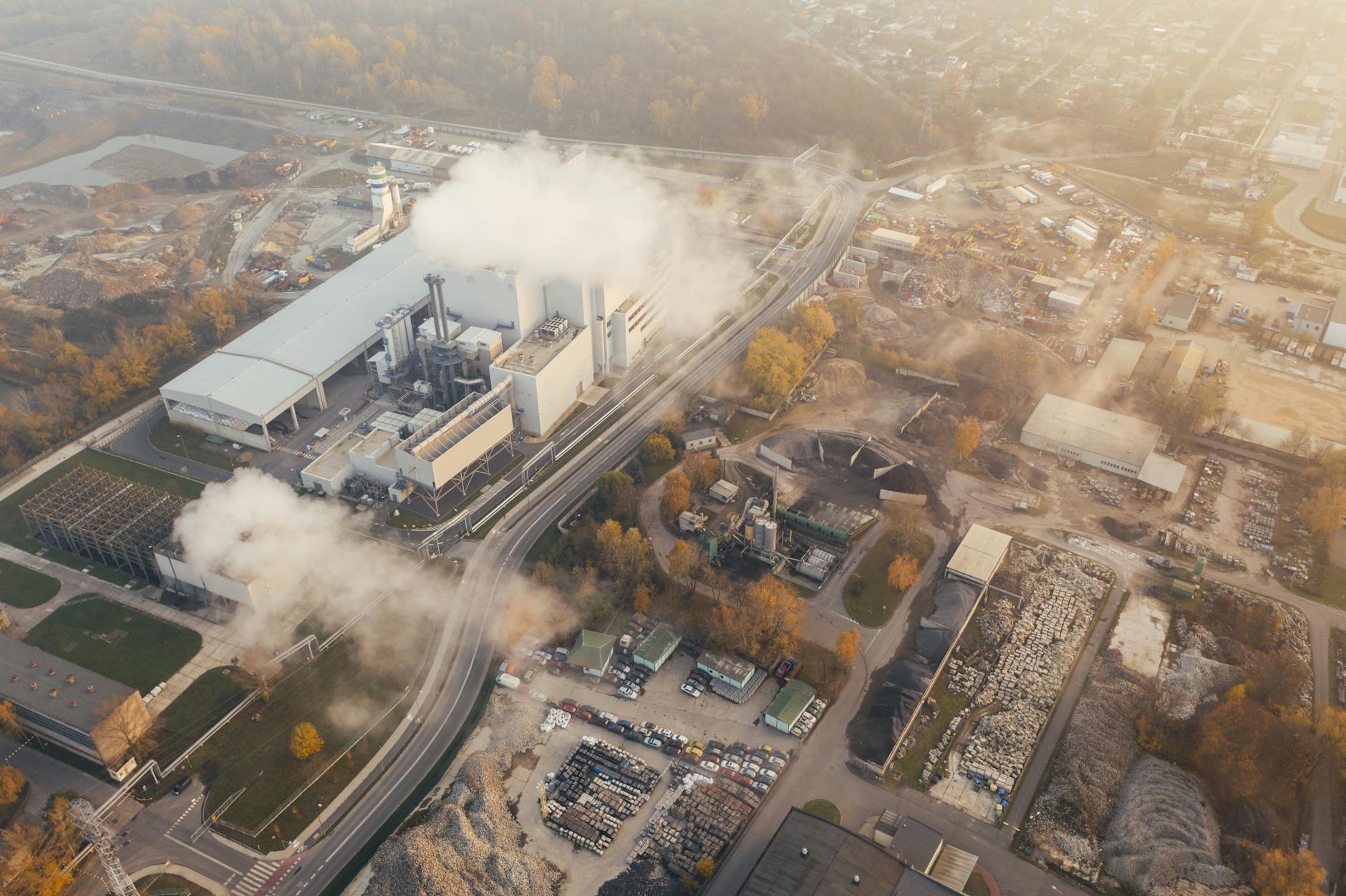
Safety Precautions in the Oil and Gas Industry
The oil and gas industry plays a pivotal role in powering our world, but amidst its significance, ensuring the safety of its workforce remains a paramount concern. This article delves into the various safety precautions and measures vital within this sector to safeguard workers, mitigate risks, and uphold industry standards.
Introduction to Safety Precautions in the Oil and Gas Industry
Importance of Safety Measures
Safety within the oil and gas industry is not just a regulatory requirement but a moral obligation to protect the workforce. With the inherent risks associated with exploration, drilling, and production, prioritizing safety is non-negotiable.
Statistics on Workplace Accidents
Before delving deeper into safety protocols, understanding the gravity of workplace accidents within this sector is crucial. Statistics often reveal the urgency for stringent safety measures to mitigate the frequency and severity of incidents.
Understanding Potential Hazards
Identifying Common Risks
The industry faces numerous hazards, including explosions, fires, chemical exposures, and machinery-related accidents. Recognizing and understanding these risks is the first step toward prevention.
Impact of Hazards on Workers
These hazards not only endanger lives but also have long-term consequences on the physical and mental well-being of workers, emphasizing the critical need for comprehensive safety protocols.
Regulatory Framework for Safety
Compliance Standards
The oil and gas industry operates under stringent regulatory frameworks set by government bodies and international organizations. Compliance with these standards is fundamental to ensuring a safe working environment.
OSHA Guidelines and Regulations
The Occupational Safety and Health Administration (OSHA) provides guidelines and regulations specifically tailored to the industry. Adhering to these standards is imperative to avoid penalties and, more importantly, to protect workers.
Personal Protective Equipment (PPE)
Importance of PPE
Personal Protective Equipment serves as the first line of defense against workplace hazards. From helmets and goggles to flame-resistant clothing, the right PPE can significantly reduce the risk of injuries.
Types of Equipment Required
The nature of the tasks dictates the type of PPE necessary. Understanding the specific equipment needed for each job role is crucial to ensuring workers’ safety.
Safety Training and Education
Training Programs
Comprehensive safety training programs are pivotal for all employees. These programs should encompass hazard identification, emergency response, and the proper use of safety equipment.
Continuous Education Initiatives
Education shouldn’t be a one-time event but an ongoing process. Regular workshops, seminars, and updates on safety protocols keep the workforce informed and vigilant.
Implementing Effective Safety Protocols
Creating Safety Protocols
Developing robust safety protocols involves identifying potential risks, establishing preventive measures, and outlining emergency procedures. Clear guidelines ensure swift and appropriate action in case of an incident.
Regular Safety Audits
Regular audits assess the effectiveness of safety protocols. It’s essential to identify areas for improvement and ensure compliance with evolving industry standards.
Emergency Response Procedures
Preparedness Plans
Preparedness is key to mitigating the impact of emergencies. Having detailed response plans for various scenarios minimizes chaos and maximizes the safety of all personnel.
Response to Potential Emergencies
From oil spills to fires, a prompt and coordinated response is critical. Regular drills and simulations prepare workers for real-life emergencies.
Culture of Safety in the Industry
Promoting Safety Culture
Creating a culture where safety is ingrained in every aspect of operations is vital. It involves fostering a mindset where safety is not just a rule but a shared value among all employees.
Employee Involvement and Engagement
Empowering employees to actively participate in safety initiatives cultivates a sense of ownership. When everyone feels responsible for safety, adherence to protocols increases.
Measuring and Improving Safety Performance
Metrics for Evaluation
Establishing measurable metrics allows for the assessment of safety performance. Incident rates, near-miss reports, and compliance levels provide insights into areas needing improvement.
Continuous Improvement Strategies
Identifying shortcomings and implementing corrective measures is an ongoing process. Constantly evolving safety protocols ensure adaptability to changing industry dynamics.
Challenges in Ensuring Safety
Addressing Common Challenges
The industry faces challenges such as high-risk tasks, varying operational environments, and workforce diversity. Finding solutions to these challenges is crucial for comprehensive safety.
Overcoming Industry-Specific Obstacles
Each sector within the oil and gas industry presents unique safety challenges. Tailoring safety measures to address these industry-specific obstacles is essential.
Safety precautions in the oil and gas industry are critical due to the high-risk nature of the work involved. Here are some key measures that are typically followed:
- Training and Education: Proper training programs for all employees, including contractors, on safety procedures, equipment operation, and emergency protocols.
- Personal Protective Equipment (PPE): Mandating the use of appropriate PPE such as helmets, gloves, goggles, fire-resistant clothing, and respiratory protection depending on the task and environment.
- Equipment Maintenance: Regular inspection, maintenance, and servicing of machinery and equipment to ensure they are in good working condition, reducing the risk of accidents.
- Risk Assessment and Management: Continuously assessing and mitigating risks through hazard identification, risk analysis, and implementation of control measures.
- Emergency Response Plans: Having detailed plans and regular drills for emergency situations such as fires, spills, or accidents, ensuring that all personnel are well-prepared to handle them.
- Safe Handling of Chemicals: Proper handling, storage, and transportation of hazardous materials, following established protocols and guidelines to prevent leaks or spills.
- Worksite Safety: Implementing safety protocols on-site, including clear signage, barriers, and restricted access to hazardous areas.
- Environmental Protection: Adhering to regulations and best practices to prevent environmental hazards such as oil spills, minimizing the impact on surrounding ecosystems.
- Behavioral Safety Programs: Encouraging a safety-oriented culture among workers, emphasizing individual responsibility for safety and promoting reporting of near misses or potential hazards.
- Regular Safety Audits and Inspections: Conducting routine inspections and audits to identify any safety issues or areas that need improvement, and promptly addressing them.
These precautions aim to ensure the well-being of employees, protect the environment, and maintain operational integrity within the oil and gas industry.
Conclusion
Safety precautions in the oil and gas industry are not just regulatory requirements but ethical imperatives. Upholding a robust safety culture, implementing effective protocols, leveraging technology, and fostering continuous improvement are pivotal in ensuring the well-being of workers and the industry’s sustainable growth.
OSHA Standards for Oil and Gas Industry
General Safety in the Oil and Gas Industry
Unique FAQs:
1. What are the most common hazards in the oil and gas industry?
The most common hazards in this industry include but are not limited to:
- Explosions and Fires: These can result from gas leaks or equipment malfunction.
- Chemical Exposure: Contact with hazardous chemicals poses health risks.
- Machinery Accidents: Working with heavy machinery presents potential risks.
- Falls and Trips: Uneven terrain and working at heights can lead to accidents.
- Ergonomic Hazards: Prolonged repetitive tasks can cause strain or injury.
2. How often should safety audits be conducted in this sector?
Safety audits should be conducted regularly, ideally following a structured schedule. Many companies perform audits quarterly, while some may opt for more frequent assessments, especially in high-risk areas or after incidents.
3. What role does employee training play in ensuring safety?
Employee training is paramount in creating a safety-conscious workforce. It educates workers about potential risks, proper use of safety equipment, emergency response procedures, and cultivates a culture of vigilance.
4. Can you explain the correlation between safety and productivity?
A safe work environment directly impacts productivity positively. When workers feel secure, they’re more focused and efficient, resulting in fewer accidents, reduced downtime, and increased morale, which ultimately enhances productivity.