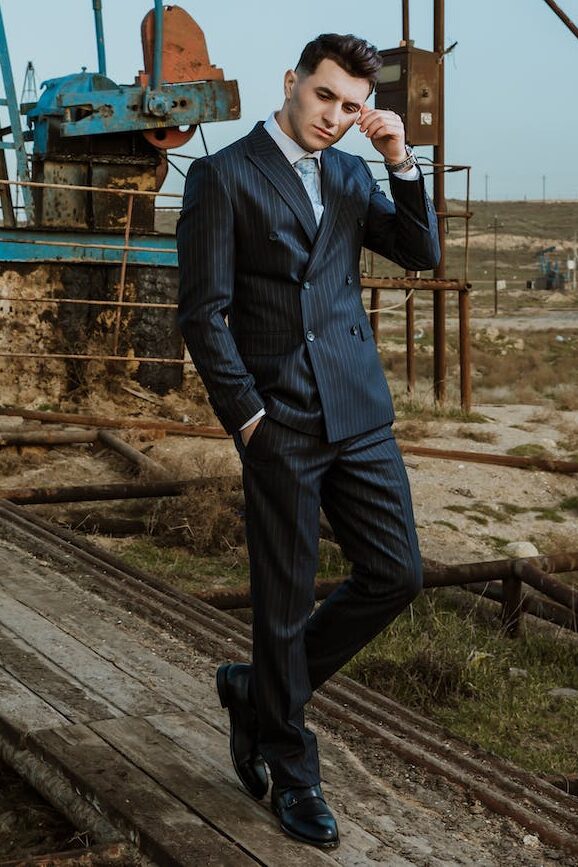
Safety Officer Interview Questions and Answers in TATA Steel
Introduction
Safety Officer Interview Questions and Answers in TATA Steel : In today’s competitive job market, securing a position as a Safety Officer at TATA Steel is not only prestigious but also challenging. To help you ace your interview, we have compiled a comprehensive list of Safety Officer interview questions and provided detailed answers. Whether you are a seasoned professional or just starting your career in safety management, these questions and answers will guide you towards success.
Tell us about yourself.
Answer: My name is John Smith, and I have over five years of experience in the field of safety management. I hold a bachelor’s degree in Safety Management, and I am passionate about ensuring the well-being of employees in the workplace. Throughout my career, I’ve had the opportunity to work with diverse teams and have successfully implemented safety protocols that have significantly reduced incidents.
What do you know about TATA Steel’s safety policies?
Answer: TATA Steel places a paramount emphasis on safety. They are committed to achieving “zero harm,” which means ensuring that no harm comes to their employees, contractors, or the environment due to their operations. TATA Steel has a robust safety culture and actively promotes safety awareness among its employees through training programs and continuous improvement initiatives.
What are the primary responsibilities of a Safety Officer at TATA Steel?
Answer: The primary responsibilities of a Safety Officer at TATA Steel encompass a wide range of tasks. These include conducting safety audits to identify potential hazards, investigating incidents to determine root causes, providing safety training to employees, and ensuring that the company complies with all relevant safety regulations. Additionally, Safety Officers play a critical role in promoting a culture of safety throughout the organization.
How do you stay updated with the latest safety regulations and standards?
Answer: Staying updated with the latest safety regulations and standards is essential in the field of safety management. To achieve this, I actively participate in seminars and conferences related to safety. I am also a member of professional safety associations that provide access to valuable resources and networking opportunities. Furthermore, I regularly read industry publications and research studies to keep abreast of emerging trends and best practices.
Explain the steps you would take to conduct a risk assessment in a steel manufacturing environment.
Answer: Conducting a risk assessment in a steel manufacturing environment involves a systematic approach. First, I would identify potential hazards by thoroughly examining the workplace and the processes involved. Next, I would assess the risks associated with each hazard, considering factors such as severity and likelihood. Based on this assessment, I would implement control measures to mitigate the identified risks. Finally, I would establish a regular review process to ensure that the risk assessment remains current and effective.
How would you handle an incident where a worker violated safety protocols?
Answer: Handling a situation where a worker violated safety protocols requires a balanced approach. I would start by addressing the issue directly with the worker, discussing the specific violation and its potential consequences. It’s essential to emphasize the importance of safety and provide any necessary retraining to ensure the worker understands the correct procedures. Additionally, I would document the incident and use it as an opportunity to reinforce the company’s commitment to safety and the consequences of non-compliance.
How do you promote a culture of safety among employees?
Answer: Promoting a culture of safety begins with effective communication. I believe in leading by example and consistently demonstrating safe behaviors. I would actively engage with employees, encouraging them to share safety concerns and ideas for improvement. Recognition programs for safe practices and teamwork can also help foster a safety-conscious environment. Regular safety meetings and training sessions would be conducted to keep safety at the forefront of everyone’s minds.
Can you provide an example of a challenging situation where your leadership helped prevent a safety incident?
Answer: In a previous role, we faced a situation where a crucial piece of safety equipment malfunctioned, which could have resulted in a significant safety hazard. I immediately assembled a team to assess the issue and implement temporary safety measures. Simultaneously, I coordinated with the equipment supplier to expedite repairs and replacements. Through effective leadership and quick decision-making, we were able to prevent any safety incidents and ensure the continued safety of our employees.
What are the unique safety challenges in the steel manufacturing industry, and how would you address them?
Answer: The steel manufacturing industry presents unique safety challenges due to the presence of heavy machinery, extreme temperatures, and exposure to various chemicals. To address these challenges, I would prioritize thorough training and education for employees, emphasizing safe operating procedures and the proper use of personal protective equipment (PPE). Regular equipment maintenance and inspections would also be implemented to reduce the risk of accidents.
Explain the role of Safety Data Sheets (SDS) in a steel manufacturing environment.
Answer: Safety Data Sheets (SDS) play a critical role in ensuring the safe handling of hazardous materials in a steel manufacturing environment. They provide detailed information about the properties of chemicals, potential hazards, safe storage and handling procedures, and emergency response measures. SDSs are essential references for employees, helping them make informed decisions and take appropriate precautions when working with chemicals.
Conclusion
Securing a Safety Officer position at TATA Steel is a significant achievement, and it comes with great responsibility. The interview questions and answers provided here serve as a valuable resource to prepare for your interview, demonstrating your expertise and commitment to safety. Remember to stay updated with the latest industry trends and regulations to excel in this role.
Safety Officer Interview Questions and Answers in Reliance Industry
Safety Officer Interview Questions and Answers in TATA Construction
Safety Officer Interview Questions and Answers in L&T Hydrocarbon
Safety Officer Interview Questions and Answers in L&T Construction
Safety Interview: Step by Step Procedure
FAQs (Frequently Asked Questions)
- What qualifications are required to become a Safety Officer at TATA Steel?Answer: TATA Steel typically requires candidates to have a bachelor’s degree in a related field, such as safety management or engineering, along with relevant certifications.
- How can I demonstrate my commitment to safety during the interview?Answer: Share examples from your past experiences where you prioritized safety and contributed to a safer work environment.
- What is the significance of TATA Steel’s commitment to “zero harm”?Answer: “Zero harm” is TATA Steel’s commitment to ensuring that no harm comes to their employees, contractors, or the environment due to their operations.
- Are there opportunities for career growth in the safety department at TATA Steel?Answer: Yes, TATA Steel values professional development, and there are opportunities for advancement within the safety department.