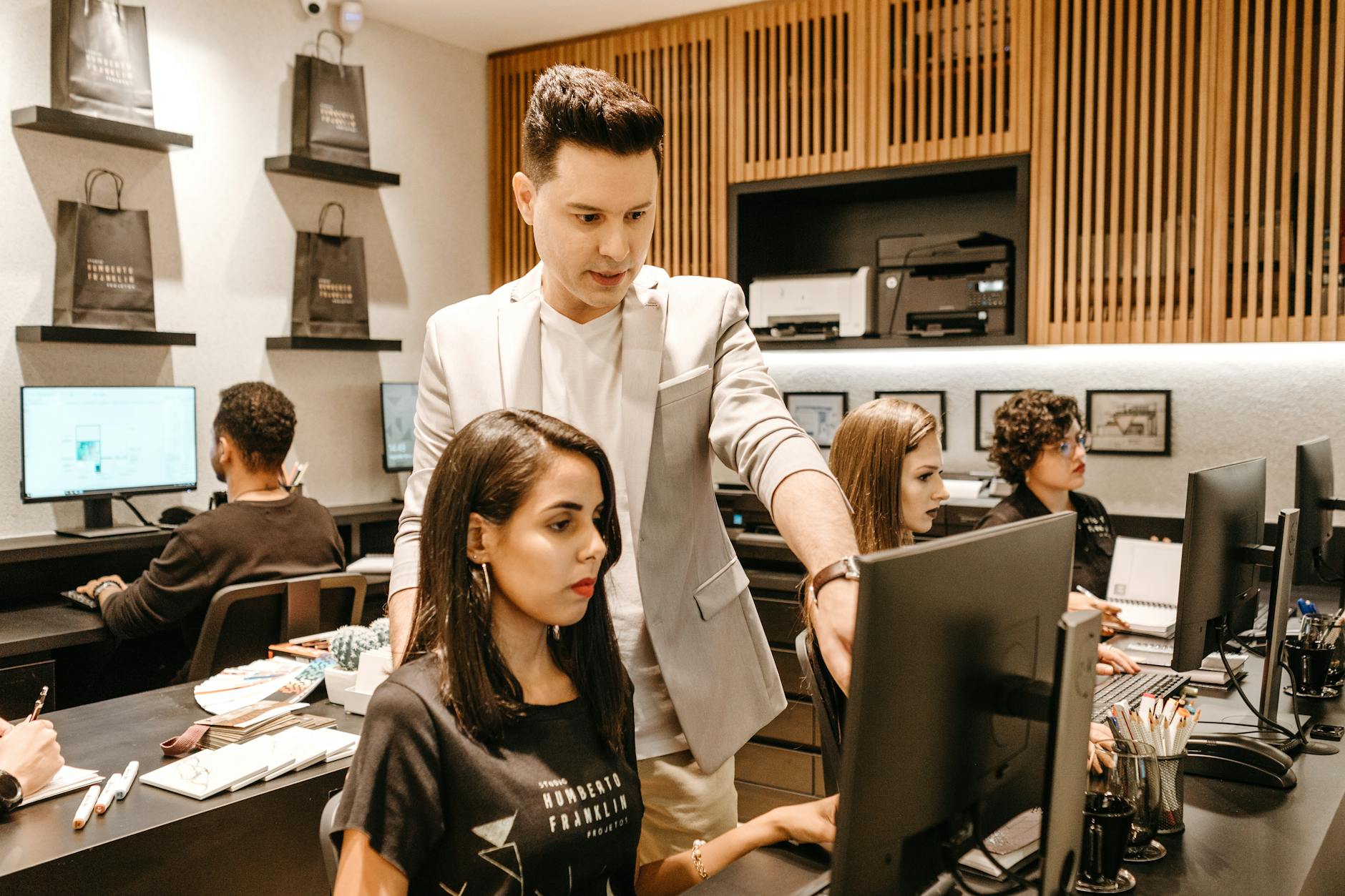
Safety Manager Responsibilities
Introduction
When you think about a safe workplace, the role of a safety manager often comes to mind. These professionals are the unsung heroes who ensure that everything runs smoothly and safely. In today’s world, the importance of safety in the workplace cannot be overstated. It’s not just about preventing accidents; it’s about creating an environment where employees feel secure and valued. So, let’s dive into the multifaceted responsibilities of a safety manager and understand why their role is pivotal.
Key Responsibilities of a Safety Manager
Development and Implementation of Safety Policies
A safety manager’s first and foremost duty is to develop comprehensive safety policies. This involves understanding the specific needs of the workplace and creating guidelines that address potential hazards. These policies act as the backbone of a company’s safety culture, outlining the dos and don’ts to ensure everyone’s well-being.
Conducting Risk Assessments
Risk assessments are crucial. Safety managers conduct these assessments to identify potential hazards and evaluate the risks associated with them. This proactive approach helps in preventing accidents before they occur, making the workplace safer for everyone.
Ensuring Compliance with Safety Regulations
Compliance is non-negotiable. Safety managers must ensure that all safety policies align with local, state, and federal regulations. This includes staying updated with changes in safety laws and implementing necessary adjustments to remain compliant.
Developing a Safety Culture
Promoting Safety Awareness
Creating a culture of safety starts with awareness. Safety managers work tirelessly to promote safety awareness among employees through various programs and initiatives. This helps in fostering a sense of responsibility and vigilance.
Training and Education Programs
Training is a cornerstone of safety. Regular training and education programs are essential for keeping employees informed about the latest safety practices and procedures. These programs should be engaging and informative to ensure maximum retention and application.
Encouraging Employee Participation
Involving employees in safety initiatives is vital. Safety managers encourage participation through safety committees, suggestion programs, and open forums. This inclusive approach ensures that everyone has a voice in maintaining a safe workplace.
Safety Inspections and Audits
Regular Workplace Inspections
Routine inspections are a must. Safety managers conduct regular inspections to identify potential hazards and ensure that safety measures are being followed. These inspections help in maintaining a safe working environment.
Internal and External Audits
Audits provide an additional layer of scrutiny. Safety managers oversee both internal and external audits to evaluate the effectiveness of safety policies and procedures. These audits are essential for continuous improvement.
Corrective Action Plans
When issues are identified, action is needed. Safety managers develop and implement corrective action plans to address any deficiencies found during inspections and audits. This ensures that safety standards are continuously met and improved.
Incident Investigation and Reporting
Procedures for Incident Reporting
Clear reporting procedures are essential. Safety managers establish protocols for reporting incidents, ensuring that all details are accurately documented. This is the first step in understanding and addressing the root cause of any issue.
Conducting Investigations
Investigations are thorough and systematic. Safety managers conduct detailed investigations to uncover the root causes of incidents. This involves collecting evidence, interviewing witnesses, and analyzing data.
Root Cause Analysis
Understanding the root cause is crucial for prevention. Safety managers use root cause analysis techniques to identify underlying issues and implement measures to prevent recurrence. This proactive approach is key to maintaining a safe workplace.
Emergency Preparedness and Response
Developing Emergency Plans
Preparation is key. Safety managers develop comprehensive emergency plans to ensure that the workplace is prepared for any potential emergency. These plans outline the steps to be taken in various scenarios, from fires to natural disasters.
Conducting Drills and Simulations
Practice makes perfect. Regular drills and simulations are conducted to ensure that employees know how to respond in an emergency. These exercises help in identifying any gaps in the emergency plans and making necessary adjustments.
Coordinating with Emergency Services
Collaboration is essential. Safety managers work closely with local emergency services to ensure a coordinated response in case of an emergency. This includes sharing information and conducting joint training exercises.
Managing Safety Documentation
Maintaining Safety Records
Documentation is a critical part of safety management. Safety managers maintain detailed records of all safety activities, including training sessions, inspections, and incident reports. These records are essential for compliance and continuous improvement.
Preparing Reports for Management
Clear communication with management is vital. Safety managers prepare regular reports that provide insights into safety performance and highlight any areas of concern. These reports help in making informed decisions about safety initiatives.
Documenting Training and Certifications
Keeping track of training and certifications is important. Safety managers ensure that all employees are up-to-date with their safety training and certifications. This documentation helps in maintaining a high standard of safety competence.
Safety Equipment and PPE Management
Ensuring Availability of Safety Equipment
Equipment availability is non-negotiable. Safety managers ensure that all necessary safety equipment is readily available and accessible to employees. This includes everything from fire extinguishers to first aid kits.
Proper Use and Maintenance of PPE
Personal Protective Equipment (PPE) is crucial for safety. Safety managers ensure that PPE is used correctly and maintained properly. Regular checks and maintenance schedules are implemented to ensure the effectiveness of PPE.
Regular Equipment Inspections
Inspection of safety equipment is a regular task. Safety managers conduct periodic inspections to ensure that all safety equipment is in good working condition. Any defective equipment is repaired or replaced promptly.
Health and Wellness Programs
Implementing Wellness Programs
Wellness programs contribute to overall safety. Safety managers implement programs that promote physical and mental well-being. These programs can include fitness initiatives, stress management workshops, and healthy eating campaigns.
Monitoring Occupational Health
Health monitoring is ongoing. Safety managers keep track of occupational health trends and address any emerging issues. This proactive approach helps in preventing health-related incidents.
Addressing Mental Health Issues
Mental health is a crucial aspect of workplace safety. Safety managers work to create a supportive environment where employees feel comfortable discussing mental health issues. This can include providing resources and support for those in need.
Safety Performance Metrics
Establishing Key Performance Indicators (KPIs)
Measuring performance is essential. Safety managers establish KPIs to monitor safety performance. These indicators provide valuable insights into the effectiveness of safety initiatives.
Analyzing Safety Data
Data analysis drives improvement. Safety managers analyze safety data to identify trends and areas for improvement. This data-driven approach ensures that safety measures are always evolving.
Reporting on Safety Performance
Regular reporting keeps everyone informed. Safety managers prepare detailed reports on safety performance, highlighting successes and areas for improvement. These reports are shared with management and employees to foster a culture of transparency.
Legal and Ethical Responsibilities
Understanding Legal Requirements
Knowledge of the law is critical. Safety managers must be well-versed in legal requirements related to workplace safety. This ensures that all safety practices are compliant with current laws.
Ethical Considerations in Safety Management
Ethics play a key role in safety management. Safety managers must consider the ethical implications of their decisions and actions. This includes ensuring that safety measures are fair and just for all employees.
Staying Updated with Safety Legislation
Legislation changes frequently. Safety managers stay updated with the latest safety laws and regulations. This ongoing education is crucial for maintaining compliance and ensuring the highest safety standards.
Communication and Leadership
Effective Communication Strategies
Communication is the backbone of safety. Safety managers develop effective communication strategies to ensure that safety messages are clear and understood by all employees. This includes regular meetings, newsletters, and training sessions.
Leading by Example
Leadership sets the tone. Safety managers lead by example, demonstrating a commitment to safety in all their actions. This encourages employees to follow suit and take safety seriously.
Building a Collaborative Safety Team
Teamwork enhances safety. Safety managers build collaborative safety teams that include representatives from various departments. This inclusive approach ensures that safety is a shared responsibility.
Continuous Improvement in Safety
Implementing Best Practices
Continuous improvement is key. Safety managers implement industry best practices to enhance safety measures. This involves staying updated with the latest safety trends and innovations.
Embracing Innovation in Safety
Innovation drives progress. Safety managers embrace new technologies and methods to improve safety. This can include everything from advanced safety equipment to new training techniques.
Learning from Past Incidents
Experience is a valuable teacher. Safety managers learn from past incidents to prevent future occurrences. This involves analyzing past mistakes and implementing measures to avoid repeating them.
Challenges Faced by Safety Managers
Common Challenges in Safety Management
Challenges are part of the job. Safety managers face various challenges, from resistance to change to limited resources. Recognizing these challenges is the first step in overcoming them.
Strategies to Overcome Challenges
Overcoming challenges requires strategy. Safety managers develop strategies to address and overcome the challenges they face. This can include gaining management support, securing funding, and fostering a safety-first culture.
A Safety Manager is responsible for ensuring the safety and health of employees within an organization. Their key responsibilities include:
Developing Safety Policies and Procedures: Create and implement safety policies, procedures, and programs that comply with local, state, and federal regulations. Ensure these policies are communicated effectively to all employees.
Risk Assessment and Hazard Identification: Conduct regular risk assessments and safety audits to identify potential hazards in the workplace. Develop strategies to mitigate identified risks.
Training and Education: Organize and conduct safety training sessions for employees. Ensure that all staff are educated on safety protocols, emergency procedures, and proper use of equipment.
Incident Investigation: Investigate workplace accidents, injuries, and near-misses to determine causes. Develop and implement corrective actions to prevent recurrence.
Compliance Monitoring: Ensure the organization complies with Occupational Safety and Health Administration (OSHA) standards and other relevant safety regulations. Stay updated on changes in safety laws and regulations.
Safety Inspections: Perform regular safety inspections of facilities, equipment, and work practices to ensure compliance with safety standards. Address any deficiencies promptly.
Record Keeping: Maintain accurate records of safety inspections, training sessions, incidents, and compliance activities. Ensure documentation is complete and up to date.
Emergency Preparedness: Develop and implement emergency response plans, including evacuation procedures, fire drills, and first aid protocols. Ensure emergency equipment is available and in good working condition.
Promoting a Safety Culture: Foster a culture of safety within the organization by encouraging proactive safety practices and open communication about safety concerns.
Liaison with Regulatory Agencies: Serve as the point of contact with regulatory agencies. Manage inspections, audits, and inquiries from these bodies.
Budget Management: Oversee the safety budget, ensuring funds are allocated effectively for safety programs, equipment, and training.
Continuous Improvement: Continuously evaluate and improve safety programs and policies based on industry best practices, technological advancements, and feedback from employees.
Employee Support and Guidance: Provide guidance and support to employees on safety-related issues, ensuring they have the resources and knowledge to perform their jobs safely.
Data Analysis: Analyze safety data and trends to identify areas for improvement. Use this data to develop targeted safety initiatives.
Coordination with Other Departments: Work closely with other departments, such as Human Resources, Operations, and Maintenance, to integrate safety into all aspects of the organization’s operations.
Conclusion
Safety managers play a crucial role in creating a safe and healthy workplace. Their responsibilities are vast and varied, encompassing everything from policy development to emergency preparedness. By taking a proactive approach and fostering a culture of safety, they ensure that employees feel secure and valued. In the end, a safe workplace is a productive workplace, and safety managers are at the heart of making this a reality.
What is the Role of the Manager in the HSE?
What Does a Safety Manager Do?
How to Write Safety Observation by Safety Officer | Download PPT
Safety Officer Duties and Responsibilities
FAQs
What qualifications are needed to become a safety manager?
To become a safety manager, typically, a bachelor’s degree in occupational health and safety, engineering, or a related field is required. Additional certifications like Certified Safety Professional (CSP) or Occupational Health and Safety Technologist (OHST) can be beneficial.
How do safety managers handle non-compliance?
Safety managers handle non-compliance by conducting investigations, identifying the reasons for non-compliance, and implementing corrective actions. They also provide additional training and reinforce the importance of safety regulations.
What are the most important skills for a safety manager?
Important skills for a safety manager include strong communication, attention to detail, problem-solving abilities, leadership, and a thorough understanding of safety regulations and best practices.
How often should safety training be conducted?
Safety training should be conducted regularly, at least annually, with additional training sessions whenever new equipment, processes, or regulations are introduced.
What role do safety managers play in employee wellness programs?
Safety managers play a key role in employee wellness programs by developing and implementing initiatives that promote physical and mental well-being, monitoring occupational health trends, and providing resources for health-related issues.