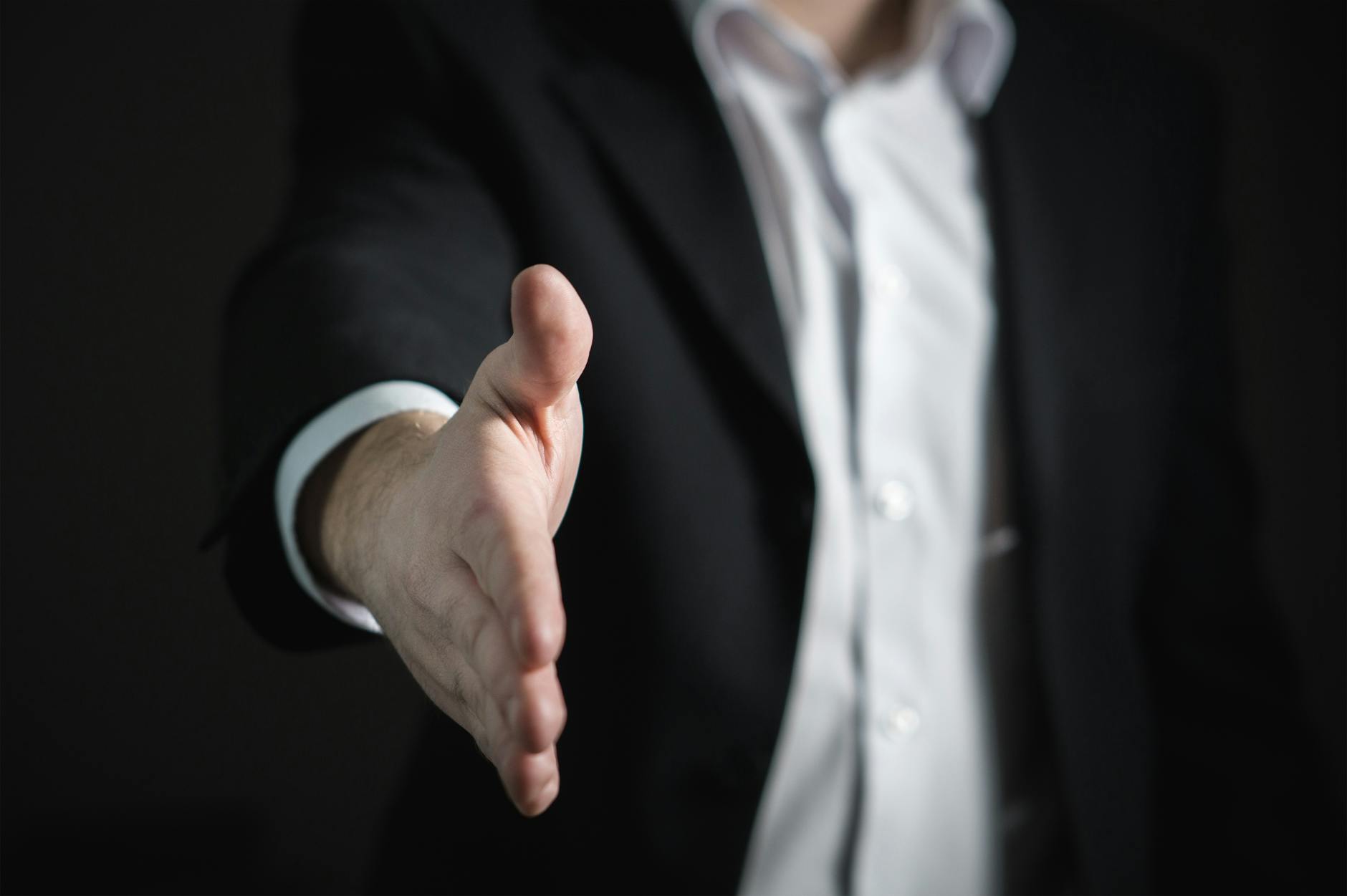
Manufacturing Safety Officer: 50+ Safety Job Interview Questions & Answers
Preparing for a Manufacturing Safety Officer interview? Below are 50+ common safety interview questions along with suggested answers to help you succeed.
General Safety Questions
1. What does a Manufacturing Safety Officer do?
A Manufacturing Safety Officer ensures compliance with OSHA and other safety regulations, conducts risk assessments, implements safety programs, investigates incidents, and trains employees on workplace safety.
2. Why is workplace safety important in manufacturing?
Workplace safety prevents injuries, reduces downtime, ensures compliance, improves productivity, and fosters a positive work culture.
3. What are the key responsibilities of a Safety Officer?
- Conducting risk assessments
- Ensuring compliance with safety laws
- Training employees on safety protocols
- Investigating accidents and near-misses
- Maintaining safety records
4. How do you stay updated with safety regulations?
By attending OSHA training, subscribing to safety newsletters, joining professional organizations (e.g., ASSP), and reviewing regulatory updates.
5. What is your approach to promoting a safety culture?
By leading by example, encouraging employee participation, recognizing safe behaviors, and providing continuous training.
OSHA & Compliance Questions
6. What are the most common OSHA violations in manufacturing?
- Lack of machine guarding
- Hazard communication failures
- Improper lockout/tagout (LOTO) procedures
- Inadequate fall protection
- Poor electrical safety practices
7. How do you ensure OSHA compliance in a manufacturing plant?
By conducting regular audits, training employees, maintaining documentation, and correcting hazards promptly.
8. What is the General Duty Clause under OSHA?
It requires employers to provide a workplace free from recognized hazards that could cause serious harm, even if no specific OSHA standard applies.
9. What are OSHA recordkeeping requirements?
Employers must record work-related injuries/illnesses on OSHA Form 300, maintain logs for five years, and report severe incidents within 24 hours.
10. How would you handle an OSHA inspection?
- Cooperate fully
- Provide requested documents
- Accompany the inspector
- Take notes on findings
- Address violations promptly
Risk Assessment & Hazard Control
11. How do you conduct a risk assessment?
- Identify hazards
- Determine who is at risk
- Evaluate risks and implement controls
- Monitor and review effectiveness
12. What are the hierarchy of controls?
- Elimination
- Substitution
- Engineering controls
- Administrative controls
- PPE
13. What is a Job Safety Analysis (JSA)?
A JSA breaks down job tasks to identify hazards and implement safety measures before work begins.
14. How do you handle chemical hazards in manufacturing?
By using SDS (Safety Data Sheets), proper labeling, ventilation, PPE, and employee training on handling/storage.
15. What is ergonomics, and why is it important in manufacturing?
Ergonomics ensures workstations are designed to reduce strain and injuries, improving productivity and worker health.
Incident Investigation & Reporting
16. How do you investigate a workplace accident?
- Secure the scene
- Interview witnesses
- Review procedures
- Identify root causes
- Recommend corrective actions
17. What is the difference between a near-miss and an incident?
A near-miss is an unplanned event that could have caused harm but didn’t, while an incident results in injury, illness, or damage.
18. Why is it important to report near-misses?
They provide early warnings of potential hazards, allowing proactive prevention before an actual injury occurs.
19. What is root cause analysis (RCA)?
A method to identify underlying causes of incidents (e.g., 5 Whys, Fishbone Diagram) to prevent recurrence.
20. How would you handle an employee who refuses to follow safety protocols?
- Explain the risks
- Provide retraining
- Enforce disciplinary action if necessary
Machine & Equipment Safety
21. What is Lockout/Tagout (LOTO)?
A safety procedure to ensure machines are properly shut off and cannot be restarted during maintenance.
22. Why is machine guarding important?
It prevents contact with moving parts, reducing amputations, crush injuries, and fatalities.
23. How do you ensure forklift safety?
- Operator training/certification
- Regular inspections
- Speed limits
- Clear pathways
- No unauthorized riders
24. What are the hazards of confined spaces?
- Toxic atmospheres
- Oxygen deficiency
- Engulfment
- Fire/explosion risks
25. How do you prevent electrical hazards?
- Regular equipment inspections
- Proper grounding
- Use of PPE
- Lockout/Tagout procedures
Fire Safety & Emergency Preparedness
26. What are the classes of fire?
- A (ordinary combustibles)
- B (flammable liquids)
- C (electrical fires)
- D (combustible metals)
- K (cooking oils)
27. How do you conduct a fire drill?
- Plan evacuation routes
- Assign roles (fire wardens)
- Sound alarms
- Track evacuation time
- Debrief afterward
28. What is an Emergency Action Plan (EAP)?
A written plan outlining procedures for fires, chemical spills, medical emergencies, and natural disasters.
29. How often should fire extinguishers be inspected?
Monthly visual checks and annual professional inspections.
30. What PPE is required for fire hazards?
Fire-resistant clothing, helmets, gloves, and self-contained breathing apparatus (SCBA) if needed.
Personal Protective Equipment (PPE)
31. When is PPE required in manufacturing?
When hazards cannot be eliminated through engineering or administrative controls.
32. How do you ensure proper PPE usage?
- Training employees
- Enforcing policies
- Providing correct fittings
- Regular inspections
33. What are common types of PPE in manufacturing?
- Hard hats
- Safety glasses
- Gloves
- Steel-toe boots
- Hearing protection
34. What are respirator protection standards?
OSHA’s Respiratory Protection Standard (29 CFR 1910.134) requires fit testing, medical evaluations, and proper maintenance.
35. How do you handle PPE non-compliance?
- Retrain employees
- Explain consequences
- Enforce disciplinary action if needed
Behavioral & Situational Safety Questions
36. How do you handle resistance to safety policies?
- Communicate benefits
- Involve employees in safety discussions
- Lead by example
- Recognize safe behaviors
37. Describe a time you improved workplace safety.
Example: “I introduced a near-miss reporting system, reducing incidents by 30% within six months.”
38. How do you prioritize safety tasks?
By assessing risks, addressing immediate hazards first, and following regulatory deadlines.
39. What would you do if you saw an unsafe act?
Stop the task, educate the worker, and report if necessary.
40. How do you measure safety performance?
Through leading indicators (training completion, near-miss reports) and lagging indicators (injury rates, lost workdays).
Manufacturing-Specific Safety Questions
41. How do you prevent slips, trips, and falls?
- Keep floors clean/dry
- Use anti-slip mats
- Mark walkways clearly
- Proper lighting
42. What are welding safety precautions?
- Proper ventilation
- Fire-resistant clothing
- Eye protection
- Gas cylinder safety
43. How do you handle hazardous waste?
- Proper labeling
- Secure storage
- Employee training
- Compliance with EPA/OSHA rules
44. What is heat stress prevention?
- Hydration breaks
- Shaded rest areas
- Lightweight clothing
- Acclimatization for new workers
45. How do you ensure crane safety?
- Operator certification
- Regular inspections
- Load limits
- Clear signals
Final Interview Tips
46. What certifications are useful for a Safety Officer?
- OSHA 30-Hour General Industry
- Certified Safety Professional (CSP)
- First Aid/CPR
- HAZWOPER (if handling hazardous materials)
47. Where do you see yourself in 5 years?
“Growing into a Senior Safety Manager role, implementing advanced safety tech like AI hazard detection.”
48. Why should we hire you as our Safety Officer?
Highlight experience, problem-solving skills, and passion for safety culture.
49. Do you have any questions for us?
- “What are the biggest safety challenges here?”
- “How does leadership support safety initiatives?”
50. How do you handle stress in high-risk environments?
“By staying organized, communicating clearly, and focusing on proactive hazard prevention.”
Bonus: 5 More Questions
- What is the role of safety committees?
- How do you train new employees on safety?
- What’s your experience with safety audits?
- How do you manage contractor safety?
- What safety software/tools have you used?
51. What is the role of safety committees?
Safety committees help promote workplace safety by:
- Reviewing incident reports and near-misses
- Conducting workplace inspections
- Recommending safety improvements
- Facilitating employee safety training
- Ensuring compliance with OSHA and company policies
Example: “In my previous role, I chaired a safety committee that reduced recordable incidents by 25% through monthly hazard assessments and employee engagement initiatives.”
52. How do you train new employees on safety?
- Orientation: Cover company safety policies, emergency procedures, and PPE requirements.
- Job-Specific Training: Teach equipment safety, hazard recognition, and safe work practices.
- Hands-On Demonstrations: Show proper use of tools, machinery, and PPE.
- Ongoing Refreshers: Conduct periodic safety meetings and drills.
Example: “I use a mix of classroom training, hands-on practice, and quizzes to ensure new hires understand critical safety protocols before they start working.”
53. What’s your experience with safety audits?
- Internal Audits: Regularly inspect work areas, equipment, and procedures.
- Third-Party Audits: Prepare for and assist with external compliance audits.
- Corrective Actions: Document findings and implement improvements.
Example: “I led quarterly safety audits that identified gaps in machine guarding, leading to a 40% reduction in equipment-related injuries.”
54. How do you manage contractor safety?
- Pre-Qualification: Verify contractors’ safety records and training.
- Safety Briefings: Provide site-specific hazards and emergency procedures.
- Oversight: Monitor compliance with safety rules (e.g., PPE, LOTO).
- Post-Work Reviews: Assess contractor performance for future engagements.
Example: “I implemented a contractor safety program requiring pre-work permits and daily toolbox talks, reducing contractor-related incidents by 50%.”
Final Tips for Your Safety Officer Interview
- Use the STAR Method (Situation, Task, Action, Result) for situational questions.
- Bring Examples of past safety improvements you’ve implemented.
- Ask Insightful Questions about the company’s safety challenges and goals.
Oil & Gas Safety Officer: 55 Safety Job Interview Questions & Answers
Construction Safety Officer: 50+ Safety Job interview Questions & Answers
10 Situational Safety Interview Questions and Answers