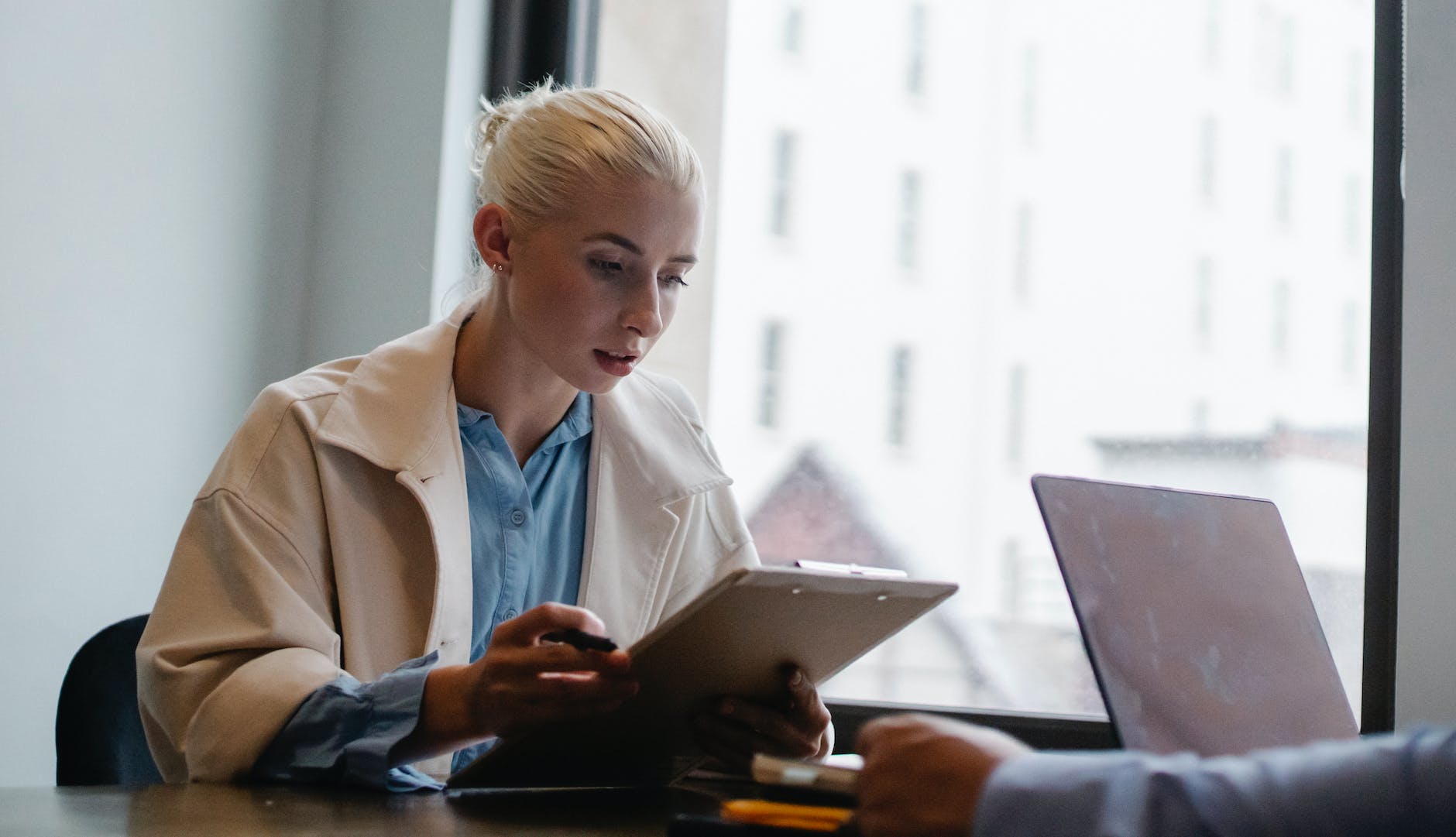
Safety Audit Reports as per Factory Act: Enhancing Workplace Safety and Compliance
Safety Audit Reports as per Factory Act : Safety within workplaces is paramount, and adhering to regulations set forth by the Factory Act is essential for ensuring a secure working environment. Central to this compliance are safety audit reports, providing a comprehensive evaluation of safety measures within factories. Let’s delve into the significance, components, and process of safety audit reports as per the Factory Act regulations.
Understanding the Factory Act Compliance:
The Factory Act establishes guidelines for workplace safety, covering aspects like working conditions, health, and safety standards. Compliance involves meeting specific requirements outlined in the act, including conducting regular safety audits.
Purpose and Benefits of Safety Audit Reports:
Safety audits serve a dual purpose of enhancing workplace safety and ensuring legal compliance. By identifying risks and areas for improvement, these reports play a pivotal role in mitigating hazards and avoiding legal repercussions.
Components of a Safety Audit Report:
A typical safety audit report includes criteria for inspection, detailing various safety parameters like equipment functionality, emergency protocols, and employee training. Reports follow a standardized format to ensure comprehensive assessments.
Conducting a Safety Audit:
Prior to audits, thorough preparations are necessary, including defining audit scope and assembling audit teams. On-site assessments involve observations, interviews, and documentation reviews to gauge compliance levels.
Interpreting Audit Findings:
Audit findings highlight areas of non-compliance, accompanied by recommendations for corrective actions. These insights assist in rectifying shortcomings and improving overall safety standards.
Implementing Changes Post Audit:
Post-audit, developing an action plan is crucial to address identified issues promptly. Continuous improvement strategies ensure sustained compliance and a proactive safety culture.
Role of Safety Audit Reports in Employee Engagement:
Involving the workforce in safety measures fosters a culture of responsibility and vigilance. Safety audits encourage employee participation, making safety a collective effort.
Measuring the Effectiveness of Safety Audits:
Evaluating the impact of safety audits requires defining relevant metrics and conducting periodic assessments to gauge long-term effectiveness.
Challenges in Conducting Safety Audits:
Resource constraints and the evolving nature of regulations pose challenges in conducting thorough and regular safety audits. Adapting to these challenges is key to maintaining compliance.
Safety Audit Report as per Factory Act
I. Executive Summary: The safety audit was conducted in accordance with the provisions of the Factory Act to assess and ensure compliance with safety standards and regulations. The audit aimed to identify potential hazards, evaluate safety protocols, and recommend improvements to enhance the overall safety of the workplace.
II. Introduction: The audit was carried out at [Company Name] located at [Address] on [Date]. The team consisted of [Number of Auditors], including safety experts and representatives from management. The audit covered all relevant areas as per the Factory Act, focusing on machinery, equipment, working conditions, and emergency preparedness.
III. Scope of the Audit: The audit encompassed the following key areas:
- Machinery and Equipment:
- Inspection of machines for proper guarding and safety features.
- Verification of maintenance records and schedules.
- Workplace Environment:
- Assessment of ventilation, lighting, and noise levels.
- Examination of ergonomic factors affecting workers.
- Occupational Health and Safety Measures:
- Review of first aid facilities and medical records.
- Evaluation of safety training programs for employees.
- Emergency Preparedness:
- Inspection of fire safety measures, including fire exits and extinguishers.
- Testing of emergency response procedures.
IV. Findings:
- Machinery and Equipment:
- [List of compliant machinery]
- [List of non-compliant machinery with recommended actions]
- Workplace Environment:
- [Summary of positive findings]
- [Areas requiring improvement and suggested measures]
- Occupational Health and Safety Measures:
- [Acknowledgment of compliance]
- [Areas needing attention and proposed corrective actions]
- Emergency Preparedness:
- [Compliance with emergency protocols]
- [Identified gaps and recommendations]
V. Recommendations:
- Implement immediate corrective actions for non-compliant machinery and equipment.
- Enhance workplace ergonomics through [specific measures].
- Conduct regular training sessions on safety protocols and emergency procedures for all employees.
- Update and maintain comprehensive records of machinery maintenance and workplace inspections.
- Periodically review and update emergency response plans to address potential risks.
VI. Conclusion: The safety audit has provided valuable insights into the compliance status of [Company Name] with the Factory Act. While commendable efforts have been made in certain areas, there is room for improvement in others. The implementation of the recommended measures will not only ensure legal compliance but, more importantly, foster a safer and healthier working environment for all employees.
VII. Acknowledgment: We would like to express our gratitude to the management and employees of [Company Name] for their cooperation and support during the safety audit process.
Date: [Date]
Auditors: [Names and Designations of Auditors]
[Seal and Signature of the Audit Team]
Safety Audit Report Example:
I. Executive Summary:
The safety audit was conducted at XYZ Manufacturing Ltd., a leading producer of automotive components, situated at 123 Industrial Avenue, on the 15th of November 2023. The audit aimed to evaluate compliance with safety regulations outlined in the Factory Act, ensuring a safe work environment for all employees.
II. Introduction:
The audit team comprised five members, including safety experts and representatives from management. The scope encompassed various departments and operational areas, focusing on machinery, workplace conditions, occupational health measures, and emergency preparedness.
III. Scenario:
The audit revealed commendable adherence to safety regulations in most areas. However, the machining department raised concerns due to the absence of proper machine guarding on a few lathes and milling machines. Additionally, ergonomic factors in the assembly line were identified as needing improvement, with repetitive strain injuries reported among workers.
IV. Findings:
- Machinery and Equipment:
- Compliance noted in 80% of machines.
- Non-compliance found in specific lathes and milling machines lacking adequate guards.
- Workplace Environment:
- Positive findings in ventilation and lighting across the facility.
- Assembly line ergonomics require attention due to reported strain injuries.
- Occupational Health and Safety Measures:
- First aid facilities and medical records are up-to-date and compliant.
- Recommended refresher training on ergonomic practices for assembly line workers.
- Emergency Preparedness:
- Well-maintained fire safety measures observed throughout the premises.
- Suggestions for a mock drill to test emergency response procedures.
V. Recommendations:
- Immediate installation of guards on identified non-compliant machines.
- Implementation of ergonomic improvements in the assembly line layout.
- Conduct monthly refresher training on ergonomics for assembly line workers.
- Organize a mock emergency drill within the next month.
VI. Conclusion:
The audit highlights XYZ Manufacturing Ltd.’s commitment to safety while pinpointing specific areas requiring attention for compliance with the Factory Act. Addressing these recommendations will not only ensure legal adherence but also promote a safer and healthier workplace for all employees.
VII. Acknowledgment:
We extend our gratitude to the management and staff of XYZ Manufacturing Ltd. for their cooperation and support during the safety audit process.
Date: 20th November 2023
Auditors: Sarah Johnson – Safety Officer Mark Thompson – Production Manager Dr. Emily White – Occupational Health Specialist Alex Carter – Safety Consultant Chris Miller – Factory Manager
[Seal and Signature of the Audit Team]
This example showcases how a safety audit report can outline both positive findings and areas that require attention, followed by actionable recommendations to ensure compliance with safety regulations.
Conclusion:
Safety audit reports play an instrumental role in ensuring workplace safety and compliance with Factory Act regulations. Regular audits, coupled with a proactive approach, are indispensable in fostering a culture of safety.
Safety Audit Definition NEBOSH
What are Three Types of Safety Audits?
Safety Audit as per IS 14489:2018
FAQs About Safety Audit Reports
- Why are safety audit reports important? Safety audit reports assess compliance and identify areas for improvement, crucial for maintaining workplace safety.
- How often should safety audits be conducted? Regular safety audits, as mandated by the Factory Act, should be conducted periodically, ensuring continual compliance.
- What happens if non-compliance is found during an audit? Non-compliance findings necessitate corrective actions to rectify issues and ensure adherence to safety standards.
- Are safety audit reports only for large factories? No, safety audit reports are essential for all workplaces, regardless of size, ensuring safety for all employees.
- How can technology aid in conducting safety audits? Technology offers tools for efficient audits, such as digital checklists and data analytics, enhancing the accuracy and speed of assessments.
I’m a graduate student in Health and Safety management and I found work very much helpful and willing to learn more.