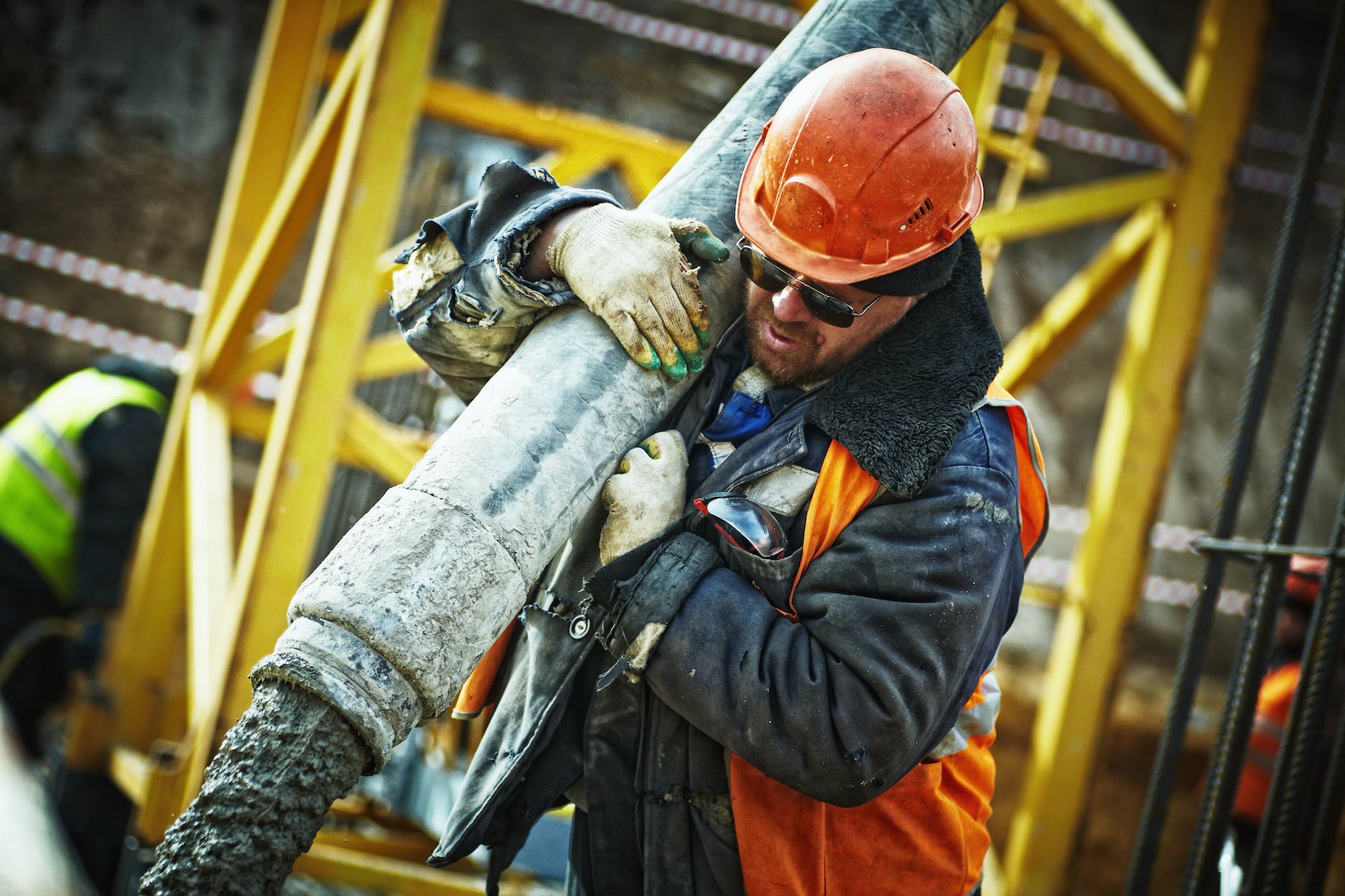
Safe Operating Procedure for Construction | Download PPT
Safe Operating Procedure for Construction : A Safe Operating Procedure (SOP) is a documented step-by-step guide that outlines how to perform a task or activity safely. It’s crucial in industries like construction where risks are high. Here’s a breakdown of developing an SOP along with a sample example for construction safety:
Steps to Develop a Safe Operating Procedure (SOP):
- Identify the Task: Determine the specific task or activity that requires an SOP. In construction, it could be “Operating Heavy Machinery.”
- Gather Information: Research best practices, regulations, and safety guidelines related to the task. Consult with experts and workers experienced in the field.
- Break Down the Steps: Outline each step of the task in a clear, sequential manner. Include safety precautions for each step.
- Risk Assessment: Identify potential hazards and risks associated with each step. Assess the level of risk and determine necessary safety measures.
- Develop the SOP: Write a detailed document including:
- Title: “Safe Operating Procedure for Operating Heavy Machinery”
- Purpose: Explain why the SOP is necessary and its intended outcomes.
- Equipment Needed: List required tools, machinery, or safety gear.
- Step-by-Step Instructions: Detail each step with clear instructions.
- Safety Precautions: Include measures to mitigate risks at each step.
- Emergency Procedures: Outline what to do in case of accidents or emergencies.
- Review and Approval: Have the SOP reviewed and approved by relevant authorities or experts.
- Training: Train personnel thoroughly on the SOP, ensuring they understand and can implement the safety measures.
Sample Example – Construction Safety SOP for Operating Heavy Machinery:
Title: Safe Operating Procedure for Operating Heavy Machinery
Purpose: To ensure the safe operation of heavy machinery to prevent accidents and injuries.
Equipment Needed:
- Heavy machinery (e.g., excavator, bulldozer)
- Personal Protective Equipment (PPE) – hard hat, gloves, steel-toed boots, reflective vest
Step-by-Step Instructions:
- Pre-Check Inspection:
- Inspect the machinery for any visible damages or malfunctions.
- Check fuel, oil, and hydraulic fluid levels.
- Ensure all safety features and warning signals are functional.
- Only certified operators should conduct inspections.
- Do not operate machinery if any faults are found. Report to supervisors.
- Start-Up Procedure:
- Start the machinery according to manufacturer guidelines.
- Allow the machine to warm up before use.
- Operate machinery only from the designated driver’s seat.
- Keep bystanders clear of the operating area.
- During Operation:
- Follow designated routes and paths.
- Maintain safe speeds and be aware of surroundings.
- Always wear seatbelts while operating.
- Avoid distractions and remain focused on the task.
- Shutdown Procedure:
- Follow manufacturer guidelines to power down the machinery.
- Engage parking brake and secure the equipment.
- Ensure the area is clear of personnel before shutting down.
- Conduct post-operation checks for any issues or damages.
Emergency Procedures:
- In case of malfunction or accident, immediately turn off the machinery.
- Evacuate the area and alert supervisors or emergency services.
Review and Approval: This SOP has been reviewed and approved by [Supervisor’s Name] on [Date].
Training: All personnel operating heavy machinery must undergo training on this SOP and demonstrate competency before operating machinery independently.
Remember, SOPs should be periodically reviewed and updated to reflect any changes in regulations, equipment, or best practices in the field.
Safety Marshal Roles and Responsibilities | Download PPT
Excavation HIRA | How to Prepare | Sample Example | Download PPT
Accident Prevention Plan (APP)| Steps | Benefits | How To Prepare | Download PPT
Job Safety Analysis (JSA) | Steps | Benefits | How To Prepare | Download PPT
Top 10 Fresher Safety Officer MCQs with Answer and Explanation | Download PPT
Frequently Asked Questions (FAQs)
1. What are SOPs, and why are they important? SOPs, or Safe Operating Procedures, are detailed step-by-step instructions outlining how to perform tasks safely. They are crucial for ensuring consistent, safe, and efficient work practices while minimizing risks and accidents.
2. How do SOPs contribute to workplace safety? SOPs serve as a guide for employees, emphasizing safety measures, proper procedures, and protocols to follow during various tasks. They promote a culture of safety, reducing the likelihood of accidents.
3. Who should develop SOPs? SOPs are typically developed by experts in the field, including safety professionals, experienced workers, and management teams. Their creation involves input from those with practical knowledge of the tasks and associated risks.
4. How often should SOPs be reviewed or updated? SOPs should be regularly reviewed, especially when there are changes in equipment, regulations, or best practices. Updates should occur whenever there’s new information or a change in processes that affect safety.
5. Are SOPs a legal requirement in workplaces? While not always a legal requirement in every industry, SOPs are highly recommended and often required by regulatory bodies to ensure compliance with safety standards. They demonstrate a commitment to safety and can be essential in legal matters regarding workplace incidents.
6. How are SOPs communicated and implemented in a workplace? SOPs are typically communicated through training sessions, manuals, and posted guidelines. Employees undergo training to understand and implement these procedures effectively.
7. What should be included in an SOP? An SOP should include a clear title, purpose, step-by-step instructions, safety precautions, emergency procedures, equipment requirements, and a review and approval section by relevant authorities.
8. How can employees provide feedback or suggest improvements to SOPs? Employees can contribute to improving SOPs by reporting issues, sharing their experiences, and suggesting revisions or enhancements through designated channels like safety committees or direct supervisors.
It’s real updates,and a great resource for me every time I read these safety materials….!
Thanks.
Thank you for kind words!