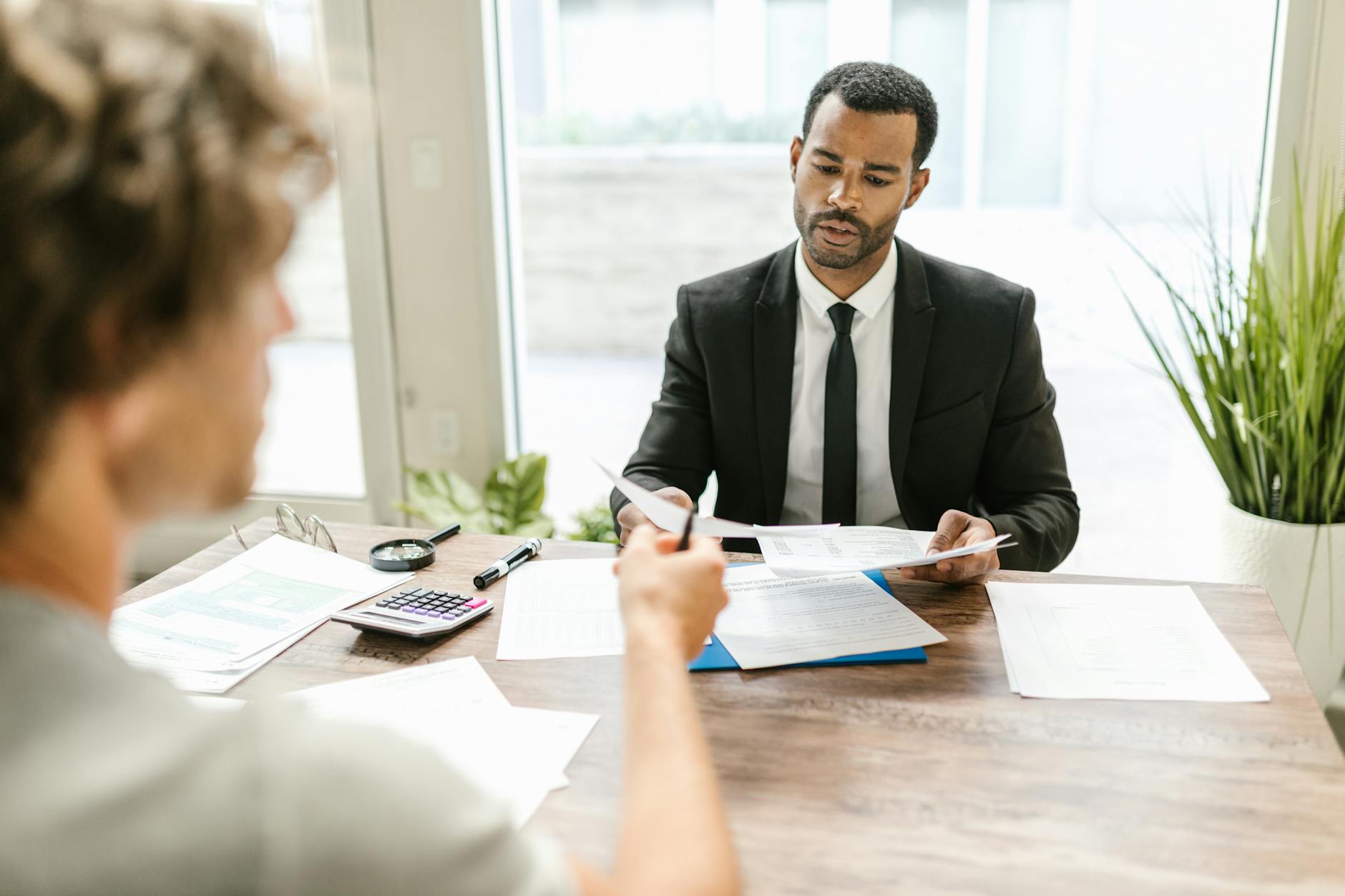
Root Cause Analysis (RCA) Interview Questions & Answers
Introduction
Root Cause Analysis (RCA) is a structured method used to identify the underlying causes of problems or incidents. It helps organizations prevent recurrence by addressing core issues rather than symptoms. RCA is widely used in industries like IT, healthcare, manufacturing, and engineering.
If you’re preparing for an interview involving RCA, you’ll need to demonstrate your problem-solving skills, analytical thinking, and familiarity with RCA methodologies like the 5 Whys, Fishbone Diagram (Ishikawa), Fault Tree Analysis (FTA), and Pareto Analysis.
Below are common RCA interview questions along with detailed answers to help you succeed.
Common RCA Interview Questions & Answers
1. What is Root Cause Analysis (RCA)?
Answer:
Root Cause Analysis is a systematic process for identifying the fundamental cause of a problem to prevent its recurrence. Instead of just treating symptoms, RCA digs deeper to find the origin of the issue using tools like the 5 Whys, Fishbone Diagram, and Fault Tree Analysis.
2. Why is RCA important in problem-solving?
Answer:
RCA is crucial because:
- It prevents recurring issues by addressing the root cause.
- Reduces costs associated with repeated failures.
- Improves process efficiency and reliability.
- Enhances decision-making with data-driven insights.
3. Explain the 5 Whys technique with an example.
Answer:
The 5 Whys involves asking “Why?” repeatedly until the root cause is uncovered.
Example:
Problem: A machine stopped working.
- Why? – The circuit overloaded.
- Why? – The bearing was not lubricated.
- Why? – The lubrication pump failed.
- Why? – The pump filter was clogged.
- Why? – No scheduled maintenance was performed.
Root Cause: Lack of preventive maintenance.
4. What is a Fishbone Diagram (Ishikawa Diagram)?
Answer:
A Fishbone Diagram is a visual tool used to categorize potential causes of a problem into groups like:
- Man (People)
- Machine (Equipment)
- Method (Process)
- Material (Resources)
- Environment (External Factors)
- Management (Policies)
It helps teams brainstorm and systematically analyze causes.
5. How do you differentiate between a symptom and a root cause?
Answer:
- Symptom: A visible effect of the problem (e.g., low productivity).
- Root Cause: The underlying reason behind the symptom (e.g., insufficient training leading to errors).
6. What are the steps in conducting an RCA?
Answer:
- Define the problem clearly.
- Collect data related to the issue.
- Identify possible causes using tools like 5 Whys or Fishbone.
- Determine the root cause.
- Develop corrective actions.
- Implement solutions and monitor results.
- Document findings for future reference.
7. What is Fault Tree Analysis (FTA)?
Answer:
FTA is a top-down, deductive approach that uses Boolean logic to analyze system failures. It starts with an undesired event (e.g., system crash) and traces back possible causes through a tree-like diagram.
8. How do you ensure RCA recommendations are implemented effectively?
Answer:
- Assign clear ownership of actions.
- Set deadlines and track progress.
- Conduct follow-up audits.
- Train employees on new processes.
- Use KPIs to measure effectiveness.
9. Can RCA be used for near-miss incidents?
Answer:
Yes, RCA is valuable for near-misses because it helps prevent future accidents by identifying weaknesses before they lead to major failures.
10. What challenges might you face during RCA?
Answer:
- Insufficient data – Lack of evidence makes analysis difficult.
- Bias – Personal opinions may influence findings.
- Complexity – Some problems have multiple root causes.
- Resistance to change – Teams may avoid implementing fixes.
Conclusion
Root Cause Analysis is a powerful tool for solving complex problems by addressing their origins. Mastering RCA methodologies and demonstrating analytical thinking in interviews will set you apart as a strong problem-solver.
How to Answer: ‘Why Should We Hire You as a Safety Officer?’ (7 Winning Responses)
30 NEBOSH IGC Interview Questions & Answers (2025)
15 Chemical Safety Interview Questions & Answers (SDS, Spills, PPE)
5 Safety Interview Mistakes to Avoid (From Real Hiring Managers)
10 Emergency Preparedness Interview Questions (With Action Plans)
FAQs on Root Cause Analysis
1. What industries commonly use RCA?
RCA is used in IT, healthcare, manufacturing, aviation, engineering, and quality management.
2. Is RCA only for large organizations?
No, RCA can be applied in small businesses and even personal problem-solving.
3. How long does an RCA process take?
It depends on the complexity—some take hours, while others require weeks for deep analysis.
4. What’s the difference between RCA and troubleshooting?
- Troubleshooting fixes immediate issues.
- RCA finds why the issue occurred to prevent recurrence.
5. Can RCA be automated?
Partial automation is possible with AI and data analytics, but human judgment is still essential.
Excellent informative platform for safety professional