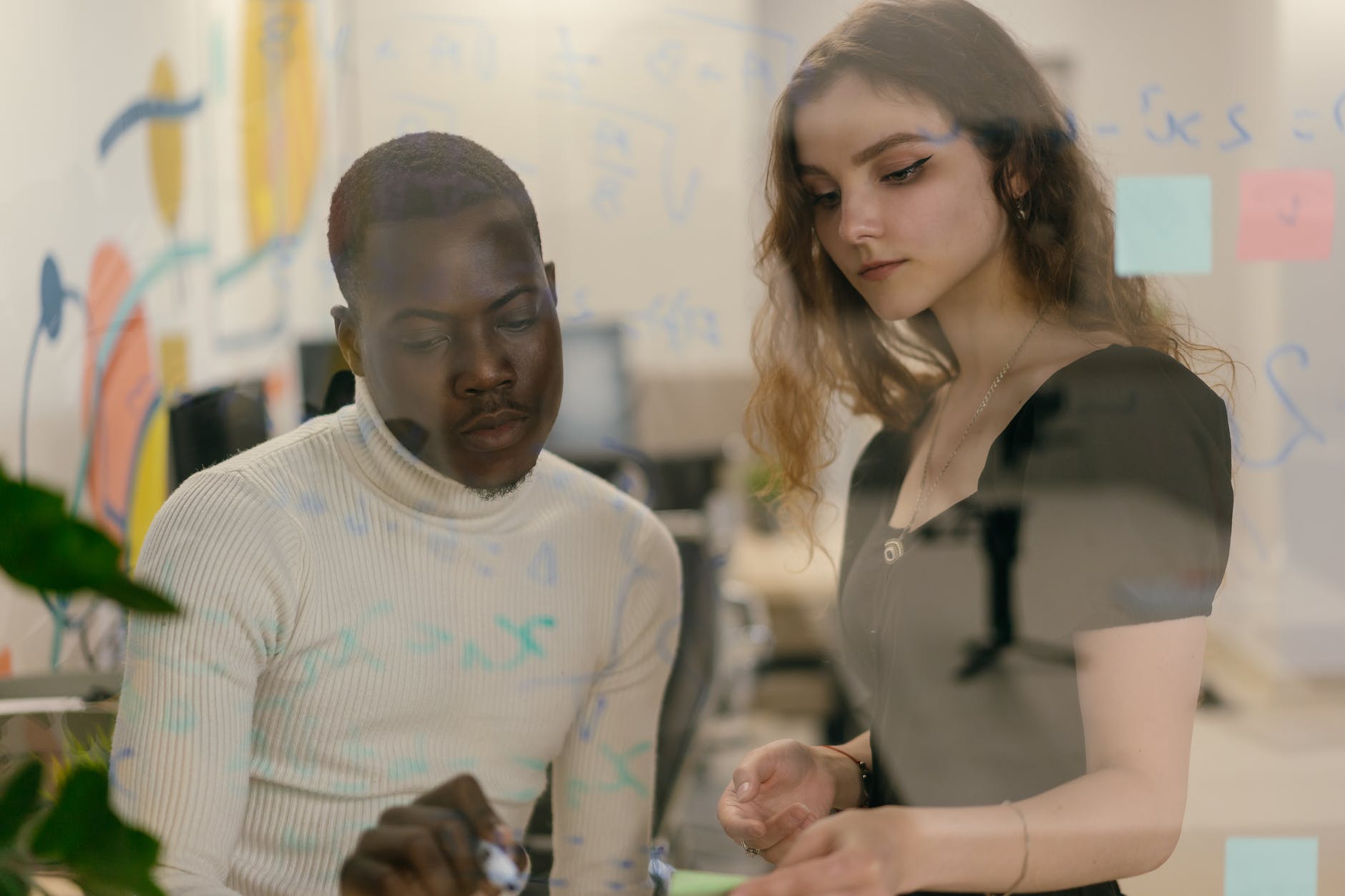
Root Cause Analysis (RCA): Identifying and Addressing Underlying Causes of Safety Incidents
Introduction
Root Cause Analysis (RCA) is a crucial methodology in safety engineering that focuses on identifying and addressing the underlying causes of safety incidents. This article explores the significance of RCA, its methodologies, and how its application contributes to creating safer workplaces and preventing the recurrence of accidents.
Understanding Root Cause Analysis (RCA)
Definition and Purpose
Root Cause Analysis is a systematic approach used to identify the fundamental cause or causes of an incident or problem. In the context of safety engineering, RCA aims to go beyond the immediate, surface-level causes and unearth the underlying factors that contributed to or allowed an incident to occur.
Preventing Recurrence
The primary purpose of RCA is not only to understand what went wrong but also to prevent the recurrence of similar incidents. By addressing the root causes, safety engineers can implement corrective actions that create lasting improvements in safety protocols and procedures.
Key Methodologies in Root Cause Analysis
Fishbone Diagram (Ishikawa or Cause-and-Effect Diagram)
The Fishbone Diagram is a visual representation that helps identify potential causes of a problem or incident. It categorizes factors contributing to the issue into categories such as equipment, personnel, processes, and environment, aiding in a comprehensive analysis.
5 Whys
The 5 Whys technique involves asking “why” repeatedly to delve deeper into the causes of an incident. By iteratively asking why an event occurred, safety engineers can peel back layers of causation to reveal the root cause.
Fault Tree Analysis (FTA)
Fault Tree Analysis is a graphical method that starts with a specific undesired event and works backward to identify the root causes. It helps safety engineers understand the combinations of events that led to the incident, enabling targeted corrective actions.
Applications of Root Cause Analysis in Safety Engineering
Incident Investigation
RCA is a critical tool in incident investigations. By systematically analyzing the incident, safety engineers can identify not only what went wrong but also why it went wrong. This insight is crucial for developing effective corrective actions.
Continuous Improvement
RCA contributes to a culture of continuous improvement. By identifying and addressing root causes, organizations can evolve their safety protocols and procedures, enhancing overall safety performance and preventing recurring incidents.
Preventive Action Planning
RCA informs the development of preventive action plans. Rather than merely reacting to incidents, safety engineers can proactively address potential issues by implementing measures that target the identified root causes.
Enhancing Safety Protocols
The insights gained from RCA enable safety engineers to enhance existing safety protocols. This may involve revising procedures, providing additional training, or improving equipment to prevent similar incidents in the future.
Challenges and Best Practices in Root Cause Analysis
Challenges
- Subjectivity: RCA can be subjective, influenced by individual perspectives and biases.
- Time-Consuming: Conducting a thorough RCA process can be time-consuming, requiring a careful examination of all relevant factors.
- Limited Data: Incomplete or limited data may hinder the accuracy of the analysis.
Best Practices
- Multidisciplinary Teams: Form multidisciplinary teams for diverse perspectives and expertise.
- Thorough Data Collection: Ensure thorough data collection to provide a comprehensive foundation for analysis.
- Continuous Learning: Foster a culture of continuous learning, encouraging teams to apply insights from previous RCAs to future incidents.
Root Cause Analysis (RCA) is a systematic process used to identify and address the underlying causes of safety incidents, accidents, or near misses. The goal of RCA is not only to determine what happened but also to understand why it happened in order to prevent similar incidents from occurring in the future. Here's a comprehensive guide to the key principles and steps involved in Root Cause Analysis for safety incidents:
Principles of Root Cause Analysis:
- Systemic Approach:
- RCA views incidents as the result of failures within a system rather than individual errors. It seeks to identify flaws in processes, procedures, or organizational systems.
- Preventive Focus:
- The primary objective of RCA is to prevent the recurrence of incidents by addressing their root causes, rather than just treating the symptoms.
Steps in Root Cause Analysis for Safety Incidents:
- Immediate Response:
- Promptly address any immediate threats or hazards resulting from the incident to ensure the safety of individuals and the environment.
- Secure the incident scene, provide medical assistance, and contain any potential further damage.
- Establish the Investigation Team:
- Assemble a multidisciplinary investigation team with individuals who have expertise in the relevant areas, including safety, operations, maintenance, and management.
- Ensure diversity in the team to bring varied perspectives to the analysis.
- Define the Problem:
- Clearly articulate the problem or incident that needs investigation.
- Develop a detailed description of the event, including the time, location, individuals involved, and any relevant factors.
- Gather Data:
- Collect all available data related to the incident, including witness statements, photographs, records, and equipment logs.
- Consider environmental conditions, equipment status, and human factors.
- Timeline and Sequence of Events:
- Develop a chronological timeline of events leading up to, during, and after the incident.
- Identify the sequence of events and the interactions between different factors.
- Immediate Causes:
- Identify the immediate causes or factors that directly contributed to the incident.
- Distinguish between active failures (e.g., human errors) and latent conditions (e.g., underlying organizational issues).
- Ask “Why” Iteratively:
- Use the “5 Whys” or a similar iterative questioning technique to explore deeper causes. Ask why the immediate cause occurred and continue probing until reaching the root cause.
- Analyze each response to uncover systemic issues rather than focusing solely on surface-level reasons.
- Root Cause Identification:
- Pinpoint the root causes, which are the fundamental issues or systemic failures that, if addressed, would prevent the recurrence of similar incidents.
- Consider factors such as organizational culture, training, communication, procedures, and equipment design.
- Causal Factor Analysis:
- Evaluate the causal factors that contributed to each identified root cause.
- Examine relationships between factors and their combined impact on safety.
- Recommend Corrective Actions:
- Develop specific and actionable corrective actions to address the root causes.
- Prioritize recommendations based on their potential effectiveness and feasibility.
- Implementation Plan:
- Develop a comprehensive plan for implementing the recommended corrective actions.
- Assign responsibilities, set deadlines, and allocate resources as needed.
- Follow-Up and Monitoring:
- Regularly monitor the implementation of corrective actions.
- Verify that the actions are effective in preventing recurrence and continuously evaluate their impact on safety performance.
- Documentation:
- Document the entire RCA process, including the incident details, investigation steps, findings, and corrective actions.
- Maintain clear records for future reference, regulatory reporting, and organizational learning.
- Communication:
- Communicate the findings and recommendations to all relevant stakeholders, including employees, management, regulators, and other interested parties.
- Share lessons learned to improve overall safety awareness.
- Continuous Improvement:
- Integrate the lessons learned from the RCA process into the organization’s safety management system.
- Foster a culture of continuous improvement by using insights gained from incident investigations to enhance safety practices, training, and procedures.
Root Cause Analysis is a dynamic process that evolves with new information and insights. It is a powerful tool for organizations committed to enhancing safety, preventing incidents, and continuously improving their safety performance.
Conclusion
In conclusion, Root Cause Analysis is a pivotal methodology in safety engineering, providing a structured approach to identify and address the underlying causes of safety incidents. By utilizing various techniques and applying RCA across incident investigations, continuous improvement initiatives, and preventive action planning, safety engineers contribute to building safer work environments and preventing future accidents.
Accident Prevention Plan (APP)
How to Investigate an Incident
Disaster Management: Preparedness, Response, and Recovery
Event Tree Analysis: Accident Investigation Method
Fault Tree Analysis: Accident Investigation Method
FAQs
- What is Root Cause Analysis (RCA) in safety engineering?
- RCA is a systematic approach to identify and address the underlying causes of safety incidents, aiming to prevent their recurrence.
- What are some key methodologies in Root Cause Analysis?
- Key methodologies include Fishbone Diagram, 5 Whys, and Fault Tree Analysis (FTA).
- How does RCA contribute to continuous improvement in safety?
- RCA contributes to continuous improvement by identifying root causes, informing preventive action plans, and enhancing safety protocols.
- What challenges are associated with Root Cause Analysis?
- Challenges include subjectivity, time consumption, and limited data availability.
- What are some best practices for effective Root Cause Analysis?
- Best practices include forming multidisciplinary teams, thorough data collection, and fostering a culture of continuous learning.