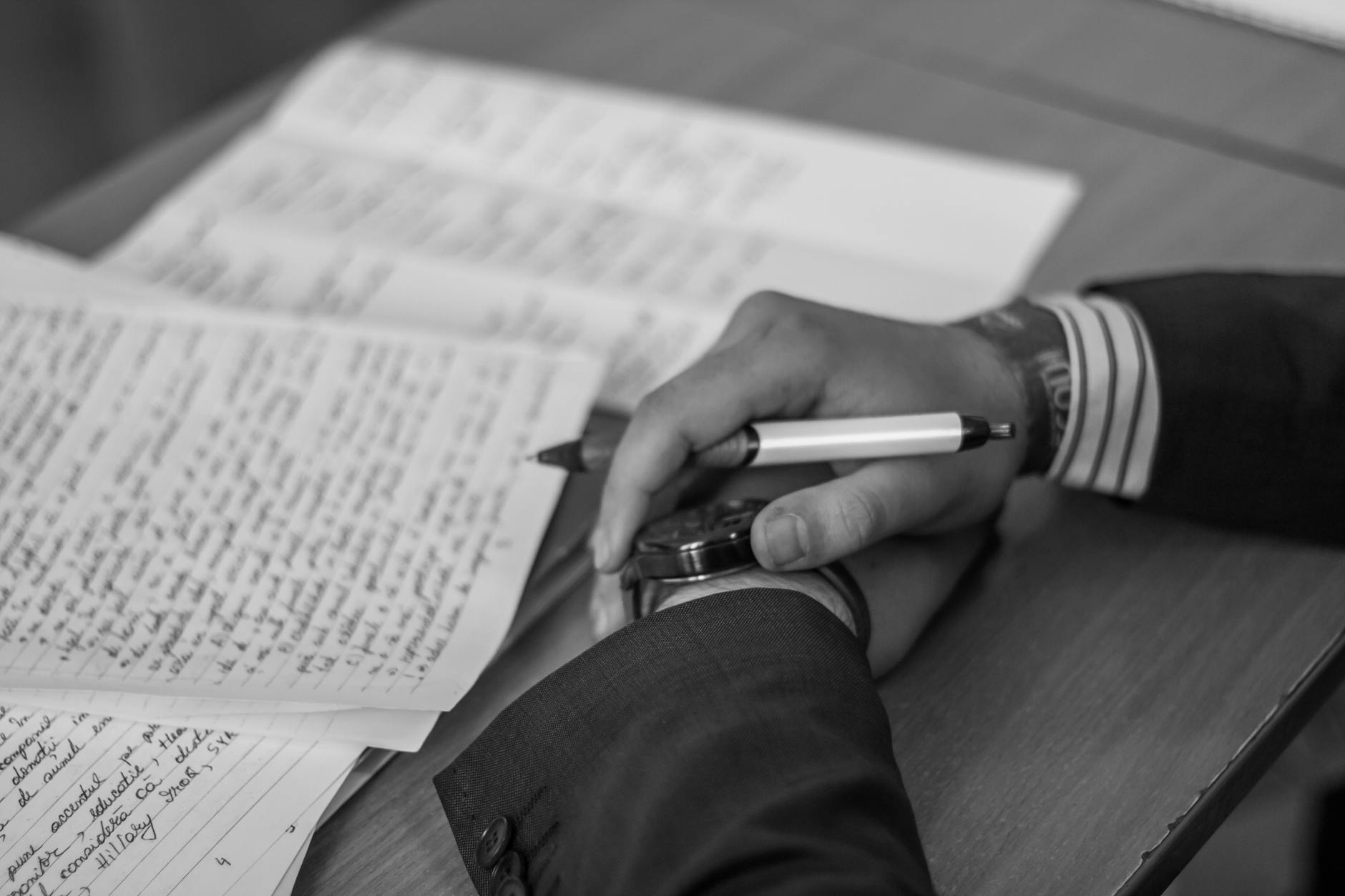
Risk Assessment vs Job Safety Analysis
Introduction
Workplace safety is more than just a buzzword; it’s a critical component of any successful organization. Ensuring that employees are safe and operations run smoothly requires meticulous planning and proactive measures. Two essential tools in the arsenal of safety professionals are Risk Assessment (RA) and Job Safety Analysis (JSA). These methodologies, while often used interchangeably, serve distinct purposes and are vital in identifying and mitigating hazards. In this article, we’ll delve into the differences and similarities between Risk Assessment and Job Safety Analysis, exploring their unique contributions to workplace safety.
Understanding Risk Assessment
Definition of Risk Assessment
Risk Assessment is a systematic process of evaluating potential risks that could be involved in a projected activity or undertaking. This process involves identifying hazards, analyzing or evaluating the risk associated with that hazard, and determining appropriate ways to eliminate or control the hazard.
Key Components of a Risk Assessment
- Hazard Identification: Recognizing things that may cause harm.
- Risk Analysis: Understanding the nature of the harm that could be caused by the hazard, how serious the harm could be, and the likelihood of it happening.
- Risk Evaluation: Comparing the level of risk against predefined acceptable levels to decide whether the risk is acceptable or needs reducing.
- Risk Control: Implementing measures to reduce the risk to an acceptable level.
The Process of Conducting a Risk Assessment
- Identify hazards by looking at the environment, equipment, and processes.
- Decide who might be harmed and how, considering employees, contractors, visitors, and the public.
- Evaluate the risks and decide on precautions.
- Record findings and implement them to ensure that the results are actionable.
- Review the assessment and update if necessary, especially when there are changes in the workplace or new risks are identified.
Understanding Job Safety Analysis
Definition of Job Safety Analysis
Job Safety Analysis (JSA), also known as Job Hazard Analysis (JHA), is a technique that focuses on job tasks to identify hazards before they occur. It involves breaking down a job into its basic steps, identifying potential hazards at each step, and determining the safest way to perform the job.
Key Components of a Job Safety Analysis
- Job Breakdown: Dividing a job into its component tasks.
- Hazard Identification: Identifying potential hazards for each task.
- Preventive Measures: Establishing methods to eliminate or reduce these hazards.
The Process of Conducting a Job Safety Analysis
- Select the job to be analyzed, typically focusing on jobs with high incident rates or significant potential hazards.
- Break the job down into a sequence of steps.
- Identify hazards associated with each step.
- Develop solutions to control or eliminate these hazards.
- Implement the solutions and ensure they are followed.
Key Differences Between Risk Assessment and Job Safety Analysis
Scope and Focus
- Risk Assessment typically covers a broad range of activities and is used to evaluate overall risks in the workplace.
- Job Safety Analysis is more focused, analyzing specific tasks within a job to identify and mitigate risks.
Timing and Frequency
- Risk Assessment is often conducted periodically or when there are significant changes in the workplace.
- Job Safety Analysis is usually performed whenever a new task is introduced or changes in procedures occur.
Level of Detail
- Risk Assessment provides a comprehensive overview of potential hazards in the workplace.
- Job Safety Analysis offers detailed insights into the safety measures for specific tasks.
Similarities Between Risk Assessment and Job Safety Analysis
Common Objectives
Both Risk Assessment and Job Safety Analysis aim to identify and mitigate hazards to prevent workplace accidents and injuries.
Shared Methodologies
Both methodologies involve hazard identification, risk evaluation, and implementation of control measures.
Integration in Safety Programs
Both Risk Assessment and Job Safety Analysis are integral parts of comprehensive safety management systems.
Benefits of Risk Assessment
Identifying Potential Hazards
Risk Assessment helps in identifying hazards that could potentially harm employees and the organization.
Mitigating Risks
By assessing risks, organizations can implement controls to mitigate these risks effectively.
Improving Workplace Safety Culture
A proactive approach to risk management fosters a culture of safety, where employees are more aware and engaged in maintaining a safe work environment.
Benefits of Job Safety Analysis
Enhancing Task-Specific Safety
JSA provides detailed insights into specific tasks, helping to identify and control hazards at a granular level.
Facilitating Employee Training
JSAs are valuable tools for training employees on the safest way to perform their jobs.
Encouraging Proactive Safety Measures
By focusing on specific tasks, JSA encourages employees to think proactively about safety measures and precautions.
When to Use Risk Assessment
Situations Where Risk Assessment is Most Effective
- When introducing new machinery or equipment.
- During significant changes in operations or processes.
- In response to incidents or near-misses to prevent recurrence.
Examples of Industries and Scenarios
- Construction: Evaluating risks associated with new projects.
- Manufacturing: Assessing risks of introducing new production lines.
- Healthcare: Managing risks related to patient care and safety.
When to Use Job Safety Analysis
Situations Where Job Safety Analysis is Most Effective
- When introducing new tasks or procedures.
- When modifying existing tasks or workflows.
- For jobs with high incident rates or significant potential hazards.
Examples of Tasks and Environments
- Oil and Gas: Analyzing tasks such as drilling operations.
- Electrical Work: Identifying hazards in tasks like wiring installations.
- Chemical Processing: Ensuring safety in handling hazardous materials.
Challenges and Limitations
Common Challenges in Risk Assessment
- Difficulty in identifying all potential hazards.
- Ensuring consistent and thorough evaluations.
- Keeping assessments up-to-date with changes in the workplace.
Common Challenges in Job Safety Analysis
- Time-consuming process for detailed job breakdowns.
- Ensuring employee participation and adherence to safety measures.
- Continuously updating JSA with changes in job tasks.
Addressing Limitations
- Regular training and engagement with employees.
- Leveraging technology for efficient assessments.
- Periodic reviews and updates to safety procedures.
Integrating Risk Assessment and Job Safety Analysis
Combining Both Approaches for Comprehensive Safety Management
Integrating RA and JSA provides a comprehensive approach to managing workplace safety, combining broad risk evaluations with detailed task-specific analyses.
Best Practices for Integration
- Use RA to identify overall workplace hazards.
- Apply JSA for detailed analysis of specific tasks identified in RA.
- Ensure continuous communication and feedback between RA and JSA processes.
Case Studies
- Manufacturing Plant: Using RA for overall safety evaluation and JSA for specific machinery operation tasks.
- Construction Site: Conducting RA for site-wide hazards and JSA for high-risk tasks like scaffolding work.
Tools and Resources
Tools for Conducting Risk Assessments
- Risk Assessment Software: Tools like Safesite and RiskWatch.
- Checklists and Templates: Predefined formats for consistent evaluations.
Tools for Conducting Job Safety Analyses
- JSA Software: Tools like JSA Builder and JSABuilder.
- Guidelines and Templates: Standardized forms for breaking down job tasks.
Recommended Resources and References
- OSHA Guidelines: Comprehensive resources on RA and JSA.
- Industry Standards: Specific guidelines from industry bodies like ANSI and ISO.
Conclusion
Risk Assessment and Job Safety Analysis are critical tools in ensuring workplace safety. While they serve different purposes, their combined use provides a robust framework for identifying and mitigating hazards. By understanding the distinctions and similarities between these methodologies, organizations can effectively integrate them into their safety programs, creating a safer work environment for all.
What are the 5 Steps of a JSA?
5 Step Process of Risk Assessment
FAQs
What is the main difference between Risk Assessment and Job Safety Analysis?
Risk Assessment provides a broad evaluation of workplace hazards, while Job Safety Analysis focuses on the safety of specific tasks.
Can Risk Assessment and Job Safety Analysis be used together?
Yes, integrating both approaches offers a comprehensive safety management strategy.
How often should Risk Assessments be conducted?
Risk Assessments should be conducted periodically and whenever significant changes occur in the workplace.
Who is responsible for conducting Job Safety Analysis?
Typically, safety officers or supervisors are responsible for conducting JSAs, but it should involve input from employees performing the tasks.
What are the most common tools used in Risk Assessment and Job Safety Analysis?
Common tools include risk assessment software, checklists, JSA software, and standardized templates.