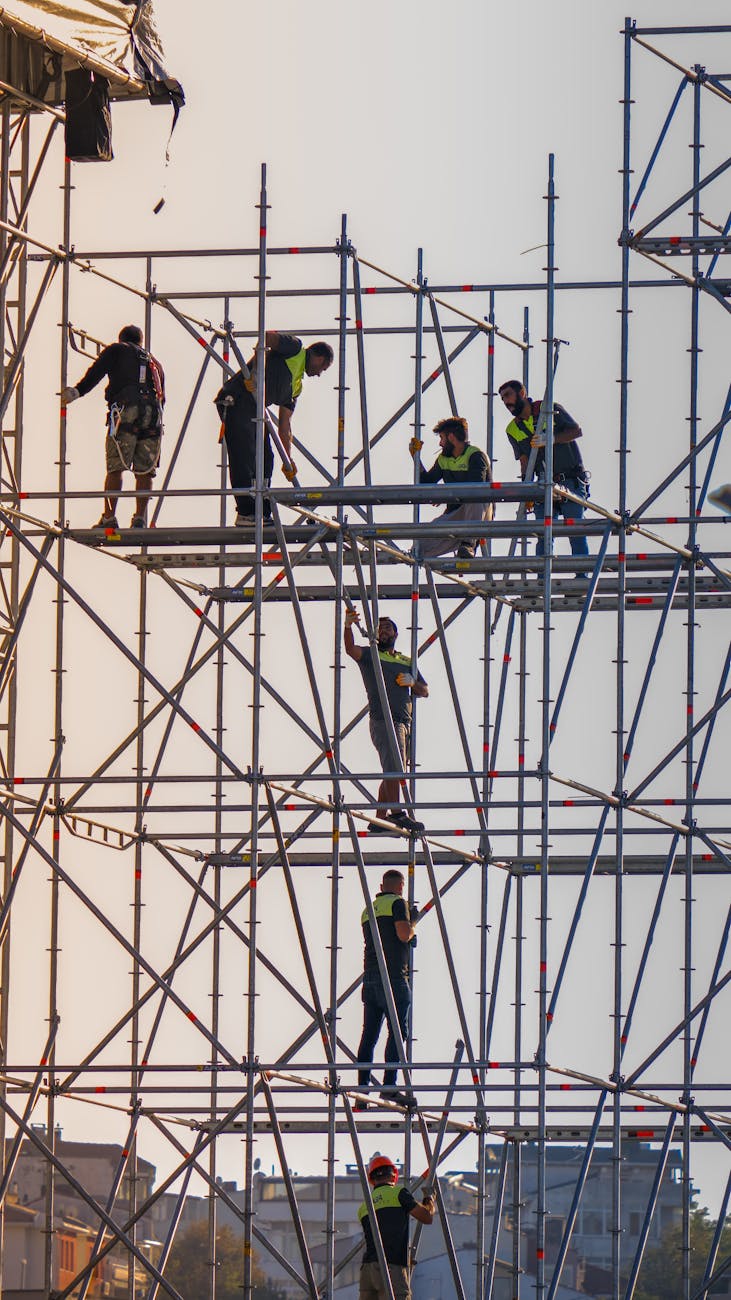
Risk Assessment & Job Safety Analysis (JSA)
Introduction
Risk Assessment and Job Safety Analysis (JSA) are essential processes in workplace safety management. They help identify potential hazards, evaluate risks, and implement control measures to prevent accidents and injuries.
- Risk Assessment is a systematic approach to recognizing hazards, analyzing their potential impact, and determining appropriate mitigation strategies.
- Job Safety Analysis (JSA) is a more detailed process that breaks down specific job tasks to identify hazards and define safe work procedures.
Both processes are crucial for maintaining a safe work environment, complying with regulations, and reducing workplace incidents.
Risk Assessment
Steps in Risk Assessment
- Identify Hazards – Recognize potential sources of harm (e.g., chemicals, machinery, ergonomic risks).
- Assess Risks – Evaluate the likelihood and severity of harm.
- Control Measures – Implement strategies to eliminate or reduce risks (e.g., PPE, engineering controls).
- Record Findings – Document hazards and actions taken.
- Review & Update – Regularly reassess risks as conditions change.
Benefits of Risk Assessment
- Prevents workplace injuries and illnesses.
- Ensures regulatory compliance (OSHA, ISO 45001).
- Improves employee awareness and safety culture.
Risk Assessment Example
Scenario: Chemical Handling in a Laboratory
Step 1: Identify Hazards
- Hazardous chemicals (e.g., sulfuric acid, solvents)
- Risk of spills, splashes, or inhalation exposure
- Improper storage leading to leaks
Step 2: Assess Risks
Hazard | Likelihood | Severity | Risk Level |
---|---|---|---|
Chemical splashes | Medium | High (burns, eye damage) | High |
Inhalation of fumes | Low | Medium (respiratory issues) | Medium |
Improper storage | Low | High (fire/chemical reaction) | Medium-High |
Step 3: Implement Control Measures
- Elimination/Substitution: Use less hazardous chemicals where possible.
- Engineering Controls: Install fume hoods and spill containment trays.
- Administrative Controls: Train employees on safe handling and emergency procedures.
- PPE: Require gloves, goggles, and lab coats.
Step 4: Record & Review
- Document findings in a risk register.
- Review annually or when new chemicals are introduced.
Job Safety Analysis (JSA)
Steps in JSA
- Select the Job – Choose high-risk or routine tasks for analysis.
- Break Down the Job – List each step involved.
- Identify Hazards – Determine risks at each step.
- Develop Controls – Define safe work practices.
- Implement & Train – Communicate procedures to workers.
Benefits of JSA
- Reduces workplace accidents.
- Enhances employee training and awareness.
- Improves operational efficiency by standardizing safe practices.
Job Safety Analysis (JSA) Example
Scenario: Changing a Flat Tire in an Auto Repair Shop
Step 1: Select the Job
- Task: Jacking up a vehicle and replacing a flat tire.
Step 2: Break Down the Job into Steps
- Park the vehicle on a flat, stable surface.
- Loosen lug nuts before lifting.
- Position the jack correctly.
- Lift the vehicle.
- Remove the flat tire and install the spare.
- Lower the vehicle and tighten lug nuts.
Step 3: Identify Hazards at Each Step
Job Step | Potential Hazard |
---|---|
1. Parking the vehicle | Vehicle may roll if not secured |
2. Loosening lug nuts | Strain injury from excessive force |
3. Positioning the jack | Jack may slip if on uneven ground |
4. Lifting the vehicle | Crush injury if jack fails |
5. Removing/installing tire | Back injury from improper lifting |
6. Lowering the vehicle | Finger pinch points |
Step 4: Develop Safe Work Procedures
- Parking: Use wheel chocks and engage parking brake.
- Loosening lug nuts: Use proper tools and body mechanics.
- Jack positioning: Place on solid, level ground; use jack stands.
- Lifting: Never place body parts under the vehicle.
- Tire handling: Lift with legs, not back.
- Lowering: Ensure hands are clear when lowering.
Step 5: Train Employees & Monitor Compliance
- Conduct hands-on training for new mechanics.
- Supervise initial attempts to ensure proper technique.
Conclusion
Risk Assessment and JSA are vital tools for ensuring workplace safety. By systematically identifying hazards and implementing control measures, organizations can protect employees, reduce incidents, and comply with safety regulations. Regular reviews and employee involvement further enhance their effectiveness.
HIRA Vs JSA Explained with 10 Examples of Each
What Is a Risk Matrix? (2025 Guide With Example)
FAQs
1. What is the difference between Risk Assessment and JSA?
- Risk Assessment evaluates overall workplace hazards, while JSA focuses on specific job tasks.
2. How often should Risk Assessments be conducted?
- They should be reviewed periodically or when new hazards are introduced (e.g., new equipment, processes).
3. Who should be involved in a JSA?
- Supervisors, safety officers, and employees performing the job should collaborate for accurate hazard identification.
4. Can JSA be used for office jobs?
- Yes, even low-risk jobs benefit from JSA to prevent ergonomic or slip/trip hazards.
5. What are common control measures in Risk Assessment?
- Elimination, substitution, engineering controls, administrative controls, and PPE.
By integrating Risk Assessment and JSA into workplace practices, organizations can foster a proactive safety culture and minimize occupational risks.