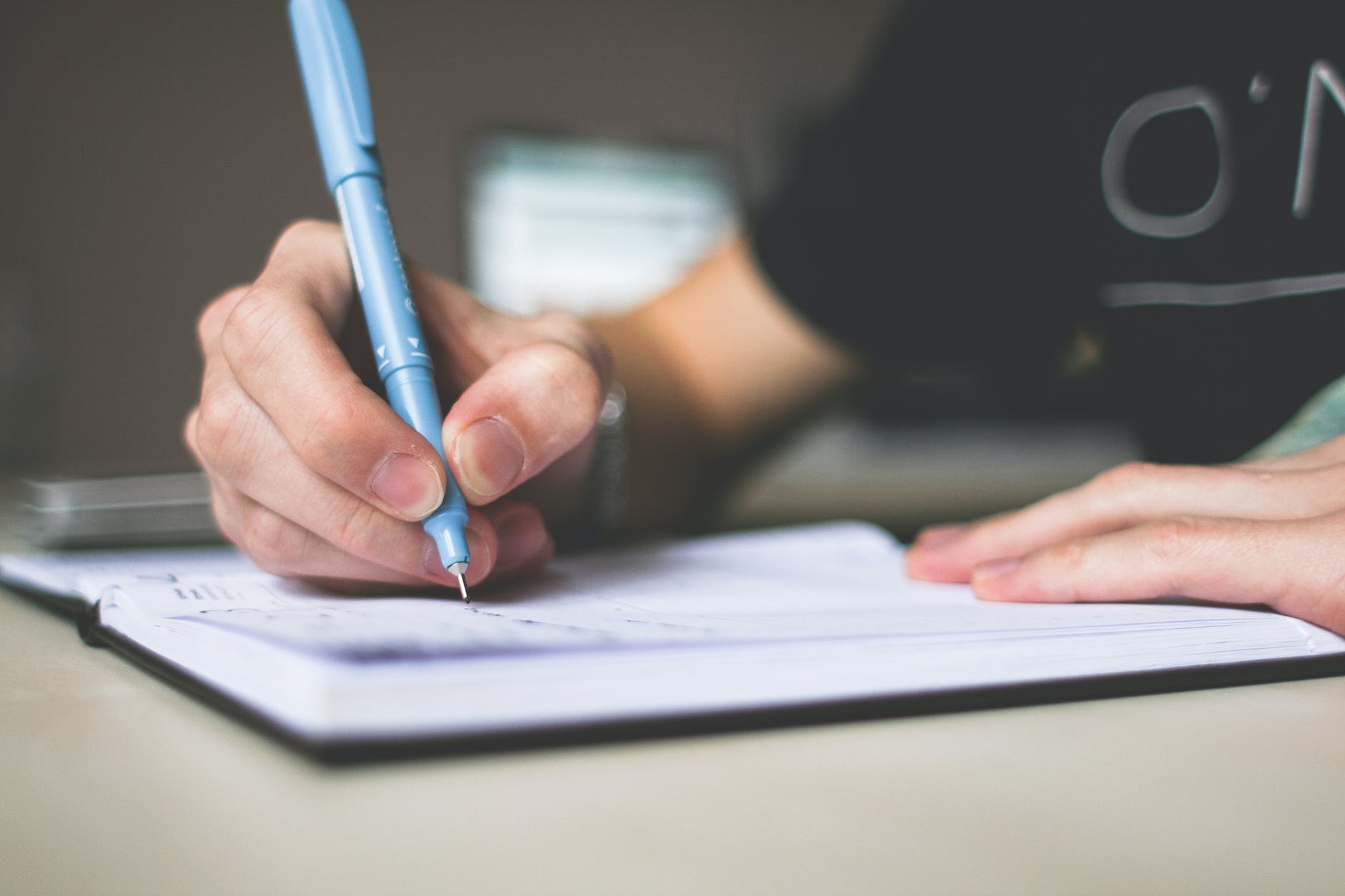
OSHA Safety and Health Management System: Creating a Secure Workplace
Introduction
In today’s dynamic business environment, ensuring the safety and health of employees has become a paramount concern for organizations. The Occupational Safety and Health Administration (OSHA) provides guidelines and standards to help businesses establish effective safety and health management systems. Let’s delve into the world of OSHA safety and health management and understand how it can benefit your organization.
Understanding OSHA Standards
OSHA, a regulatory body, sets and enforces safety and health standards to ensure workplaces are free from hazards. Companies must comply with OSHA regulations, and having a robust safety and health management system is crucial for adherence. This includes understanding the specific standards related to your industry and implementing measures to meet compliance.
Benefits of Implementing OSHA Guidelines
Implementing OSHA guidelines goes beyond mere compliance; it brings substantial benefits to your organization. Enhanced workplace safety reduces accidents and injuries, fostering a positive work environment. Furthermore, compliance with OSHA regulations helps organizations avoid legal issues and penalties, ensuring a smooth operation.
Components of an Effective Safety and Health Management System
A successful safety and health management system involves a combination of key components. Conducting thorough risk assessments, identifying hazards, and implementing preventive measures are integral parts. Employee training and awareness programs play a crucial role, ensuring everyone understands and follows safety protocols. Additionally, having clear incident reporting and investigation procedures is essential for a proactive approach to safety.
Creating a Safety Culture
Building a safety culture within your organization is more than just following regulations—it’s about fostering a mindset that prioritizes safety. Leaders play a vital role in promoting a culture where safety is not just a set of rules but a way of life for every employee.
Integration with Other Business Processes
Safety should not be a standalone element but seamlessly integrated into daily operations. Aligning safety goals with overall business objectives ensures that safety becomes a natural part of the organizational culture, rather than an isolated practice.
Employee Involvement and Communication
Active employee participation is crucial for the success of any safety program. Encourage open communication channels for reporting concerns and incidents. Regular safety meetings and updates keep employees informed and engaged in the safety initiatives.
Periodic Audits and Assessments
Regular evaluations and audits are essential for ensuring the effectiveness of your safety program. Identifying areas for improvement and making necessary adjustments based on assessments contribute to the continuous enhancement of safety measures.
Training Programs for Employees
Designing effective training modules tailored to your industry and specific risks is vital. Regular training keeps employees informed about the latest safety regulations and equips them with the knowledge to handle potential hazards.
Utilizing Technology for Safety Management
In the digital age, technology plays a pivotal role in enhancing safety measures. Various tools and software are available to streamline safety processes, from incident reporting to tracking employee training progress.
Case Studies of Successful Implementations
Examining case studies of organizations that have successfully implemented OSHA guidelines provides valuable insights. Learning from their experiences can help other companies navigate challenges and adopt best practices.
Challenges in Implementing OSHA Guidelines
While the benefits are clear, implementing OSHA guidelines comes with challenges. Identifying common hurdles, such as resistance to change or resource constraints, and developing strategies to overcome them are crucial steps in ensuring successful implementation.
Measuring the Success of a Safety Program
Key performance indicators (KPIs) are essential for measuring the success of your safety program. Tracking incident rates, employee participation in training, and timely reporting and resolution of safety concerns are metrics that can gauge the effectiveness of your safety initiatives.
Future Trends in OSHA Safety Management
As technology advances, new trends emerge in safety management. Keeping an eye on these trends and being prepared for changes in OSHA regulations ensures that your organization stays ahead in providing a safe working environment.
The Occupational Safety and Health Administration (OSHA) Safety and Health Management System (SHMS) is a comprehensive framework designed to help organizations create and maintain a safe and healthy work environment. The primary goal of the SHMS is to prevent workplace injuries, illnesses, and fatalities by promoting proactive safety measures and continuous improvement.
Key elements of OSHA's Safety and Health Management System include:
- Management Leadership and Employee Involvement:
- Top management commitment to safety.
- Involvement of employees in safety decision-making processes.
- Worksite Analysis:
- Regular hazard identification and assessment.
- Evaluation of existing safety programs and processes.
- Hazard Prevention and Control:
- Implementation of effective controls to eliminate or minimize hazards.
- Emergency response planning and procedures.
- Training and Education:
- Providing relevant safety training for all employees.
- Ensuring that employees understand potential hazards and safe work practices.
- Evaluation of Program Effectiveness:
- Continuous monitoring and evaluation of the safety program.
- Making adjustments and improvements based on evaluation results.
- Communication and Coordination:
- Clear communication of safety policies and procedures.
- Collaboration among different levels of the organization to address safety concerns.
- Recordkeeping and Documentation:
- Maintaining accurate records of safety incidents, training, and inspections.
- Documenting corrective actions taken to address identified hazards.
- Employee Rights and Responsibilities:
- Ensuring that employees are aware of their rights related to safety.
- Encouraging employees to actively participate in safety initiatives.
- Contractor and Vendor Management:
- Establishing safety expectations for contractors and vendors.
- Ensuring that external parties adhere to safety standards while working on-site.
- Continuous Improvement:
- Establishing a culture of continuous improvement in safety performance.
- Learning from incidents and near misses to prevent future occurrences.
Organizations can adopt the OSHA SHMS principles and tailor them to their specific industry, size, and nature of operations. Implementing an effective safety and health management system not only helps in compliance with OSHA regulations but also contributes to creating a safer and healthier workplace for employees. Regular reviews and updates to the SHMS ensure its ongoing relevance and effectiveness in preventing accidents and promoting overall well-being in the workplace.
Conclusion
In conclusion, prioritizing OSHA safety and health management systems is not just a regulatory requirement; it’s an investment in the well-being of your employees and the success of your organization. Creating a secure workplace involves a multifaceted approach, from understanding regulations to fostering a safety culture and embracing technological advancements.
OSHA Safety Officer Certification
OSHA Safety Manager Requirements
Frequently Asked Questions (FAQs)
- How often should safety training be conducted for employees?
- Safety training should be conducted regularly, with refresher courses at least annually, to ensure employees are well-informed about the latest regulations and practices.
- What are some common challenges in implementing OSHA guidelines?
- Common challenges include resistance to change, lack of resources, and the need for cultural shifts within the organization.
- How can technology assist in safety management?
- Technology can assist in safety management through tools and software for incident reporting, training tracking, and real-time monitoring of safety metrics.
- What are the key performance indicators (KPIs) for measuring safety program success?
- KPIs include incident rates, employee participation in training, and the timely reporting and resolution of safety concerns.
- Where can I get more information about OSHA guidelines and standards?
- For detailed information on OSHA guidelines and standards, visit the official OSHA website or consult with a certified safety professional.