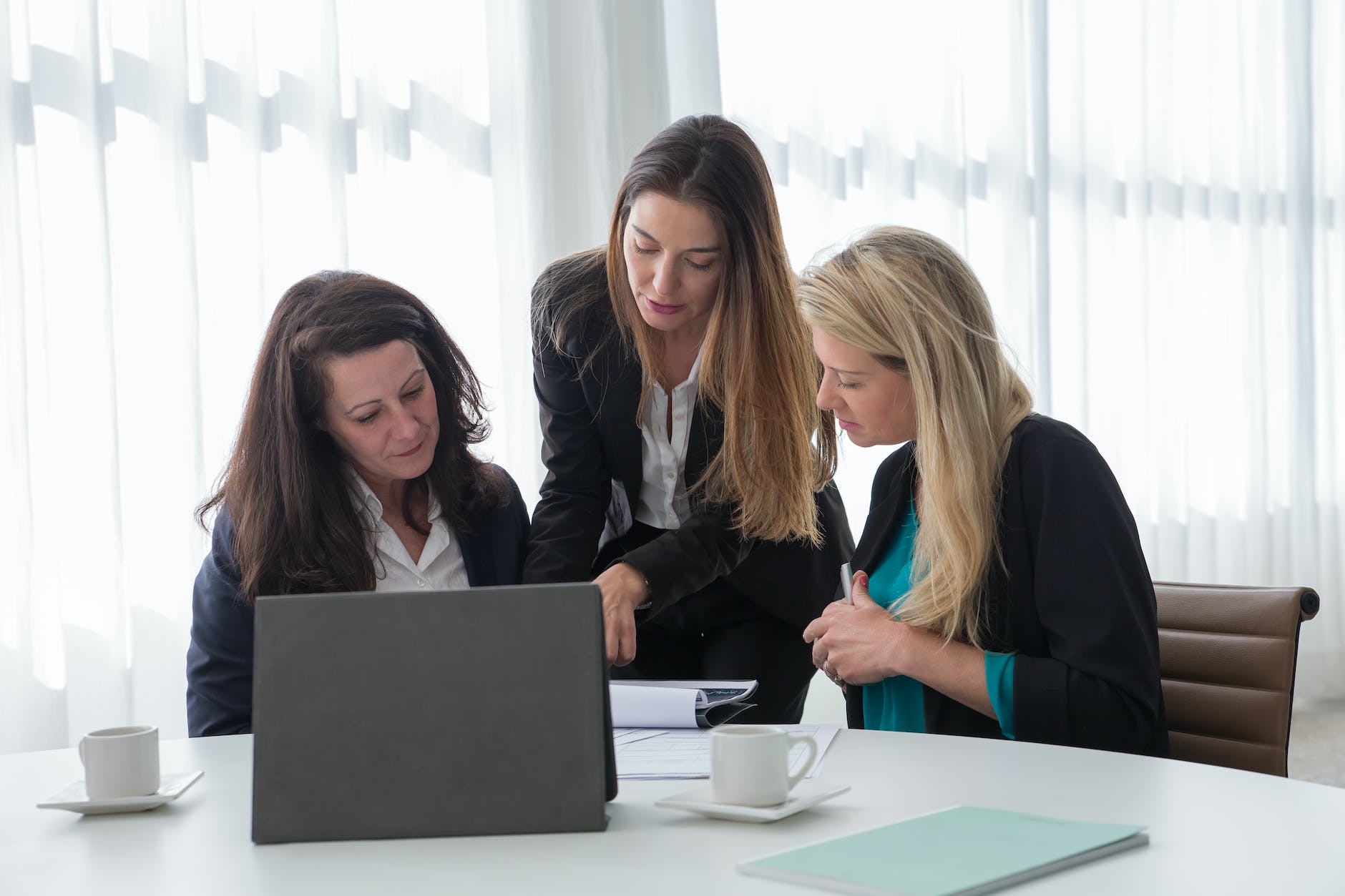
OSHA Monthly Safety Topics 2024
Introduction
OSHA Monthly Safety Topics 2024 : In the dynamic landscape of workplaces, safety remains a paramount concern. The Occupational Safety and Health Administration (OSHA) plays a pivotal role in ensuring that businesses adhere to stringent safety regulations. One noteworthy aspect of OSHA’s strategy is the focus on monthly safety topics, a proactive approach to address evolving risks and challenges.
OSHA’s Role in Workplace Safety
OSHA, established to enforce safety and health regulations, strives to create a secure working environment for employees across industries. By setting and enforcing standards, OSHA significantly contributes to reducing workplace accidents and promoting overall well-being.
Evolution of Monthly Safety Topics
The concept of monthly safety topics has evolved over the years. Initially introduced as a means to address specific hazards, OSHA now tailors these topics to reflect current industry trends and emerging risks. This adaptive approach ensures that safety measures remain relevant in an ever-changing work environment.
Significance of Monthly Safety Topics
The implementation of monthly safety topics is not merely a bureaucratic requirement; it is a proactive strategy to reduce accidents and enhance employee awareness. By focusing on specific issues each month, companies can systematically address potential hazards, fostering a culture of safety.
OSHA Monthly Safety Topics for 2024
As we step into 2024, OSHA has identified key safety topics crucial for workplace well-being. These topics are carefully chosen based on emerging risks and industry-specific concerns. Understanding these topics is essential for companies aiming to prioritize safety in their operations.
Here are some potential OSHA (Occupational Safety and Health Administration) monthly safety topics for the year 2024:
January: Emergency Preparedness
- Focus on creating and practicing emergency response plans.
- Conduct fire drills and ensure all employees know evacuation routes.
February: Ergonomics in the Workplace
- Address ergonomic issues to prevent musculoskeletal disorders.
- Provide training on proper workstation setup and posture.
March: Hazard Communication
- Emphasize the importance of clear communication about workplace hazards.
- Train employees on the use of safety data sheets (SDS) and labels.
April: Fall Prevention
- Highlight the risks of falls and methods to prevent them.
- Inspect and maintain fall protection equipment.
May: Electrical Safety
- Educate employees on electrical hazards and safe work practices.
- Conduct electrical equipment inspections and address any issues.
June: Heat Stress Prevention
- Implement measures to prevent heat-related illnesses.
- Provide training on recognizing and responding to heat stress.
July: Machine Guarding
- Review and update machine guarding procedures.
- Train employees on the importance of machine safety.
August: Respiratory Protection
- Evaluate respiratory hazards in the workplace.
- Ensure proper use and maintenance of respiratory protection equipment.
September: Hazardous Materials Handling
- Review procedures for the safe handling, storage, and disposal of hazardous materials.
- Conduct inventory checks and update safety protocols.
October: Confined Space Safety
- Identify confined spaces in the workplace.
- Train employees on proper entry procedures and rescue protocols.
November: Personal Protective Equipment (PPE)
- Ensure employees are using appropriate PPE.
- Conduct a PPE assessment and provide necessary equipment.
December: Winter Weather Safety
- Address cold weather hazards and precautions.
- Train employees on winter driving safety and cold stress prevention.
Remember to customize these topics based on the specific hazards and needs of your workplace. Regular training and reinforcement of safety practices are essential for maintaining a safe working environment.
Implementing Safety Measures
Adhering to OSHA guidelines involves more than just ticking boxes. It requires a proactive approach to implement safety measures effectively. From regular equipment maintenance to creating emergency response plans, companies must take tangible steps to ensure a secure working environment.
Employee Training and Awareness
Safety measures are only effective when employees are well-informed. Ongoing training programs are essential to communicate the importance of safety practices and educate employees on the latest protocols. Effectively conveying this information fosters a sense of responsibility among employees.
Technology and Safety
In the digital age, technology plays a crucial role in enhancing workplace safety. From smart sensors to virtual reality training, innovative solutions are transforming how companies approach safety. Embracing these technologies can significantly contribute to accident prevention.
Challenges in Safety Implementation
Despite the clear benefits, companies often face challenges in implementing safety measures. Whether due to budget constraints or resistance to change, overcoming these obstacles requires a strategic approach. Identifying and addressing these challenges head-on is crucial for success.
OSHA’s Support Resources
OSHA provides a wealth of resources to support companies in their safety endeavors. From informative guides to training materials, leveraging these resources enhances a company’s ability to implement effective safety measures.
Conclusion
In conclusion, prioritizing workplace safety is not just a legal requirement but a moral obligation. OSHA’s monthly safety topics serve as a roadmap for companies to navigate potential hazards and create a secure working environment. By staying informed, implementing proactive measures, and fostering a culture of safety, businesses can ensure the well-being of their most valuable asset—their employees.
20 Safety Training Topics for Your Workplace
What is Safety Induction Training?
Safety Induction Training for New Employees
Frequently Asked Questions (FAQs)
- What is the purpose of OSHA’s monthly safety topics?
- OSHA’s monthly safety topics aim to address specific workplace hazards systematically and proactively.
- How does technology contribute to workplace safety?
- Technology, such as smart sensors and virtual reality training, enhances workplace safety by providing innovative solutions for accident prevention.
- What are the common challenges in implementing safety measures?
- Challenges in safety implementation can include budget constraints, resistance to change, and inadequate training.
- Why is the human element crucial in maintaining workplace safety?
- While technology is essential, the commitment of employees to safety is vital in creating a secure working environment.
- Where can companies find OSHA’s support resources?
- OSHA provides a variety of resources on its official website, offering guides, training materials, and other valuable information.