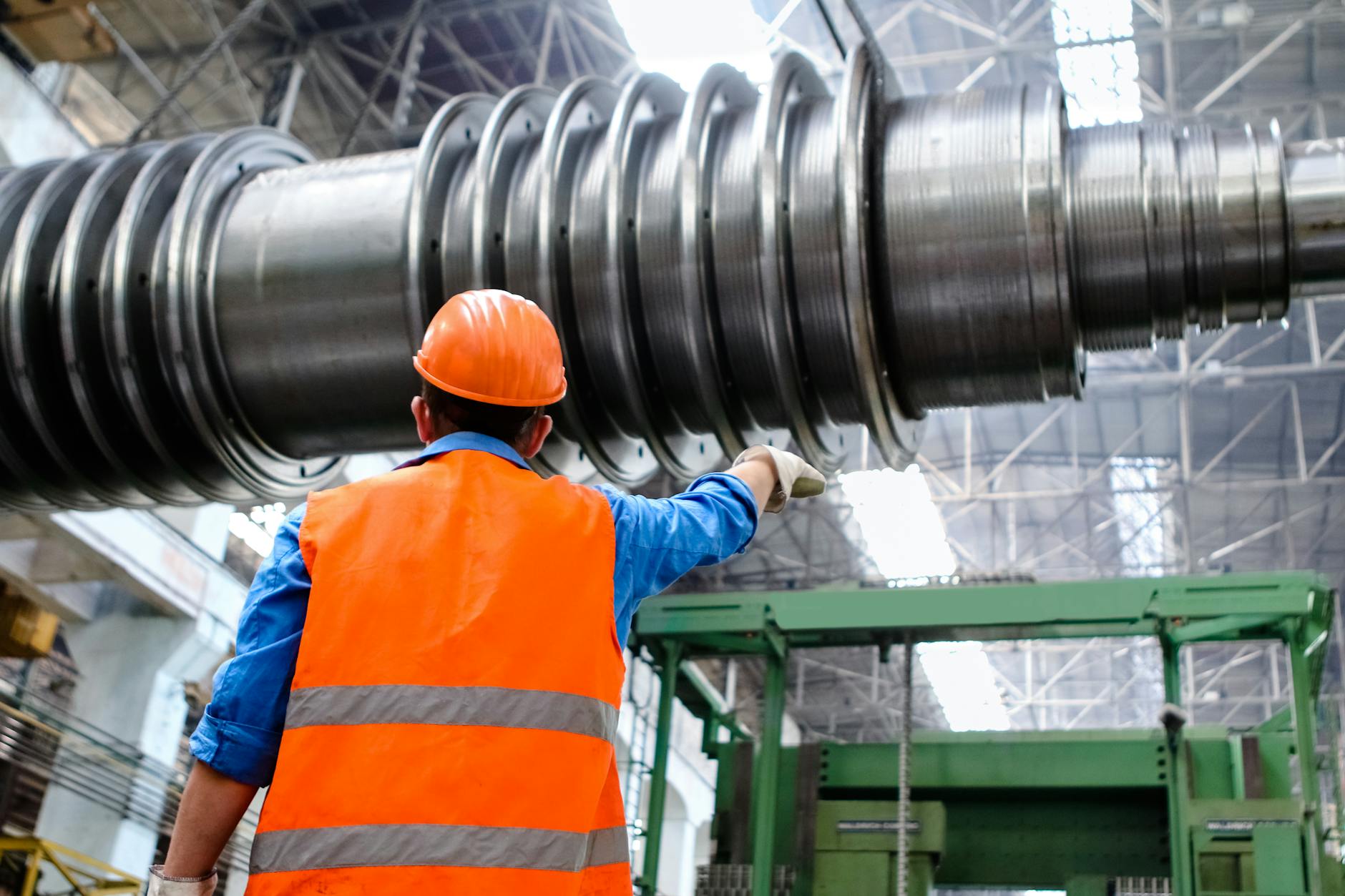
Manufacturing Safety: Machine Guarding & Lockout-Tagout (LOTO)
Introduction
Manufacturing environments contain heavy machinery and equipment that pose serious hazards, including crushing, entanglement, and electrical risks. Proper safety measures—such as Machine Guarding and Lockout-Tagout (LOTO)—are essential to prevent injuries and fatalities.
This training covers:
- Machine Guarding – Preventing contact with moving parts
- Lockout-Tagout (LOTO) – Safely de-energizing equipment for maintenance
Adhering to OSHA standards and best practices ensures a safer workplace for all employees.
Machine Guarding Safety
Machine guards are physical barriers that prevent workers from coming into contact with hazardous moving parts.
Key Safety Measures:
- Use Fixed Guards – Permanent barriers for high-risk areas (e.g., presses, saws).
- Install Interlocked Guards – Automatically shuts off machinery when opened.
- Ensure Adjustable Guards – For varying material sizes (e.g., conveyor belts).
- Conduct Regular Inspections – Check for damaged or missing guards before operation.
- Train Employees – Workers must never remove or bypass guards.
Common Hazards Without Proper Guarding:
- Amputations from rotating parts
- Crushing injuries in pinch points
- Flying debris causing eye injuries
Lockout-Tagout (LOTO) Safety
LOTO procedures ensure machines are properly shut off and cannot be restarted during maintenance or servicing.
Key Safety Measures:
- Identify Energy Sources – Electrical, hydraulic, pneumatic, mechanical, etc.
- Shut Down Equipment Properly – Follow manufacturer guidelines.
- Apply Locks & Tags – Only the authorized worker removes them.
- Verify Zero Energy State – Test that equipment cannot restart.
- Train All Employees – Workers must understand LOTO procedures.
When is LOTO Required?
- Servicing or repairing machinery
- Clearing jams or blockages
- Performing maintenance on electrical systems
Conclusion
Manufacturing safety relies on proper machine guarding and strict LOTO compliance to prevent catastrophic injuries. By following OSHA regulations (29 CFR 1910.147 for LOTO and 29 CFR 1910.212 for machine guarding), companies can reduce workplace accidents and ensure employee safety.
Regular training, hazard assessments, and enforcement of safety protocols are critical to maintaining a secure manufacturing environment.
National Fire Service Day 2025: History, Significance, and Key Facts
How to Implement Behavior-Based Safety (BBS) – 10 Key Questions
Construction Safety Scaffolding, Excavation, and Crane Safety
Slip, Trip, and Fall Prevention Strategies
Oil & Gas Industry HSE Challenges and Solutions
FAQs
1. What are the types of machine guards?
- Fixed guards (permanent barriers)
- Interlocked guards (disable machine when opened)
- Adjustable guards (flexible for different operations)
- Self-adjusting guards (move with the material)
2. Who can remove a lock in a LOTO procedure?
Only the authorized employee who applied the lock can remove it, unless a formal shift-change procedure is followed.
3. What is the difference between lockout and tagout?
- Lockout uses a physical lock to prevent machine activation.
- Tagout uses a warning tag but does not physically prevent operation (requires additional safety measures).
4. Can machine guards be removed temporarily?
No, guards should never be removed during operation. If maintenance requires removal, LOTO must be applied first.
5. What are common LOTO violations?
- Failure to lockout all energy sources
- Not verifying zero energy state
- Using tags without locks when possible
By implementing these safety practices, manufacturers can drastically reduce workplace injuries and ensure compliance with safety regulations. Stay safe!