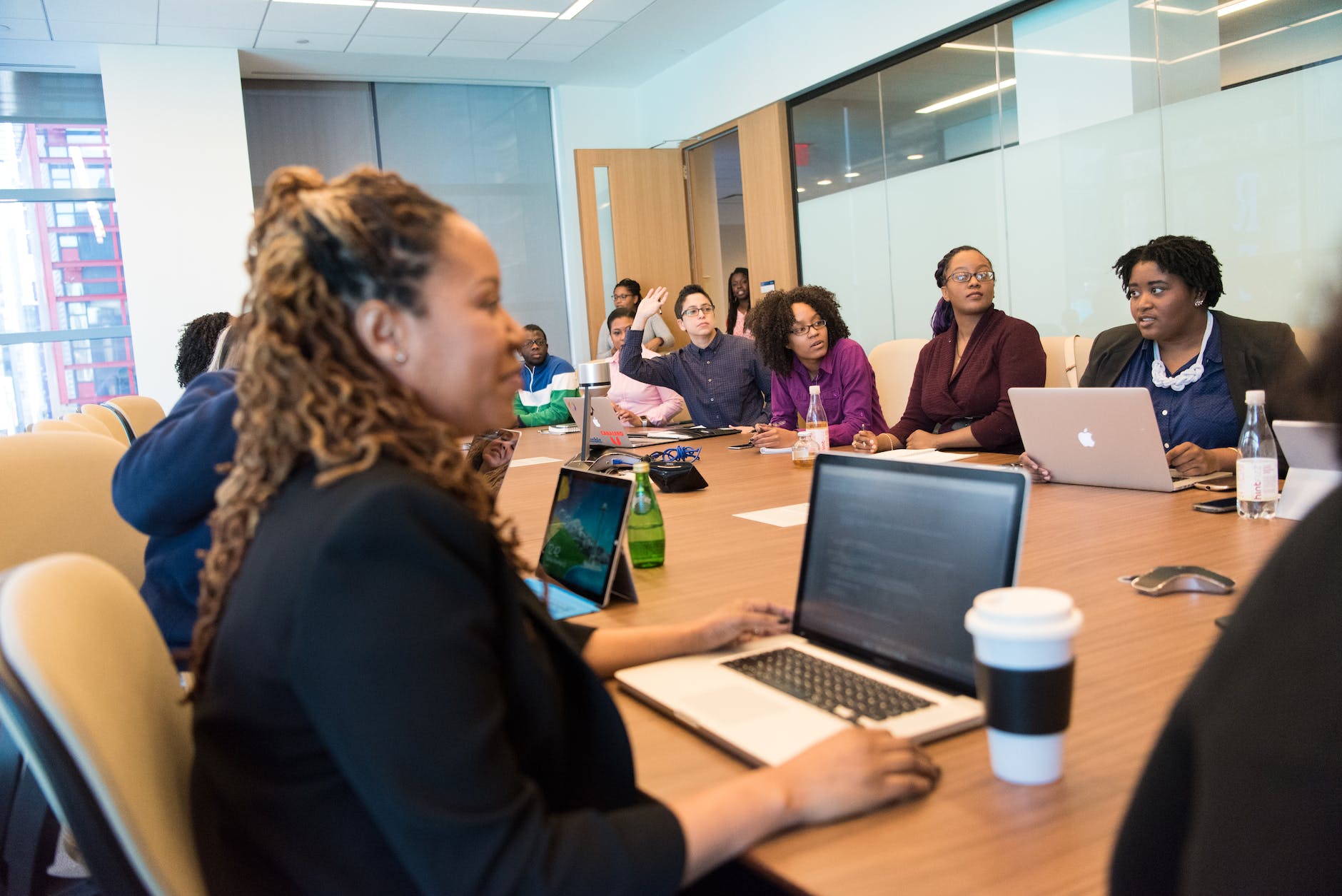
LOTO Safety Training: Ensuring Workplace Safety Through Lockout Tagout Procedures
Introduction
LOTO Safety Training :Workplace safety is a paramount concern for both employers and employees. Accidents and injuries not only impact the well-being of workers but can also result in financial losses for businesses. Lockout Tagout (LOTO) safety training is a critical component of maintaining a safe work environment. In this article, we will explore the importance of LOTO safety training, its procedures, and its role in preventing workplace accidents.
The Importance of LOTO Safety Training
Ensuring the safety of employees should be a top priority for any organization. LOTO safety training plays a vital role in achieving this goal. This training is designed to prevent accidents caused by the unexpected energization or start-up of machinery and equipment during maintenance or servicing.
Understanding Lockout Tagout (LOTO)
LOTO is a safety procedure that involves the isolation and de-energization of machinery or equipment before maintenance or repair work begins. This is done by physically locking the equipment and tagging it to indicate that it should not be operated until the lock and tag are removed. LOTO procedures are designed to protect employees from hazardous energy sources and potential accidents.
Legal Requirements for LOTO
There are stringent legal requirements in place to ensure that LOTO procedures are followed. OSHA (Occupational Safety and Health Administration) mandates that employers establish and implement an energy control program. Failure to comply with these regulations can result in severe penalties and fines.
LOTO Procedures and Guidelines
LOTO procedures can vary depending on the equipment and industry. However, some common steps include:
1. Notify Employees
- Inform employees about the nature and purpose of the LOTO procedure.
2. Equipment Shutdown
- Turn off the machinery or equipment and follow proper shutdown procedures.
3. Isolation
- Physically isolate the equipment from its energy source.
4. Lockout and Tagout
- Lock the equipment using authorized locks and tag it with specific information.
5. Verification
- Ensure that the equipment is in a de-energized state.
6. Maintenance or Servicing
- Conduct maintenance or servicing work safely.
Equipment Inspection and Maintenance
Regular inspection and maintenance of LOTO devices and equipment are essential to guarantee their effectiveness. Damaged locks or tags can compromise safety. Employers should establish an inspection schedule to ensure that all LOTO equipment is in optimal condition.
Employee Training and Education
Proper training is crucial for both employees and employers. Employees need to understand the LOTO procedures, while employers must provide training and assess employee competence. This education helps in preventing accidents and ensuring that everyone follows the established safety protocols.
Scenario: Preventing a Conveyor Belt Accident
Imagine a bustling manufacturing facility where a team is responsible for maintaining and servicing the conveyor belt system that transports heavy materials within the factory. The workers are experienced, and they have been trained in LOTO safety procedures. Let’s see how this training comes into play:
Scenario Part 1: LOTO Training and Preparation
- Employee Training: The employees involved in conveyor belt maintenance have undergone comprehensive LOTO safety training. They are well aware of the potential hazards and know the correct procedures for lockout and tagout.
- Pre-Maintenance Planning: Before any maintenance work begins, the team gathers for a pre-maintenance meeting. They discuss the tasks at hand, identify the equipment to be worked on, and ensure everyone understands their roles.
Scenario Part 2: The Maintenance Task
- Equipment Shutdown: The conveyor belt system is scheduled for routine maintenance, and the employees begin by safely shutting down the system following the standard operating procedures.
- Isolation and LOTO: After the equipment is shut down, each employee isolates the segment of the conveyor belt they will work on. They lock out the energy sources and tag them with clear and standardized tags that bear their name, date, and the purpose of the lockout.
- Verification: Before starting work, each employee double-checks that the equipment is de-energized by attempting to start it, which should fail due to the proper LOTO procedures.
Scenario Part 3: Preventing Accidents
- Maintenance Tasks: The employees carry out their maintenance tasks, such as cleaning, repairing, and lubricating the conveyor belt. They do so without any fear of sudden start-ups or unexpected movements.
Scenario Part 4: Task Completion and Safety Measures
- Task Completion: After all maintenance tasks are completed, the employees remove their locks and tags, restoring the conveyor belt to operational status.
- Safety First: The team conducts one final check to ensure that the conveyor belt functions as expected. They also verify that no tools or equipment are left behind in the machinery.
Scenario Part 5: The Importance of LOTO Training
- Success and Safety: In this scenario, the LOTO safety training pays off. No accidents or injuries occur during the maintenance work, and the employees complete their tasks safely and efficiently.
- Compliance with Regulations: By following proper LOTO procedures, the facility remains in compliance with OSHA regulations, preventing potential fines and penalties.
This scenario demonstrates how LOTO safety training, when diligently followed, can prevent workplace accidents, ensuring the safety of employees and the smooth operation of machinery in a manufacturing environment. It also highlights the importance of continuous training, awareness, and adherence to safety protocols.
Types of LOTO (Lockout-Tagout)
LOTO in Various Industries
LOTO safety training is applicable across various industries, including manufacturing, construction, and healthcare. Each industry has specific equipment and energy sources, but the principles of LOTO remain consistent.
Case Studies: The Consequences of LOTO Failure
Several case studies highlight the severe consequences of LOTO failures. These real-life examples underscore the importance of strict adherence to LOTO procedures to prevent accidents and protect workers.
Benefits of Effective LOTO Programs
Implementing an effective LOTO program offers numerous benefits, including reduced workplace accidents, improved employee safety, and compliance with legal regulations. It also contributes to increased productivity as a well-maintained and safe workplace is more efficient.
Common LOTO Misconceptions
There are several misconceptions regarding LOTO procedures. We will address these misconceptions to ensure a clear understanding of the process.
The Role of Employers and Employees
Both employers and employees play crucial roles in the success of LOTO safety programs. Employers must provide the necessary training and resources, while employees are responsible for following LOTO procedures diligently.
Implementing an Effective LOTO Program
Establishing an effective LOTO program involves meticulous planning, employee involvement, and regular program evaluations. This section will provide guidance on how to set up a successful LOTO safety program.
Measuring LOTO Program Effectiveness
Evaluating the effectiveness of a LOTO program is essential. This section will discuss key performance indicators and methods to assess program success.
Conclusion
In conclusion, Lockout Tagout (LOTO) safety training is a critical component of maintaining a safe workplace. It is essential for preventing accidents, ensuring employee safety, and complying with legal requirements. By implementing effective LOTO procedures and programs, employers can create a safer and more productive work environment.
FAQs
1. Why is LOTO safety training important?
LOTO safety training is crucial because it prevents accidents during equipment maintenance or servicing, ensuring employee safety and legal compliance.
2. What are the legal requirements for LOTO?
OSHA mandates that employers establish and implement energy control programs, and failure to comply can result in severe penalties and fines.
3. Are LOTO procedures the same for all industries?
LOTO procedures may vary by industry, but the core principles remain consistent across various sectors.
4. How can I measure the effectiveness of a LOTO program?
Measuring the effectiveness of a LOTO program can be done through performance indicators and regular evaluations.
5. What are the consequences of LOTO failures?
LOTO failures can lead to severe accidents and injuries, making it vital to follow LOTO procedures rigorously.
Hi there, where can I enroll this course?