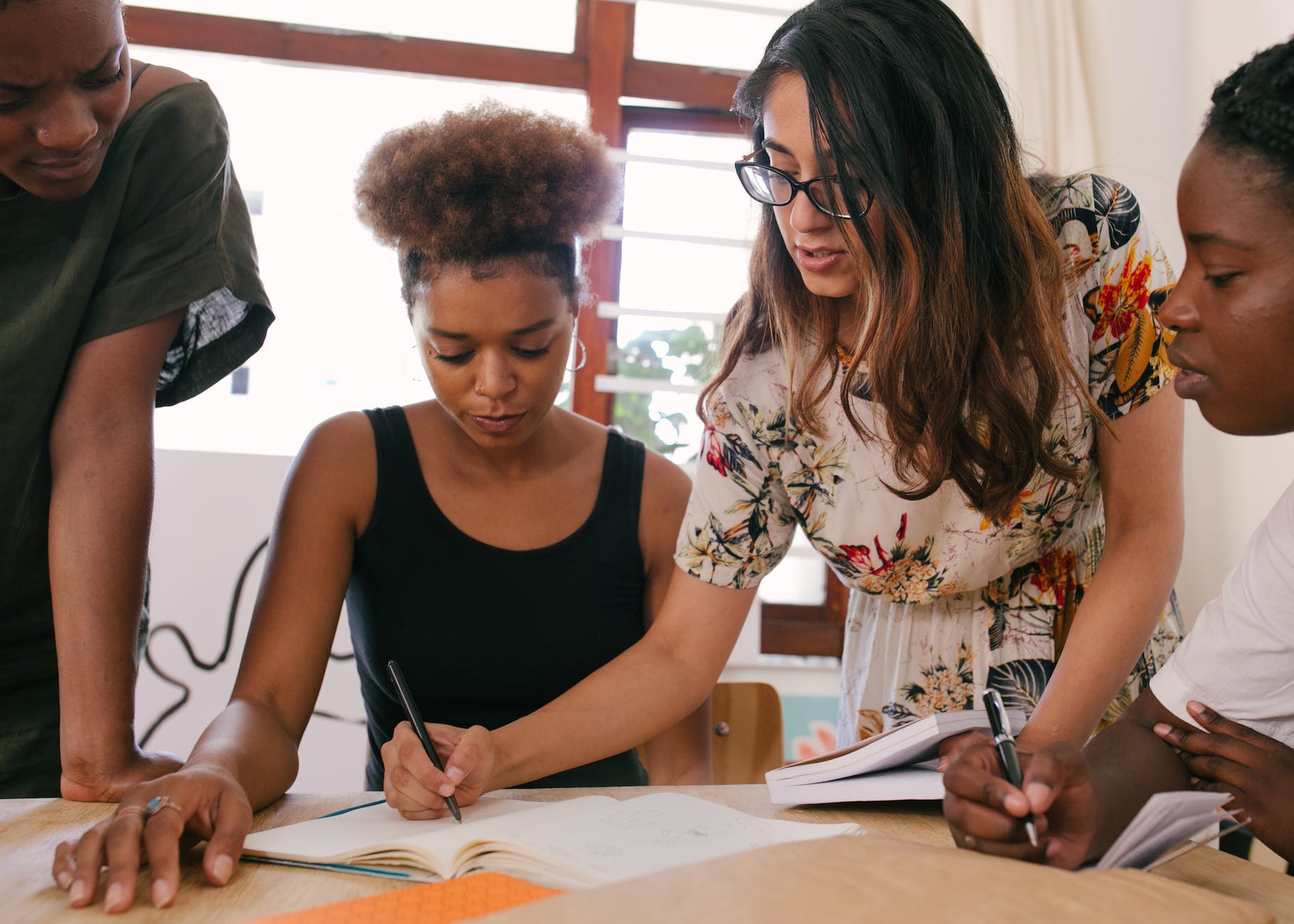
Lockout Tagout Compliance: Ensuring Workplace Safety
Lockout Tagout Compliance : In today’s fast-paced industrial landscape, workplace safety is of paramount importance. One critical aspect of ensuring employee safety, especially in industries dealing with machinery and equipment, is Lockout Tagout (LOTO) compliance. This practice aims to prevent unexpected equipment startup and hazardous energy release during maintenance or servicing. In this article, we’ll delve into the significance of LOTO compliance, its key components, implementation strategies, and its role in preventing accidents. So, let’s explore how Lockout Tagout compliance can be the cornerstone of workplace safety.
Understanding Lockout Tagout (LOTO)
Lockout Tagout (LOTO) refers to a set of safety procedures designed to protect employees from hazardous energy sources during maintenance and servicing activities. These sources include electrical, mechanical, hydraulic, pneumatic, chemical, and thermal energy. The LOTO process involves isolating the energy sources, locking them out to prevent accidental activation, and placing tags to indicate the inaccessibility of the equipment.
The Importance of LOTO Compliance
LOTO compliance is vital because it prevents numerous accidents that can result from the unexpected startup of equipment. It ensures that machinery or equipment undergoing maintenance cannot be powered on, eliminating the risk of injury to workers. By adhering to LOTO procedures, companies prioritize the safety of their employees and create a safer working environment.
Key Components of a Successful LOTO Program
Identification of Energy Sources
Before implementing LOTO procedures, it’s crucial to identify all energy sources associated with each piece of equipment. This comprehensive identification helps in formulating effective lockout tagout procedures.
Written Procedures and Guidelines
Clear and well-documented procedures are the backbone of LOTO compliance. These guidelines outline the steps for isolating energy sources, affixing locks and tags, and verifying the equipment’s de-energized state before maintenance.
Employee Training and Awareness
Proper training is key to LOTO success. Employees involved in maintenance activities must be educated about the importance of LOTO, the correct procedures, and the potential consequences of non-compliance.
Lockout Tagout Equipment
The right tools make a difference. Lockout tagout equipment, such as padlocks, tags, lockout hasps, and circuit breaker locks, are essential for effective energy isolation.
Implementing a Robust LOTO Procedure
Conducting a Comprehensive Risk Assessment
Before crafting LOTO procedures, a thorough risk assessment is essential. This assessment identifies potential hazards, evaluates risks, and guides the development of appropriate lockout tagout measures.
Developing LOTO Procedures
LOTO procedures should be tailored to each piece of equipment. They should detail the steps to de-energize, lock, and tag equipment, as well as the protocols for removing locks and tags after maintenance.
Employee Training and Communication
Training sessions should emphasize not only the procedural aspects of LOTO but also the rationale behind them. Employees need to understand the potential dangers and their role in maintaining a safe work environment.
Regular Audits and Reviews
A successful LOTO program requires consistent evaluation. Regular audits ensure that procedures are followed correctly, equipment is functioning optimally, and any necessary adjustments are made.
Benefits of LOTO Compliance
Prevention of Accidents
LOTO compliance significantly reduces the risk of accidents caused by unexpected equipment activation. It safeguards employees from injury and protects company assets from damage.
Enhancement of Workplace Safety Culture
By prioritizing safety through LOTO compliance, companies foster a culture of vigilance and responsibility among employees, resulting in a safer overall work environment.
Legal and Regulatory Compliance
Many industries are subject to regulations that mandate LOTO compliance. Adhering to these regulations not only prevents penalties but also demonstrates a commitment to safety.
Challenges in LOTO Implementation
Resistance to Change
Implementing LOTO procedures might face resistance due to a shift in established work practices. Addressing concerns and providing comprehensive training can alleviate this resistance.
Ensuring Consistent Adherence
Maintaining consistent LOTO compliance can be challenging. Regular training, audits, and continuous improvement efforts are essential to overcome this challenge.
Real-world Examples of Successful LOTO Programs
General Electric (GE)
GE’s robust LOTO program involves thorough training, detailed procedures, and regular audits. This has resulted in a significant reduction in accidents during maintenance.
Lockheed Martin
Lockheed Martin emphasizes LOTO compliance through a company-wide safety culture. Their approach has led to enhanced employee awareness and a substantial decrease in incidents.
Continuous Improvement and Evolution of LOTO Practices
As technology and processes evolve, so do LOTO practices. Companies should stay updated with the latest safety standards and continuously improve their LOTO procedures.
Conclusion
Lockout Tagout compliance is a cornerstone of workplace safety. By implementing comprehensive procedures, providing proper training, and fostering a culture of safety, companies can protect their employees, prevent accidents, and ensure regulatory compliance. Prioritizing LOTO is a proactive step towards a safer and more productive work environment.
Industrial Safety Protocols for LOTO (Lockout-Tagout)
FAQs (Frequently Asked Questions)
Q1: What industries require Lockout Tagout compliance? Lockout Tagout compliance is essential in industries involving machinery, equipment, and hazardous energy sources, such as manufacturing, construction, and energy production.
Q2: How often should LOTO procedures be audited? Regular audits of LOTO procedures should be conducted at least annually, or whenever changes are made to equipment or processes.
Q3: Can’t employees simply rely on personal protective equipment (PPE)? While PPE is important, LOTO procedures complement PPE by directly preventing equipment activation, reducing the risk of accidents.
Q4: What are the legal consequences of LOTO non-compliance? LOTO non-compliance can lead to severe penalties, including fines and legal actions. It can also result in injuries and damage to equipment.
Q5: How can companies encourage employees to embrace LOTO procedures? Companies can encourage employee buy-in by providing comprehensive training, highlighting success stories, and fostering a culture of safety awareness.