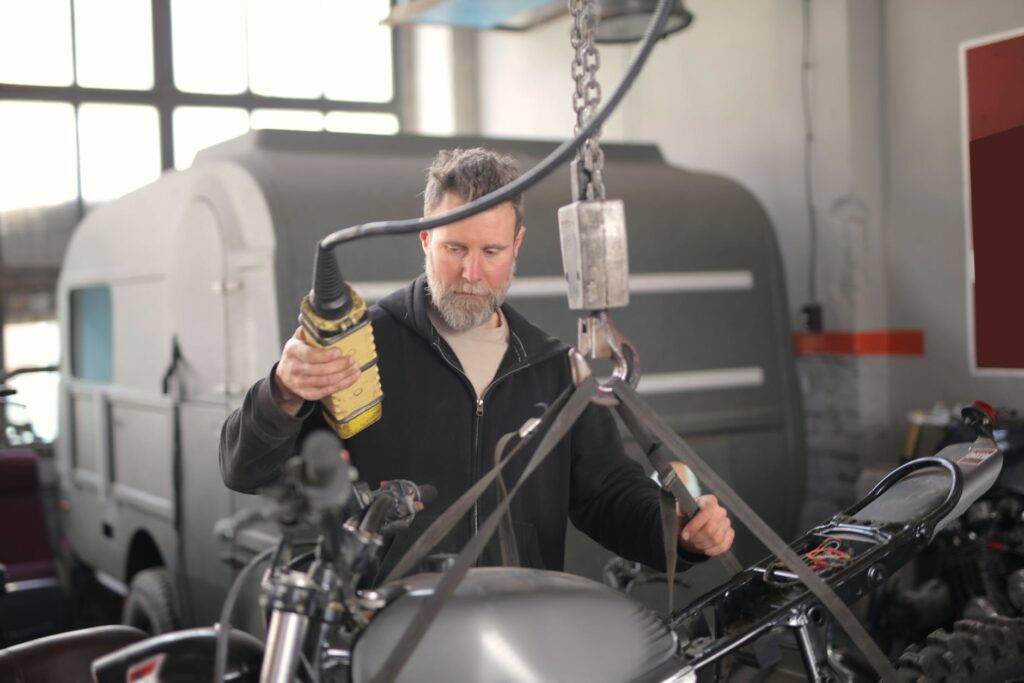
Lifting Tools and Tackles Rejection Criteria: Ensuring Safety and Reliability
In industries where heavy lifting is routine, the efficiency and safety of operations hinge upon the reliability of lifting tools and tackles. Understanding rejection criteria is paramount to maintain safety standards and operational efficiency.
Introduction to Lifting Tools and Tackles
In any industrial setting, the use of lifting tools and tackles is indispensable. These tools facilitate the movement of heavy loads and play a pivotal role in various sectors such as construction, manufacturing, and logistics.
Understanding Rejection Criteria
Rejection criteria encompass specific parameters that determine the usability and safety of lifting tools and tackles. These criteria revolve around various factors, including wear and tear, material defects, and compliance with safety standards.
Safety Standards and Compliance
Regulatory bodies and standards stipulate the guidelines for the design, manufacture, and usage of lifting equipment. Compliance ensures that the tools meet the necessary safety requirements.
Common Rejection Criteria
Identifying wear and tear indications, material defects, and corrosion are critical aspects of assessing rejection criteria. These factors often determine the usability and safety of lifting tools.
The rejection criteria for lifting tools and tackles generally involve several factors that might make them unsuitable or unsafe for use. Here are some common rejection criteria:
- Visible Damage: Any visible damage such as cracks, bends, distortions, or excessive wear can render a lifting tool or tackle unsafe for use and lead to rejection.
- Corrosion: Significant rust or corrosion weakens the structural integrity of the tool or tackle, making it unsafe for lifting heavy loads.
- Missing or Defective Components: Missing parts, like safety pins, shackles, or hooks, or any defective components, can compromise the safety of the lifting equipment.
- Improper Markings or Labels: If the equipment lacks proper markings, identification, or load capacity labels, it may not be safe for use.
- Incorrect or Expired Certification: Lifting tools and tackles should have valid and up-to-date certification indicating compliance with safety standards. Expired certifications or non-compliance may lead to rejection.
- Overload or Misuse: If the tool or tackle has been subjected to an overload beyond its rated capacity or has been misused, it should be rejected to prevent accidents.
- Inadequate Maintenance: Lack of proper maintenance, regular inspections, or repairs can compromise the safety of the equipment and lead to rejection.
- Incompatibility: Using the wrong type of tool or tackle for a specific lifting job, or using incompatible components, can pose serious risks and lead to rejection.
- Manufacturer’s Recommendations: Disregarding the manufacturer’s guidelines or recommendations for safe use and maintenance can be a cause for rejection.
Regular inspections and adherence to safety protocols are crucial to identifying and rejecting lifting tools and tackles that don't meet safety standards, preventing potential accidents and injuries.
Difference Between Hydra Crane and Farana Crane | Download PPT
Top 10 Safety Supervisor Interview Questions and Answers | Download PPT
Safe Operating Procedure for Construction | Download PPT
Risk Assessment for Construction Site | Download PPT
Inspection and Maintenance Protocols
Routine inspections and proper maintenance are crucial for ensuring the longevity and safety of lifting tools. Adhering to structured protocols minimizes the risk of unexpected failures.
Training and Awareness
Training programs create awareness about handling lifting equipment and understanding rejection criteria. Educating personnel mitigates risks associated with improper handling.
Consequences of Ignoring Rejection Criteria
Neglecting rejection criteria can lead to catastrophic failures, compromising both safety and operational efficiency. Identifying and addressing rejection criteria prevent potential hazards.
Conclusion
Adherence to rejection criteria is integral to ensuring the safety and reliability of lifting tools and tackles. Prioritizing safety measures and complying with rejection criteria safeguards against potential hazards.
FAQs
- What are rejection criteria in lifting tools? Rejection criteria refer to specific parameters or conditions that determine whether a lifting tool or tackle is deemed safe and usable. These criteria often include factors such as wear and tear, material defects, and compliance with safety standards. Meeting these criteria ensures the tool’s reliability and safety for use.
- How often should lifting equipment undergo inspection? The frequency of inspections for lifting equipment depends on various factors, including the type of equipment, its usage intensity, and regulatory requirements. Generally, routine inspections should be conducted at regular intervals, often specified by industry standards, manufacturer recommendations, or specific job site protocols.
- What are the consequences of ignoring rejection criteria? Neglecting rejection criteria can lead to severe consequences, including equipment failure, workplace accidents, injuries, and even fatalities. Ignoring these criteria compromises safety and operational efficiency, posing significant risks to both personnel and infrastructure.
- Are there industry-specific rejection criteria? Yes, different industries might have unique rejection criteria based on the nature of their operations, environmental conditions, and specific safety requirements. Industries such as construction, manufacturing, logistics, and oil and gas, among others, may have distinct criteria tailored to their needs.
- What role does technology play in assessing rejection criteria? Technology plays a pivotal role in assessing rejection criteria by enabling more precise inspections and evaluations of lifting tools and tackles. Innovations like advanced sensors, data analytics, and remote monitoring systems enhance the accuracy and efficiency of assessing rejection criteria, ensuring higher levels of safety and reliability.