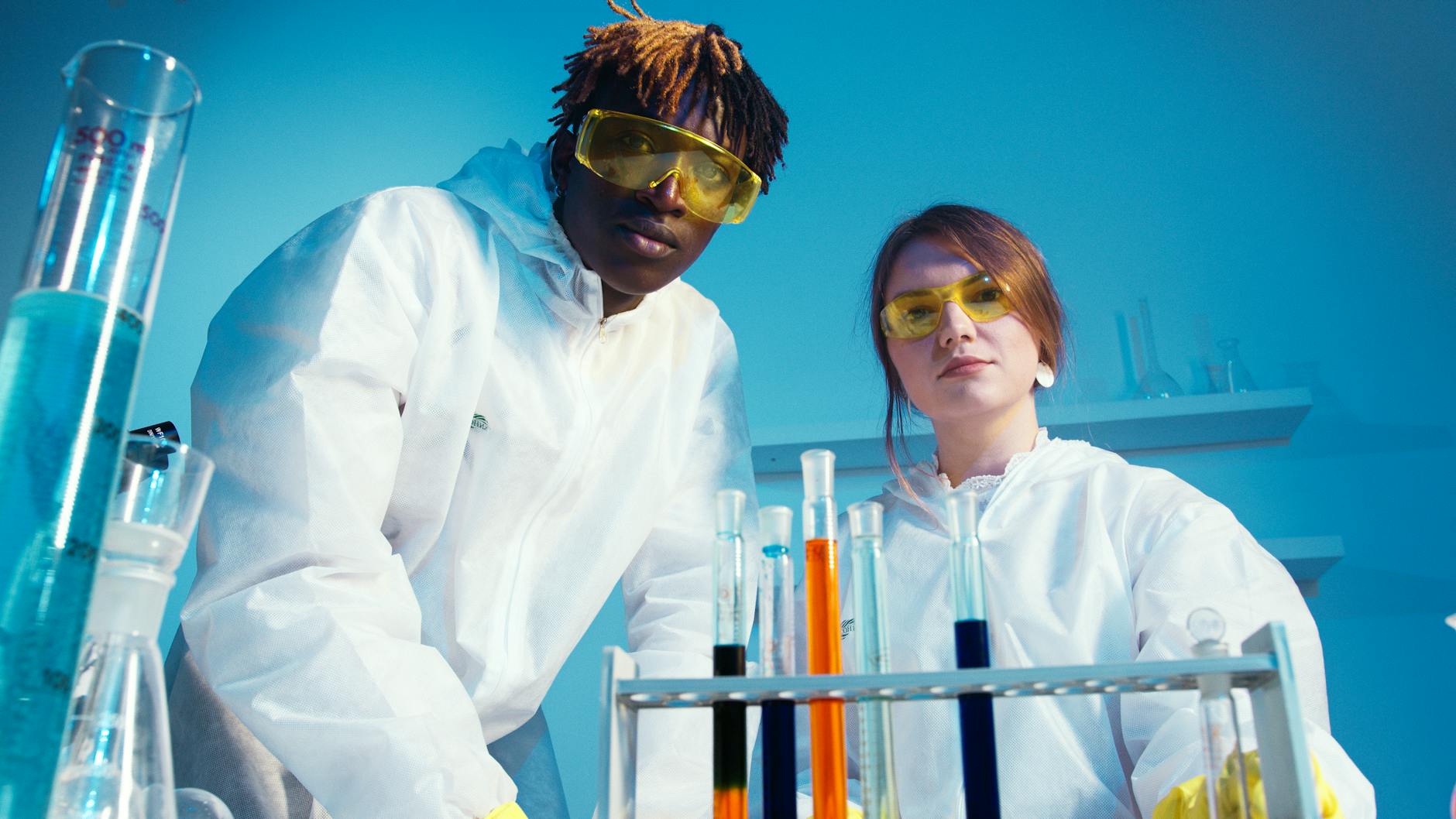
Laboratory Safety: Equipment Use and Chemical Handling
Introduction
Laboratories are essential spaces for scientific research and experimentation, but they also come with inherent risks. Ensuring the safety of personnel requires strict adherence to laboratory safety protocols, particularly in the use of equipment and handling of chemicals. This article explores key aspects of laboratory safety, emphasizing the proper use of equipment and best practices for chemical handling.
Proper Equipment Use in Laboratories
- Training and Familiarization
- Providing comprehensive training for laboratory personnel on the proper use of equipment
- Ensuring that individuals are familiar with the functionalities, limitations, and safety features of each piece of equipment they use
- Regular Equipment Inspections
- Implementing a schedule for regular inspections of laboratory equipment
- Checking for signs of wear, damage, or malfunction to address issues promptly and prevent accidents
- Calibration and Maintenance
- Conducting regular calibration and maintenance of laboratory instruments
- Ensuring the accuracy and reliability of equipment results and minimizing the risk of errors
- Emergency Shutdown Procedures
- Establishing clear emergency shutdown procedures for all equipment
- Training personnel on how to safely shut down equipment in case of malfunctions or emergencies to prevent further hazards
- Personal Protective Equipment (PPE) Use
- Mandating the use of appropriate PPE when operating specific equipment
- Ensuring that personnel wear protective gear such as gloves, goggles, or lab coats as required for different tasks
- Designated Equipment Areas
- Designating specific areas for certain equipment based on safety considerations
- Preventing the overcrowding of workspaces and facilitating organized and safe equipment use
- Prohibition of Unauthorized Modifications
- Strictly prohibiting unauthorized modifications or alterations to laboratory equipment
- Ensuring that only qualified personnel perform any adjustments or modifications to maintain equipment integrity
Best Practices for Chemical Handling in Laboratories
- Chemical Compatibility Checks
- Conducting thorough checks for chemical compatibility before combining or storing substances
- Preventing hazardous reactions by ensuring that chemicals are stored and used appropriately
- Labeling of Chemicals
- Implementing a comprehensive chemical labeling system
- Clearly labeling all containers with information on the contents, hazards, and necessary precautions for safe handling
- Proper Storage Procedures
- Adhering to proper storage procedures for chemicals
- Segregating incompatible substances, storing flammables in designated cabinets, and maintaining an organized inventory
- Ventilation Systems
- Ensuring adequate ventilation in the laboratory to minimize exposure to chemical fumes
- Using fume hoods and ventilation systems to control airborne contaminants during experiments
- Emergency Eyewash and Shower Stations
- Installing emergency eyewash and shower stations in accessible locations
- Providing immediate decontamination options in case of accidental chemical exposure to eyes or skin
- Spill Response Training
- Providing training on proper spill response procedures
- Equipping personnel with the knowledge and tools to manage chemical spills effectively and minimize their impact
- Waste Disposal Guidelines
- Establishing clear guidelines for the disposal of chemical waste
- Ensuring that personnel are aware of proper disposal methods and adhere to regulatory requirements
Conclusion
In conclusion, maintaining a safe laboratory environment involves meticulous attention to equipment use and chemical handling. By emphasizing training, regular inspections, and adherence to safety protocols, organizations can create a culture of safety in laboratories. Implementing best practices for equipment use and chemical handling not only protects personnel but also contributes to the integrity and success of scientific endeavors.
Mental Health in the Workplace: Addressing Psychological Safety as a Safety Officer
Safety Inspections: A Step-by-Step Guide for Safety Officers
Implementing and Evaluating Safety Training Programs for Employees
Occupational Health and Safety Trends: Staying Ahead as a Safety Officer
Emergency Response Planning: Best Practices for Safety Officers
Frequently Asked Questions (FAQs)
- Why is regular equipment inspection important in laboratory safety?
- Regular equipment inspection is important in laboratory safety to identify signs of wear, damage, or malfunction promptly. Addressing issues early helps prevent accidents and ensures the reliability of laboratory instruments.
- What are the key components of proper chemical handling in laboratories?
- Key components of proper chemical handling include chemical compatibility checks, comprehensive labeling, proper storage procedures, adequate ventilation, emergency eyewash and shower stations, spill response training, and clear guidelines for waste disposal.
- Why is it crucial to use personal protective equipment (PPE) when operating laboratory equipment?
- It is crucial to use PPE when operating laboratory equipment to protect personnel from potential hazards. This includes wearing gloves, goggles, or lab coats as required for different tasks to minimize the risk of injuries or exposure.
- How can laboratories ensure chemical compatibility during experiments?
- Laboratories can ensure chemical compatibility during experiments by conducting thorough checks before combining or storing substances. This helps prevent hazardous reactions and ensures the safe use of chemicals.
- What is the significance of emergency eyewash and shower stations in laboratories?
- Emergency eyewash and shower stations are significant in laboratories as they provide immediate decontamination options in case of accidental chemical exposure to eyes or skin, minimizing the potential impact on personnel.
- Why should unauthorized modifications to laboratory equipment be strictly prohibited?
- Unauthorized modifications to laboratory equipment should be strictly prohibited to maintain equipment integrity. Only qualified personnel should perform adjustments or modifications to ensure the safety and proper functioning of the equipment.