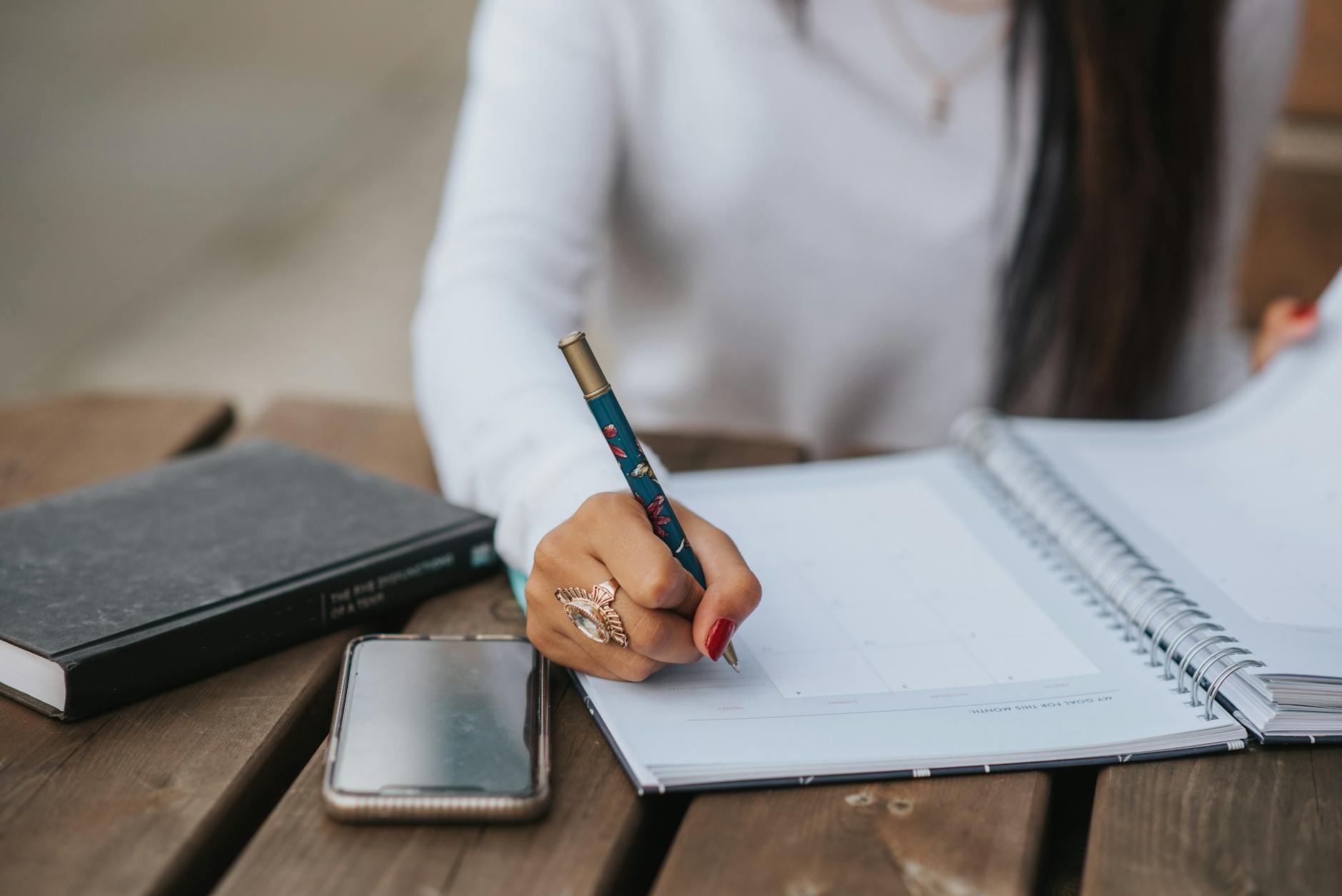
Kaizen Process
Introduction to Kaizen Process
Kaizen, a Japanese term meaning “change for the better” or “continuous improvement,” is a philosophy and methodology aimed at driving efficiency, quality, and innovation within organizations. Originating from post-World War II Japan, Kaizen has evolved into a widely adopted business strategy globally, spanning industries from manufacturing to healthcare and beyond.
Origin and History of Kaizen
Kaizen traces its roots to Japan, particularly to the manufacturing sector, where it emerged as a response to the country’s post-war economic challenges. The concept was popularized by pioneers like Toyota, who integrated it into their production processes to enhance productivity and quality.
Principles of Kaizen
Continuous Improvement
At the heart of Kaizen lies the principle of continuous improvement. It emphasizes incremental changes over time, focusing on small, manageable improvements rather than radical transformations.
Standardization
Another key principle of Kaizen is standardization, which involves establishing standardized processes and procedures to streamline operations and eliminate waste.
Employee Involvement
Kaizen places a strong emphasis on employee involvement and empowerment. It encourages frontline workers to actively participate in identifying improvement opportunities and implementing changes.
Benefits of Implementing Kaizen
Implementing Kaizen offers several benefits for organizations:
Increased Efficiency
By continuously identifying and eliminating inefficiencies, Kaizen helps organizations optimize their processes and workflows, leading to increased efficiency and productivity.
Cost Reduction
Kaizen’s focus on waste reduction and process improvement enables organizations to minimize costs associated with unnecessary delays, defects, and excess inventory.
Enhanced Quality
Through a relentless pursuit of improvement, Kaizen fosters a culture of quality excellence, resulting in products and services that consistently meet or exceed customer expectations.
Steps to Implement Kaizen
Implementing Kaizen involves several key steps:
- Identify Opportunities for Improvement: Analyze existing processes and workflows to identify areas where improvements can be made.
- Develop a Plan: Once improvement opportunities are identified, develop a detailed plan outlining the specific changes to be implemented and the expected outcomes.
- Implement Changes: Execute the planned improvements, ensuring that all stakeholders are engaged and aligned with the proposed changes.
- Monitor Progress: Continuously monitor the implemented changes to assess their impact and identify further areas for improvement.
Examples of Successful Kaizen Implementation
Numerous organizations have successfully implemented Kaizen to drive improvement across various aspects of their operations. For example, Toyota’s Toyota Production System (TPS) is a prime example of how Kaizen principles can revolutionize manufacturing processes, leading to significant improvements in efficiency, quality, and customer satisfaction.
Challenges in Implementing Kaizen
Despite its many benefits, implementing Kaizen can pose several challenges for organizations:
Resistance to Change
Introducing changes to established processes and workflows can be met with resistance from employees who may be comfortable with the status quo.
Lack of Leadership Support
Successful implementation of Kaizen requires strong leadership support and commitment. Without the necessary buy-in from top management, efforts to drive continuous improvement may falter.
Tips for Overcoming Challenges
To overcome challenges in implementing Kaizen, organizations can:
- Foster a culture of open communication and collaboration, encouraging employees to actively participate in the improvement process.
- Provide training and resources to equip employees with the skills and knowledge needed to drive change effectively.
- Lead by example, with senior leaders demonstrating their commitment to continuous improvement through their actions and decisions.
Kaizen in Different Industries
While Kaizen originated in the manufacturing sector, its principles and methodologies have been successfully applied across various industries, including healthcare, hospitality, and service-based industries.
Kaizen is a Japanese term that translates to "change for the better" or "continuous improvement." It refers to a philosophy or approach to improvement that emphasizes making small, incremental changes over time rather than large, sweeping changes all at once. The goal of kaizen is to continuously improve processes, products, or services in order to increase efficiency, quality, and overall effectiveness.
In a kaizen process, teams or individuals regularly identify areas for improvement, brainstorm solutions, implement changes on a small scale, and then evaluate the results. This iterative cycle allows organizations to steadily make progress towards their goals and adapt to changing circumstances.
Kaizen is often associated with lean manufacturing principles and is commonly used in industries such as manufacturing, healthcare, and software development. However, the principles of kaizen can be applied to any process or organization seeking to improve performance and achieve excellence.
Conclusion
The Kaizen process offers a powerful framework for driving continuous improvement and innovation within organizations. By embracing its principles and methodologies, organizations can unlock new levels of efficiency, quality, and employee engagement, positioning themselves for long-term success in today’s rapidly changing business landscape.
Mobile Equipment Safety: Prioritizing Operator Training and Maintenance Practices
Zero Harm Culture: Nurturing a Safety Mindset in the Workplace
Chemical Hygiene in Laboratories: Promoting Safe Handling and Storage Practices
Radiation Monitoring: Safeguarding Environments through Dosimetry and Contamination Control
FAQs
- Is Kaizen only applicable to manufacturing industries? No, Kaizen principles can be applied to various industries, including healthcare, hospitality, and service-based sectors, to drive continuous improvement and innovation.
- How long does it take to see results from implementing Kaizen? The timeline for seeing results from Kaizen implementation can vary depending on the scope of the improvements and the level of organizational commitment. However, organizations often start to see tangible benefits within a few months of initiating the process.
- What role do employees play in the Kaizen process? Employees play a central role in the Kaizen process by actively participating in identifying improvement opportunities, implementing changes, and sustaining continuous improvement efforts over time.
- What are some common pitfalls to avoid when implementing Kaizen? Common pitfalls to avoid when implementing Kaizen include a lack of leadership support, failure to engage employees effectively, and a reluctance to embrace change.
- How can organizations sustain the momentum of continuous improvement over time? To sustain the momentum of continuous improvement, organizations should cultivate a culture of learning and adaptation, regularly review and reassess their processes, and celebrate achievements and successes along the way.