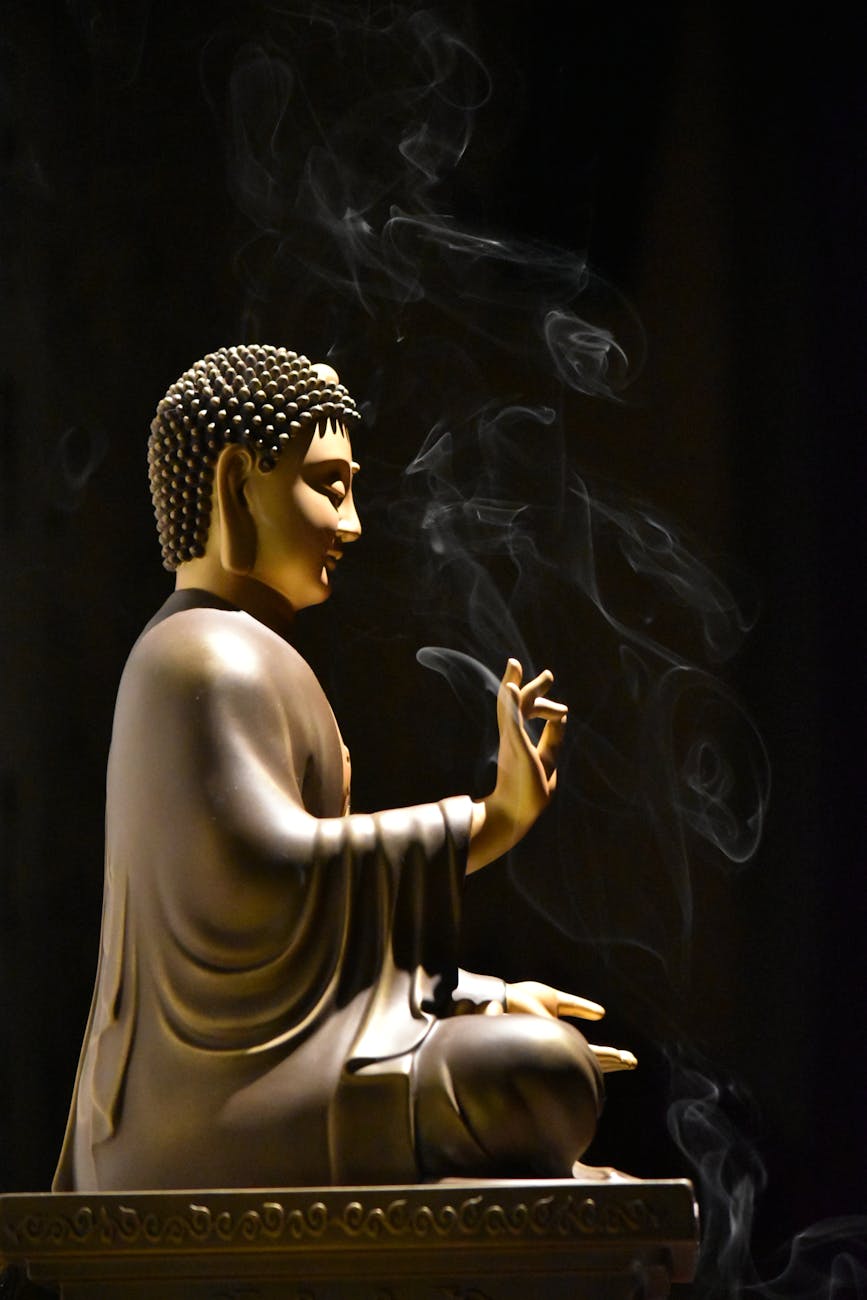
Kaizen Philosophy: A Path to Continuous Improvement
In today’s rapidly evolving business landscape, companies are constantly seeking ways to enhance efficiency, boost productivity, and stay competitive. One philosophy that has gained widespread recognition for achieving these goals is Kaizen. Rooted in Japanese management practices, Kaizen focuses on continuous improvement through incremental changes, involving every member of the organization, from top management to frontline workers.
Origin and Background of Kaizen
Kaizen, which translates to “change for better” in Japanese, traces its roots back to post-World War II Japan. It emerged as a response to the country’s efforts to rebuild its economy and enhance productivity. The concept was popularized by Japanese corporations like Toyota, which integrated it into their production systems to achieve remarkable results.
Meaning and Principles of Kaizen
At its core, Kaizen emphasizes the relentless pursuit of improvement in all aspects of an organization’s operations. It is based on several key principles, including:
- Continuous Improvement: Kaizen advocates making small, incremental changes on a daily basis rather than pursuing large-scale overhauls.
- Respect for People: It recognizes the importance of empowering employees and involving them in decision-making processes.
- Elimination of Waste: Kaizen aims to identify and eliminate inefficiencies and non-value-added activities in processes.
- Standardization: Establishing standard procedures and practices ensures consistency and reliability in operations.
Continuous Improvement in Kaizen
Central to Kaizen philosophy is the concept of continuous improvement. This involves:
Daily Improvements
Encouraging employees to seek out opportunities for improvement in their daily tasks and processes.
Small Incremental Changes
Focusing on making small, manageable changes over time, rather than waiting for major breakthroughs.
Implementation of Kaizen in Different Industries
Kaizen has proven to be adaptable and effective across various industries, including manufacturing, service, and healthcare. In the manufacturing sector, companies have used Kaizen principles to streamline production processes, reduce waste, and improve product quality. Similarly, service-oriented businesses have applied Kaizen to enhance customer satisfaction, optimize service delivery, and increase operational efficiency. In the healthcare sector, Kaizen has been instrumental in improving patient care, reducing medical errors, and enhancing overall healthcare delivery.
Benefits of Kaizen Philosophy
The adoption of Kaizen philosophy offers numerous benefits to organizations, including:
- Increased Efficiency: By continuously identifying and eliminating inefficiencies, organizations can streamline processes and improve productivity.
- Employee Engagement: Involving employees in the improvement process fosters a sense of ownership and commitment, leading to higher levels of engagement and morale.
- Quality Improvement: Kaizen’s focus on standardization and waste reduction results in improved product and service quality, leading to greater customer satisfaction.
Challenges and Obstacles in Implementing Kaizen
While Kaizen offers significant benefits, its implementation is not without challenges. Common obstacles include resistance to change, lack of management support, and insufficient resources or expertise. Overcoming these challenges requires strong leadership, effective communication, and a willingness to invest in training and development.
Successful Examples of Kaizen Implementation
Numerous organizations have successfully implemented Kaizen principles to achieve impressive results. One notable example is Toyota, which revolutionized the automotive industry with its Toyota Production System, built on the foundations of Kaizen. By continuously improving processes and empowering employees, Toyota has become synonymous with efficiency, quality, and innovation.
Steps to Implement Kaizen in an Organization
Implementing Kaizen requires a systematic approach and a commitment to continuous improvement. Key steps include:
- Creating a Kaizen Culture: Foster an environment that encourages innovation, experimentation, and continuous learning.
- Training and Education: Provide employees with the necessary skills and knowledge to identify and implement improvements.
- Empowering Employees: Give employees the autonomy and authority to make decisions and implement changes within their areas of expertise.
Tools and Techniques Used in Kaizen
Several tools and techniques are commonly used in Kaizen initiatives to facilitate improvement efforts, including:
- Gemba Walks: Leaders and employees observe processes firsthand to identify opportunities for improvement.
- 5S Methodology: Sort, Set in order, Shine, Standardize, and Sustain – a systematic approach to workplace organization and cleanliness.
- Poka-Yoke (Error Proofing): Implementing mechanisms to prevent errors or defects before they occur, minimizing the need for rework or corrections.
Kaizen vs. Other Improvement Philosophies
While Kaizen shares similarities with other improvement philosophies like Lean Manufacturing and Six Sigma, it has distinct characteristics that set it apart. Unlike Lean, which focuses on eliminating waste, or Six Sigma, which aims to reduce variation, Kaizen emphasizes continuous, incremental improvement and employee involvement in decision-making processes.
Conclusion
In conclusion, Kaizen philosophy offers a proven framework for achieving continuous improvement and driving organizational success. By focusing on small, incremental changes, empowering employees, and fostering a culture of innovation, organizations can unlock new levels of efficiency, quality, and competitiveness.
Mobile Equipment Safety: Prioritizing Operator Training and Maintenance Practices
Zero Harm Culture: Nurturing a Safety Mindset in the Workplace
FAQs about Kaizen Philosophy
- What does Kaizen mean? Kaizen is a Japanese term that translates to “change for better” and refers to the philosophy of continuous improvement in all aspects of an organization’s operations.
- How is Kaizen different from Lean Manufacturing? While both Kaizen and Lean Manufacturing aim to improve efficiency and eliminate waste, Kaizen focuses on continuous, incremental improvement, whereas Lean often involves larger-scale process redesign.
- What are some common challenges in implementing Kaizen? Challenges in implementing Kaizen may include resistance to change, lack of management support, and insufficient resources or expertise.
- Can Kaizen be applied outside of the manufacturing industry? Yes, Kaizen principles are applicable to various industries, including service, healthcare, and education, where they can help improve processes, enhance quality, and increase efficiency.
- How can organizations foster a culture of Kaizen? Organizations can foster a culture of Kaizen by promoting employee involvement and empowerment, providing training and education, and recognizing and rewarding continuous improvement efforts.