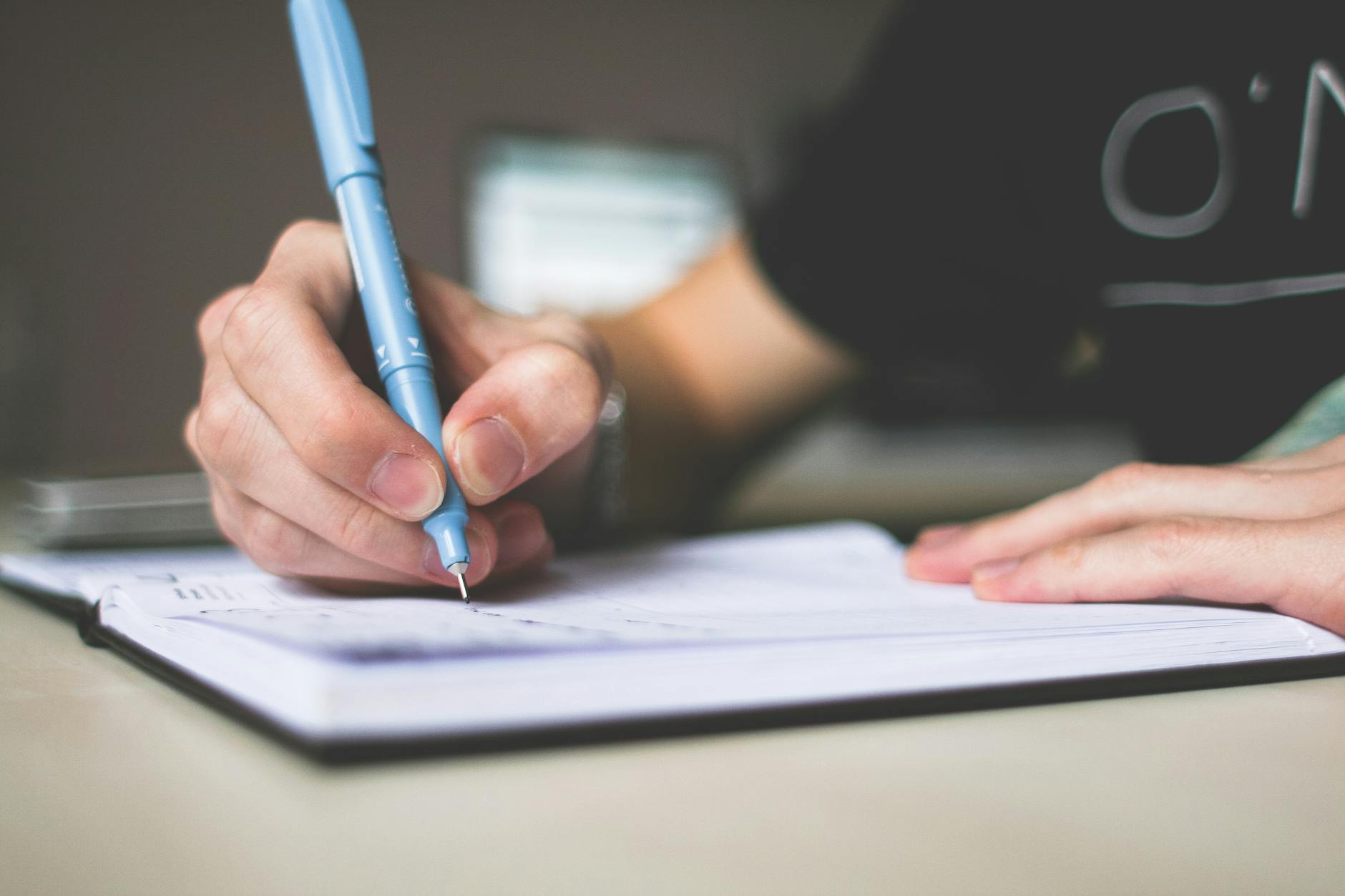
Kaizen Examples
Introduction to Kaizen
Kaizen, originating from Japan, is a concept deeply ingrained in the philosophy of continuous improvement. It emphasizes making small, incremental changes to processes, products, or services to achieve better results over time. The term “Kaizen” itself translates to “change for better” or “continuous improvement.”
Principles of Kaizen
At the heart of Kaizen lie several key principles:
- Continuous improvement: Encouraging ongoing efforts to enhance processes and systems.
- Standardization: Establishing standardized procedures to streamline operations.
- Employee involvement: Involving employees at all levels in the improvement process.
- Incremental changes: Focusing on small, manageable improvements rather than drastic overhauls.
Kaizen Examples in Manufacturing
In the manufacturing sector, Kaizen has been instrumental in revolutionizing production processes. Examples include:
- Toyota Production System: Toyota pioneered the application of Kaizen in manufacturing, leading to significant improvements in efficiency and quality.
- Gemba Kaizen: This approach focuses on making improvements at the workplace (Gemba) by involving frontline workers in identifying and solving problems.
- 5S methodology: Sort, Set in Order, Shine, Standardize, and Sustain—this methodology helps organize the workplace for maximum efficiency and productivity.
Kaizen Examples in Healthcare
In healthcare, Kaizen principles have been applied to enhance patient care and operational efficiency. Examples include:
- Reducing patient wait times: Hospitals have used Kaizen to streamline processes, leading to reduced wait times for patients.
- Improving hospital workflows: Kaizen methodologies have helped optimize workflows, ensuring smoother operations and better patient outcomes.
- Implementing lean management: Lean principles, closely aligned with Kaizen, have been adopted in healthcare settings to eliminate waste and improve resource utilization.
Kaizen Examples in Software Development
Software development teams have embraced Kaizen to foster continuous improvement and agility. Examples include:
- Agile methodologies: Agile frameworks such as Scrum and Kanban emphasize iterative development and continuous feedback, aligning closely with Kaizen principles.
- Scrum framework: Scrum promotes regular inspection and adaptation, enabling teams to continuously improve their processes and deliver better products.
- Continuous integration and deployment: By automating build, test, and deployment processes, software teams can achieve faster feedback cycles and drive continuous improvement.
Kaizen Examples in Education
In the education sector, Kaizen principles have been applied to enhance teaching methodologies and learning outcomes. Examples include:
- Implementing student feedback systems: Educators use feedback from students to identify areas for improvement and make incremental changes to their teaching methods.
- Improving teaching methodologies: Kaizen encourages educators to experiment with new teaching techniques and continuously refine their approaches based on student feedback.
- Enhancing learning environments: Schools and universities apply Kaizen principles to create supportive learning environments that foster student engagement and success.
Kaizen Examples in Personal Development
On a personal level, Kaizen can be applied to self-improvement and skill development. Examples include:
- Habit formation: Adopting Kaizen principles can help individuals establish and reinforce positive habits over time, leading to personal growth and development.
- Time management techniques: By making small adjustments to their daily routines, individuals can gradually improve their time management skills and productivity.
- Skill enhancement strategies: Kaizen encourages lifelong learning and skill development, prompting individuals to continuously seek opportunities for growth and improvement.
Benefits of Kaizen
The benefits of implementing Kaizen are manifold, including:
- Increased efficiency: By eliminating waste and optimizing processes, organizations can achieve higher levels of efficiency and productivity.
- Higher quality products or services: Continuous improvement leads to better quality products or services, enhancing customer satisfaction and loyalty.
- Better employee morale and satisfaction: Involving employees in the improvement process fosters a culture of engagement and empowerment, leading to higher levels of job satisfaction and motivation.
Challenges of Implementing Kaizen
Despite its many benefits, implementing Kaizen can pose several challenges, including:
- Resistance to change: Some employees may resist Kaizen initiatives due to fear of the unknown or reluctance to leave their comfort zones.
- Lack of resources: Limited resources, such as time, budget, or expertise, can hinder Kaizen implementation efforts.
- Cultural barriers: Cultural differences and organizational inertia may impede the adoption of Kaizen principles in certain contexts.
How to Implement Kaizen Successfully
To overcome these challenges and ensure successful Kaizen implementation, organizations can take several key steps, including:
- Leadership support: Strong leadership commitment is essential for driving Kaizen initiatives and fostering a culture of continuous improvement.
- Employee training and involvement: Providing employees with the necessary training and resources empowers them to actively participate in the improvement process.
- Continuous monitoring and evaluation: Regularly monitoring and evaluating the results of Kaizen initiatives allows organizations to identify areas for further improvement and adjust their strategies accordingly.
Kaizen vs. Other Improvement Methodologies
While Kaizen shares similarities with other improvement methodologies such as Six Sigma and Lean management, there are distinct differences:
- Contrasting Kaizen with Six Sigma: While both focus on process improvement, Six Sigma places greater emphasis on statistical analysis and achieving defect reduction targets.
- Differentiating Kaizen from Lean management: While Kaizen is a key component of Lean management, Lean encompasses a broader set of principles aimed at eliminating waste and maximizing value for customers.
Real-life Kaizen Success Stories
Numerous organizations across various industries have achieved remarkable success through Kaizen initiatives. Some notable examples include:
- Toyota: The Toyota Production System, rooted in Kaizen principles, has enabled the company to become a global leader in automotive manufacturing.
- General Electric: GE implemented Kaizen methodologies to improve efficiency and quality in its production processes, resulting in significant cost savings and customer satisfaction.
- Amazon: Amazon continuously applies Kaizen principles to its operations, driving innovation and efficiency across its vast network of warehouses and fulfillment centers.
Conclusion
In conclusion, Kaizen stands as a powerful philosophy and methodology for driving continuous improvement and innovation in organizations of all sizes and industries. By embracing Kaizen principles and practices, businesses can achieve higher levels of efficiency, quality, and employee engagement, ultimately leading to greater success and competitiveness in the marketplace.
Mobile Equipment Safety: Prioritizing Operator Training and Maintenance Practices
Zero Harm Culture: Nurturing a Safety Mindset in the Workplace
Chemical Hygiene in Laboratories: Promoting Safe Handling and Storage Practices
Radiation Monitoring: Safeguarding Environments through Dosimetry and Contamination Control
FAQs
- What are some quick Kaizen examples for small businesses? Quick Kaizen examples for small businesses include implementing visual management systems, conducting regular Gemba walks, and organizing Kaizen events to address specific challenges.
- How long does it typically take to see results from Kaizen implementation? The timeline for seeing results from Kaizen implementation can vary depending on the nature of the improvements and the organization’s readiness for change. In many cases, organizations may start to see tangible results within a few weeks or months of implementing Kaizen initiatives.
- Can Kaizen be applied to non-profit organizations? Yes, Kaizen principles can be applied to non-profit organizations to improve their operations, enhance service delivery, and maximize the impact of their programs and initiatives.
- Are there any industries where Kaizen is not suitable? Kaizen principles can be applied to virtually any industry or sector, as the concept of continuous improvement is universally applicable. However, industries with highly regulated environments or rigid operating procedures may face greater challenges in implementing Kaizen.
- What role does employee feedback play in Kaizen? Employee feedback plays a crucial role in Kaizen, as it provides valuable insights into areas for improvement and helps identify opportunities for innovation. By involving employees in the improvement process and soliciting their feedback, organizations can foster a culture of continuous improvement and empowerment.