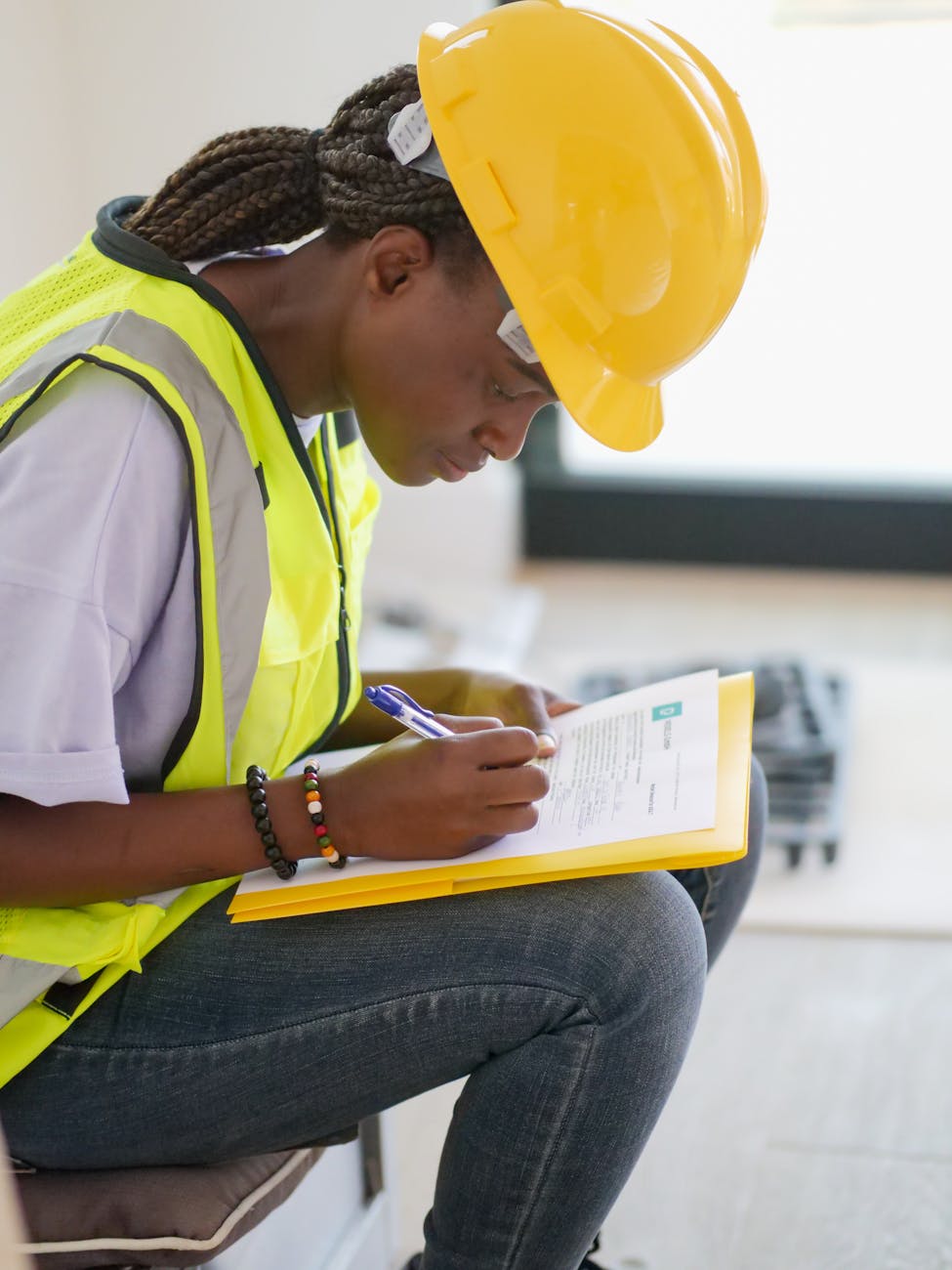
JSA Vs HIRA
Introduction
Workplace safety is a top priority across all industries. Companies must identify potential hazards and implement preventive measures to protect workers. Two widely used safety tools in risk assessment are Job Safety Analysis (JSA) and Hazard Identification and Risk Assessment (HIRA). While both serve the purpose of hazard identification, they differ in methodology, application, and scope.
In this article, we’ll break down JSA and HIRA, compare their differences, and help you understand when and how to use them for effective workplace safety.
What is JSA (Job Safety Analysis)?
JSA, or Job Safety Analysis, is a systematic approach to identifying potential hazards in a specific job task. It helps in understanding the risks associated with individual tasks and provides preventive measures to minimize accidents.
Purpose and Importance of JSA
JSA is primarily used to analyze step-by-step job tasks to pinpoint hazards before work begins. It helps in:
- Identifying unsafe job steps
- Preventing accidents and injuries
- Training workers on potential risks
- Ensuring compliance with safety regulations
Steps Involved in Job Safety Analysis (JSA)
- Identifying Job Tasks – Breaking down a job into smaller, manageable tasks.
- Recognizing Hazards – Identifying hazards associated with each task.
- Assessing Risks – Determining the level of risk for each identified hazard.
- Implementing Control Measures – Taking preventive steps to reduce or eliminate risks.
What is HIRA (Hazard Identification and Risk Assessment)?
HIRA, or Hazard Identification and Risk Assessment, is a broader safety assessment tool used to evaluate risks across an entire workplace, not just specific job tasks.
Purpose and Importance of HIRA
HIRA plays a critical role in developing workplace safety plans by:
- Identifying all potential hazards in a work environment
- Assessing the probability and severity of risks
- Implementing preventive and control measures
- Ensuring long-term safety compliance
Steps Involved in HIRA
- Identifying Hazards – Recognizing potential dangers in the workplace (chemical, mechanical, biological, etc.).
- Evaluating Risk Levels – Assessing the likelihood and severity of hazards.
- Implementing Preventive Measures – Taking steps to eliminate or reduce risk exposure.
Key Differences Between JSA and HIRA
Feature | JSA (Job Safety Analysis) | HIRA (Hazard Identification & Risk Assessment) |
---|---|---|
Scope | Specific job task | Entire workplace or system |
Focus | Step-by-step job analysis | Overall workplace hazards |
Application | Construction, manufacturing, oil & gas | Industries with multiple hazard types |
Risk Level | Task-specific hazards | Organizational risk assessment |
Outcome | Safe job procedures | Comprehensive risk control plan |
When to Use JSA vs HIRA?
- Use JSA when analyzing individual job tasks to ensure step-by-step safety.
- Use HIRA when assessing workplace hazards on a broader scale.
- Use both together when combining task-specific risk assessments with an overall safety strategy.
Benefits of JSA and HIRA in Workplace Safety
Both JSA and HIRA help in:
✅ Reducing workplace accidents and injuries
✅ Improving compliance with safety laws
✅ Enhancing worker awareness of hazards
✅ Strengthening safety culture within an organization
Challenges in Implementing JSA and HIRA
- Lack of worker participation – Employees may not engage in the process fully.
- Time-consuming process – Thorough risk assessments require significant time and effort.
- Inconsistent implementation – Companies may struggle to maintain regular assessments.
How to Overcome These Challenges?
- Provide safety training to all workers.
- Set a clear schedule for safety assessments.
- Encourage management to support and enforce safety measures.
Here are sample examples of Job Safety Analysis (JSA) and Hazard Identification and Risk Assessment (HIRA) for better understanding:
Example of Job Safety Analysis (JSA)
Job Task: Operating an Angle Grinder in a Workshop
Step | Potential Hazard | Risk Level (Low/Medium/High) | Control Measures |
---|---|---|---|
1. Inspecting the grinder before use | Faulty or damaged equipment | Medium | Perform a pre-use inspection, ensure all parts are secure |
2. Wearing personal protective equipment (PPE) | Lack of PPE can lead to injuries | High | Wear safety glasses, gloves, ear protection, and a dust mask |
3. Starting the grinder | Flying debris or sparks | High | Stand to the side, ensure workspace is clear, hold the tool firmly |
4. Grinding the material | Grinder kickback, hand injury, fire risk | High | Use both hands, maintain correct posture, avoid flammable materials |
5. Turning off and storing the grinder | Grinder overheating, improper storage | Medium | Allow cooling before storage, place in designated safe area |
✅ Outcome: The operator follows the correct procedures, reducing the risk of injury.
Example of Hazard Identification and Risk Assessment (HIRA)
Work Area: Construction Site
Hazard Type | Potential Hazard | Likelihood (Low/Medium/High) | Severity (Low/Medium/High) | Risk Level | Control Measures |
---|---|---|---|---|---|
Physical Hazards | Falling from heights while working on scaffolding | High | High | High | Use fall protection gear (harness, guardrails), train workers, conduct safety checks |
Chemical Hazards | Exposure to toxic fumes from welding | Medium | High | High | Use ventilation systems, provide respiratory protection, limit exposure time |
Electrical Hazards | Contact with live wires during electrical work | Medium | High | High | De-energize circuits, wear insulated gloves, use proper tools |
Mechanical Hazards | Getting caught in machinery | Medium | High | High | Use machine guards, train workers, ensure emergency stop buttons are functional |
Ergonomic Hazards | Repetitive lifting of heavy objects causing back strain | High | Medium | High | Train workers in proper lifting techniques, use mechanical aids (hoists, forklifts) |
✅ Outcome: The overall workplace is assessed for multiple hazards, and risk control measures are put in place to ensure worker safety.
Key Takeaways:
- JSA is used for specific job tasks, identifying step-by-step hazards and controls.
- HIRA evaluates overall workplace hazards, assessing their likelihood and severity.
- Both methods together help create a safer work environment.
Conclusion
JSA and HIRA are essential risk assessment tools that contribute to a safer work environment. While JSA focuses on analyzing specific job tasks, HIRA evaluates risks on a broader scale. By effectively implementing both, companies can create a strong safety culture and prevent workplace accidents.
Who Should Perform a Risk Assessment?
What is a Risk Assessment at Work?
FAQs
1. What is the main difference between JSA and HIRA?
JSA focuses on job-specific hazards, while HIRA assesses risks across an entire workplace.
2. Is JSA better than HIRA?
Neither is better; they serve different purposes. JSA is task-focused, while HIRA is workplace-focused.
3. How often should JSA and HIRA be conducted?
JSA should be conducted before performing hazardous tasks. HIRA should be updated regularly or after changes in the work environment.
4. Who is responsible for conducting JSA and HIRA?
Safety officers, supervisors, and management teams are responsible, along with worker participation.
5. Can JSA and HIRA be used together?
Yes, they complement each other to provide a complete workplace safety assessment.