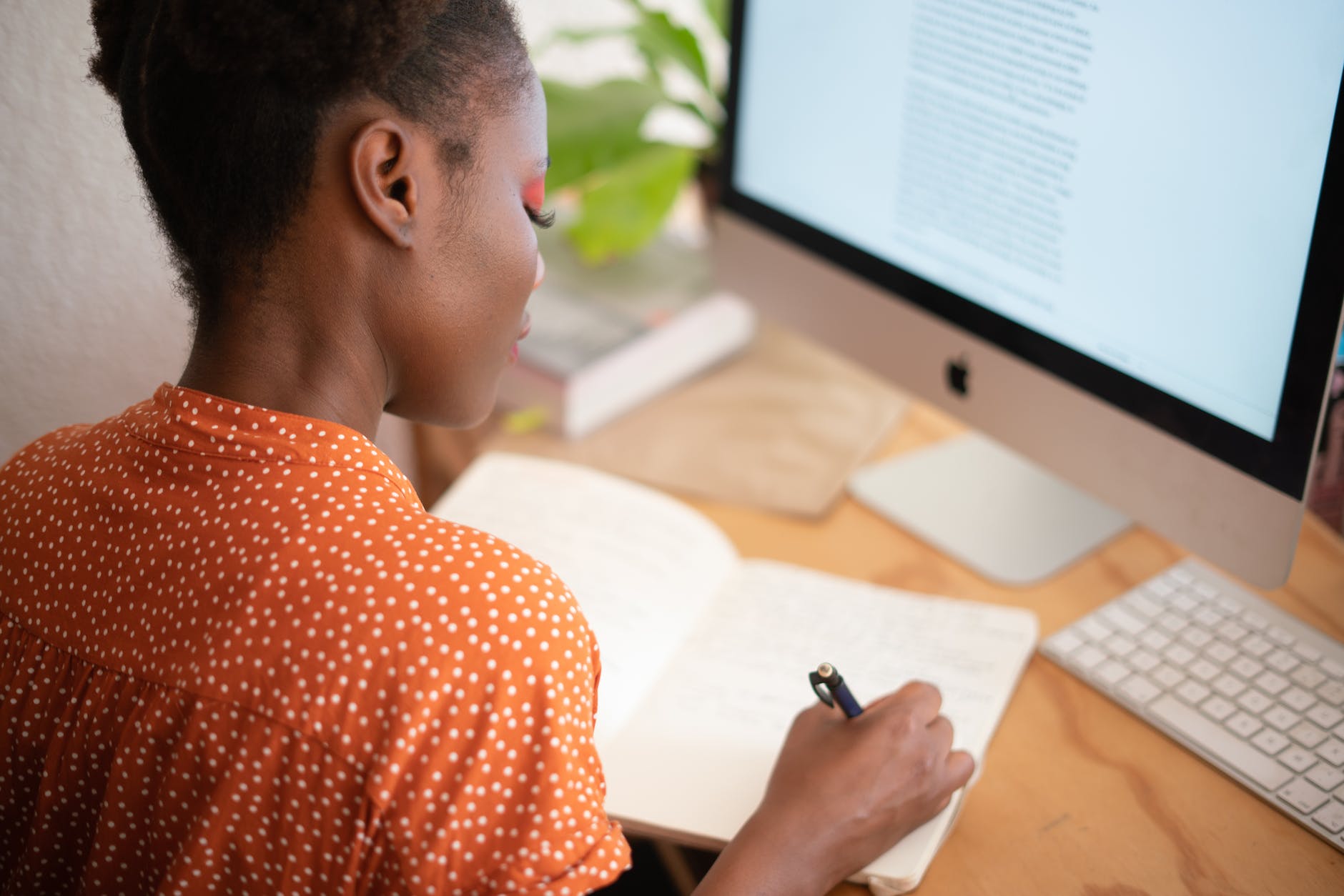
Job Safety Analysis (JSA) | Steps | Benefits | How To Prepare | Download PPT
In today’s dynamic work environment, prioritizing the safety of employees is paramount. Job Safety Analysis (JSA) stands as a cornerstone in achieving this goal, providing a systematic approach to identifying potential hazards, mitigating risks, and ensuring a secure workplace.
I. Introduction
A. Definition of Job Safety Analysis (JSA)
Job Safety Analysis, commonly known as JSA or Job Hazard Analysis (JHA), is a process used to identify potential hazards associated with specific job tasks. It involves breaking down each task into manageable steps, analyzing the associated risks, and implementing preventive measures.
B. Importance of JSA in Workplace Safety
Ensuring a safe working environment is not only a legal requirement but also a moral obligation for employers. JSA plays a crucial role in enhancing workplace safety by proactively addressing potential dangers, reducing the likelihood of accidents, and fostering a culture of vigilance among employees.
II. Steps of Job Safety Analysis
A. Identification of Job Tasks
The first step in conducting a JSA is to identify the various tasks involved in a particular job. This comprehensive task list serves as the foundation for the analysis.
B. Breaking Down Job Tasks into Steps
Once the tasks are identified, they are further broken down into individual steps. This step-by-step breakdown allows for a detailed examination of each element within a task.
C. Identification of Potential Hazards
For each step, potential hazards are identified. These hazards can range from physical risks to environmental factors, helping to pinpoint areas that require attention.
D. Implementation of Safety Measures
After identifying hazards, the next crucial step is implementing safety measures. This can involve the use of protective equipment, changes in work processes, or the introduction of safety protocols.
E. Review and Revision of JSA
JSA is not a one-time process. Regular reviews and revisions are essential to adapt to changes in job tasks, equipment, or work environments.
III. Benefits of Job Safety Analysis
A. Reduction of Workplace Accidents
One of the primary benefits of JSA is a significant reduction in workplace accidents. By proactively addressing potential hazards, the likelihood of incidents occurring is minimized.
B. Enhanced Employee Awareness
JSA fosters a culture of awareness among employees. When workers are actively involved in the analysis process, they become more vigilant about their surroundings and potential risks.
C. Compliance with Safety Regulations
Adhering to safety regulations is a legal requirement for businesses. JSA ensures that an organization is in compliance with these regulations, avoiding legal complications.
D. Improved Communication in the Workplace
The process of JSA encourages open communication between employees and employers. It creates a platform for discussing safety concerns, suggestions, and feedback.
IV. How To Prepare Job Safety Analysis
A. Involvement of Employees
Employees are on the frontline of job tasks, making their involvement crucial in the JSA process. Their firsthand knowledge can contribute valuable insights into potential hazards.
B. Utilization of Safety Guidelines
Utilizing established safety guidelines and standards provides a structured approach to JSA. These guidelines act as a reference point for identifying common hazards.
C. Regular Training Sessions
Conducting regular training sessions on JSA ensures that employees are well-versed in the process. This training enhances their ability to identify and address potential hazards.
D. Documentation and Record-Keeping
Thorough documentation of JSA processes and outcomes is essential. It serves as a record of safety measures implemented and provides insights for future improvements.
V. Sample Example with Scenario
A. Overview of a Job Task
Let’s consider a construction site where welding is a common task.
B. Breakdown of Task into Steps
- Preparation of Welding Equipment
- Gathering necessary tools and materials.
- Setting Up Work Area
- Ensuring a well-ventilated space with proper safety barriers.
- Welding Process
- Executing the welding task with precision.
- Post-Welding Cleanup
- Safely handling hot equipment and disposing of waste.
C. Identification of Potential Hazards
- Electrical Hazards
- Ensuring proper grounding of welding equipment.
- Fumes and Ventilation
- Implementing measures to minimize exposure to welding fumes.
- Fire Hazards
- Keeping flammable materials away from the welding area.
D. Application of Safety Measures
- Personal Protective Equipment (PPE)
- Ensuring welders wear appropriate PPE, including helmets and gloves.
- Ventilation Systems
- Installing proper ventilation to minimize fume inhalation.
- Fire Extinguishers
- Having accessible fire extinguishers in the vicinity.
VI. Importance of Regular JSA Reviews
A. Adaptation to Changes in the Work Environment
As workplaces evolve, regular JSA reviews are vital to address new hazards associated with changes in equipment, processes, or workspaces.
B. Continuous Improvement in Safety Protocols
JSA reviews provide an opportunity for continuous improvement. Feedback from employees and real-time data help enhance safety protocols.
VII. Challenges in Implementing JSA
A. Employee Resistance
Some employees may resist the JSA process, perceiving it as an additional burden. Overcoming this resistance requires effective communication and highlighting the benefits.
B. Time and Resource Constraints
Limited time and resources can hinder the implementation of JSA. Proper planning and resource allocation are essential to overcome these challenges.
VIII. Overcoming Challenges in JSA Implementation
A. Employee Training Programs
Educating employees about the importance of JSA through training programs can alleviate resistance and foster a sense of ownership.
B. Allocation of Sufficient Resources
Ensuring that adequate time and resources are allocated to the JSA process is crucial. This investment pays off in the form of a safer work environment.
IX. Common Misconceptions About JSA
A. Myth-Busting Facts
Addressing common misconceptions about JSA, such as it being time-consuming or applicable only to certain industries, helps promote a more accurate understanding.
X. Conclusion
A. Recap of JSA Importance
Job Safety Analysis is not merely a regulatory requirement; it is a proactive approach to safeguarding the well-being of employees. By systematically analyzing job tasks, identifying hazards, and implementing preventive measures, organizations create a safer and more productive work environment.
B. Call to Action for Workplace Safety
The responsibility for workplace safety lies with every individual in an organization. Embracing and implementing JSA is a collective effort that contributes to a culture of safety and well-being.
Top 10 Fresher Safety Officer MCQs with Answer and Explanation | Download PPT
Is NEBOSH recognized in Canada and the USA? | Download PPT
Top 10 Safety Officer Interview Questions and Answers | Download PPT
12 Elements of Safety Management System (SMS) | Download PPT
6 Pillars of Process Safety | Download PPT
XI. FAQs
A. What is the primary goal of Job Safety Analysis?
The primary goal of Job Safety Analysis is to proactively identify and address potential hazards associated with specific job tasks, ultimately reducing the risk of workplace accidents.
B. How often should JSA be reviewed and updated?
JSA should be regularly reviewed and updated, especially when there are changes in job tasks, equipment, or work environments. This ensures the continued effectiveness of safety measures.
C. Can JSA be applied to all types of jobs?
Yes, JSA can be applied to a wide range of jobs across various industries. Its adaptability makes it a versatile tool for ensuring workplace safety.
D. Are there legal requirements for conducting JSA?
While specific legal requirements may vary, many jurisdictions mandate the implementation of safety measures, and JSA is a widely accepted practice to meet these requirements.
E. How can employees contribute to the JSA process?
Employee involvement is crucial in the JSA process. Their firsthand knowledge of job tasks and potential hazards provides valuable insights. Encouraging open communication and participation fosters a safer work environment.
Very good material