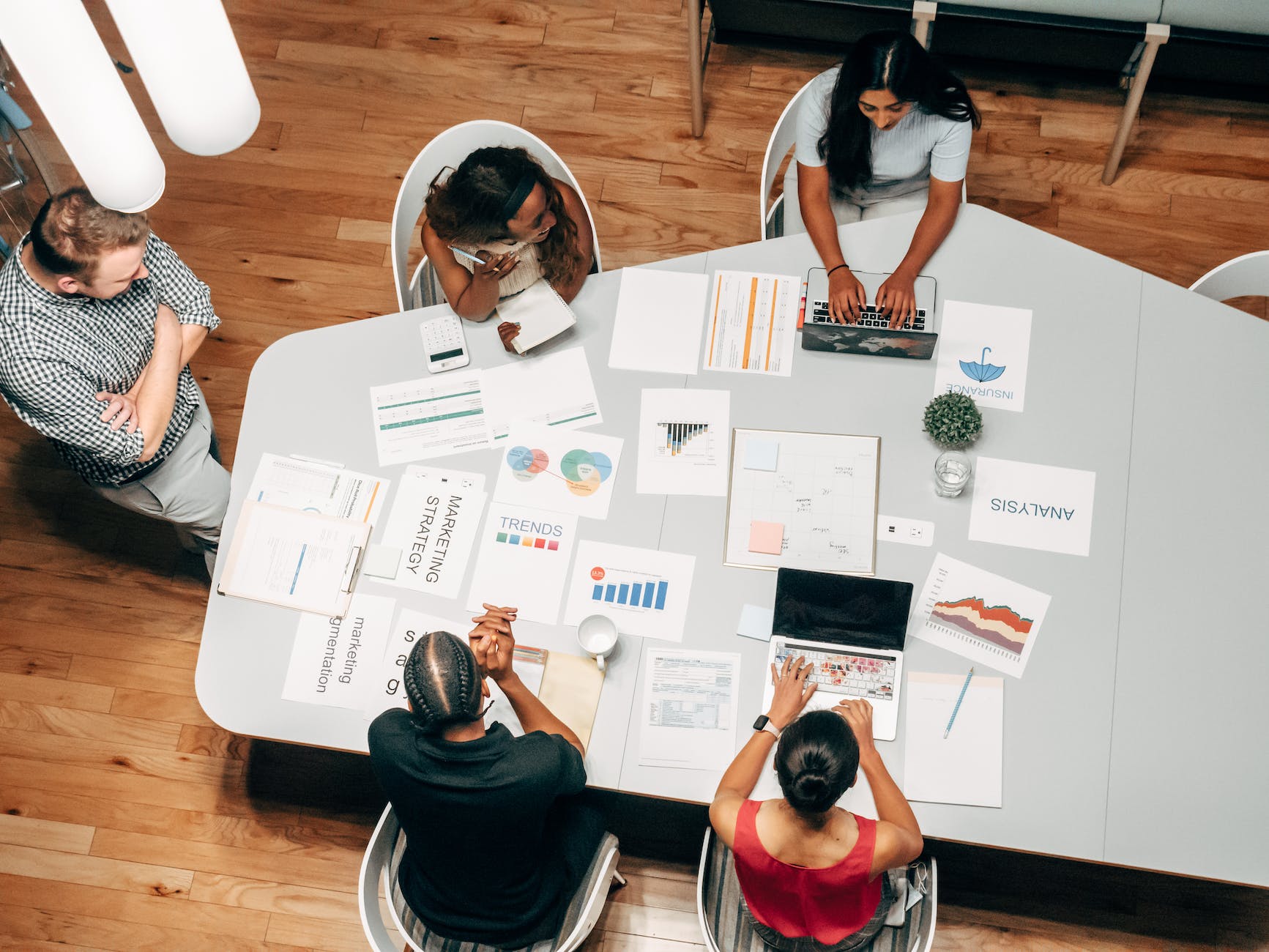
Job Hazard Analysis Steps
Introduction to Job Hazard Analysis
In the realm of occupational safety, Job Hazard Analysis (JHA) stands as a crucial process to identify potential risks in a workplace.
Importance of Job Hazard Analysis
Understanding the significance of conducting JHA enlightens employers and employees alike about the pivotal role it plays in ensuring workplace safety.
OSHA Standards and Job Hazard Analysis
Compliance with Occupational Safety and Health Administration (OSHA) standards underscores the necessity of incorporating JHA within organizational frameworks.
Steps in Conducting Job Hazard Analysis
Step 1: Selection of Job
Initiating the JHA process involves choosing a specific job or task for analysis.
Step 2: Breaking Down the Job
A detailed breakdown of the selected job into smaller, manageable steps becomes the foundation for thorough analysis.
Step 3: Identifying Potential Hazards
Identification of potential hazards associated with each step elucidates the risks involved.
Step 4: Determine Preventive Measures
Formulating preventive measures or controls mitigates identified hazards, emphasizing proactive risk management.
Step 5: Documenting Findings
Recording observations and hazard mitigations in a structured manner establishes a tangible record for future reference.
Step 6: Implementing Changes
Implementing the devised preventive measures seamlessly integrates safety protocols into daily work routines.
Step 7: Review and Update
Regular review and updates to the JHA ensure its relevance and effectiveness in adapting to dynamic work environments.
Here's an example related to scaffolding in the context of Job Hazard Analysis:
Scenario: Scaffolding Erection
Step 1: Selection of Job The selected job for analysis is the erection of scaffolding at a construction site.
Step 2: Breaking Down the Job Break the scaffolding erection process into steps:
- Gathering materials
- Checking ground stability
- Assembling base frames
- Erecting vertical members
- Placing horizontal braces
- Securing planks for work platforms
Step 3: Identifying Potential Hazards
- Falls: Workers may fall during assembly or disassembly.
- Structural Stability: Unstable ground or incorrect assembly could lead to collapse.
- Material Handling: Lifting heavy components can cause strains or injuries.
- Tool Safety: Misuse of tools while assembling scaffolding.
Step 4: Determine Preventive Measures
- Fall Protection: Use harnesses, guardrails, or safety nets.
- Inspection: Ensure the ground’s stability before setup.
- Training: Properly train workers on assembly procedures.
- Tools and Equipment: Use appropriate tools and ensure they’re in good condition.
Step 5: Documenting Findings Record observations, identified hazards, and measures taken to mitigate risks in a JHA document.
Step 6: Implementing Changes Implement safety measures outlined in the JHA, ensuring all workers are aware and follow protocols.
Step 7: Review and Update Regularly review the scaffolding erection process, update safety protocols, and provide additional training if needed.
This example highlights the systematic analysis of erecting scaffolding, identifying potential hazards, and implementing preventive measures to ensure the safety of workers on-site.
Benefits of Implementing Job Hazard Analysis
The integration of JHA yields numerous benefits, including heightened safety awareness, reduced incidents, and enhanced productivity.
Common Challenges in Implementing JHA
Despite its advantages, challenges such as resistance to change and insufficient training can hinder the effective implementation of JHA.
Conclusion
Job Hazard Analysis remains an indispensable tool in fostering a safe and secure work environment. Its systematic approach in identifying and mitigating risks not only prioritizes safety but also contributes significantly to organizational efficiency.
Job Safety Analysis Definition
FAQs
- What industries benefit most from Job Hazard Analysis? Industries with high-risk tasks or environments, such as construction, manufacturing, healthcare, and oil & gas, benefit significantly from Job Hazard Analysis. However, JHA can be applied across various sectors to enhance workplace safety.
- How often should a Job Hazard Analysis be updated? Job Hazard Analysis should be regularly reviewed and updated to ensure its relevance. Ideally, it should be revisited whenever there are changes in work processes, equipment, or if new hazards emerge. Ongoing evaluation ensures that safety measures stay current and effective.
- Can employees actively participate in the JHA process? Yes, involving employees in the Job Hazard Analysis process is beneficial. Their firsthand experience and insights into daily tasks can provide valuable input to identify hazards accurately. Engaging employees fosters a safety culture and encourages ownership of safety measures.
- What is the role of management in implementing JHA effectively? Management plays a crucial role in effectively implementing Job Hazard Analysis. Their support, commitment, and provision of resources for training and hazard mitigation are essential. Additionally, they set the tone for safety culture within the organization.
- Are there software tools available to streamline the JHA process? Yes, there are various software tools designed specifically for Job Hazard Analysis. These tools assist in organizing, documenting, and tracking hazard identification, making the JHA process more efficient. They often provide templates, checklists, and reporting features to streamline the analysis.