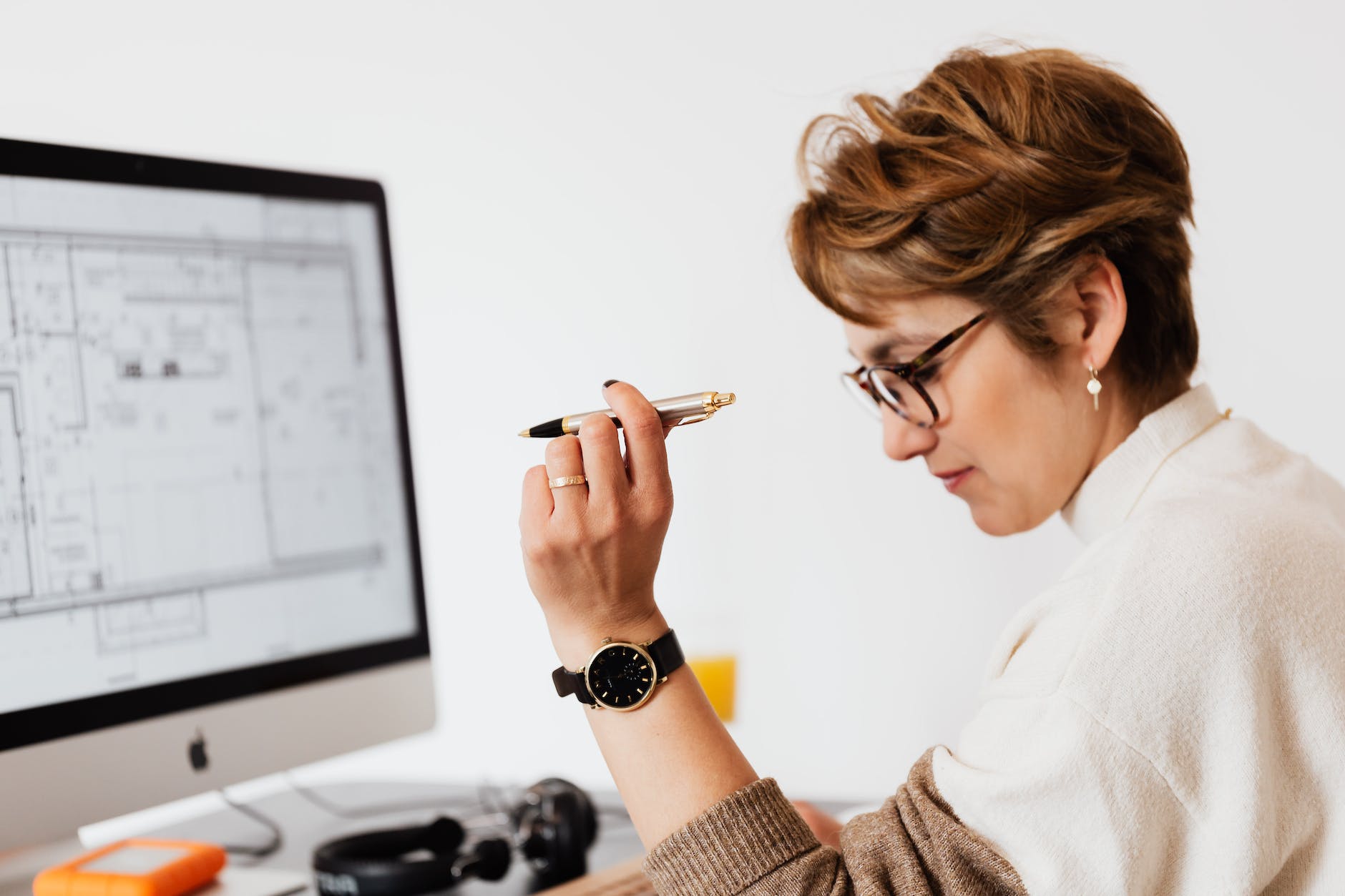
Job Hazard Analysis: Enhancing Workplace Safety
Safety in the workplace is paramount, and ensuring it requires meticulous planning and assessment. One crucial tool that significantly contributes to workplace safety is Job Hazard Analysis (JHA). Let’s delve into what JHA entails and why it’s indispensable.
Introduction to Job Hazard Analysis
Importance of Workplace Safety
Workplace safety isn’t just a legal requirement; it’s a moral responsibility. Employees deserve a safe environment, free from hazards that can cause harm or accidents.
What is Job Hazard Analysis?
Job Hazard Analysis, or JHA, is a systematic approach used to identify potential hazards associated with a specific job or task. Its primary goal is to prevent accidents and injuries by proactively addressing risks.
Steps to Conduct a Job Hazard Analysis
Step 1: Selecting the Job or Task
The first step in JHA involves choosing the job or task that requires analysis. It’s essential to focus on tasks with the potential for accidents or injuries.
Step 2: Identifying Potential Hazards
Thoroughly examine the selected job to identify potential hazards. These hazards could range from equipment malfunctions to unsafe working conditions.
Step 3: Determining Preventive Measures
Once hazards are identified, the next step is devising preventive measures to eliminate or mitigate these risks effectively.
Benefits of Implementing Job Hazard Analysis
Increased Safety Awareness
JHA fosters a culture of safety awareness among employees. It encourages them to actively identify and address potential hazards in their work environment.
Reduced Workplace Accidents and Injuries
By proactively identifying and mitigating risks, JHA significantly reduces the likelihood of workplace accidents and injuries.
Challenges in Conducting Job Hazard Analysis
Lack of Employee Participation
One of the primary challenges in JHA implementation is the reluctance or lack of participation from employees, hindering the effectiveness of the analysis.
Time and Resource Constraints
Conducting a thorough JHA requires time and resources, which can sometimes be limited in certain work environments.
Best Practices for Effective Job Hazard Analysis
Involving Employees in the Process
Incorporating employees into the JHA process increases their commitment to safety protocols and ensures a comprehensive analysis.
Regular Reviews and Updates
Continuously reviewing and updating the JHA ensures that new hazards are identified and addressed promptly.
Industries and Sectors that Benefit from Job Hazard Analysis
Construction
The construction industry significantly benefits from JHA due to its inherently hazardous nature involving heavy machinery and high-risk tasks.
Healthcare
In healthcare settings, JHA is vital in mitigating risks associated with patient care, handling equipment, and exposure to infectious materials.
Legal Compliance and Job Hazard Analysis
Occupational Safety and Health Administration (OSHA) Guidelines
JHA aligns with OSHA guidelines, making it a crucial tool for legal compliance in maintaining workplace safety standards.
Importance of Compliance
Adhering to regulatory standards not only ensures legal compliance but also protects employees and employers from potential liabilities.
A job hazard analysis (JHA) is a process that involves examining a job or task to identify potential hazards that could cause harm to workers. It aims to systematically break down a job into its basic steps, look at the potential hazards associated with each step, and determine preventive measures to mitigate these risks.
The steps involved in conducting a job hazard analysis typically include:
- Selecting the Job or Task: Choose the specific job or task to be analyzed. This could be anything from operating machinery to performing maintenance tasks.
- Breaking Down the Job: Identify and list all the individual steps involved in completing the job. This includes both major and minor tasks.
- Identifying Potential Hazards: For each step, analyze and identify potential hazards or sources of harm. These hazards could be physical, chemical, biological, ergonomic, or related to the work environment.
- Determining Control Measures: Once hazards are identified, determine the appropriate control measures to eliminate or minimize the risks. This could involve engineering controls, administrative controls, or personal protective equipment (PPE).
- Implementing Controls: Put the control measures into action. Ensure that workers are trained on these measures and that they are readily available and used properly.
- Reviewing and Updating: Periodically review the analysis to ensure its effectiveness and update it whenever there are changes in the job or workplace conditions.
By conducting a thorough job hazard analysis, employers can create a safer work environment, reduce the likelihood of workplace injuries or accidents, and ensure compliance with safety regulations.
Conclusion
Job Hazard Analysis is not merely a protocol; it’s a proactive approach to safeguarding the well-being of every individual in a work environment. By identifying and mitigating risks, JHA is an indispensable tool in ensuring workplace safety.
Job Safety Analysis Definition
5 Importance of Risk Management
FAQs
- Is Job Hazard Analysis mandatory for all industries? Job Hazard Analysis isn’t universally mandatory, but it’s highly recommended across all industries to enhance safety.
- How often should a Job Hazard Analysis be updated? Regular updates are crucial; typically, it’s recommended to review and update JHA annually or when work conditions change significantly.
- Who should be involved in conducting a Job Hazard Analysis? Ideally, employees directly involved in the task, supervisors, safety officers, and relevant stakeholders should partake in the JHA process.
- Can Job Hazard Analysis prevent all workplace accidents? While JHA significantly reduces risks, it can’t entirely eliminate the possibility of accidents. It’s a preventive measure to minimize such occurrences.
- Is Job Hazard Analysis a one-time process? No, JHA is an ongoing process. Regular reviews and updates ensure it remains effective and relevant to the changing work environment.
Hi hope you are doing well.
With great honor and respect it is stated that I have more then 4 years of experience in the safety sector, I have done all the safety certification with site experience and expertise.
I wish to work under your supervision in your company. I will try my best to full fill your desire and will give you my best.
Best regards Asif