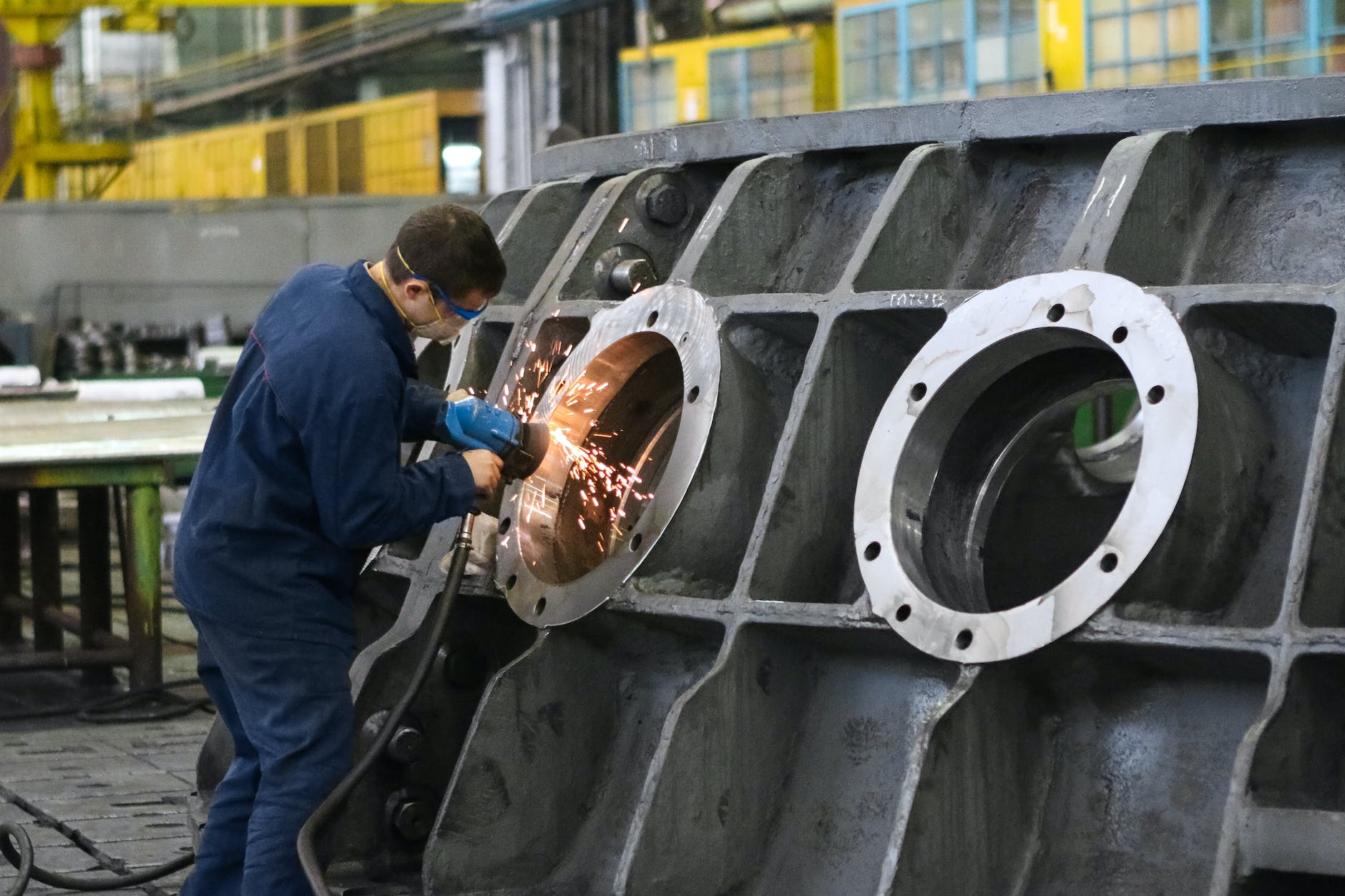
Industrial Safety Information: Ensuring a Secure Workplace
Industrial Safety Information : In today’s fast-paced industrial landscape, safety should always be a top priority. Ensuring the well-being of employees and protecting valuable assets is not just a legal requirement but also a moral obligation. In this article, we will delve into the critical aspects of industrial safety information, offering insights and guidelines to create a secure workplace environment.
Introduction
Industrial safety is not merely a checkbox to mark off; it’s a crucial component of responsible business operations. Ensuring the safety of your workforce and the integrity of your equipment can prevent accidents, save lives, and safeguard your company’s reputation.
Understanding Industrial Safety
Before diving deeper, let’s define what industrial safety is. It encompasses a set of procedures, guidelines, and practices designed to minimize the risk of accidents, injuries, and property damage within industrial settings.
The Importance of Industrial Safety
Safety isn’t just about avoiding accidents; it’s about fostering a culture of well-being. Prioritizing industrial safety leads to increased employee morale, reduced downtime, and enhanced productivity. Moreover, it keeps your organization in compliance with legal requirements.
Legal Regulations and Compliance
Various laws and regulations exist to govern industrial safety. These include OSHA in the United States, which sets standards and conducts inspections to ensure workplaces adhere to safety protocols. Non-compliance can result in hefty fines and legal consequences.
Identifying Hazards
An essential step in ensuring industrial safety is identifying potential hazards within the workplace. These can range from faulty machinery to chemical exposure. A thorough hazard assessment is critical.
Risk Assessment
Once hazards are identified, conducting risk assessments helps prioritize them based on severity and likelihood. This process informs safety measures and resource allocation.
Safety Training Programs
Investing in comprehensive safety training programs is a wise choice. Employees must be well-versed in safety protocols and aware of the risks associated with their tasks.
Personal Protective Equipment (PPE)
PPE, such as helmets, gloves, and goggles, plays a vital role in mitigating risks. Ensure that employees have access to and use the appropriate PPE for their jobs.
Emergency Response Plans
Preparedness is key. Every organization should have well-documented emergency response plans in place to address various scenarios, from fires to chemical spills.
Safety Inspections and Audits
Regular inspections and audits are essential to identify and rectify safety deficiencies. This proactive approach prevents accidents before they occur.
Reporting Incidents and Near-Misses
Encourage a culture of reporting incidents and near-misses without fear of reprisal. Learning from mistakes and close calls is a powerful tool for improving safety.
Continuous Improvement
Industrial safety is an ongoing process. Continuously assess and refine safety protocols to adapt to changing circumstances and new risks.
Safety Culture
A strong safety culture involves all employees actively participating in safety initiatives. When safety becomes everyone’s responsibility, accidents decrease.
Conclusion
Industrial safety isn’t just a necessity; it’s a competitive advantage and a moral duty. Prioritizing safety through compliance, risk assessment, training, and a strong safety culture benefits employees, organizations, and the community at large.
How to Promote a Safe Workplace
Occupational Health and Safety (OHS) Guidelines
FAQs
1. How can I improve safety in my industrial workplace? Start by conducting a thorough risk assessment, implementing robust training programs, and fostering a safety-conscious culture.
2. What are the legal consequences of neglecting industrial safety regulations? Neglecting safety regulations can lead to hefty fines, legal actions, and damage to your organization’s reputation.
3. How can I encourage employees to report incidents and near-misses? Create an environment where reporting is encouraged and rewarded, and ensure that employees understand the importance of learning from incidents.
4. Are there industry-specific safety guidelines to follow? Yes, many industries have their own specific safety regulations and guidelines. It’s essential to research and adhere to these standards.
5. What role does management play in fostering a safety culture? Management sets the tone for safety within an organization. Their commitment to safety and active participation in safety initiatives are crucial for creating a culture of safety.