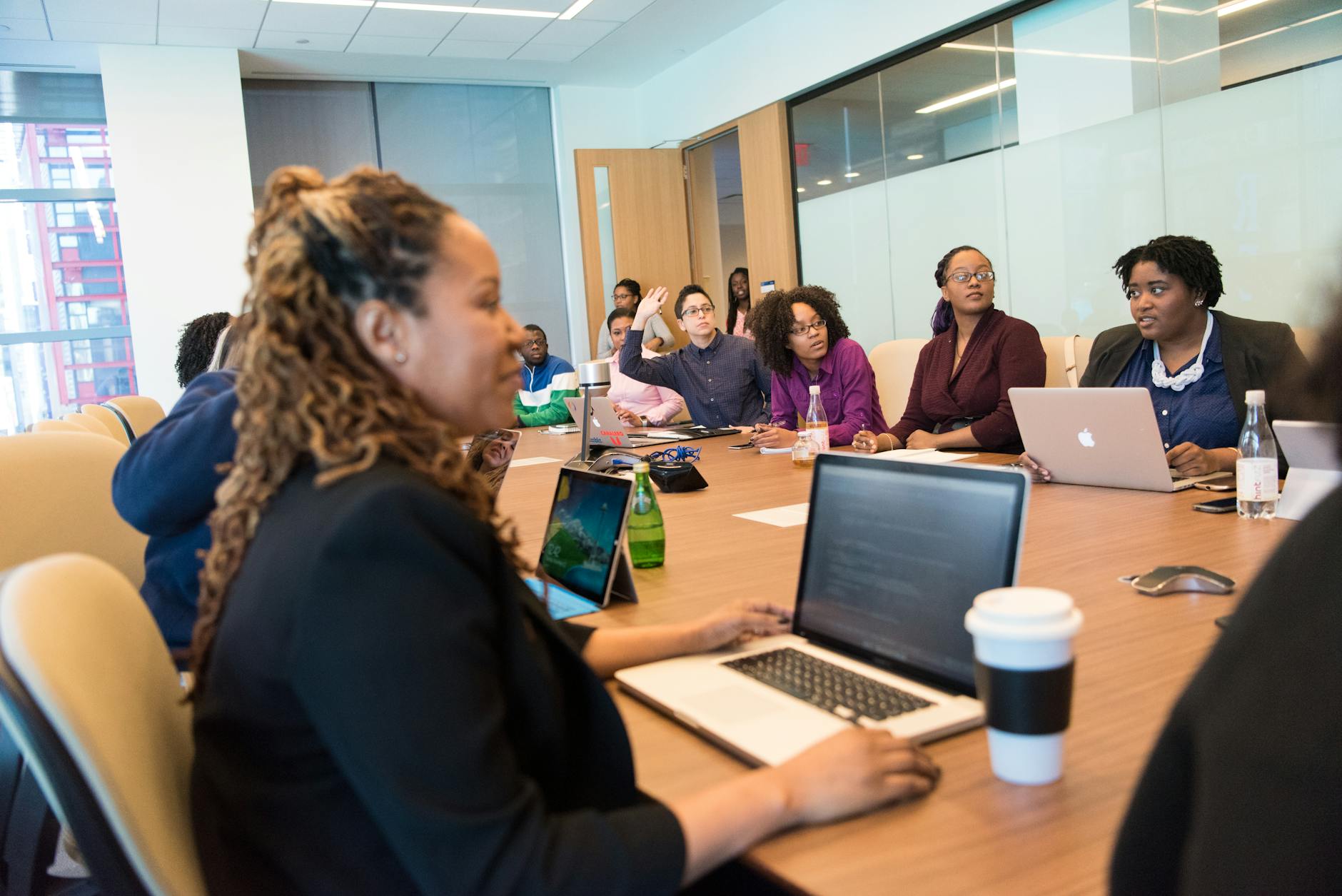
HSE Training Requirements in OSHA Standards
Health, Safety, and Environmental (HSE) training is a critical aspect of workplace safety and regulatory compliance. In the United States, the Occupational Safety and Health Administration (OSHA) sets standards and guidelines to ensure the safety and well-being of workers across various industries. Understanding and adhering to OSHA’s HSE training requirements are essential for employers and employees alike to create a safe and healthy work environment.
Introduction to HSE Training Requirements
Importance of Health, Safety, and Environmental (HSE) Training
HSE training plays a vital role in preventing workplace accidents, injuries, and illnesses. By providing employees with the necessary knowledge and skills, organizations can mitigate risks and create a culture of safety. Proper training not only protects employees but also enhances productivity and reduces operational costs.
Overview of OSHA Standards
OSHA establishes and enforces standards to ensure safe and healthful working conditions for workers in the United States. These standards cover a wide range of industries and hazards, including construction, manufacturing, healthcare, and more. Compliance with OSHA regulations is mandatory for employers, and failure to meet the standards can result in penalties and fines.
General HSE Training Requirements
Basic Elements of HSE Training
HSE training programs typically include instruction on hazard recognition, risk assessment, and safe work practices. Employers must ensure that employees receive training relevant to their job duties and workplace hazards. Topics may include fire safety, chemical handling, ergonomics, and emergency procedures.
Understanding OSHA Guidelines
Employers are responsible for familiarizing themselves with OSHA regulations applicable to their industry and ensuring compliance with specific training requirements. OSHA provides resources, guidelines, and training materials to help employers meet their obligations and create a safe work environment.
Specific HSE Training Requirements
Hazard Communication Training
OSHA’s Hazard Communication Standard (HCS) requires employers to provide employees with information and training on hazardous chemicals present in the workplace. This includes understanding safety data sheets (SDS), chemical labeling, and proper handling procedures.
Emergency Response Training
Employees must be trained to respond effectively to workplace emergencies, such as fires, chemical spills, and medical incidents. Training should cover evacuation procedures, emergency contacts, and the proper use of emergency equipment.
Personal Protective Equipment (PPE) Training
OSHA mandates that employers assess workplace hazards and provide appropriate personal protective equipment (PPE) to employees. Training on the selection, use, and maintenance of PPE is essential to ensure its effectiveness in protecting workers from injury or exposure.
Workplace Violence Prevention Training
In occupations where the risk of workplace violence is present, employers must provide training to help employees recognize warning signs, defuse potentially violent situations, and respond appropriately to incidents.
Bloodborne Pathogens Training
Employees at risk of occupational exposure to blood or other potentially infectious materials must receive training on the prevention of bloodborne pathogens, including hepatitis B, hepatitis C, and HIV.
Electrical Safety Training
Workers who may be exposed to electrical hazards must receive training on safe work practices, lockout/tagout procedures, and the identification of electrical hazards in the workplace.
Confined Space Entry Training
Employees involved in confined space work must be trained to recognize hazards, use appropriate entry procedures, and respond to emergencies safely.
Respiratory Protection Training
Workers required to wear respiratory protection devices must undergo training on their proper use, maintenance, and limitations to ensure effective protection against airborne contaminants.
Implementation of HSE Training Programs
Developing a Comprehensive Training Plan
Employers should develop a comprehensive HSE training plan that addresses the specific needs and risks of their workplace. This plan should outline training objectives, content, methods, and frequency of training sessions.
Integrating Training into Daily Operations
HSE training should be integrated into daily operations to ensure that employees understand and apply safety principles in their work. Incorporating safety reminders, toolbox talks, and job-specific training modules can reinforce learning and promote a safety-conscious culture.
Evaluating Training Effectiveness
Employers should regularly evaluate the effectiveness of their HSE training programs through feedback, assessments, and performance metrics. Adjustments may be necessary to address gaps in knowledge or changes in workplace conditions.
Compliance and Enforcement
OSHA Inspections and Audits
OSHA conducts inspections and audits to ensure compliance with regulatory standards and identify workplace hazards. Employers should be prepared to demonstrate compliance with HSE training requirements and address any deficiencies promptly.
Consequences of Non-compliance
Failure to comply with OSHA standards, including HSE training requirements, can result in citations, fines, and penalties. Non-compliance may also lead to legal liabilities, reputational damage, and increased insurance costs for employers.
Best Practices for HSE Training
Engaging Employees in Training
Employers should actively involve employees in HSE training by soliciting feedback, encouraging participation, and recognizing achievements. Engaged employees are more likely to retain information and apply safety practices in their daily work.
Continuous Improvement of Training Programs
HSE training programs should evolve to address emerging hazards, regulatory changes, and organizational needs. Regular review and updating of training materials ensure that employees receive the most relevant and up-to-date information.
OSHA, the Occupational Safety and Health Administration, sets out various training requirements to ensure workplace safety and compliance with regulations. Here are some general guidelines for training requirements in OSHA standards:
- Hazard Communication (HazCom): This standard requires employers to provide comprehensive training to employees who work with hazardous chemicals. Training should cover chemical hazards, safety data sheets (SDS), labeling requirements, and appropriate protective measures.
- Lockout/Tagout (LOTO): Employees involved in servicing or maintenance of machines or equipment where unexpected energization or start-up could occur must receive training in lockout/tagout procedures. This training ensures they understand how to safely isolate energy sources and prevent accidental startup.
- Respiratory Protection: Workers who are required to wear respirators must undergo training on proper respirator use, maintenance, and fit testing. This training ensures they understand the limitations of their respirators and how to use them effectively.
- Confined Spaces: Employers must provide confined space entry training to workers who may enter confined spaces. This includes understanding hazards associated with confined spaces, proper entry procedures, and emergency response protocols.
- Fall Protection: Employees who may be exposed to fall hazards must receive training on fall protection systems and equipment. This includes instruction on how to properly use personal fall arrest systems, guardrails, and other protective measures.
- Electrical Safety: Workers exposed to electrical hazards must be trained in electrical safety practices, including lockout/tagout procedures, proper use of personal protective equipment (PPE), and recognizing electrical hazards.
- Machine Guarding: Training on machine guarding is necessary for employees who work with or around machinery. This training covers the importance of machine guarding, recognizing hazards, and safe operating procedures.
- Bloodborne Pathogens: Employees who may be exposed to blood or other potentially infectious materials must receive training on bloodborne pathogens. This includes understanding the risks associated with exposure, methods of transmission, and proper use of PPE.
- Emergency Action Plans (EAP): Employers must develop and implement emergency action plans, and employees must be trained on these plans. This includes evacuation procedures, emergency communication, and roles and responsibilities during emergencies.
These are just a few examples of training requirements outlined in various OSHA standards. Employers are responsible for identifying applicable standards to their workplace and ensuring that employees receive appropriate training to perform their jobs safely.
Conclusion
In conclusion, HSE training is essential for promoting a safe and healthy work environment and complying with OSHA standards. By investing in comprehensive training programs, employers can protect their employees, reduce workplace incidents, and enhance overall business performance.
OSHA Certification Online Free
How to Get OSHA 510 Certification
FAQs
- What are the consequences of non-compliance with OSHA’s HSE training requirements?
- Non-compliance with OSHA’s HSE training requirements can result in citations, fines, and penalties imposed by OSHA. Additionally, failure to adhere to these standards may lead to legal liabilities, reputational damage, and increased insurance costs for employers.
- How often should employers provide HSE training to employees?
- The frequency of HSE training depends on various factors, including the nature of the workplace hazards, job responsibilities, and regulatory requirements. Generally, initial training should be provided to new employees, and refresher training should be conducted periodically to reinforce knowledge and address any changes in hazards or regulations.
- Are there any exemptions to OSHA’s HSE training standards?
- OSHA standards apply to most workplaces in the United States, but there are some exemptions and special considerations for certain industries and situations. Employers should familiarize themselves with the specific standards applicable to their industry and consult with OSHA or legal experts if they have questions about exemptions.
- Can employers use third-party training providers to fulfill HSE training requirements?
- Yes, employers can use third-party training providers to fulfill HSE training requirements, as long as the training meets OSHA standards and addresses the specific hazards and needs of the workplace. It’s essential for employers to ensure that the training provider is reputable, qualified, and able to deliver effective training.
- What resources are available to help employers develop HSE training programs?
- OSHA provides a wealth of resources to help employers develop and implement effective HSE training programs. These resources include guidance documents, training materials, online courses, and consultation services. Employers can also seek assistance from industry associations, trade unions, and professional organizations specializing in workplace safety and health.