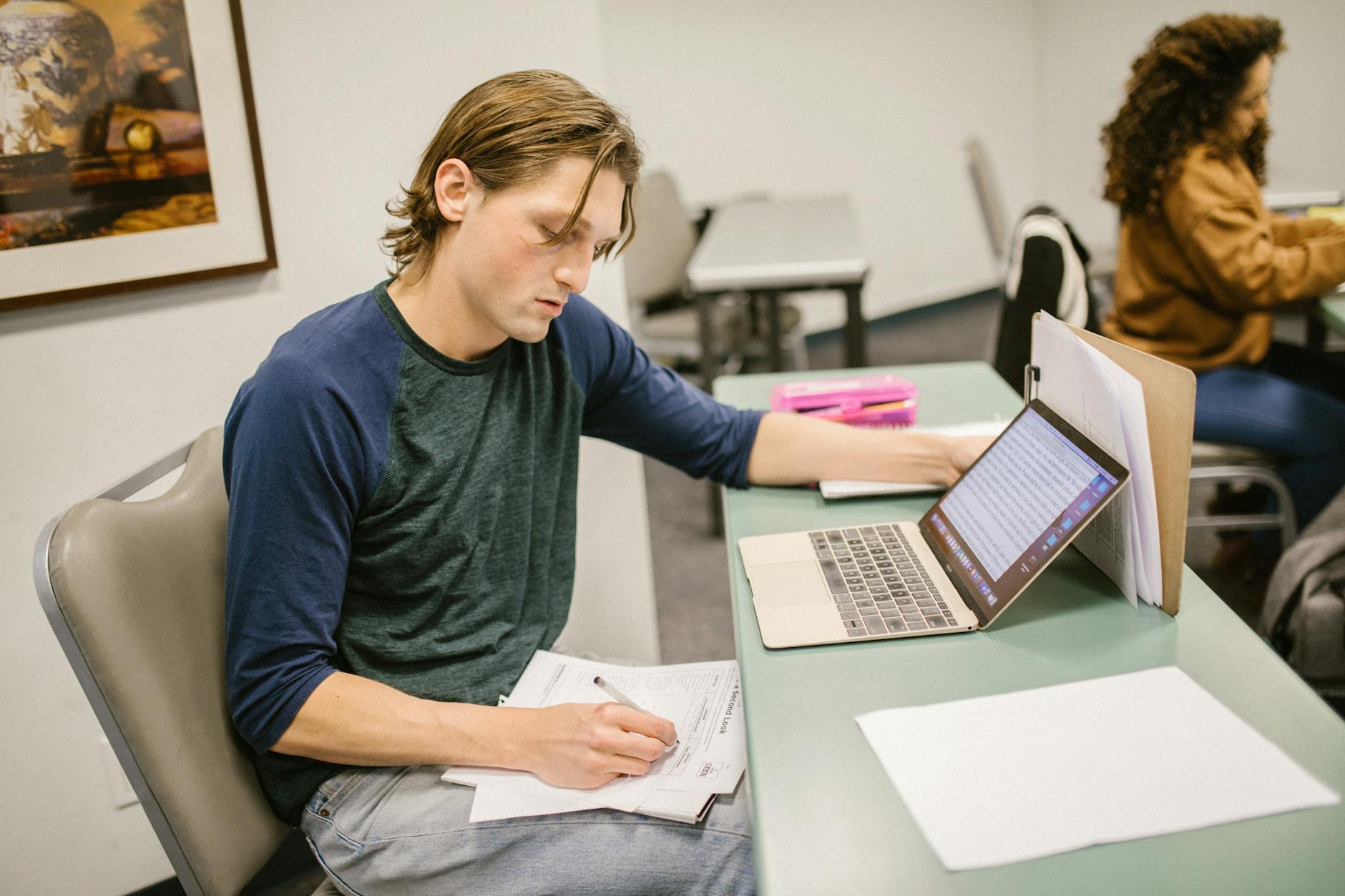
HSE Risk Assessment Techniques
Risk assessment is a fundamental component of Health, Safety, and Environment (HSE) management. It involves identifying potential hazards, evaluating the risks associated with them, and implementing measures to control or eliminate those risks. Effective risk assessment not only ensures compliance with legal requirements but also protects employees, reduces incidents, and enhances workplace productivity. In this article, we’ll explore the most effective HSE risk assessment techniques, providing you with a step-by-step guide to creating a safer work environment.
1. What is HSE Risk Assessment?
HSE risk assessment is a systematic process of identifying hazards, analyzing the risks they pose, and determining appropriate control measures. It is a proactive approach to preventing workplace accidents, illnesses, and environmental damage. The goal is to minimize risks to an acceptable level, ensuring the safety and well-being of employees and the surrounding environment.
2. Why is Risk Assessment Important?
- Legal Compliance: Many countries require employers to conduct risk assessments under occupational health and safety laws.
- Accident Prevention: Identifying and mitigating risks reduces the likelihood of workplace incidents.
- Cost Savings: Preventing accidents and illnesses can save organizations significant costs related to medical expenses, legal fees, and lost productivity.
- Employee Confidence: A safe workplace boosts employee morale and trust in the organization.
- Environmental Protection: Risk assessments help identify and mitigate environmental hazards, promoting sustainability.
3. Step-by-Step Guide to Conducting an HSE Risk Assessment
Here’s a detailed breakdown of the risk assessment process:
Step 1: Identify Hazards
- Workplace Inspections: Walk through the workplace to identify potential hazards, such as slippery floors, exposed wiring, or hazardous chemicals.
- Employee Feedback: Consult employees, as they often have firsthand knowledge of workplace risks.
- Review Incident Reports: Analyze past incidents to identify recurring hazards.
- Check Equipment and Machinery: Ensure all equipment is properly maintained and used correctly.
Step 2: Determine Who Might Be Harmed
- Employees: Consider all workers, including full-time, part-time, and temporary staff.
- Visitors: Include contractors, clients, and other visitors who may be exposed to hazards.
- Vulnerable Groups: Pay special attention to vulnerable individuals, such as pregnant women, young workers, or those with disabilities.
Step 3: Evaluate the Risks
- Likelihood: Assess how likely it is that a hazard will cause harm.
- Severity: Determine the potential consequences of the hazard, such as minor injury, major injury, or fatality.
- Risk Matrix: Use a risk matrix to prioritize risks based on their likelihood and severity.
Step 4: Implement Control Measures
- Elimination: Remove the hazard entirely, if possible.
- Substitution: Replace the hazard with a safer alternative.
- Engineering Controls: Use physical changes, such as machine guards or ventilation systems, to reduce risks.
- Administrative Controls: Implement policies, procedures, and training to minimize exposure to hazards.
- Personal Protective Equipment (PPE): Provide PPE as a last line of defense.
Step 5: Record Your Findings
- Document the hazards identified, the risks assessed, and the control measures implemented.
- Ensure the risk assessment report is accessible to all employees.
Step 6: Review and Update
- Regularly review your risk assessment to ensure it remains accurate and effective.
- Update the assessment whenever there are significant changes in the workplace, such as new equipment, processes, or regulations.
4. Common HSE Risk Assessment Techniques
Here are some widely used techniques for conducting HSE risk assessments:
1. Qualitative Risk Assessment
- Description: This technique uses descriptive scales to evaluate the likelihood and severity of risks.
- Example: A risk matrix with categories like “Low,” “Medium,” and “High.”
- Best For: Small businesses or workplaces with straightforward hazards.
2. Quantitative Risk Assessment
- Description: This technique uses numerical values to quantify risks, such as probability percentages or financial impact.
- Example: Calculating the probability of a chemical spill and its potential financial consequences.
- Best For: Complex industries like oil and gas or chemical manufacturing.
3. Job Safety Analysis (JSA)
- Description: This technique breaks down a job into individual tasks and identifies hazards associated with each task.
- Example: Analyzing the steps involved in operating a forklift and identifying potential risks.
- Best For: High-risk jobs or tasks with repetitive motions.
4. Hazard and Operability Study (HAZOP)
- Description: This technique systematically examines processes to identify deviations from intended operations and their potential consequences.
- Example: Analyzing a chemical plant’s operations to identify risks like leaks or explosions.
- Best For: Process industries like pharmaceuticals or petrochemicals.
5. Failure Mode and Effects Analysis (FMEA)
- Description: This technique identifies potential failure modes in a system, process, or product and assesses their impact.
- Example: Evaluating the failure modes of a machine and their effects on production.
- Best For: Manufacturing and engineering industries.
6. Bowtie Analysis
- Description: This technique visualizes risks using a bowtie diagram, with the hazard in the center, preventive controls on the left, and mitigative controls on the right.
- Example: Analyzing the risk of a fire and identifying preventive measures (e.g., fire alarms) and mitigative measures (e.g., fire extinguishers).
- Best For: High-risk industries like aviation or mining.
5. Tips for Effective Risk Assessment
- Involve Employees: Employees often have valuable insights into workplace hazards.
- Use Checklists: Checklists ensure that no hazards are overlooked during the assessment.
- Stay Updated: Keep abreast of new regulations, technologies, and best practices in HSE.
- Train Assessors: Ensure that those conducting risk assessments are properly trained and competent.
- Communicate Findings: Share the results of the risk assessment with all relevant stakeholders.
6. Common Challenges in Risk Assessment
- Incomplete Hazard Identification: Missing hazards can lead to unaddressed risks.
- Subjectivity: Qualitative assessments can be subjective, leading to inconsistent results.
- Resource Constraints: Small businesses may lack the resources to conduct thorough risk assessments.
- Resistance to Change: Employees may resist implementing new control measures.
To overcome these challenges, prioritize thoroughness, use multiple assessment techniques, and foster a culture of safety.
7. Tools and Software for Risk Assessment
Several tools and software solutions can streamline the risk assessment process:
- Risk Assessment Templates: Pre-designed templates help standardize the process.
- HSE Software: Tools like SafetyCulture, iAuditor, and RiskWatch automate risk assessments and generate reports.
- Mobile Apps: Apps like HSE Toolkit provide on-the-go access to risk assessment tools.
8. Case Study: Successful Risk Assessment in Action
Scenario: A manufacturing plant identified frequent incidents of machinery-related injuries.
Solution: The plant conducted a Job Safety Analysis (JSA) and implemented engineering controls (e.g., machine guards) and administrative controls (e.g., training programs).
Outcome: Machinery-related injuries decreased by 70% within six months.
9. Conclusion
HSE risk assessment is a vital process for identifying and mitigating workplace hazards. By using techniques like qualitative and quantitative assessments, JSA, HAZOP, and Bowtie Analysis, organizations can create safer and more compliant workplaces. Remember, risk assessment is an ongoing process that requires regular review and employee involvement. Start implementing these techniques today to protect your workforce, reduce incidents, and promote a culture of safety.
Hazard Identification and Risk Assessment Matrix
5 Hierarchy of Control with Examples
Hazard Hierarchy of Control | Free Download PPT
Importance of HIRA (Hazard Identification and Risk Assessment)