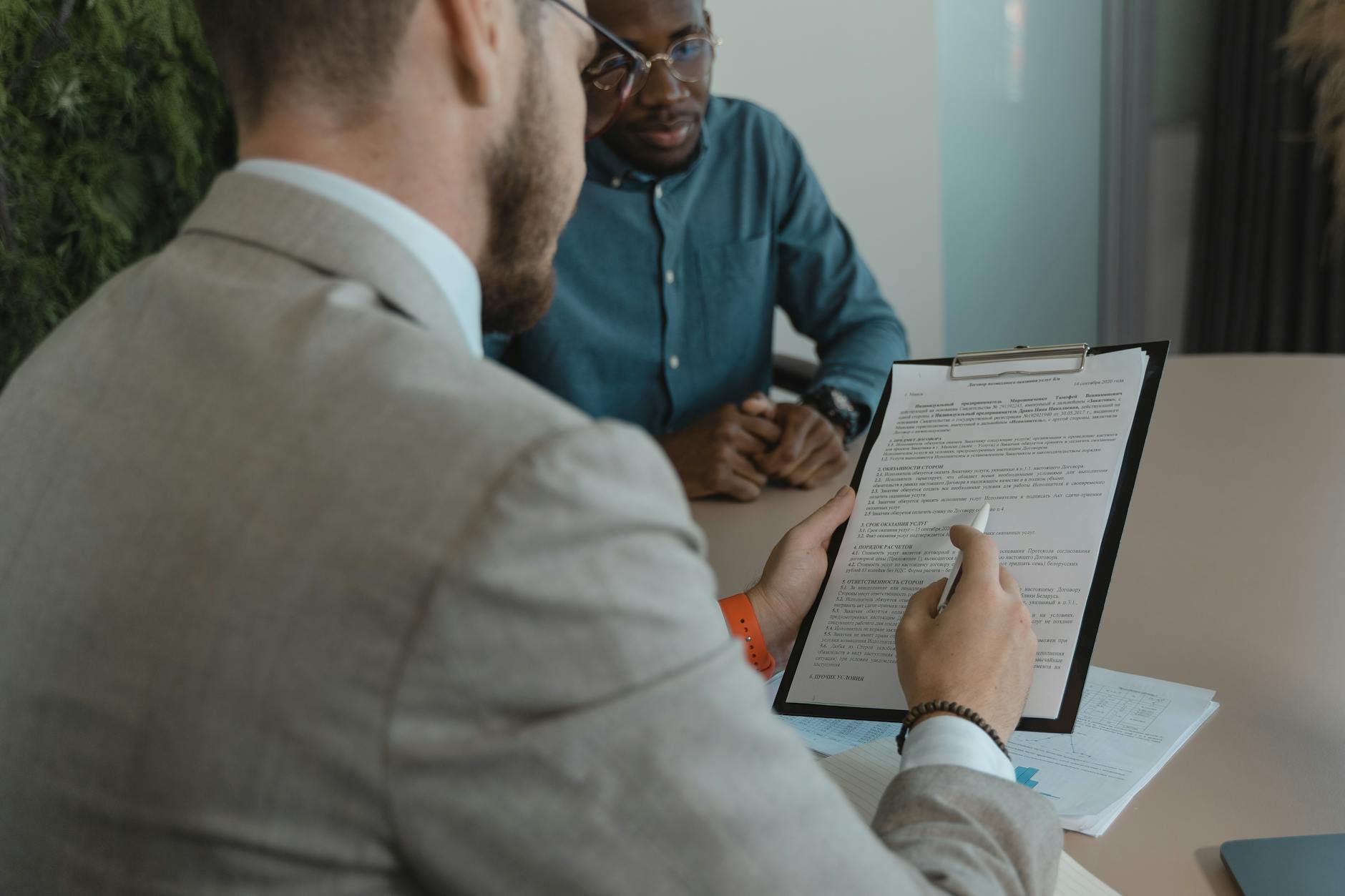
HSE Engineer Interview Questions and Answers in 2025
1. What does HSE stand for, and why is it important in an organization?
Answer: HSE stands for Health, Safety, and Environment. It is crucial because it ensures a safe working environment, reduces risk to employees, and helps in maintaining environmental sustainability, which contributes to the overall well-being of the workforce and the organization’s reputation.
2. Can you describe your experience with HSE regulations?
Answer: I have extensive experience working with OSHA, EPA, and local regulations. I ensure that the company complies with all the relevant legal and environmental standards and promote safety training programs for employees.
3. How do you ensure compliance with safety standards on-site?
Answer: I conduct regular safety audits, risk assessments, and inspections to identify hazards. I also develop and implement safety protocols, deliver training programs, and ensure workers are properly equipped with safety gear.
4. What is your approach to conducting a risk assessment?
Answer: I use a systematic approach to identify potential hazards in the workplace. This includes reviewing past incidents, conducting interviews with workers, analyzing work processes, and determining the likelihood and severity of risks. I then implement controls to mitigate the risks.
5. Can you give an example of a safety program you’ve developed?
Answer: I developed a “Behavior-Based Safety Program” that focused on encouraging safe behaviors. It included observations, feedback sessions, and reward systems to promote safety. The program resulted in a 25% reduction in accidents in the first year.
6. How do you handle emergency situations?
Answer: I follow the emergency response plan, which includes evacuation procedures, first-aid protocols, and coordination with emergency services. I also ensure that regular drills are conducted so everyone knows their role in case of an emergency.
7. How do you stay updated with changing safety regulations?
Answer: I attend HSE conferences, subscribe to industry publications, and take part in webinars. I also network with other safety professionals to stay informed about any changes in safety regulations.
8. How would you handle a situation where a worker refuses to follow safety protocols?
Answer: I would first speak with the worker to understand the reason behind their behavior. I would then explain the importance of safety protocols and the potential consequences of not following them. If the issue persists, I would escalate the matter to management for further action.
9. What safety systems are you familiar with?
Answer: I am familiar with Safety Management Systems (SMS) like ISO 45001, behavior-based safety programs, risk assessment systems, and emergency response protocols. I also have experience using digital safety tools for tracking incidents and managing safety data.
10. Describe a situation where you improved safety performance.
Answer: In my previous role, I identified a high rate of near-miss incidents in a warehouse. I implemented a near-miss reporting system and safety workshops, which resulted in a 30% decrease in actual accidents within the first six months.
11. What is your experience with incident investigation?
Answer: I am experienced in conducting incident investigations by gathering facts, interviewing witnesses, identifying root causes, and recommending corrective actions to prevent recurrence. I ensure that the investigation report is thorough and actionable.
12. How do you ensure the safety of workers when using hazardous chemicals?
Answer: I ensure that proper risk assessments are conducted before using hazardous chemicals, that workers are trained in handling them safely, and that appropriate Personal Protective Equipment (PPE) is used. I also ensure that Material Safety Data Sheets (MSDS) are available and up to date.
13. What are some key performance indicators (KPIs) you would track to measure safety?
Answer: KPIs include accident frequency rates, near-miss reports, safety audit results, training completion rates, and employee participation in safety programs.
14. How do you promote a safety culture within an organization?
Answer: I promote a safety culture by encouraging open communication, offering safety training, recognizing employees who demonstrate excellent safety practices, and involving everyone in safety-related decision-making processes.
15. What role does leadership play in maintaining safety in the workplace?
Answer: Leadership sets the tone for safety by prioritizing it in daily operations, leading by example, allocating resources for safety programs, and creating a culture where safety is everyone’s responsibility.
16. How would you assess the environmental risks in a workplace?
Answer: I would conduct a thorough review of the workplace, including evaluating emissions, waste management practices, energy consumption, and water usage. I would then identify potential environmental risks and recommend solutions to minimize the impact.
17. Have you ever dealt with a workplace accident? What steps did you take?
Answer: Yes, I’ve handled workplace accidents by immediately ensuring medical attention for the injured, securing the accident scene to prevent further incidents, conducting an investigation, and implementing corrective actions to prevent recurrence.
18. How do you manage safety training for new employees?
Answer: I ensure that new employees undergo comprehensive safety training, including a general orientation and specific training based on their roles. This includes both theoretical and practical training, such as emergency response and hazard identification.
19. What are some common safety hazards in the oil and gas industry?
Answer: Common hazards include exposure to toxic chemicals, falls from heights, fire and explosion risks, equipment malfunctions, and poor ergonomics. I work to mitigate these risks through continuous training, proper maintenance, and ensuring safety standards are met.
20. How do you handle contractor safety on-site?
Answer: I ensure that contractors are pre-qualified for safety, adhere to the same safety standards as regular employees, and receive proper orientation and training. I also monitor their work and enforce compliance with safety protocols.
21. What are your thoughts on zero-accident policies?
Answer: While a zero-accident policy is an admirable goal, I believe it’s important to focus on continuous improvement, risk mitigation, and fostering a safety culture. It’s more practical to aim for zero incidents through proactive safety measures.
22. How do you handle conflicting safety opinions on-site?
Answer: I would listen to all parties involved, analyze the situation, and base my decision on established safety standards and regulations. If needed, I would consult with experts or refer to regulatory guidelines to ensure the best decision is made.
23. What are the most critical elements of an effective HSE management system?
Answer: The critical elements include clear policies, risk assessments, employee involvement, regular safety audits, management review, and continuous improvement practices. Communication and training are also key to ensuring success.
24. How do you balance safety with productivity?
Answer: Safety should never be compromised for productivity. I work to ensure that safety protocols are integrated into workflows in a way that doesn’t hinder productivity. Efficiency can be achieved through proper planning, training, and hazard controls.
25. How would you approach a situation where safety measures are costing the company too much?
Answer: I would evaluate the cost-effectiveness of current safety measures, seeking alternatives or improvements that maintain safety standards while reducing costs. I would also present data to show the long-term cost savings of maintaining strong safety protocols.
26. How do you handle documentation and reporting in HSE?
Answer: I ensure that all incidents, audits, inspections, and training sessions are documented accurately and promptly. I maintain detailed records and provide reports to management, following the company’s procedures for transparency and compliance.
27. What tools and software do you use to manage HSE activities?
Answer: I use software such as SAP EHS, Proact, and SafetyCulture to track incidents, conduct audits, and manage safety documentation. These tools help streamline reporting and improve data accuracy.
28. How do you motivate employees to prioritize safety?
Answer: I motivate employees by recognizing their safety efforts, providing incentives for meeting safety goals, and fostering a work environment where they feel their health and safety are valued. Regular safety meetings and open communication are also key.
29. What are some effective ways to handle fatigue-related safety risks?
Answer: I ensure that employees have proper rest periods, implement shift rotation systems, and encourage awareness about the signs of fatigue. I also promote an open dialogue about fatigue management and create a supportive environment.
30. What would you do if you identified a serious safety violation?
Answer: I would immediately address the violation, stopping the activity if necessary to prevent harm. I would then conduct a thorough investigation, report the incident to management, and ensure corrective actions are taken to prevent recurrence.
Safety Manager Interview Questions and Answers in 2025
Safety Engineer Interview Questions and Answers 2025
Safety Officer Interview Questions and Answers in 2025
Safety Manager: 25 Safety Manager Technical Calculation Interview Questions and Answers
Safety Supervisor: 25 Safety Supervisor Technical Calculation Interview Questions and Answers