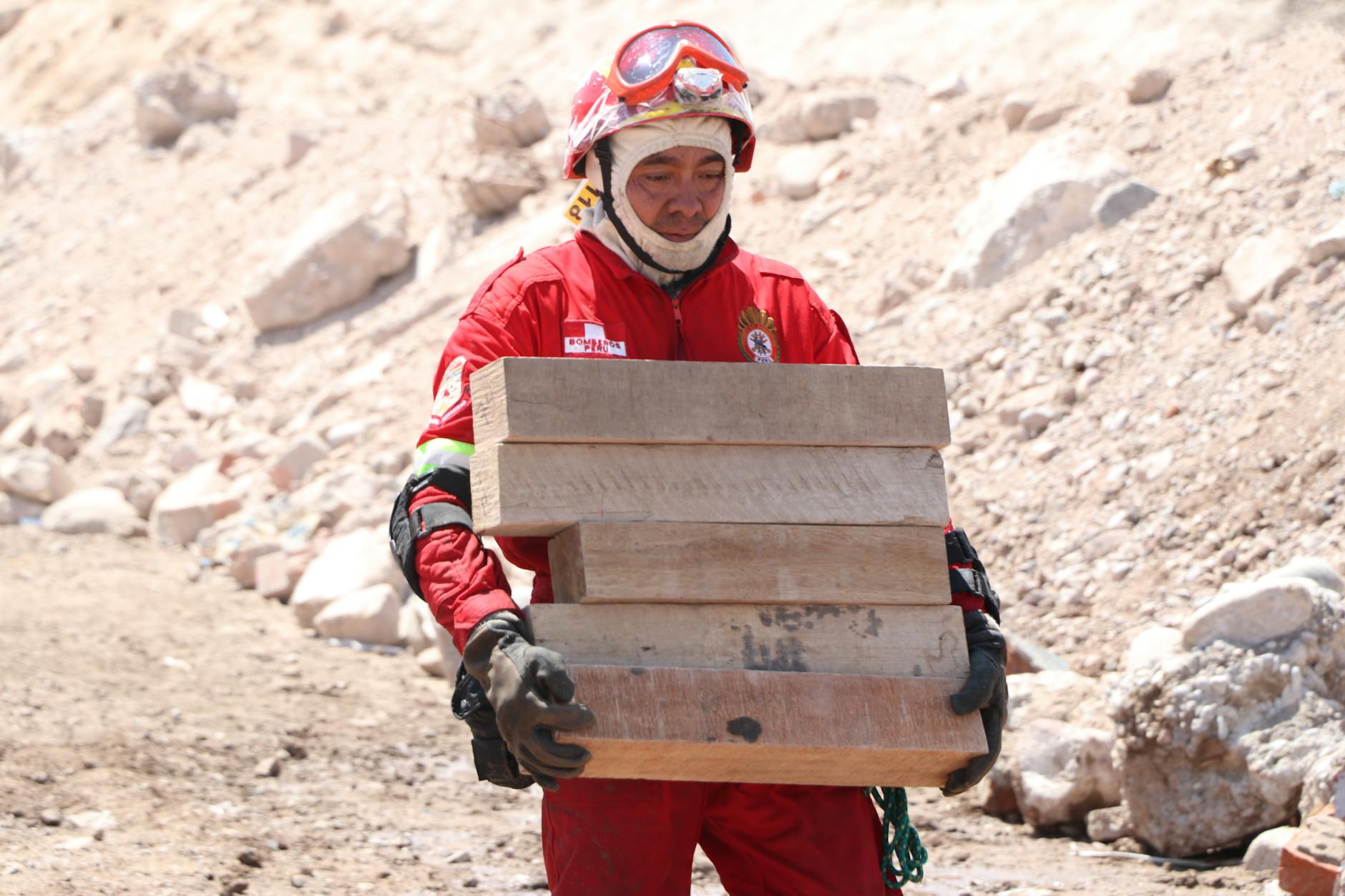
HSE Best Practices for Workplaces
Health, Safety, and Environment (HSE) is a critical aspect of any workplace, regardless of the industry. Implementing effective HSE practices not only ensures compliance with regulations but also fosters a safe and productive work environment. In this article, we’ll explore the best HSE practices for workplaces, covering everything from risk assessment to employee training and emergency preparedness. Whether you’re an HSE professional, a manager, or a business owner, these strategies will help you create a safer and more sustainable workplace.
1. Develop a Comprehensive HSE Policy
A well-defined HSE policy is the foundation of a safe workplace. Here’s how to create one:
- Define Objectives: Clearly outline your organization’s commitment to health, safety, and environmental protection.
- Assign Responsibilities: Designate roles and responsibilities for HSE management at all levels of the organization.
- Set Standards: Establish measurable goals for safety performance and environmental sustainability.
- Communicate the Policy: Ensure all employees are aware of the policy and understand their role in maintaining a safe workplace.
Your HSE policy should be reviewed and updated regularly to reflect changes in regulations, industry standards, and organizational goals.
2. Conduct Regular Risk Assessments
Risk assessment is a cornerstone of HSE management. Here’s how to do it effectively:
- Identify Hazards: Look for potential hazards in the workplace, such as chemical exposure, machinery risks, or ergonomic issues.
- Evaluate Risks: Assess the likelihood and severity of each hazard.
- Implement Controls: Introduce measures to eliminate or reduce risks, such as engineering controls, administrative controls, or personal protective equipment (PPE).
- Monitor and Review: Regularly review your risk assessments to ensure they remain accurate and effective.
Involve employees in the risk assessment process, as they often have valuable insights into workplace hazards.
3. Provide HSE Training for Employees
Training is essential for ensuring that employees understand and adhere to HSE practices. Here’s what to include in your training program:
- General Safety Training: Cover basic safety principles, emergency procedures, and the proper use of PPE.
- Job-Specific Training: Provide training tailored to the specific hazards and risks associated with each role.
- Environmental Awareness: Educate employees on sustainable practices, such as waste reduction and energy conservation.
- Refresher Courses: Offer regular training updates to reinforce knowledge and address new risks.
Use a mix of training methods, including classroom sessions, e-learning modules, and hands-on demonstrations.
4. Promote a Safety Culture
A strong safety culture is key to the success of any HSE program. Here’s how to foster one:
- Lead by Example: Managers and supervisors should demonstrate a commitment to safety in their actions and decisions.
- Encourage Reporting: Create a system for employees to report hazards, near-misses, and incidents without fear of retaliation.
- Recognize and Reward: Acknowledge employees who contribute to a safer workplace through awards or incentives.
- Communicate Regularly: Use newsletters, posters, and meetings to keep safety top of mind.
A positive safety culture encourages employees to take ownership of their own safety and that of their colleagues.
5. Implement Effective Emergency Preparedness Plans
Being prepared for emergencies can save lives and minimize damage. Here’s how to create an effective emergency preparedness plan:
- Identify Potential Emergencies: Consider scenarios like fires, chemical spills, natural disasters, and medical emergencies.
- Develop Response Procedures: Outline clear steps for responding to each type of emergency.
- Assign Roles: Designate employees to specific roles, such as evacuation coordinators or first aid responders.
- Conduct Drills: Regularly practice emergency procedures to ensure everyone knows what to do.
- Review and Update: Continuously improve your plan based on feedback and lessons learned from drills or actual incidents.
6. Monitor and Measure HSE Performance
Tracking your HSE performance helps you identify areas for improvement and demonstrate compliance. Here’s how to do it:
- Set Key Performance Indicators (KPIs): Examples include the number of incidents, near-misses, and safety training completion rates.
- Use Technology: Implement HSE software to track incidents, conduct audits, and generate reports.
- Conduct Audits: Regularly assess your HSE practices to ensure they align with regulations and best practices.
- Analyze Data: Use data to identify trends, root causes of incidents, and opportunities for improvement.
Share performance results with employees to keep them informed and engaged in your HSE efforts.
7. Focus on Environmental Sustainability
HSE isn’t just about safety—it’s also about protecting the environment. Here are some best practices for environmental sustainability:
- Reduce Waste: Implement recycling programs and minimize waste generation.
- Conserve Energy: Use energy-efficient equipment and encourage employees to turn off lights and devices when not in use.
- Manage Emissions: Monitor and reduce greenhouse gas emissions from your operations.
- Comply with Regulations: Stay up-to-date with environmental laws and ensure your practices meet or exceed requirements.
Sustainability initiatives not only benefit the environment but can also improve your organization’s reputation and reduce costs.
8. Engage Employees in HSE Initiatives
Employees are your greatest asset when it comes to HSE. Here’s how to involve them:
- Safety Committees: Establish committees to discuss safety concerns and develop solutions.
- Feedback Mechanisms: Provide channels for employees to share their ideas and concerns about HSE.
- Empowerment: Give employees the authority to stop work if they identify unsafe conditions.
- Training Participation: Involve employees in the development and delivery of HSE training programs.
Engaged employees are more likely to take ownership of HSE practices and contribute to a safer workplace.
9. Stay Updated on HSE Regulations and Standards
HSE regulations and standards are constantly evolving. Here’s how to stay informed:
- Subscribe to Newsletters: Sign up for updates from regulatory bodies like OSHA, NEBOSH, and IOSH.
- Attend Industry Events: Participate in conferences, webinars, and workshops to learn about the latest trends and best practices.
- Network with Peers: Join professional associations and online forums to exchange knowledge with other HSE professionals.
Staying updated ensures that your HSE practices remain compliant and effective.
10. Continuously Improve Your HSE Program
HSE is an ongoing process, not a one-time effort. Here’s how to continuously improve your program:
- Learn from Incidents: Investigate incidents to identify root causes and implement corrective actions.
- Benchmark Against Industry Standards: Compare your practices with those of industry leaders to identify areas for improvement.
- Seek Feedback: Regularly ask employees for feedback on your HSE program and make adjustments as needed.
- Invest in Innovation: Explore new technologies and methodologies to enhance your HSE practices.
Conclusion
Implementing HSE best practices in the workplace is essential for protecting employees, ensuring compliance, and promoting sustainability. By developing a comprehensive HSE policy, conducting regular risk assessments, providing training, fostering a safety culture, and continuously improving your program, you can create a safer and more productive work environment. Remember, HSE is a shared responsibility—everyone in the organization has a role to play. Start implementing these best practices today and make safety a priority in your workplace.
Hazard Identification and Risk Assessment Matrix
5 Hierarchy of Control with Examples