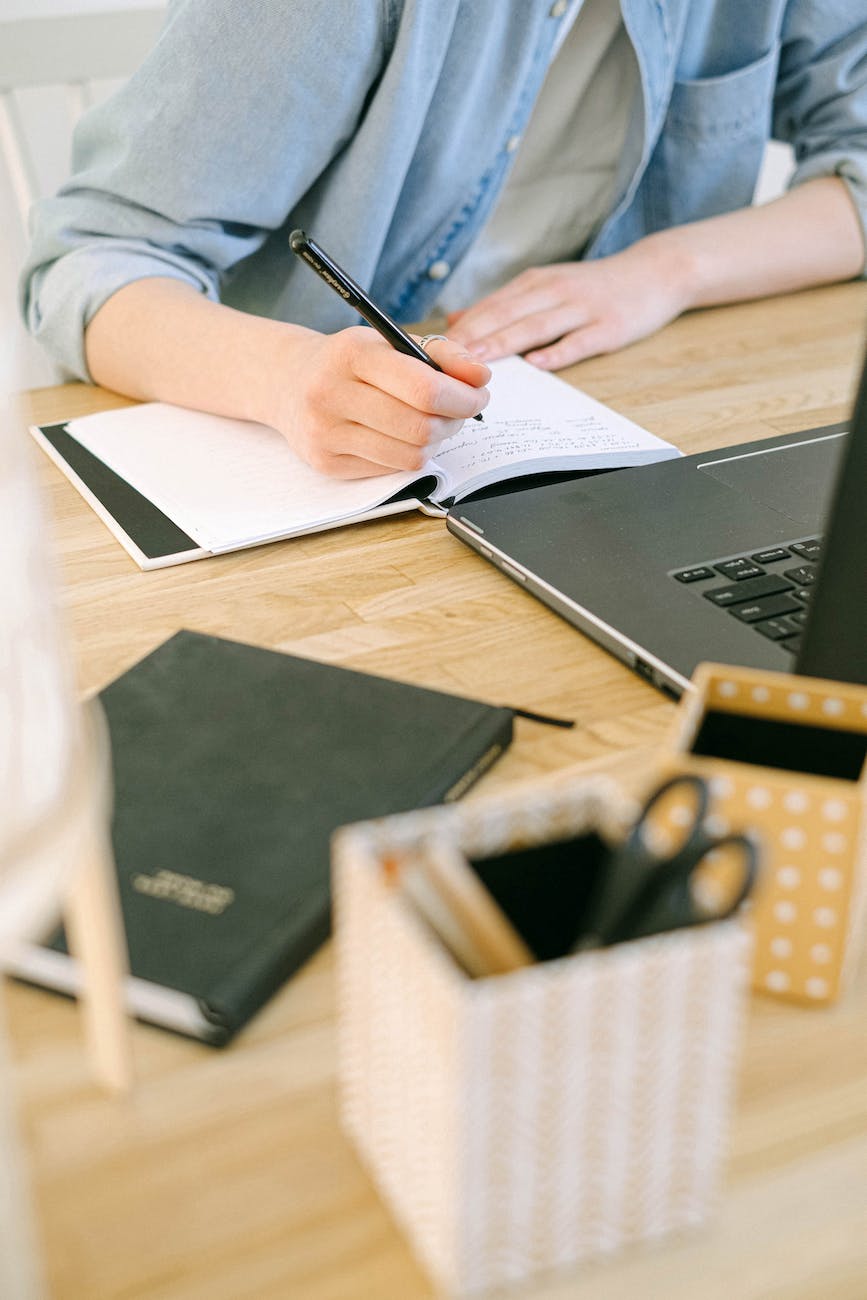
How to Write Standard Operating Procedure
Standard Operating Procedures (SOPs) serve as foundational documents outlining step-by-step instructions for completing tasks within an organization. These documents are crucial for ensuring consistency, efficiency, and quality across operations. SOPs encompass detailed guidelines that help employees understand their roles, responsibilities, and the precise steps needed to carry out various processes.
Key Elements of Writing SOPs
Clear Objectives and Scope
An effective SOP begins with a clear definition of its objectives and scope. This clarity ensures that the document focuses on specific tasks or processes, eliminating ambiguity for those following it.
Detailed Step-by-Step Instructions
Each SOP must contain comprehensive, sequential instructions. Breaking down tasks into smaller, actionable steps facilitates easy comprehension and execution by individuals at different skill levels.
Compliance and Regulatory Considerations
SOPs should align with industry standards and comply with relevant regulations. Addressing legal and compliance aspects within the document is crucial for maintaining organizational integrity.
Writing a standard operating procedure (SOP) involves several key steps:
- Title and Purpose: Begin with a clear title that defines the process or activity. Follow it with a brief description or purpose of the SOP.
- Scope: Define the scope of the procedure—what it covers, its boundaries, and what it doesn’t include.
- Responsibilities: Specify who is responsible for carrying out each step or task within the procedure.
- Materials and Equipment: List all necessary materials, tools, and equipment required to execute the procedure.
- Procedure Steps: Detail each step of the process in a clear, sequential manner. Use numbered lists or bullet points for easy comprehension.
- Safety Measures: Include safety precautions or specific measures to ensure the safety of individuals involved in executing the procedure.
- Troubleshooting: Anticipate potential issues or challenges that may arise during the process and provide solutions or troubleshooting steps.
- Quality Control: Describe any checkpoints, quality assurance steps, or checkpoints to ensure the procedure is carried out correctly.
- References and Documents: Include any references, guidelines, or supporting documents that are essential for executing the procedure.
- Review and Approval: Have the SOP reviewed by relevant stakeholders to ensure accuracy, compliance, and effectiveness. Obtain necessary approvals before finalizing the document.
- Version Control: Implement a system to track revisions and updates to the SOP. Maintain a record of version history and ensure that the latest version is accessible to all relevant personnel.
- Training: Develop a training plan or materials to ensure that individuals involved understand and can effectively execute the procedure.
Remember, an SOP should be clear, concise, and easily understandable by anyone following it. Regular reviews and updates are also crucial to keep the procedure current and aligned with any changes in processes or regulations.
Structuring an SOP
Title and Purpose
An SOP should have a concise title that reflects its purpose. Clearly stating the document’s objective at the outset helps readers understand its relevance.
Responsibilities and Stakeholders
Identifying key stakeholders and outlining their responsibilities within the SOP ensures accountability and smooth execution of tasks.
Procedures and Workflows
Presenting procedures in a logical sequence with visual aids, if applicable, aids in understanding complex workflows.
Writing Style and Language in SOPs
Clarity and Simplicity
Using plain language devoid of jargon ensures easy comprehension for all readers. Simple sentences and clear instructions are the cornerstones of an effective SOP.
Consistent Formatting and Tone
Maintaining a consistent format and tone throughout the document enhances readability and professionalism.
SOP Implementation and Review Process
Training and Communication
Proper training and effective communication regarding SOPs are imperative. Employees must be well-versed in utilizing these documents to uphold operational standards.
Feedback and Improvement Loops
Regular feedback mechanisms and periodic reviews help identify inefficiencies and facilitate continuous improvement in SOPs.
Here's an example of a Standard Operating Procedure (SOP) for "Work at Height":
Title: Work at Height Standard Operating Procedure
Purpose: This SOP outlines the safety measures and procedures to be followed when working at heights to minimize the risk of accidents or injuries.
Scope: This procedure applies to all employees and contractors involved in tasks that require working at heights exceeding above ground level.
Responsibilities:
- Workers: Follow all safety protocols, wear appropriate personal protective equipment (PPE), and report any hazards immediately.
- Supervisors: Ensure workers are trained, conduct pre-task briefings, inspect equipment, and enforce safety procedures.
- Safety Officers: Conduct regular site inspections, provide guidance on safety practices, and review and update this SOP as needed.
Materials and Equipment:
- Safety harnesses and lanyards
- Guardrails and toe boards
- Secure scaffolding or elevated work platforms
- Safety nets
- Helmets, gloves, and appropriate footwear
Procedure Steps:
- Risk Assessment and Planning:
- Before starting work, conduct a thorough risk assessment of the site.
- Identify potential hazards, assess the stability of structures, and plan for emergency procedures.
- Training and Certification:
- Ensure all personnel involved in work at height are adequately trained and certified for the task.
- Provide training on equipment use, emergency procedures, and safe work practices.
- Preparation and Inspection:
- Inspect all equipment and tools to be used for working at heights.
- Check the condition and integrity of ladders, scaffolds, harnesses, and other safety gear before use.
- Personal Protective Equipment (PPE):
- Workers must wear appropriate PPE, including safety harnesses, helmets, gloves, and non-slip footwear.
- Ensure PPE is correctly fitted and in good condition.
- Securing the Work Area:
- Erect guardrails, toe boards, or safety nets where applicable.
- Secure scaffolding or elevated work platforms properly to prevent movement or instability.
- Work Execution:
- Use designated access points to reach heights whenever possible.
- Avoid overreaching while working and maintain three points of contact when climbing.
- Secure tools and materials to prevent dropping objects.
- Communication and Monitoring:
- Maintain clear communication among workers engaged in tasks at height.
- Regularly monitor the work area for any changes or potential hazards.
- Emergency Procedures:
- Establish emergency rescue procedures and ensure all workers are familiar with them.
- Have a rescue plan in place in case of accidents or emergencies.
References and Documents:
- Relevant safety regulations and guidelines.
- Manufacturer’s instructions for equipment use and maintenance.
Review and Approval: This SOP shall be reviewed annually or whenever there are significant changes in work procedures or regulations. Approval from the Safety Manager is required for any updates.
Conclusion
In conclusion, crafting a well-defined Standard Operating Procedure involves meticulous attention to detail, clarity in communication, and adherence to industry standards. These documents serve as guiding principles for employees, ensuring operational efficiency and consistency.
7 Steps of Standard Operating Procedure
Step-by-Step Standard Operating Procedure
Standard Operating Procedure Examples
List of Standard Operating Procedures
FAQs on Writing Standard Operating Procedures
- Why are SOPs essential in a business setting? SOPs are crucial in a business as they provide clear guidelines and instructions for performing tasks consistently. They ensure uniformity, efficiency, and quality in operations, reducing errors and improving productivity.
- How often should SOPs be updated or reviewed? SOPs should undergo regular reviews to keep pace with changing processes, technologies, or regulations. Typically, they are reviewed annually or whenever there’s a significant change in the workflow.
- Can SOPs be adapted for different departments within an organization? Yes, SOPs can and often should be tailored to suit the specific needs and processes of different departments. While the basic structure might remain the same, the content can be customized to fit each department’s requirements.
- What role does employee training play in implementing SOPs effectively? Employee training is pivotal for successful SOP implementation. Training ensures that employees understand and follow the procedures outlined in the SOP, reducing errors and ensuring compliance.
- Are there software tools available to streamline SOP creation and management? Yes, there are various software tools designed specifically for creating, managing, and updating SOPs. These tools offer features like templates, version control, and collaborative editing, making SOP management more efficient.
To the hsestudyguide.com webmaster, Thanks for the well-written and informative post!