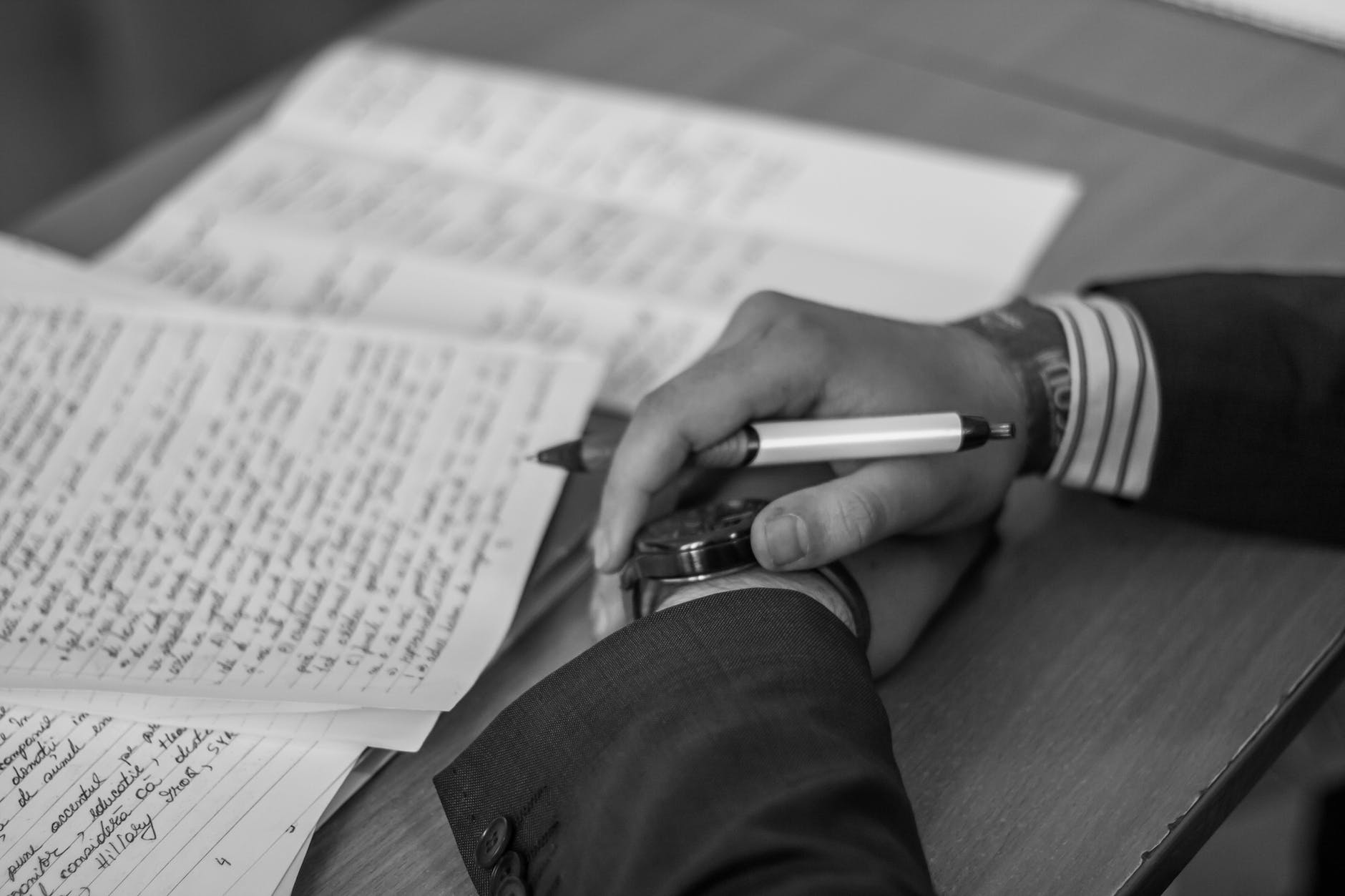
How to Validate Root Cause in Six Sigma
Root cause validation is a critical step in the Six Sigma methodology, a powerful approach aimed at improving processes and eliminating defects. In this article, we will explore the intricacies of validating root causes in Six Sigma, understanding the challenges, and employing effective strategies for successful validation.
Introduction
Six Sigma, a data-driven methodology, seeks to enhance process efficiency and minimize variations, ultimately leading to improved product or service quality. Central to its success is the identification and validation of root causes, laying the foundation for sustainable process improvement.
Understanding Six Sigma Methodology
At its core, Six Sigma strives for excellence by reducing defects and ensuring consistency. This methodology operates on statistical principles, employing a structured approach known as DMAIC – Define, Measure, Analyze, Improve, and Control.
The Role of Root Cause Analysis in Six Sigma
Root cause analysis is pivotal in the Six Sigma journey, as it helps identify the underlying issues contributing to defects. This proactive approach ensures that corrective measures address the core problems, preventing recurrence.
Challenges in Identifying Root Causes
Despite its effectiveness, the root cause identification process is not without challenges. Common obstacles include inadequate data, biased assumptions, and resistance to change. Overcoming these hurdles is crucial for accurate analysis.
Six Sigma Tools for Root Cause Analysis
DMAIC, a structured problem-solving method, guides Six Sigma practitioners. Tools like Fishbone Diagrams and Pareto Analysis play key roles in identifying root causes, providing a visual representation of complex relationships.
Validation of Root Causes
Validating identified root causes is a critical phase in Six Sigma, ensuring that the proposed causes indeed contribute to the observed issues. This step enhances the reliability of the improvement process.
Methods for Validating Root Causes
Statistical analysis forms the backbone of root cause validation in Six Sigma. By leveraging data-driven approaches, practitioners can establish the credibility of identified causes. Real-life examples further illustrate the effectiveness of these methods.
Common Pitfalls in Validation Process
Errors in the validation stage can undermine the entire Six Sigma effort. Avoiding common pitfalls, such as incomplete data or hasty conclusions, is essential to maintain accuracy and reliability.
Perplexity in Six Sigma Validation
Perplexity, a measure of uncertainty, is inherent in the validation process. Striking a balance between complexity and clarity is crucial, ensuring a detailed analysis without overwhelming stakeholders.
Burstiness in Six Sigma Validation
Burstiness, the sporadic nature of data, adds another layer of complexity. Effectively managing burstiness allows practitioners to extract valuable insights, contributing to a more comprehensive understanding of root causes.
Balancing Specificity and Context in Validation
Maintaining specificity in root cause validation is crucial for accuracy. However, it’s equally important not to lose the broader context. Real-world examples demonstrate how Six Sigma practitioners can achieve this delicate balance.
Engaging the Reader in Six Sigma Validation
Writing in a conversational style, incorporating relatable scenarios, and using active voice techniques are essential to keep the reader engaged. By humanizing the technical aspects, the article becomes more accessible to a broader audience.
In Six Sigma, validating the root cause is a crucial step to ensure that the identified cause is indeed responsible for the observed problem. The validation process helps confirm that addressing the root cause will lead to a sustainable solution. Here are steps to validate the root cause in Six Sigma:
- Data Analysis:
- Collect and analyze relevant data to verify that the root cause is consistently associated with the problem.
- Use statistical methods to validate the significance of the correlation between the identified root cause and the observed issues.
- Correlation and Causation:
- Distinguish between correlation and causation. Ensure that the identified root cause is not just coincidentally associated with the problem but has a causal relationship.
- Verification through Evidence:
- Gather supporting evidence or documentation that links the root cause to the problem. This could include historical data, process maps, or any other relevant information.
- Expert Opinion:
- Seek input from subject matter experts or those with experience in the process. Their insights can provide additional validation and confidence in the identified root cause.
- Validation Testing:
- Implement a pilot test or validation study to assess the impact of addressing the root cause. This can help verify that the proposed solution effectively eliminates or reduces the problem.
- Control Group:
- If applicable, use a control group or comparative analysis to validate the effectiveness of addressing the root cause. Compare outcomes between a group where the root cause is addressed and a group where it is not.
- Feedback from Stakeholders:
- Obtain feedback from relevant stakeholders, including those directly affected by the problem and those involved in the process. Their perspectives can provide valuable insights into the validity of the root cause.
- Documentation:
- Document the validation process and results. This documentation is essential for future reference, audit purposes, and to communicate the validity of the identified root cause to others in the organization.
- Iterative Approach:
- Be open to feedback and continuously evaluate the effectiveness of the solution. If the problem persists or new issues arise, reassess the root cause and make adjustments as needed.
- Project Review:
- Conduct a thorough review of the entire Six Sigma project, including the identification and validation of the root cause. This ensures that the methodology and findings are robust and can withstand scrutiny.
Remember that the goal of Six Sigma is to achieve process improvement and long-term sustainability. Validating the root cause is a critical aspect of ensuring that the improvements made will have a lasting impact on the process.
Conclusion
In conclusion, validating root causes in Six Sigma is an intricate process that demands attention to detail and adherence to the methodology’s principles. A successful validation ensures that improvements are not only effective but sustainable in the long run.
FAQs
- What is Six Sigma?
- Six Sigma is a data-driven methodology aimed at improving process efficiency and minimizing defects through a structured problem-solving approach.
- How does DMAIC methodology contribute to Six Sigma?
- DMAIC, which stands for Define, Measure, Analyze, Improve, and Control, guides Six Sigma practitioners in a systematic approach to problem-solving and process improvement.
- Why is it essential to validate root causes?
- Validating root causes ensures that proposed solutions address the core issues, enhancing the reliability and effectiveness of the Six Sigma improvement process.
- Can you provide an example of successful root cause validation?
- Certainly! In a manufacturing setting, after identifying a machine malfunction as a root cause, rigorous statistical analysis confirmed the correlation, leading to targeted repairs and improved overall efficiency.
- What challenges commonly arise in Six Sigma validation?
- Challenges include inadequate data, biased assumptions, and resistance to change. Overcoming these hurdles is crucial for accurate root cause analysis in Six Sigma.