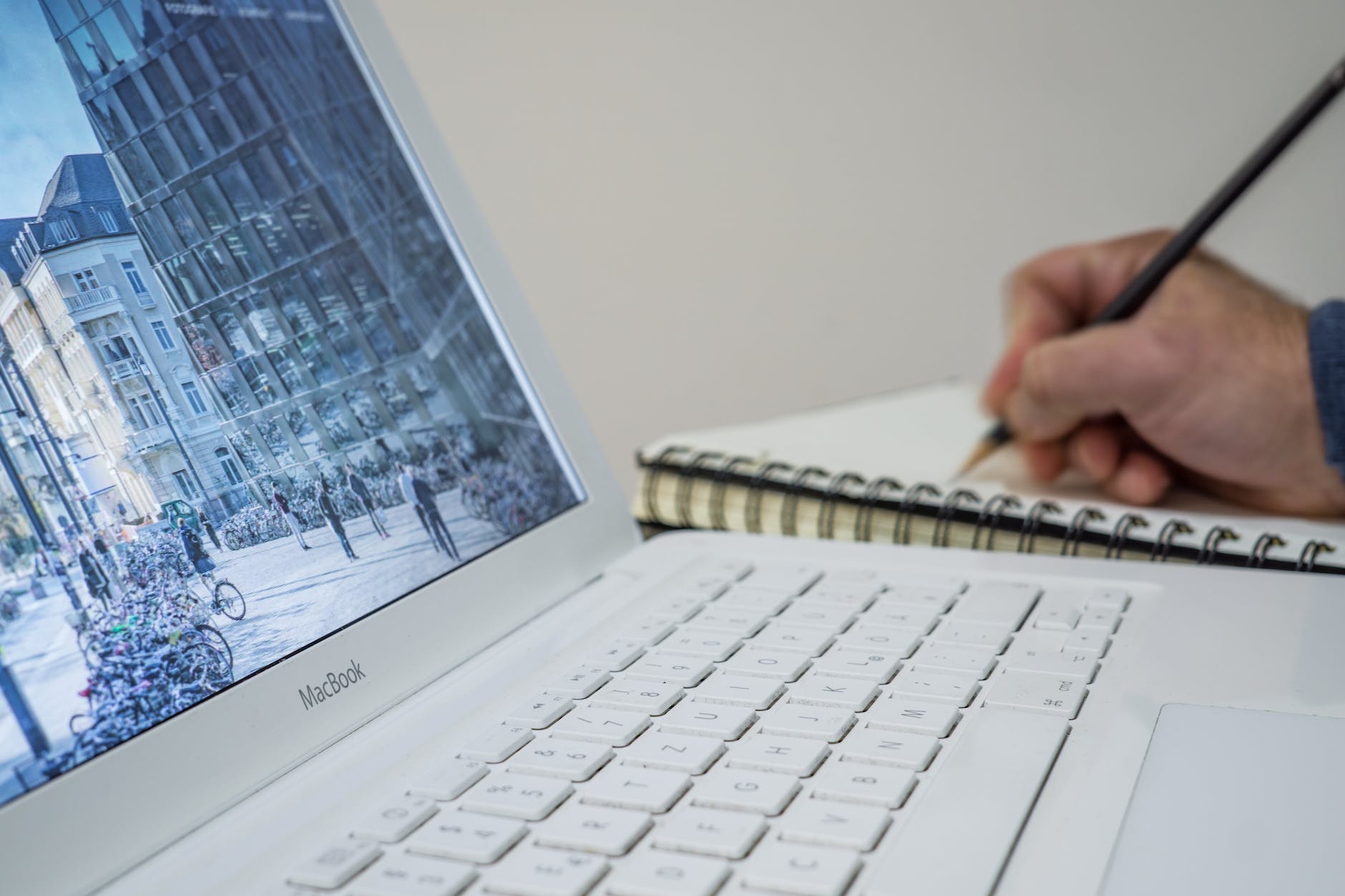
How To Prepare Risk Assessment for Noise
Introduction
How To Prepare Risk Assessment for Noise : In today’s industrial and commercial settings, noise is an omnipresent factor that can have adverse effects on both employees and the environment. To ensure a safe and compliant working environment, it is crucial to prepare a comprehensive noise risk assessment. This article will guide you through the process of creating a noise risk assessment from scratch, covering all the necessary aspects to keep your workplace in harmony.
Understanding Noise Risk
Noise risk is the potential harm or damage that can arise from exposure to excessive noise levels. This risk is not limited to hearing impairment but can also lead to other health problems, reduced productivity, and increased stress levels among employees. Understanding and mitigating noise risk is, therefore, of paramount importance.
Regulations and Compliance
Before diving into the nitty-gritty of noise risk assessment, it’s essential to be aware of the legal obligations and compliance requirements in your region. Noise regulations and permissible exposure limits may vary, but they generally aim to protect workers from excessive noise exposure. Ensure that you are well-versed in the specific laws applicable to your industry.
Steps to Prepare a Noise Risk Assessment
Creating a noise risk assessment involves several critical steps:
Identifying Noise Sources
Begin by identifying all potential sources of noise in your workplace. Categorize them as per their impact and frequency.
Noise Measurement
Use appropriate equipment to measure the noise levels accurately. This data is crucial for assessing risks and implementing control measures.
Risk Factors
Determine the factors contributing to noise-related risks, such as noise duration and intensity.
Assessing Exposure
Evaluate the level of exposure to noise for employees. This will help identify high-risk areas.
Risk Mitigation Strategies
Implement strategies to reduce noise risks, including engineering controls and administrative measures.
Personal Protective Equipment (PPE)
Provide suitable PPE to employees, such as ear protection, to further reduce noise exposure.
Training and Education
Educate employees about noise risks, prevention measures, and the proper use of PPE.
Record Keeping
Maintain comprehensive records of noise assessments and control measures for compliance and future reference.
Periodic Reviews
Regularly review and update noise risk assessments to ensure continued effectiveness.
Scenario: A Manufacturing Facility
Imagine you are the safety officer at a bustling manufacturing facility. The plant operates 24/7, with a variety of heavy machinery and equipment constantly in use. The cacophony of sounds within the facility ranges from the rhythmic hum of conveyor belts to the deafening clatter of metal stamping machines. It’s your responsibility to ensure the safety of the employees and compliance with noise regulations. Let’s walk through a noise risk assessment for this manufacturing facility:
Step 1: Identifying Noise Sources
You start by identifying the primary noise sources within the facility:
- Stamping Machines: The stamping machines that create metal components are incredibly noisy, with levels reaching 110 dB.
- Conveyor Belts: The continuous operation of conveyor belts generates a consistent 85 dB of noise.
- Forklifts: Forklifts beep when in reverse, and their engines add to the overall noise.
- Production Team: Employees operating machinery, especially those without hearing protection, contribute to noise exposure.
Step 2: Noise Measurement
You deploy a professional noise monitoring system to measure the noise levels accurately. This monitoring shows that the stamping machines’ noise levels are indeed hazardous to hearing.
Step 3: Risk Factors
Analyzing the data, you realize that noise intensity and duration are the two primary risk factors. Employees working around the stamping machines experience prolonged high-intensity noise levels.
Step 4: Assessing Exposure
You assess employee exposure based on their work hours and proximity to the noisy machinery. Those near the stamping machines are most at risk, particularly when they work extended shifts.
Step 5: Risk Mitigation Strategies
To mitigate the noise risks, you decide to implement several strategies:
- Engineering Controls: You opt for noise-reducing measures like installing acoustic enclosures around the stamping machines.
- Administrative Measures: You adjust work shifts to limit employee exposure to noisy machinery.
- PPE: You ensure that all employees working in noisy areas wear appropriate ear protection.
Step 6: Training and Education
You conduct workshops to educate employees about noise risks, the importance of wearing ear protection, and the correct use of such equipment.
Step 7: Record Keeping
Detailed records are maintained, including noise monitoring results, measures taken, and incidents related to noise exposure.
Step 8: Periodic Reviews
You establish a regular review schedule to evaluate the effectiveness of the implemented measures and update them as needed.
With these measures in place, you successfully reduce noise-related risks in your manufacturing facility, creating a safer and more comfortable work environment for your employees. Your commitment to noise risk assessment and mitigation ensures the well-being of your staff and compliance with the relevant regulations.
Case Studies
Let’s take a look at some real-life examples where noise risk assessments were conducted successfully. These case studies provide valuable insights and practical applications of the steps outlined in this article.
Conclusion
In conclusion, preparing a risk assessment for noise is an essential aspect of workplace safety and compliance. By identifying noise sources, accurately measuring noise levels, assessing exposure, and implementing risk mitigation strategies, you can create a safer and more productive work environment.
Acceptable Noise Levels in the Workplace
Noise Level Standards for Industry
Effects of Noise in the Workplace
Frequently Asked Questions (FAQs)
- Why is noise risk assessment important?
- Noise risk assessment is crucial for identifying and mitigating potential harm to employees and the environment due to excessive noise exposure.
- What are the legal requirements for noise risk assessment?
- Legal requirements vary by region, but they generally aim to protect workers from excessive noise exposure. Familiarize yourself with your local regulations.
- What is the role of personal protective equipment (PPE) in noise risk reduction?
- PPE, such as ear protection, can help reduce the risk of noise-related harm by providing a barrier between employees and excessive noise.
- How often should noise risk assessments be reviewed and updated?
- Noise risk assessments should be periodically reviewed and updated to ensure they remain effective and compliant with changing circumstances.
- What are some common engineering controls for noise risk mitigation?
- Engineering controls may include the use of quieter machinery, sound barriers, and acoustical enclosures to reduce noise levels in the workplace.