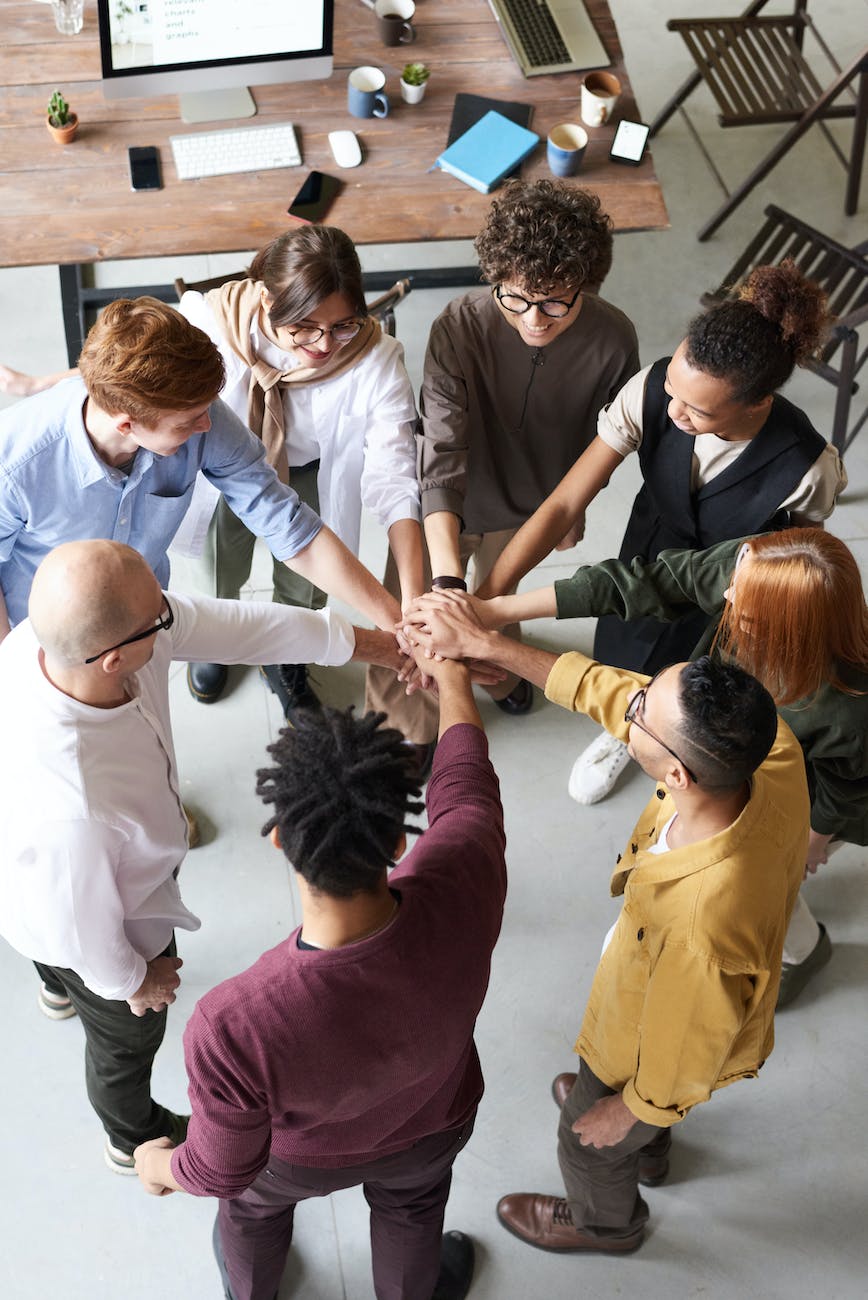
How To Conduct a Toolbox Talk Meeting at the Site
How To Conduct a Toolbox Talk Meeting : In the fast-paced world of construction and industrial work, safety is of paramount importance. Workers face numerous risks and hazards on a daily basis, making it crucial to have regular safety discussions. One effective way to address these concerns is through a “Toolbox Talk” meeting. This article will guide you through the process of conducting a successful Toolbox Talk meeting at the job site.
Introduction to Toolbox Talk
What is a Toolbox Talk?
A Toolbox Talk, also known as a safety meeting or tailgate meeting, is a short, informal discussion aimed at promoting safety awareness and addressing specific hazards and safety issues in the workplace. These talks are typically conducted at the job site before work begins, ensuring that all team members are aware of potential risks and safety protocols.
Importance of Toolbox Talks
Toolbox Talks play a vital role in maintaining a safe working environment. They foster a culture of safety, empower employees to voice their concerns, and ultimately reduce the likelihood of accidents and injuries. By investing time in regular safety discussions, companies demonstrate their commitment to the well-being of their workforce.
Preparing for the Meeting
Setting a Date and Time
To conduct an effective Toolbox Talk, start by scheduling the meeting at a time when all team members can attend. Avoid conflicting with critical work hours and ensure that everyone has ample time to focus on safety.
Selecting the Topic
Choose a relevant safety topic for discussion. Topics can range from the proper use of personal protective equipment (PPE) to specific job-related hazards. Selecting the right topic is essential to ensure that the meeting addresses current safety concerns.
Gathering Necessary Materials
Prepare any visual aids or props needed for the discussion. These might include safety posters, equipment samples, or accident case studies. Having these materials ready will enhance the effectiveness of the Toolbox Talk.
Assembling the Team
Involving All Stakeholders
Ensure that all relevant team members are included in the meeting. This includes workers, supervisors, and even subcontractors who are present on-site. A diverse group can provide valuable perspectives on safety issues.
Assigning Roles
Designate a facilitator to lead the discussion and a scribe to document the meeting’s key points and action items. Assigning roles ensures that the meeting runs smoothly and that important details are captured.
Ensuring Participation
Encourage active participation by creating an open and non-judgmental environment. Emphasize that every team member’s input is valuable and that safety is a collective responsibility.
Conducting the Meeting
Starting with Safety Reminders
Begin the Toolbox Talk by reminding everyone of the importance of safety. Highlight any recent incidents or near misses to underscore the relevance of the discussion.
Discussing the Chosen Topic
Delve into the selected safety topic, providing clear explanations and practical examples. Use real-life scenarios to make the topic relatable to the team.
Encouraging Questions and Feedback
Invite questions and encourage team members to share their experiences and insights. An interactive discussion promotes a deeper understanding of safety issues.
Ensuring Engagement
Using Visual Aids
Visual aids such as diagrams, videos, or infographics can help convey complex safety concepts effectively. Visuals are especially useful for team members who may have language barriers.
Sharing Real-Life Experiences
Share stories of past incidents or near misses that relate to the chosen topic. Personal anecdotes can make safety issues more tangible and memorable.
Interactive Discussions
Engage the team in discussions and hypothetical scenarios. Encourage them to brainstorm safety solutions and share their thoughts on improving safety measures.
Documenting the Toolbox Talk
Keeping Records
Maintain detailed records of each Toolbox Talk, including the date, topic, attendees, key points discussed, and action items assigned. This documentation helps track progress and compliance.
Monitoring Progress
Regularly review Toolbox Talk records to assess whether safety measures are being implemented and whether incident rates are decreasing.
Reviewing Previous Talks
Periodically revisit past Toolbox Talk topics to reinforce key safety concepts and ensure that they remain a priority.
Post-Meeting Actions
Implementing Safety Measures
Act on the action items identified during the Toolbox Talk. Ensure that safety measures are put in place promptly and effectively.
Following Up on Action Items
Assign responsibility for action items and set deadlines for completion. Regularly follow up to ensure that safety improvements are being made.
Encouraging Continuous Improvement
Promote a culture of continuous improvement by seeking feedback from team members and making adjustments to the Toolbox Talk process as needed.
Benefits of Toolbox Talks
Enhanced Safety Awareness
Toolbox Talks increase awareness of workplace hazards, making employees more vigilant about safety.
Improved Communication
Regular safety discussions foster open communication between team members and management.
Reduced Incidents and Accidents
By addressing safety concerns proactively, Toolbox Talks help reduce the number of workplace incidents and accidents.
Challenges and Solutions
Overcoming Resistance
Some team members may be resistant to Toolbox Talks. Address their concerns and emphasize the benefits of safety discussions.
Addressing Language Barriers
In multicultural workplaces, language barriers can be a challenge. Use visual aids and consider providing translations to ensure understanding.
Dealing with Time Constraints
In busy work environments, finding time for Toolbox Talks can be challenging. Schedule them strategically to minimize disruptions.
Measuring the Impact
Analyzing Incident Data
Track incident rates over time to assess the impact of Toolbox Talks on safety performance.
Employee Feedback Surveys
Collect feedback from team members to gauge the effectiveness of the Toolbox Talk process and make improvements.
Benchmarking with Industry Standards
Compare your safety performance with industry benchmarks to identify areas for improvement.
Legal and Regulatory Compliance
OSHA Requirements
Ensure that your Toolbox Talks comply with Occupational Safety and Health Administration (OSHA) regulations and any relevant local laws.
Local Regulations
Be aware of and adhere to any local safety regulations and requirements that apply to your specific industry or region.
Liability Mitigation
Regular Toolbox Talks can help mitigate liability by demonstrating a commitment to safety and a proactive approach to risk management.
Toolbox Talk Best Practices
Consistency is Key
Maintain a regular schedule of Toolbox Talks to keep safety a top priority.
Tailoring Topics to the Audience
Select topics that are relevant to the specific work being performed and the audience’s needs.
Celebrating Safety Successes
Acknowledge and celebrate safety milestones and achievements to motivate the team.
Conclusion
Prioritizing safety through Toolbox Talks is a vital component of any successful construction or industrial operation. By conducting regular meetings, addressing safety concerns, and fostering a culture of continuous improvement, organizations can create safer and more productive work environments.
Driving Safety At Work Toolbox Talk (TBT)
Confined Space Safety Toolbox Talk (TBT)
Environment Safety Toolbox Talk (TBT)
Hot Work Safety Toolbox Talk (TBT)
FAQs (Frequently Asked Questions)
- What is the ideal frequency for Toolbox Talk meetings?The frequency of Toolbox Talk meetings can vary depending on the industry and the specific risks involved. However, conducting them weekly or at the start of each shift is a common practice to keep safety a constant focus.
- Can Toolbox Talks be conducted virtually?Yes, Toolbox Talks can be conducted virtually, especially in situations where in-person meetings are not feasible. Virtual meetings can use video conferencing platforms to ensure remote team members are included.
- How can I encourage reluctant team members to participate?To encourage reluctant team members, emphasize the importance of their input in maintaining a safe work environment. Create a non-judgmental atmosphere and acknowledge their contributions.
- Are there any specific topics that should be covered regularly?Topics should be chosen based on the most relevant safety concerns at the time. However, topics such as PPE, hazard identification, and emergency procedures are often covered regularly.
- What should be included in the meeting minutes?Meeting minutes should include the date, topic discussed, names of attendees, key points covered, action items assigned, and deadlines for completion. These records help track safety progress and compliance.