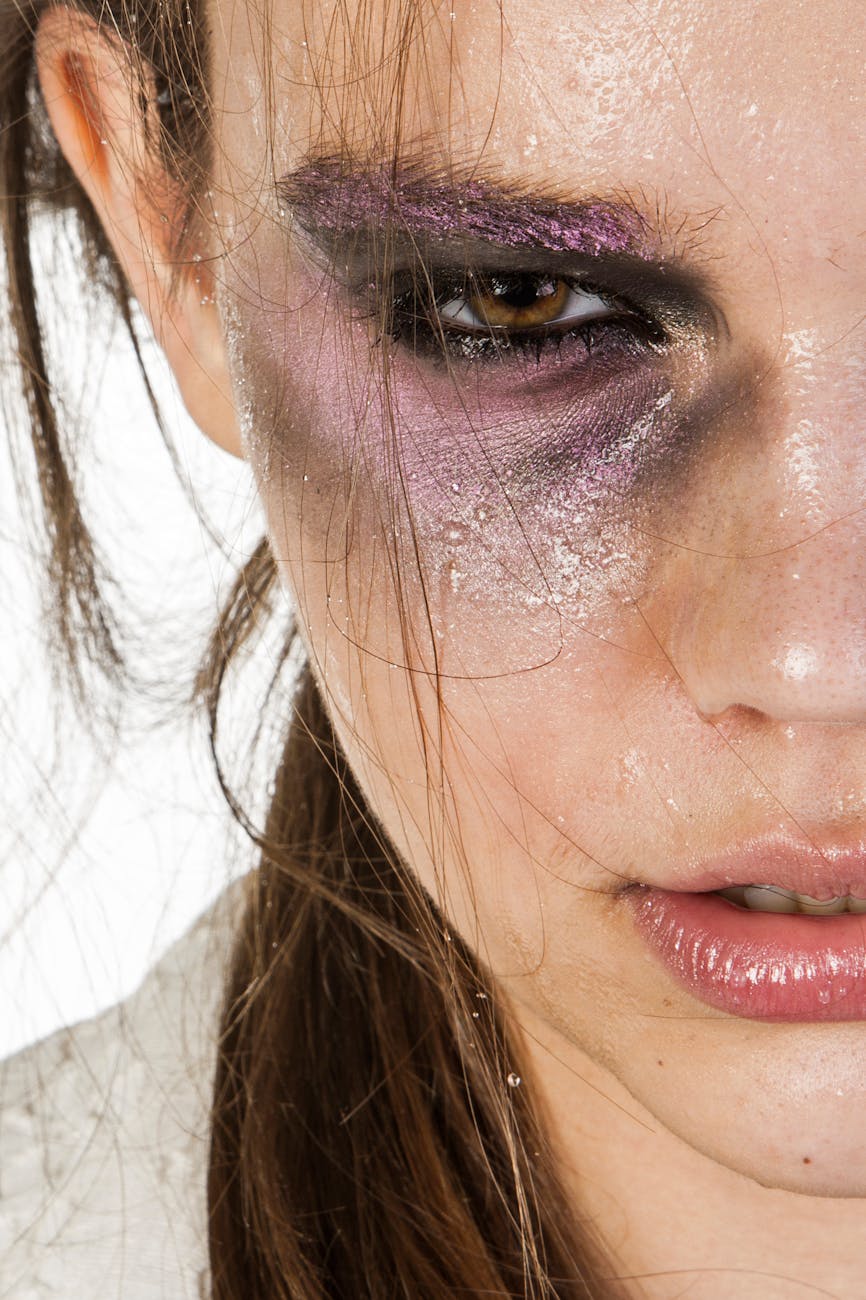
Heat Stress Definition OSHA
Heat stress poses significant risks to workers exposed to high temperatures in various industries. Understanding the concept, its definition by OSHA, and effective management strategies are crucial for ensuring the safety and well-being of employees.
Introduction to Heat Stress
Heat stress occurs when the body’s mechanisms for regulating internal temperature are overwhelmed by external heat conditions. This condition can lead to serious health issues if not addressed promptly. In the workplace, where individuals may be exposed to extreme temperatures, heat stress becomes a pertinent concern.
Heat Stress Definition by OSHA
The Occupational Safety and Health Administration (OSHA) defines heat stress as the net heat load to which a worker is exposed from the combined contributions of metabolic heat, environmental factors, and clothing worn. OSHA outlines specific parameters for defining heat stress, including temperature, humidity, air movement, and radiant heat sources.
Factors Contributing to Heat Stress
Several factors contribute to the development of heat stress in the workplace. Environmental factors such as high temperature, humidity, and lack of airflow play a significant role. Additionally, job-related factors like physical exertion, heavy protective clothing, and prolonged exposure to heat sources increase the risk. Individual factors such as age, fitness level, and pre-existing health conditions also influence susceptibility to heat stress.
Recognizing Heat Stress Symptoms
It’s essential for employers and employees to recognize the early signs of heat stress. Physical symptoms may include profuse sweating, dizziness, nausea, and headaches. Behavioral symptoms such as irritability, confusion, and decreased coordination should also be taken seriously.
Health Risks Associated with Heat Stress
Heat stress can lead to various health risks, both in the short and long term. Short-term effects may include heat rash, heat cramps, and heat exhaustion, which can progress to heat stroke if not treated promptly. Long-term exposure to high temperatures increases the risk of heat-related illnesses and may exacerbate pre-existing medical conditions.
OSHA Regulations on Heat Stress Management
OSHA has established regulations and guidelines to protect workers from heat stress hazards. Employers are required to assess the risk of heat stress in their workplaces and implement appropriate controls to prevent heat-related illnesses and injuries. OSHA provides specific guidelines for heat stress prevention, including scheduling rest breaks, providing access to cool drinking water, and implementing engineering controls to reduce heat exposure.
Heat Stress Prevention Strategies
Preventing heat stress requires a comprehensive approach that includes engineering controls, administrative controls, and the use of personal protective equipment (PPE). Engineering controls may involve implementing ventilation systems, shading work areas, and installing cooling equipment. Administrative controls include adjusting work schedules, providing training on heat stress awareness, and monitoring weather conditions. Personal protective equipment such as lightweight and breathable clothing, cooling vests, and hats with brims can also help mitigate heat exposure.
Training and Education
Educating workers about the risks of heat stress and how to prevent it is essential for ensuring their safety. OSHA recommends training programs that cover topics such as recognizing the signs of heat stress, proper hydration, and acclimatization techniques. Employers should also provide information on the importance of taking breaks in shaded or air-conditioned areas and avoiding excessive physical exertion during peak heat hours.
Monitoring and Evaluation
Implementing a heat stress monitoring program allows employers to assess the effectiveness of their prevention strategies and make necessary adjustments. Monitoring may involve measuring environmental conditions, conducting heat stress surveys among workers, and tracking incidents of heat-related illnesses. Regular evaluation of the program ensures that controls are adequate and employees are adequately protected from heat stress hazards.
Importance of Heat Stress Management in Various Industries
Heat stress is a prevalent concern in industries such as construction, agriculture, and manufacturing, where workers are often exposed to high temperatures for prolonged periods. Implementing proper heat stress management measures is essential for protecting the health and safety of employees in these sectors.
Technological Solutions for Heat Stress Prevention
Advancements in technology have led to the development of innovative tools and devices for preventing heat stress. Wearable sensors that monitor body temperature, smartphone apps that provide real-time heat stress alerts, and cooling garments with integrated fan systems are among the technological solutions available to help workers stay safe in hot environments.
Psychological Impact of Heat Stress
In addition to its physical effects, heat stress can also have a significant impact on mental health. Working in hot environments for extended periods can lead to increased stress, fatigue, and decreased cognitive function. Employers should be mindful of the psychological effects of heat stress and provide support services to help employees cope with the challenges.
Supporting Employees in Hot Environments
Employers can support employees working in hot environments by implementing policies and practices that prioritize their well-being. Providing adequate breaks, access to shaded areas, and cool drinking water are simple yet effective measures to prevent heat-related illnesses. Additionally, encouraging open communication and fostering a culture of safety can empower workers to voice concerns and seek assistance when needed.
Conclusion
Heat stress presents significant risks to workers exposed to high temperatures in various industries. Understanding OSHA’s definition of heat stress and implementing effective management strategies are essential for protecting employee health and safety. By prioritizing heat stress prevention through education, training, and technological solutions, employers can create safer working environments and reduce the incidence of heat-related illnesses and injuries.
Top 10 OSHA Violations in 2024
OSHA Standards for Construction and General Industry
FAQs
- What are the common symptoms of heat stress? Common symptoms of heat stress include profuse sweating, dizziness, nausea, headaches, and confusion.
- How can employers prevent heat stress in the workplace? Employers can prevent heat stress by implementing engineering controls, providing adequate breaks, ensuring proper hydration, and educating workers about heat stress awareness.
- Are there specific regulations for managing heat stress in the workplace? Yes, OSHA has established regulations and guidelines for managing heat stress hazards in the workplace to protect workers from heat-related illnesses and injuries.
- What industries are most at risk for heat stress? Industries such as construction, agriculture, manufacturing, and mining are among the most at risk for heat stress due to prolonged exposure to high temperatures.
- How can technology help prevent heat stress? Technology can help prevent heat stress by providing real-time monitoring of environmental conditions, alerting workers to potential hazards, and offering innovative cooling solutions such as wearable devices and cooling garments.