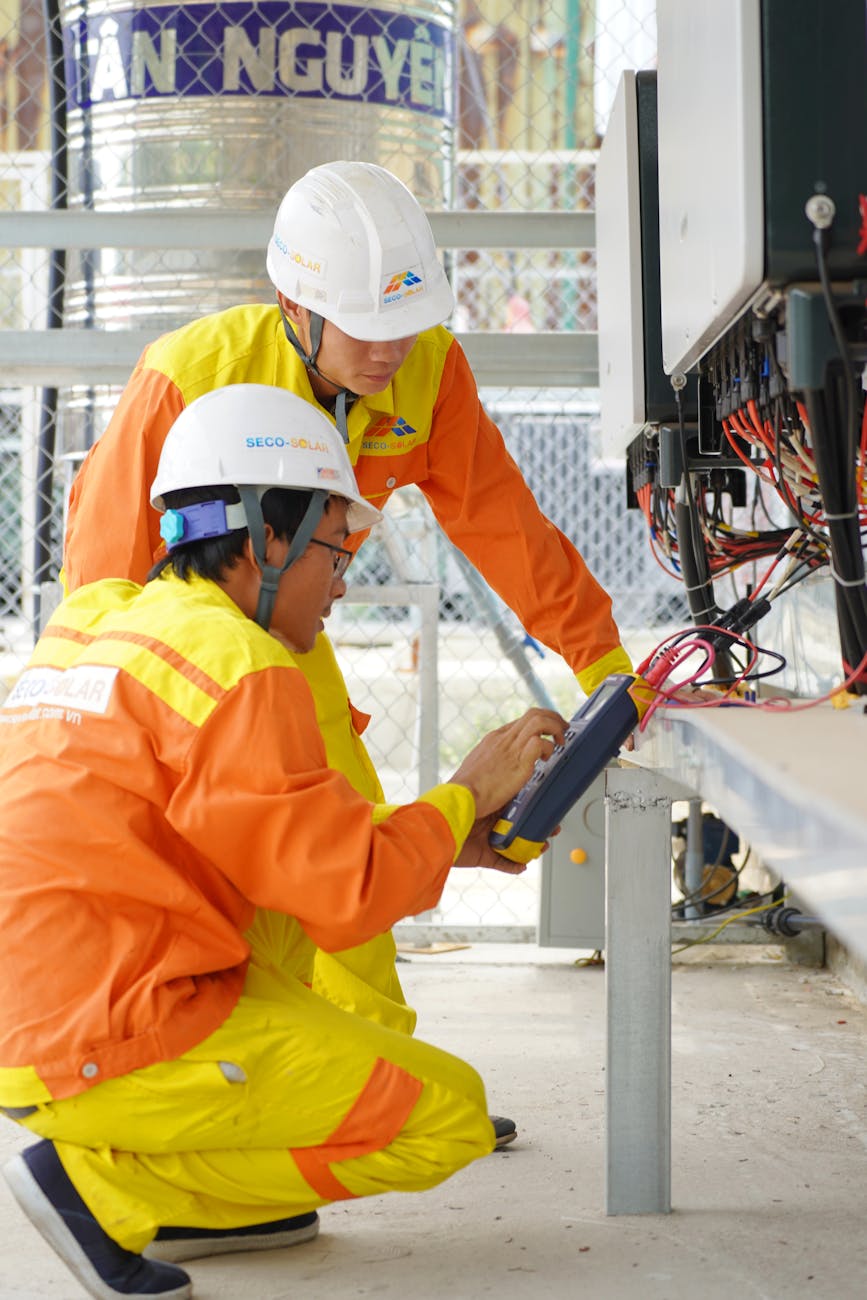
5 HAZOP Interview Questions for Process Safety Engineers
Introduction
Process Safety Engineers play a crucial role in identifying and mitigating risks in industrial processes. A Hazard and Operability Study (HAZOP) is a structured technique used to assess potential hazards in process systems. During interviews for Process Safety Engineer roles, candidates are often tested on their HAZOP knowledge. Below are five key HAZOP interview questions to help you prepare.
5 Essential HAZOP Interview Questions
1. What is HAZOP, and what are its main objectives?
Answer:
HAZOP (Hazard and Operability Study) is a systematic risk assessment method used to identify potential hazards and operability issues in process systems. Its main objectives include:
- Identifying deviations from design intent.
- Assessing risks associated with process deviations.
- Recommending safeguards to mitigate hazards.
- Improving process safety and reliability.
2. Explain the role of guide words in a HAZOP study.
Answer:
Guide words are predefined terms (e.g., NO, MORE, LESS, AS WELL AS, PART OF, REVERSE, OTHER THAN) used to systematically explore deviations from normal operation. They help the HAZOP team brainstorm potential failure scenarios by applying these words to process parameters (e.g., flow, pressure, temperature).
3. How do you determine the severity and likelihood of a hazard in a HAZOP study?
Answer:
Severity is assessed based on the potential consequences (e.g., injury, environmental damage, financial loss), while likelihood evaluates how probable the event is. A risk matrix is often used to categorize risks as Low, Medium, High, or Intolerable, guiding decision-making on necessary controls.
4. What are the key differences between HAZOP and other risk assessment methods like FMEA or What-If Analysis?
Answer:
- HAZOP: Structured, uses guide words, focuses on process deviations.
- FMEA (Failure Mode and Effects Analysis): Examines failure modes of individual components.
- What-If Analysis: Less structured, relies on brainstorming “what-if” scenarios.
HAZOP is best for complex process systems, while FMEA is more suited for equipment-level analysis.
5. How would you handle disagreements within a HAZOP team regarding a identified risk?
Answer:
- Encourage open discussion to understand different perspectives.
- Refer to industry standards or historical incident data for justification.
- Involve a senior facilitator or independent expert if consensus isn’t reached.
- Document differing opinions and rationale for future reference.
Conclusion
Preparing for HAZOP-related interview questions ensures you demonstrate expertise in process safety methodologies. Understanding guide words, risk assessment techniques, and team dynamics in HAZOP studies will help you stand out as a strong candidate for Process Safety Engineer roles.
10 Lockout/Tagout – LOTO Interview Questions & Answers
10 One Minute Safety Interview Questions (Quick Answers)
10 Risk Assessment Interview Questions (+ Matrix Examples)
5 Safety Scenario Questions & How to Answer Them
10 Tricky Behavioral Safety Interview Questions (+ Sample Answers)
FAQs
How often should a HAZOP study be conducted?
HAZOP studies are typically performed during design, after major modifications, or every 3-5 years for existing plants, depending on regulatory requirements and process changes.
Who should be part of a HAZOP team?
A multidisciplinary team including process engineers, safety engineers, operators, maintenance personnel, and a HAZOP facilitator.
Can HAZOP be applied to non-process industries?
Yes, HAZOP principles can be adapted for software, mechanical systems, and other industries, though it is most common in chemical and process industries.
What are common pitfalls in a HAZOP study?
- Inadequate team expertise.
- Rushing through deviations.
- Poor documentation.
- Ignoring human factors.
Is HAZOP qualitative or quantitative?
HAZOP is primarily qualitative, but quantitative risk assessment (QRA) may follow if deeper analysis is needed.
What documents are required before starting a HAZOP study?
Key documents include:
- P&IDs (Piping and Instrumentation Diagrams)
- Process Flow Diagrams (PFDs)
- Operating procedures
- Material safety data sheets (MSDS)
- Previous risk assessments
What is the role of a HAZOP leader/facilitator?
The facilitator:
- Guides the team through the study
- Ensures all deviations are considered
- Maintains focus and prevents tangents
- Documents findings and recommendations
How long does a typical HAZOP study take?
Duration depends on process complexity:
- Small systems: A few days
- Large plants: Weeks to months
- Sessions are usually 3-6 hours per day to maintain focus
What’s the difference between HAZOP and LOPA (Layer of Protection Analysis)?
- HAZOP: Identifies hazards and potential deviations
- LOPA: Semi-quantitative method that evaluates safeguards after HAZOP to determine if risks are adequately controlled
How do you prioritize HAZOP recommendations?
Recommendations are prioritized based on:
- Risk ranking (severity × likelihood)
- Cost-benefit analysis
- Regulatory requirements
- Operational criticality
Can HAZOP identify all possible hazards?
No method is exhaustive, but HAZOP is systematic and significantly reduces the chance of missing major hazards when properly conducted.
What software tools are used for HAZOP studies?
Common tools include:
- PHA-Pro
- Dyadem PHAWorks
- SpheraCloud (formerly Process Hazard Analysis Software)
- Excel-based templates for smaller studies
How do you validate HAZOP study results?
Validation methods include:
Field verification of safeguards
Peer review by independent experts
Comparing with incident history
Cross-checking with other risk assessments