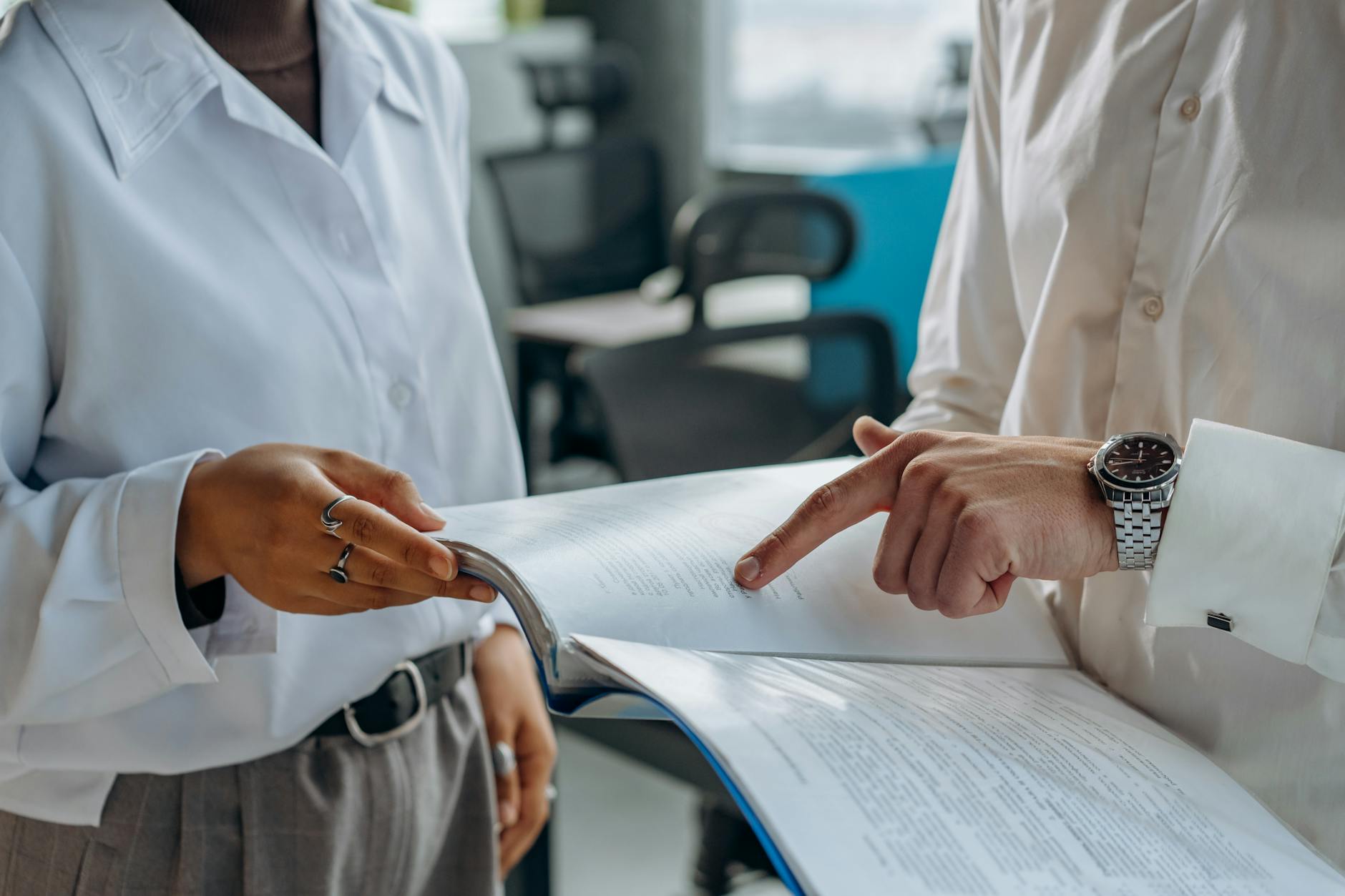
HAZOP Analysis Example
Introduction
Understanding the fundamentals of HAZOP analysis and its critical role in various industries is pivotal for ensuring safety and operational excellence. This article delves into the concept, methodology, and practical examples of HAZOP analysis, shedding light on its significance in risk management.
What is HAZOP analysis?
HAZOP, which stands for Hazard and Operability Study, is a systematic method used to identify potential hazards and operability issues in industrial processes. It involves a detailed examination of a system to pinpoint deviations from design intent that could result in hazardous situations.
Importance of HAZOP analysis
The significance of HAZOP analysis lies in its ability to proactively identify risks and prevent potential accidents or failures. By systematically assessing processes, it helps industries mitigate risks, ensuring safer operations and protecting personnel and assets.
Understanding HAZOP
Methodology behind HAZOP analysis
The methodology of HAZOP involves a multidisciplinary team analyzing the process systematically by examining nodes and deviations.
Key elements in a HAZOP study
The study involves identifying deviations, determining their causes, and evaluating the consequences of these deviations.
Steps in conducting a HAZOP analysis
The process typically includes planning, team formation, process understanding, conducting studies, and implementing recommendations.
HAZOP Analysis in Various Industries
HAZOP analysis finds extensive applications across industries.
HAZOP analysis in industry
Industries like chemical, petrochemical, and manufacturing heavily rely on HAZOP to ensure safety and compliance.
HAZOP analysis in manufacturing
In manufacturing, HAZOP is used to assess processes and prevent potential hazards in production lines.
HAZOP analysis in process safety
For maintaining process safety in industries like oil and gas, HAZOP analysis plays a pivotal role in risk management.
Benefits of HAZOP
Identifying potential hazards
HAZOP aids in recognizing potential dangers, allowing proactive measures to eliminate or minimize risks.
Enhancing safety measures
By pinpointing vulnerabilities, HAZOP enables industries to strengthen safety protocols, ensuring a secure working environment.
Cost-effectiveness through risk reduction
Implementing HAZOP analysis can lead to cost savings by preventing accidents and minimizing downtime, ultimately enhancing operational efficiency.
Real-life Examples
HAZOP analysis in chemical processing
In chemical processing, HAZOP analysis is conducted to identify risks associated with various chemical reactions and processes.
HAZOP analysis in oil and gas industry
HAZOP is crucial in the oil and gas sector to assess risks in drilling, refining, and transportation processes.
HAZOP analysis in pharmaceutical manufacturing
In pharmaceutical manufacturing, HAZOP helps in identifying potential risks in the production of medicines, ensuring product quality and safety.
Hazard and Operability (HAZOP) analysis is a structured method used to identify potential hazards and operability issues in processes, systems, or designs. Let's consider an example of a HAZOP analysis for a chemical manufacturing process involving the production of a cleaning solvent.
Process Description: The process involves mixing chemicals A and B in a reactor at a specific temperature and pressure to produce the cleaning solvent.
Nodes for Analysis:
- Parameter: Temperature
- Intended Operation: Maintain temperature at 70°C.
- Deviation: Increase in temperature due to a malfunction in the temperature control system.
- Consequence: Higher temperatures might cause a runaway reaction, leading to a possible explosion or degradation of the product, which could result in toxic fumes.
- Parameter: Pressure
- Intended Operation: Maintain pressure at 3 atm.
- Deviation: Pressure spikes due to a blockage in the vent.
- Consequence: Higher pressure could rupture equipment or cause leaks, leading to exposure of operators to hazardous chemicals or damage to the facility.
- Parameter: Flow Rate of Chemical A
- Intended Operation: Maintain a specific flow rate.
- Deviation: Decrease in the flow rate of Chemical A due to a valve failure.
- Consequence: Insufficient supply of Chemical A could lead to an incomplete reaction, resulting in the formation of unwanted by-products or an unstable product.
- Parameter: Mixing Time
- Intended Operation: Maintain a specific mixing time.
- Deviation: Shorter mixing time due to equipment malfunction.
- Consequence: Inadequate mixing might lead to uneven distribution of chemicals, causing variations in product quality or potential reactivity issues.
- Parameter: Operator Error
- Intended Operation: Proper training and adherence to procedures.
- Deviation: Operator error in adding incorrect quantities of chemicals.
- Consequence: Incorrect proportions of chemicals can lead to an unsafe or ineffective product, posing risks during use or storage.
Mitigation Measures:
- Implement redundant temperature control systems and alarms to prevent overheating.
- Install pressure relief valves and conduct regular maintenance to prevent blockages.
- Use flow sensors and automatic shutdown systems to detect and address flow rate deviations.
- Provide comprehensive training for operators and implement double-check procedures for chemical quantities.
- Conduct routine equipment inspections and preventive maintenance.
The HAZOP analysis enables the identification of potential deviations from the intended operation and their possible consequences, allowing for the implementation of preventive measures to mitigate risks and enhance the safety and operability of the process.
Conclusion
HAZOP analysis stands as a cornerstone in risk management strategies across industries. Its systematic approach in identifying and mitigating risks not only ensures safety but also enhances operational efficiency.
OSHA Hazard Identification Requirements
OSHA Hazard Identification Training Tool
Hazard Identification Methods in the Workplace
FAQs on HAZOP Analysis
1. What industries benefit from HAZOP analysis?
HAZOP analysis is beneficial across industries like chemical, manufacturing, oil and gas, pharmaceuticals, and more.
2. How does HAZOP analysis enhance safety measures?
By identifying potential hazards, HAZOP allows industries to implement targeted safety measures, reducing risks significantly.
3. Is HAZOP analysis a regulatory requirement?
While not always mandatory, many industries adhere to HAZOP analysis as part of their safety and risk management protocols.
4. How often should HAZOP studies be conducted?
The frequency of HAZOP studies varies based on industry standards and the complexity of processes, typically conducted at regular intervals or during process modifications.
5. Can HAZOP analysis prevent all accidents?
While HAZOP analysis significantly reduces risks, it doesn’t guarantee the prevention of all accidents. It serves as a proactive measure to mitigate potential hazards.