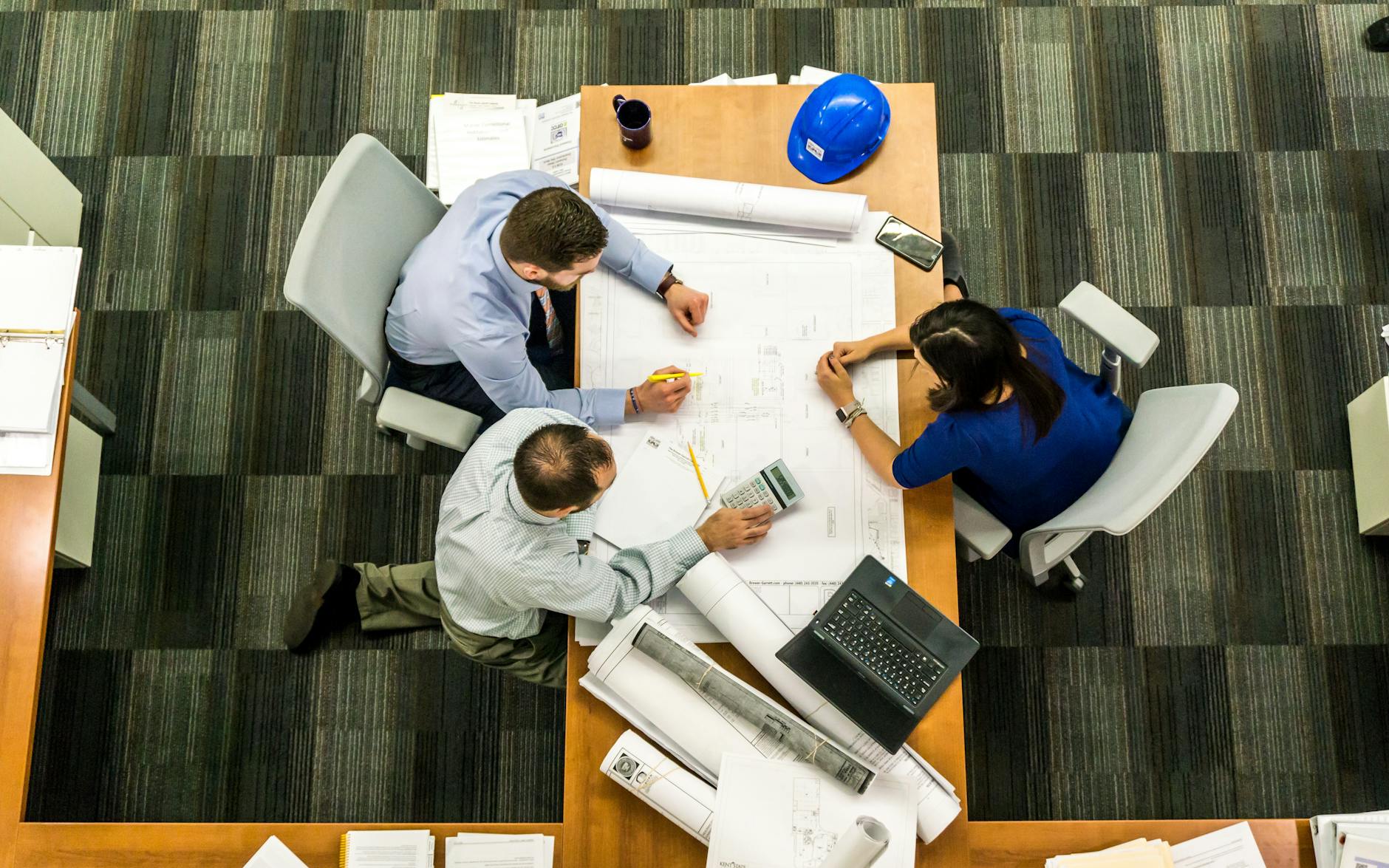
What Are the Five Standard Operating Procedures?
Introduction
Ever wonder how organizations maintain seamless operations, ensure safety, and meet quality standards? It all comes down to Standard Operating Procedures (SOPs). SOPs are the backbone of consistent and efficient workflows, ensuring everyone is on the same page. Let’s dive into what SOPs are, why they matter, and explore the five essential types.
Understanding Standard Operating Procedures (SOPs)
Definition of SOPs
SOPs are detailed written instructions designed to achieve uniformity in performing specific functions. They act as a guide, detailing how tasks should be done, by whom, and under what conditions.
Key Objectives of SOPs
Ensuring Consistency
By outlining step-by-step instructions, SOPs ensure tasks are performed consistently, regardless of who is executing them.
Enhancing Efficiency
Clear guidelines reduce ambiguity, saving time and resources by streamlining processes.
Maintaining Compliance
Many industries require adherence to regulations. SOPs help ensure compliance with legal, safety, and quality standards.
Why Are SOPs Essential?
Benefits of SOPs
- Improved Training and Onboarding
New employees can quickly get up to speed with well-documented procedures. - Reduced Errors and Risks
SOPs minimize mistakes by providing clear instructions. - Improved Employee Accountability
With documented expectations, employees understand their roles better.
The Five Standard Operating Procedures
SOP 1: Safety and Emergency Procedures
Importance of Safety SOPs
Safety is paramount in any organization. Proper procedures can prevent accidents and save lives.
Examples of Safety Procedures
- Fire evacuation plans.
- Hazard identification protocols.
- First aid and medical emergency steps.
SOP 2: Operational Workflow Procedures
Streamlining Daily Operations
These SOPs cover day-to-day activities, ensuring operations run smoothly.
Examples of Workflow SOPs
- Manufacturing assembly processes.
- Customer service protocols.
SOP 3: Maintenance Procedures
Importance of Preventive Maintenance
Regular maintenance reduces downtime and extends equipment life.
Examples of Maintenance SOPs
- HVAC system inspections.
- Equipment calibration routines.
SOP 4: Quality Control Procedures
Ensuring Product and Service Standards
These procedures verify that outputs meet established standards.
Examples of Quality Control SOPs
- Product testing guidelines.
- Inspection checklists.
SOP 5: Communication and Reporting Procedures
Improving Internal Communication
Effective communication is critical for teamwork and reporting progress or issues.
Examples of Reporting SOPs
- Incident reporting protocols.
- Weekly progress report templates.
How to Create Effective SOPs
Identify Key Processes
Pinpoint areas where consistency is essential, such as safety or quality.
Involve Team Members
Collaboration ensures the SOPs are practical and tailored to real-world needs.
Use Clear and Concise Language
Avoid jargon; make the instructions easy to understand.
Regularly Update and Review SOPs
Processes evolve, and SOPs should too. Regular reviews keep them relevant.
Challenges in Implementing SOPs
Resistance to Change
Employees may hesitate to adopt new procedures. Address concerns with proper training.
Keeping SOPs Relevant
Outdated SOPs can cause confusion. Regular updates are non-negotiable.
Ensuring Adherence
Monitoring and reinforcement are key to making SOPs a part of daily routines.
Conclusion
Standard Operating Procedures are crucial for maintaining safety, efficiency, and consistency in any organization. By implementing the five essential SOPs—safety, workflow, maintenance, quality control, and communication—you can ensure smooth operations and a productive work environment.
Tower Crane Limit Switch Types
How Many Earthing Required for Tower Crane
FAQs
- What is the primary purpose of an SOP?
SOPs ensure consistency, compliance, and efficiency in processes. - How often should SOPs be updated?
Ideally, SOPs should be reviewed annually or whenever processes change. - Who is responsible for creating SOPs in a company?
Usually, department heads or designated process owners create SOPs. - Can SOPs improve workplace safety?
Absolutely. Clear safety procedures can prevent accidents and ensure a safer work environment. - Are SOPs necessary for small businesses?
Yes! Even small businesses benefit from organized and consistent workflows.