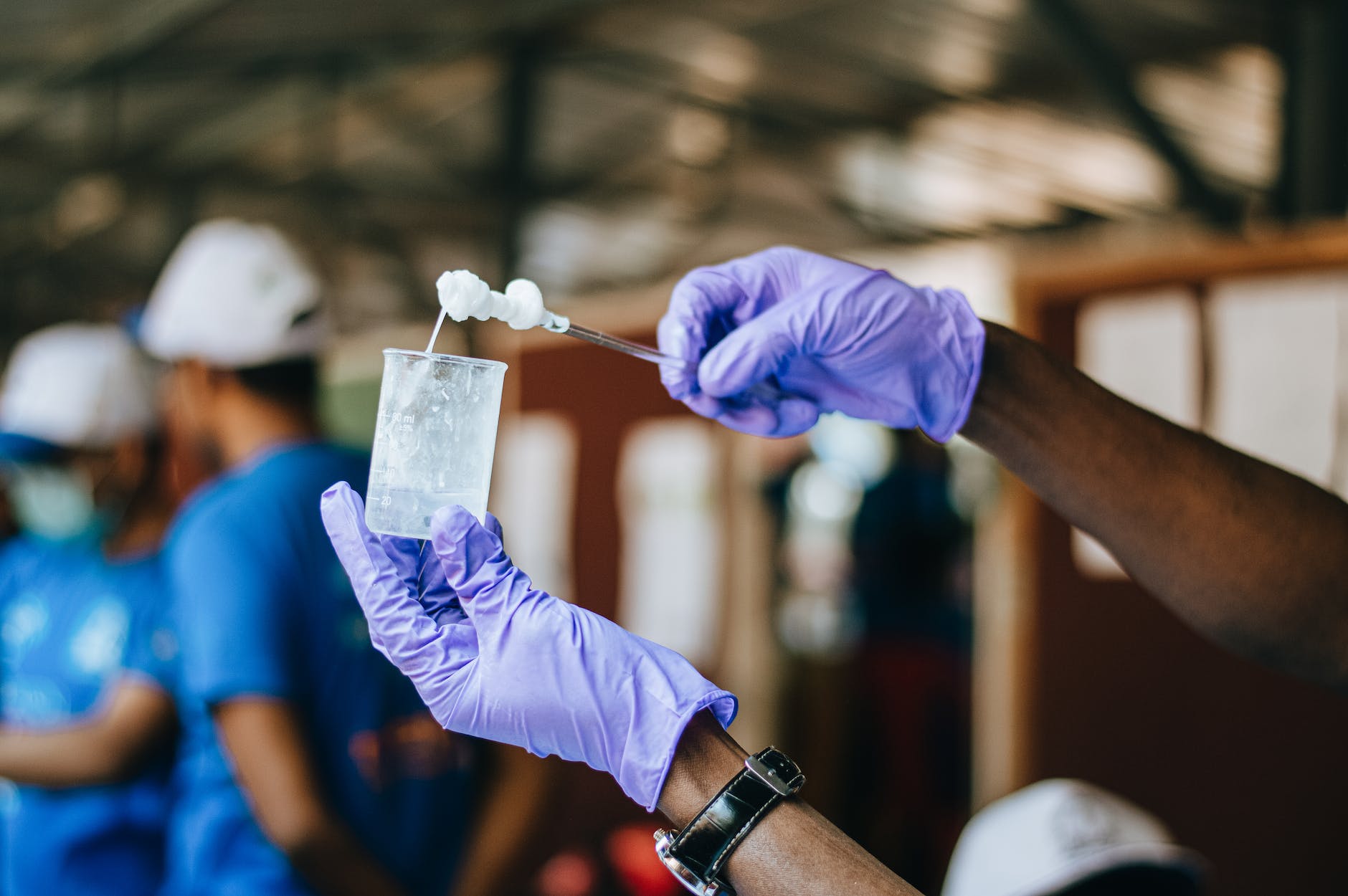
Failure Mode Effect Analysis (FMEA): Accident Investigation Method
Accidents can have significant consequences in various industries, from manufacturing to healthcare. Understanding the root causes of accidents is crucial to prevent their recurrence and ensure the safety of individuals involved. One effective method for investigating accidents and uncovering their underlying causes is Failure Mode Effect Analysis (FMEA).
Introduction
Accidents, regardless of their nature, can have devastating consequences. They lead to injuries, loss of life, property damage, and can even impact an organization’s reputation and financial stability. Investigating accidents thoroughly is vital not only for legal and regulatory compliance but also to prevent similar incidents in the future. One methodology that has gained prominence in this area is Failure Mode Effect Analysis (FMEA).
What is Failure Mode Effect Analysis (FMEA)?
Failure Mode Effect Analysis (FMEA) is a systematic approach used to evaluate potential failure modes within a process, system, or product and assess the effects of those failures. It involves identifying failure modes, analyzing their potential consequences, and prioritizing them based on their potential risks. FMEA helps organizations understand the weak points in their processes and take proactive steps to mitigate risks before they lead to accidents.
The Importance of Accident Investigation
Accident investigation is a critical component of safety management. It provides insights into the underlying causes of accidents, allowing organizations to address root issues and prevent recurrence. Through thorough investigation, organizations can uncover contributing factors such as human error, equipment malfunction, or process deficiencies.
Key Components of FMEA
4.1 Identifying Failure Modes
The first step in FMEA is to identify potential failure modes – the ways in which a process or system could fail. This involves brainstorming and considering various scenarios that could lead to undesirable outcomes.
4.2 Assessing Effects
Once failure modes are identified, the next step is to assess the potential effects of each failure. This helps in understanding the severity of the consequences, from minor inconveniences to major safety hazards.
4.3 Determining Causes and Likelihood
Understanding why a failure might occur is crucial. Organizations need to delve into the causes behind each potential failure mode and assess the likelihood of those causes leading to actual failures.
4.4 Assigning Risk Priority Numbers (RPN)
Risk Priority Numbers are calculated by multiplying the severity, likelihood, and detectability scores of each failure mode. This helps prioritize failure modes based on their potential impact.
Application of FMEA in Different Industries
FMEA is a versatile methodology that can be applied across various industries. It’s used in manufacturing to identify potential defects, in healthcare to improve patient safety, and even in software development to enhance reliability.
Benefits of Using FMEA for Accident Investigation
Using FMEA for accident investigation offers several benefits. It allows organizations to take a proactive approach to safety, identify potential risks, prioritize corrective actions, and improve overall processes.
Challenges and Limitations of FMEA
While FMEA is a powerful tool, it does come with challenges. It requires thorough data collection, cross-functional collaboration, and continuous monitoring. Additionally, it might not uncover every possible failure mode.
Comparison with Other Accident Investigation Methods
FMEA stands out due to its proactive nature. Unlike some other methods that focus solely on analyzing past incidents, FMEA helps prevent future accidents by addressing potential failure modes.
Case Study: FMEA in Automotive Safety
In the automotive industry, FMEA has played a pivotal role in enhancing safety. By analyzing potential failure modes in vehicle systems, manufacturers have been able to implement design changes that reduce the risk of accidents.
Steps to Conduct a Successful FMEA
Conducting a successful FMEA involves several key steps:
10.1 Assembling a Cross-Functional Team
Bringing together experts from different fields ensures a comprehensive analysis of potential failure modes.
10.2 Selecting the Process to Analyze
Choose the process, system, or product that requires analysis and improvement.
10.3 Identifying Potential Failure Modes
Brainstorm and identify all potential failure modes within the selected process.
10.4 Determining Severity of Effects
Assess the potential impact of each failure mode’s effects on safety and operations.
10.5 Assessing Likelihood and Detection
Evaluate the likelihood of each failure mode occurring and the ability to detect it before it leads to harm.
10.6 Calculating Risk Priority Numbers
Assign RPN to each failure mode to prioritize them for corrective actions.
10.7 Prioritizing and Implementing Actions
Based on RPN, prioritize failure modes and implement actions to mitigate risks.
The Role of Leadership in FMEA Implementation
Leadership commitment is crucial for successful FMEA implementation. It provides the necessary resources, support, and organizational culture for effective accident prevention.
Continuous Improvement and FMEA
FMEA is not a one-time process. It should be integrated into an organization’s continuous improvement efforts to ensure ongoing safety and operational enhancement.
Conclusion
Failure Mode Effect Analysis (FMEA) is a robust method for investigating accidents and preventing their recurrence. By systematically identifying potential failure modes, assessing their effects, and prioritizing actions, organizations can enhance safety and operational reliability across various industries.
Bow Tie Analysis: Accident Investigation Method
Root Cause Analysis: Accident Investigation Method
5 Why Analysis: Accident Investigation Method
Difference between Accident and Incident in the workplace
How we can do Accident Investigation in Safety field
FAQs
14.1 What is the primary goal of FMEA?
The primary goal of FMEA is to proactively identify potential failure modes, assess their impact, and prioritize actions to prevent accidents and enhance safety.
14.2 How does FMEA differ from RCA (Root Cause Analysis)?
While both methods investigate accidents, FMEA focuses on analyzing potential failures before they occur, whereas RCA delves into the root causes of specific incidents after they’ve happened.
14.3 Can FMEA be applied in service-based industries?
Yes, FMEA can be applied in service-based industries to identify potential failure modes in processes and enhance service quality.
14.4 Is FMEA a one-time process or an ongoing practice?
FMEA is an ongoing practice that should be integrated into an organization’s continuous improvement efforts for sustained safety enhancement.
14.5 What are some common challenges in implementing FMEA effectively?
Implementing FMEA effectively requires thorough data collection, cross-functional collaboration, and consistent leadership support. It can be challenging to ensure all potential failure modes are identified and addressed.