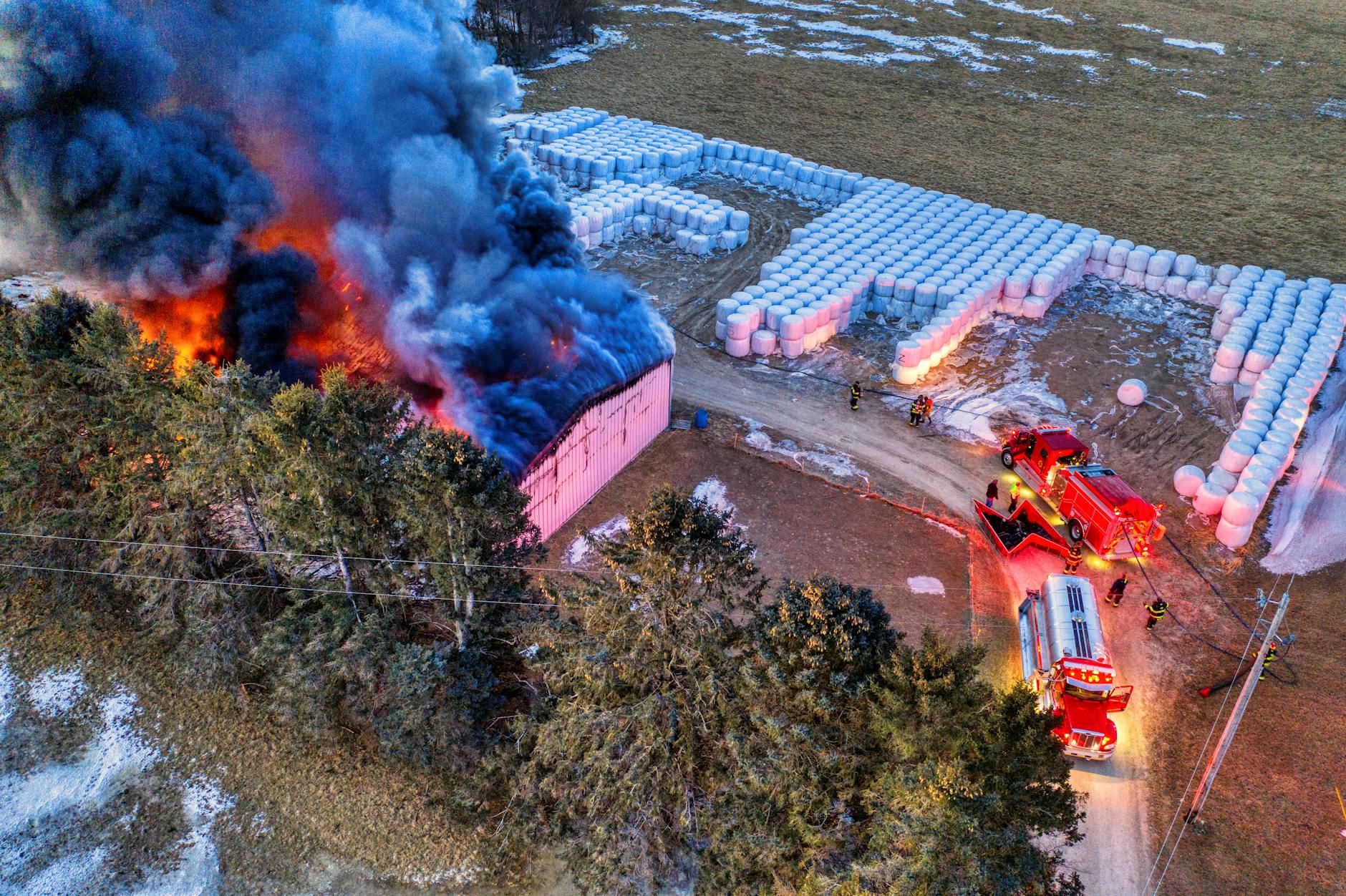
Factory Accident Examples: What Went Wrong?
Introduction
Factory accidents can have devastating consequences, including injuries, fatalities, and significant financial losses. Understanding what went wrong in past incidents helps improve safety measures and prevent future disasters. This article examines real-world factory accident examples, analyzes their causes, and discusses lessons learned to enhance workplace safety.
Notable Factory Accident Examples
1. Texas City Refinery Explosion (2005)
- What Happened? A massive explosion at BP’s Texas City refinery killed 15 workers and injured 180.
- Cause: Overfilled distillation tower led to flammable liquid vapor release, ignited by a nearby truck.
- Key Failures: Poor safety culture, inadequate maintenance, and lack of hazard awareness.
2. Rana Plaza Collapse (2013)
- What Happened? A garment factory in Bangladesh collapsed, killing over 1,100 workers.
- Cause: Structural failure due to unauthorized building expansions and poor construction standards.
- Key Failures: Ignored safety warnings, lack of regulatory enforcement, and unethical cost-cutting.
3. Imperial Sugar Dust Explosion (2008)
- What Happened? A sugar dust explosion in Georgia killed 14 and injured dozens.
- Cause: Accumulated sugar dust ignited, triggering a massive blast.
- Key Failures: Inadequate dust control, poor ventilation, and lack of OSHA compliance.
4. Fukushima Daiichi Nuclear Disaster (2011)
- What Happened? Following an earthquake and tsunami, Japan’s Fukushima nuclear plant suffered meltdowns.
- Cause: Flooding disabled backup generators, leading to cooling system failure.
- Key Failures: Insufficient disaster preparedness and outdated safety protocols.
Lessons Learned
- Proactive Safety Measures: Regular inspections, hazard assessments, and worker training are critical.
- Regulatory Compliance: Factories must adhere to safety standards (OSHA, ISO, etc.).
- Emergency Preparedness: Robust disaster response plans can save lives.
Conclusion
Factory accidents often result from preventable errors—poor maintenance, ignored warnings, or weak safety cultures. By learning from past disasters, companies can implement stronger protections, ensuring safer workplaces for employees.
10 Near-Miss Discussion Examples (+Reporting Format)
Top 20 Near Miss Reporting Examples & Lessons Learned
Classification of Accidents in Safety
Examples of Near Miss Reporting
Near Miss Reporting Procedure
FAQs
What are the most common causes of factory accidents?
Common causes include equipment malfunctions, human error, poor training, lack of safety protocols, and hazardous material mishandling.
How can factories prevent explosions?
Proper ventilation, regular equipment checks, dust control, and flammable material storage compliance can reduce explosion risks.
What role does management play in factory safety?
Management must enforce safety policies, provide training, conduct risk assessments, and ensure regulatory compliance.
Why do factory accidents keep happening?
Accidents persist due to negligence, cost-cutting on safety, lack of enforcement, and failure to learn from past incidents.
What should workers do if they notice safety hazards?
Workers should report hazards immediately to supervisors, follow safety protocols, and use whistleblower protections if ignored.